Introduction to Rigid-Flex PCBs
Rigid-Flex PCBs are a unique type of printed circuit board that combines both rigid and flexible substrates into a single, integrated design. This innovative approach offers numerous advantages over traditional rigid PCBs, including improved reliability, reduced size and weight, and enhanced design flexibility. As electronic devices continue to shrink in size and increase in complexity, rigid-flex PCBs have become an increasingly popular choice for a wide range of applications, from consumer electronics to aerospace and military systems.
In this article, we will explore the key concepts and techniques involved in rigid-flex PCB design, providing you with the knowledge and skills necessary to create highly efficient and reliable designs. We will cover topics such as material selection, layer stackup, design rules, and manufacturing considerations, as well as best practices for optimizing your rigid-flex PCB designs for rapid prototyping and production.
Understanding the Benefits of Rigid-flex PCBs
Increased Reliability
One of the primary benefits of rigid-flex PCBs is their increased reliability compared to traditional rigid PCBs. By eliminating the need for connectors and cables between rigid sections, rigid-flex PCBs minimize the potential for connection failures and signal integrity issues. This is particularly important in applications where vibration, shock, or thermal stress are a concern, as the integrated nature of rigid-flex PCBs helps to distribute these stresses more evenly throughout the assembly.
Reduced Size and Weight
Another significant advantage of rigid-flex PCBs is their ability to reduce the overall size and weight of electronic assemblies. By combining rigid and flexible sections into a single, compact package, designers can eliminate the need for bulky connectors and cables, resulting in a more streamlined and lightweight design. This is especially valuable in applications where space is limited, such as wearable devices, implantable medical devices, or aerospace systems.
Enhanced Design Flexibility
Rigid-flex PCBs also offer enhanced design flexibility compared to traditional rigid PCBs. The ability to incorporate flexible sections allows designers to create three-dimensional shapes and configurations that would be impossible with rigid PCBs alone. This enables the creation of more complex and innovative designs, such as folded or rolled assemblies, that can be tailored to fit specific form factors or packaging requirements.
Mastering the Fundamentals of Rigid-flex PCB Design
Material Selection
Selecting the appropriate materials for your rigid-flex PCB is crucial to ensuring optimal performance and reliability. The most common materials used for the rigid sections of the PCB are FR-4, a glass-reinforced epoxy laminate, and polyimide, a high-performance polymer known for its excellent thermal and mechanical properties. For the flexible sections, materials such as polyimide, polyester, or PEEK are typically used, depending on the specific requirements of the application.
When choosing materials for your rigid-flex PCB, consider factors such as the operating temperature range, mechanical stresses, and chemical exposure that the assembly will be subjected to. Additionally, ensure that the selected materials are compatible with each other and with the manufacturing processes involved in fabricating the PCB.
Layer Stackup Design
Designing an effective layer stackup is another essential aspect of rigid-flex PCB design. The layer stackup refers to the arrangement of conductive layers, insulating layers, and adhesives that make up the PCB. A well-designed layer stackup ensures proper signal integrity, minimizes electromagnetic interference (EMI), and facilitates manufacturability.
When designing your layer stackup, consider the following best practices:
- Use symmetrical layer stackups whenever possible to minimize warpage and improve dimensional stability.
- Ensure adequate spacing between conductive layers to minimize crosstalk and signal integrity issues.
- Use ground planes and power planes to provide shielding and reduce EMI.
- Incorporate adhesive layers between the rigid and flexible sections to ensure reliable bonding and prevent delamination.
Here is an example of a typical 6-layer rigid-flex PCB Stackup:
Layer | Material | Thickness (mm) |
---|---|---|
Top Cover | Polyimide | 0.025 |
Top Copper | Copper | 0.018 |
Dielectric 1 | FR-4 | 0.200 |
Inner Copper 1 | Copper | 0.035 |
Dielectric 2 | FR-4 | 0.400 |
Inner Copper 2 | Copper | 0.035 |
Dielectric 3 | FR-4 | 0.200 |
Bottom Copper | Copper | 0.018 |
Bottom Cover | Polyimide | 0.025 |
Design Rules and Constraints
To ensure the manufacturability and reliability of your rigid-flex PCB, it is essential to adhere to a set of design rules and constraints. These rules govern various aspects of the design, such as minimum trace widths, clearances, via sizes, and bend radii. Failure to comply with these rules can result in manufacturing defects, reduced reliability, and increased costs.
Some common design rules for rigid-flex PCBs include:
- Minimum trace width: 0.075 mm (3 mil)
- Minimum trace spacing: 0.075 mm (3 mil)
- Minimum via diameter: 0.200 mm (8 mil)
- Minimum via-to-via spacing: 0.250 mm (10 mil)
- Minimum bend radius: 6 times the thickness of the flexible layer
It is important to consult with your PCB manufacturer to obtain their specific design rules and constraints, as these may vary depending on their capabilities and processes.
