Printed circuit board (PCB) prototyping is a critical step in the electronics development process. Prototyping allows designers to test concepts, validate functionality, and de-risk technology prior to committing to full production. For companies without specialized in-house capabilities, partnering with an experienced PCB prototyping service provider can accelerate development and improve outcomes. This guide examines key factors to consider when selecting a PCB prototyping partner.
Benefits of Using a Prototyping Service
Partnering with an external prototyping service offers several advantages:
Specialized Expertise
- Access to engineering resources with industry-leading fabrication and assembly capabilities.
- Knowledge to evaluate designs for manufacturability and testability.
- Experience supporting complex layouts and HDI technology.
Advanced Equipment
- Availability of advanced tools like direct imaging systems, high-accuracy lasers, AOI inspection.
- Wide range of assembly technologies from hand soldering to advanced automation.
- Sophisticated test systems to validate performance.
Improved Economics
- Avoid capital investment required for internal prototyping infrastructure.
- Leverage economies of scale across aggregated volumes.
- Reduce labor costs associated with hiring specialized staff.
Accelerated Speed
- Rapid turnaround by eliminating setup time for new capabilities.
- Avoid effort required to qualify new internal processes.
- Priority scheduling services to meet urgent deadlines.
Prototyping Process Steps
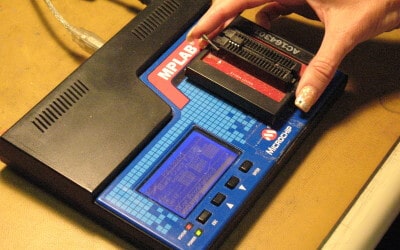
A PCB prototyping service guides each design through the following fundamental steps:
Engineering Design Review
- Evaluate customer design files including schematics, layouts, BOM, etc.
- Provide DFM recommendations to optimize manufacturability.
- Resolve any identified issues prior to build.
Prototype Fabrication
- Produce high-quality PCBs meeting specifications using fabrication technologies like photolithography, laser direct imaging, etching, AOI.
- Offer wide range of options for layers, materials, finishes, tolerances, impedances.
Circuit Assembly
- Precisely place and solder components onto boards by hand or using automated pick-and-place and reflow.
- Manage procurement for BOM components.
- Inspect assemblies for defects using microscopy and x-ray.
Testing and Validation
- Functionally test boards using flying probe, in-circuit test, or customer-provided vectors.
- Perform environmental stress screening including burn-in and thermal cycling.
- Evaluate signal integrity, EMI, and other electrical performance characteristics.
Documentation
- Provide thorough reporting with test data, inspection results, build photos, and other details.
- Archive design data and prototypes for future modifications or reproductions.
Delivery
- Carefully package prototypes to prevent damage in shipping.
- Offer express turnaround to meet urgent schedules.
Capabilities to Look For
When vetting PCB prototyping partners, seek providers offering the following key capabilities:
- Engineering expertise – skilled resources available for design reviews and recommendations from concept through testing.
- Wide range of fabrication capabilities – technology agnostic approach using combination of photoimageable ink, laser direct imaging, photolithography, to meet needs.
- Assembly technology – manual assembly, automated SMT lines, and combinations to optimize each build.
- Comprehensive testing services – bare board testing, flying probe, boundary scan, AOI, x-ray, fixture testing, environmental stress screening.
- Flexible order quantities – ability to support builds from 1-100 boards with rapid turnaround.
- ITAR compliance – required for defense-related designs with export controls.
- Strong quality systems – ISO 9001 or AS9100 certification indicates well-controlled processes.
- Trust and security – protection of intellectual property and customer data integrity.
Selecting a Prototyping Partner
When researching circuit board prototyping providers, consider the following criteria:
Technical Expertise
- Experience specific to your application area or industry.
- Engineering depth to support complex layouts and next-gen technologies.
- Knowledge of emerging standards, equipment, and processes.
Quality Processes
- Consistency and precision achievable across sequential prototype revisions.
- Well-defined quality control procedures at all process steps.
- Track record of delivering highyielding, high-reliability prototypes.
Range of Offerings
- Assess breadth of in-house services vs. reliance on external partners.
- Availability of advanced technologies like HDI, RF, or mixed signal.
- Flexibility to handle low to mid-volume production.
Customer Service
- Responsiveness to requests for quotes, engineering inquiries, and urgent needs.
- Willingness to partner on design reviews and participative problem solving.
- Protecting confidentiality of intellectual property and data.
Pricing
- Competitive pricing reflective of total value delivered.
- Clear breakdown of NRE and per board costs.
- Flexible budgetary options from fixed-price to time and materials models.
Establishing an Effective Partnership
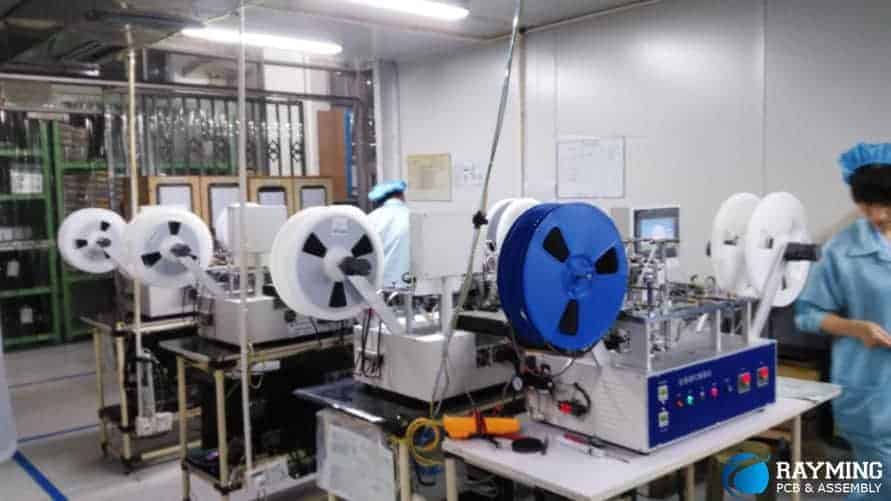
To maximize success, effective communication and collaboration between designer and prototyping partner is essential. Recommended practices include:
- Engage early in the design cycle for greatest impact, not just prior to build.
- Maintain ongoing dialog, particularly with engineering contacts.
- Clearly document all specifications, requirements, and acceptance criteria.
- Review milestone progress together.
- Establish change management procedures.
- Celebrate successes and jointly resolve issues.
With robust processes on both sides, PCB prototyping services help accelerate time-to-market and reduce overall development risk.
Frequently Asked Questions
What are the main benefits of outsourcing versus building prototypes internally?
The principal benefits of outsourcing prototyping include:
- Access to advanced specialized equipment without capital investment
- Availability of skilled technical expertise
- Improved economics from economies of scale
- Accelerated turnaround time
- Allowing internal teams to focus on design vs. production
What minimum information does the prototyping provider need?
At a minimum, the provider needs:
- Complete schematics indicating all components
- PCB layout gerber files
- Bill of materials detailing all component values
- Layer stackup cross-section
- Any special fabrication specifications
- Preferred target quantity and delivery timeframe
What types of testing services should be utilized?
Common testing services to consider include:
- Netlist testing of bare boards
- Flying probe electrical testing
- Boundary scan for digital logic
- X-ray inspection of solder joints
- Functional validation to application requirements
- Environmental stress screening
How many prototype iterations are typical?
Most projects require 2-4 prototype iterations to verify the design, uncover issues, refine the implementation, and qualify manufacturing processes prior to starting production. Complex projects may require more iterations.
At what point does it make sense to transition from prototyping to production?
The transition point depends on the maturity of the design and confidence in meeting all specifications. For simple designs, the handoff may occur after 1-2 prototypes. For complex projects, production may only start after 4+ prototype iterations and comprehensive qualification testing is complete.
0 Comments