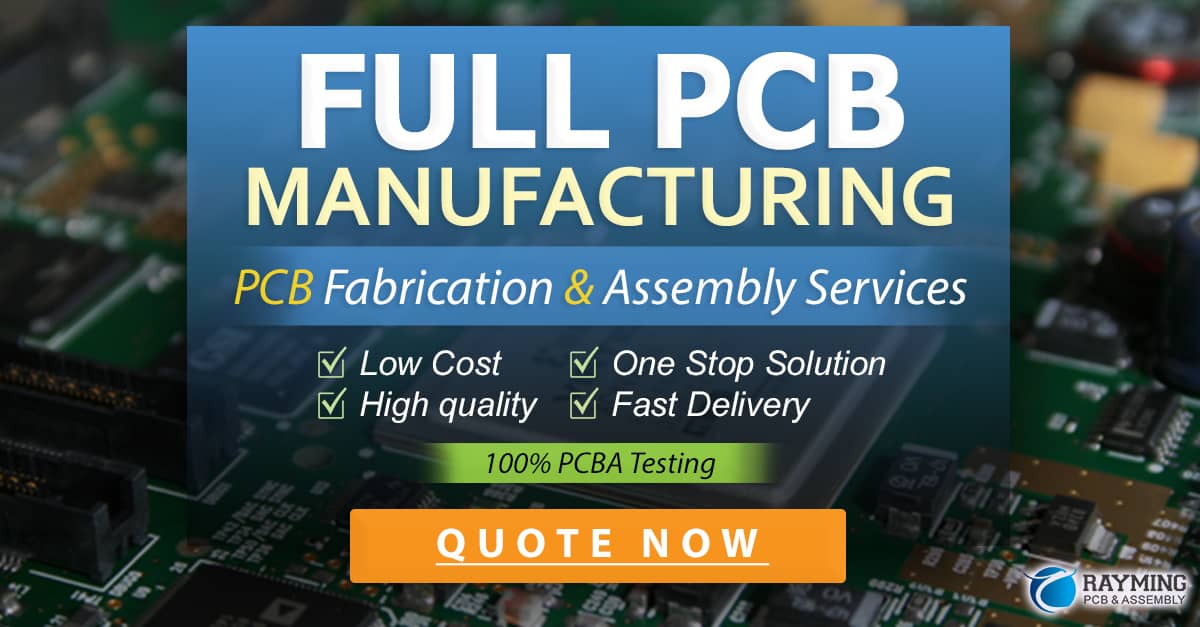
Advanced Techniques for Optimizing Rigid-flex PCB Design
Signal Integrity Analysis
Signal integrity is a critical concern in rigid-flex PCB design, particularly as signal speeds and frequencies continue to increase. To ensure optimal signal quality and minimize issues such as crosstalk, reflections, and EMI, it is essential to perform signal integrity analysis during the design process.
There are several tools and techniques available for analyzing signal integrity in rigid-flex PCBs, including:
- Time-domain reflectometry (TDR): Used to measure impedance discontinuities and identify potential signal integrity issues.
- Frequency-domain analysis: Used to evaluate the frequency response of the PCB and identify resonances or other frequency-dependent effects.
- Eye diagram analysis: Used to assess the quality of high-speed digital signals and identify issues such as jitter, noise, or intersymbol interference.
By incorporating signal integrity analysis into your design process, you can identify and mitigate potential issues early on, reducing the risk of costly redesigns or manufacturing defects.
Thermal Management
Thermal management is another important consideration in rigid-flex PCB design, particularly in applications where high power densities or extreme operating temperatures are involved. Proper thermal management helps to ensure the reliability and longevity of the assembly by preventing overheating and thermal stress.
Some strategies for effective thermal management in rigid-flex PCBs include:
- Using thermally conductive materials, such as metal-Core PCBs or thermally enhanced dielectrics, to improve heat dissipation.
- Incorporating thermal vias or heat sinks to provide additional cooling paths for high-power components.
- Optimizing component placement and routing to minimize thermal hotspots and promote even heat distribution.
- Using thermal simulation tools to analyze the thermal performance of the assembly and identify potential issues.
By addressing thermal management early in the design process, you can ensure that your rigid-flex PCB will perform reliably even in demanding thermal environments.
Design for Manufacturing (DFM)
Design for Manufacturing (DFM) is a critical aspect of rigid-flex PCB design that focuses on optimizing the design for manufacturability, reliability, and cost-effectiveness. By incorporating DFM principles into your design process, you can streamline production, reduce the risk of defects, and minimize manufacturing costs.
Some key DFM considerations for rigid-flex PCBs include:
- Adhering to the manufacturer’s design rules and constraints to ensure compatibility with their processes and equipment.
- Using standard materials, components, and processes whenever possible to reduce costs and lead times.
- Minimizing the number of layers and complex features to simplify manufacturing and improve yields.
- Incorporating testability features, such as test points or boundary scan, to facilitate testing and debugging.
- Collaborating closely with your PCB manufacturer throughout the design process to identify and address potential manufacturing challenges.
By prioritizing DFM in your rigid-flex PCB design, you can ensure a smooth transition from prototyping to production and maximize the success of your project.
Best Practices for Rapid Rigid-flex PCB Design
Collaborative Design Process
To streamline the rigid-flex PCB design process and ensure optimal results, it is essential to foster a collaborative design environment that involves all stakeholders, including electrical engineers, mechanical engineers, PCB designers, and manufacturers. By working together closely throughout the design process, teams can identify and address potential issues early on, reducing the risk of costly redesigns or delays.
Some best practices for collaborative rigid-flex PCB design include:
- Establishing clear communication channels and protocols to ensure that all stakeholders are informed and involved throughout the process.
- Using cloud-based design tools and version control systems to facilitate real-time collaboration and ensure that all team members are working with the most up-to-date design files.
- Conducting regular design reviews and milestone meetings to assess progress, identify potential issues, and make necessary adjustments.
- Leveraging the expertise of your PCB manufacturer to ensure that the design is optimized for manufacturability and reliability.
By fostering a collaborative and iterative design process, you can accelerate the development of your rigid-flex PCB and ensure that the final product meets all performance, reliability, and cost requirements.
Design Reuse and Modular Design
Another effective strategy for accelerating rigid-flex PCB design is to leverage design reuse and modular design principles. By creating reusable design blocks or modules that can be easily integrated into multiple projects, you can reduce design time, minimize errors, and improve consistency across your product line.
Some tips for implementing design reuse and modular design in your rigid-flex PCB projects include:
- Identifying common functional blocks or subsystems that can be designed as reusaBLE Modules, such as power supplies, communication interfaces, or sensor modules.
- Creating a library of proven design elements, such as schematic symbols, footprints, and layout patterns, that can be easily accessed and incorporated into new designs.
- Using parametric design techniques to create flexible, scalable modules that can be easily adapted to different requirements or specifications.
- Documenting design guidelines and best practices to ensure that reusable modules are consistently implemented across projects and teams.
By embracing design reuse and modular design, you can significantly reduce the time and effort required to develop new rigid-flex PCBs while also improving the quality and reliability of your designs.
FAQs
- What are the key benefits of using rigid-flex PCBs compared to traditional rigid PCBs?
-
Rigid-flex PCBs offer several key benefits, including increased reliability, reduced size and weight, and enhanced design flexibility. By eliminating the need for connectors and cables between rigid sections, rigid-flex PCBs minimize the potential for connection failures and signal integrity issues. Additionally, the ability to incorporate flexible sections enables the creation of more complex and innovative three-dimensional designs that can be tailored to specific form factors or packaging requirements.
-
What materials are commonly used in rigid-flex PCB design?
-
The most common materials used for the rigid sections of the PCB are FR-4, a glass-reinforced epoxy laminate, and polyimide, a high-performance polymer known for its excellent thermal and mechanical properties. For the flexible sections, materials such as polyimide, polyester, or PEEK are typically used, depending on the specific requirements of the application.
-
What are some important design rules and constraints to consider when designing rigid-flex PCBs?
-
Some common design rules for rigid-flex PCBs include minimum trace widths of 0.075 mm (3 mil), minimum trace spacing of 0.075 mm (3 mil), minimum via diameters of 0.200 mm (8 mil), minimum via-to-via spacing of 0.250 mm (10 mil), and minimum bend radii of 6 times the thickness of the flexible layer. It is important to consult with your PCB manufacturer to obtain their specific design rules and constraints, as these may vary depending on their capabilities and processes.
-
How can signal integrity be analyzed and optimized in rigid-flex PCB design?
-
Signal integrity can be analyzed and optimized using several tools and techniques, including time-domain reflectometry (TDR) to measure impedance discontinuities, frequency-domain analysis to evaluate the frequency response of the PCB, and eye diagram analysis to assess the quality of high-speed digital signals. By incorporating signal integrity analysis into the design process, potential issues can be identified and mitigated early on, reducing the risk of costly redesigns or manufacturing defects.
-
What are some best practices for ensuring a rapid and efficient rigid-flex PCB design process?
- To ensure a rapid and efficient rigid-flex PCB design process, it is important to foster a collaborative design environment that involves all stakeholders, use cloud-based design tools and version control systems to facilitate real-time collaboration, conduct regular design reviews and milestone meetings, and leverage the expertise of your PCB manufacturer. Additionally, implementing design reuse and modular design principles can significantly reduce design time, minimize errors, and improve consistency across your product line.
Conclusion
Rigid-flex PCBs offer numerous advantages over traditional rigid PCBs, enabling the creation of more reliable, compact, and innovative electronic assemblies. By mastering the fundamentals of rigid-flex PCB design, including material selection, layer stackup design, and design rules, and by incorporating advanced techniques such as signal integrity analysis, thermal management, and Design for Manufacturing (DFM), you can create highly optimized designs that meet the most demanding performance, reliability, and cost requirements.
Furthermore, by adopting best practices for rapid rigid-flex PCB design, such as fostering a collaborative design process, leveraging design reuse and modular design principles, and working closely with your PCB manufacturer, you can streamline the development process and accelerate time-to-market for your products.
As the demand for more complex and miniaturized electronic devices continues to grow, the importance of mastering rigid-flex PCB design will only continue to increase. By staying up-to-date with the latest tools, techniques, and best practices in this field, you can position yourself as a leader in the industry and deliver innovative, high-quality products that meet the evolving needs of your customers.
0 Comments