Introduction to Glass Transition Temperature (Tg)
Glass Transition Temperature (Tg) is a crucial property for materials used in the manufacturing of Printed Circuit Boards (PCBs). It is the temperature at which a material transitions from a hard, glassy state to a soft, rubbery state. This transition is characterized by a significant change in the material’s mechanical and electrical properties, making it essential for designers and manufacturers to understand and consider when selecting materials for PCB Production.
What is a Printed Circuit Board (PCB)?
A Printed Circuit Board (PCB) is a fundamental component in modern electronics. It is a flat board made of insulating materials, such as fiberglass or composite epoxy, with conductive pathways etched or printed onto its surface. These pathways, called traces, connect various electronic components, such as resistors, capacitors, and integrated circuits, to form a functional electronic device.
PCBs are used in a wide range of applications, from consumer electronics like smartphones and laptops to industrial equipment, automotive systems, and aerospace technology. They offer several advantages over traditional point-to-point wiring, including:
- Compact size and reduced weight
- Improved reliability and consistency
- Ease of mass production
- Enhanced signal integrity and reduced electromagnetic interference (EMI)
The Importance of Glass Transition Temperature (Tg) in PCB Materials
The Glass Transition Temperature (Tg) of a PCB material is a critical factor in determining its suitability for a given application. Materials with a higher Tg are generally more stable and less prone to deformation or degradation under high-temperature conditions. This is particularly important for PCBs used in harsh environments, such as automotive or aerospace applications, where exposure to elevated temperatures is common.
On the other hand, materials with a lower Tg may be more flexible and easier to work with during the manufacturing process. They may also be less expensive than high-Tg materials. However, their reduced thermal stability can lead to issues such as warping, delamination, or reduced performance over time.
Common PCB Materials and Their Glass Transition Temperatures
There are several materials commonly used in the production of PCBs, each with its own set of properties and Glass Transition Temperatures. Some of the most widely used materials include:
FR-4
FR-4 is a composite material consisting of a fiberglass cloth impregnated with an epoxy resin. It is the most widely used PCB material due to its excellent balance of mechanical, electrical, and thermal properties. FR-4 has a Glass Transition Temperature ranging from 130°C to 180°C, depending on the specific formulation and manufacturing process.
Property | Value |
---|---|
Dielectric Constant (at 1 MHz) | 4.5 – 4.7 |
Dissipation Factor (at 1 MHz) | 0.02 – 0.03 |
Thermal Conductivity | 0.3 – 0.4 W/m·K |
Coefficient of Thermal Expansion (CTE) | 12 – 16 ppm/°C |
Glass Transition Temperature (Tg) | 130°C – 180°C |
Polyimide
Polyimide is a high-performance polymer known for its excellent thermal stability, chemical resistance, and mechanical strength. It is often used in applications that require operation at elevated temperatures or exposure to harsh environmental conditions. Polyimide has a Glass Transition Temperature ranging from 260°C to 400°C, depending on the specific formulation.
Property | Value |
---|---|
Dielectric Constant (at 1 MHz) | 3.2 – 3.5 |
Dissipation Factor (at 1 MHz) | 0.002 – 0.003 |
Thermal Conductivity | 0.1 – 0.2 W/m·K |
Coefficient of Thermal Expansion (CTE) | 20 – 30 ppm/°C |
Glass Transition Temperature (Tg) | 260°C – 400°C |
PTFE (Polytetrafluoroethylene)
PTFE, also known by the brand name Teflon, is a fluoropolymer with exceptional dielectric properties, low dissipation factor, and high thermal stability. It is often used in high-frequency applications, such as radar systems and microwave circuits. PTFE has a Glass Transition Temperature around 115°C to 130°C.
Property | Value |
---|---|
Dielectric Constant (at 1 MHz) | 2.1 – 2.3 |
Dissipation Factor (at 1 MHz) | 0.0002 – 0.0004 |
Thermal Conductivity | 0.2 – 0.3 W/m·K |
Coefficient of Thermal Expansion (CTE) | 100 – 200 ppm/°C |
Glass Transition Temperature (Tg) | 115°C – 130°C |
Rogers Materials (e.g., RO4003, RO4350B)
Rogers Corporation produces a range of high-performance PCB materials designed for demanding applications, such as high-frequency communications and aerospace systems. These materials offer excellent dielectric properties, low loss, and controlled thermal expansion. The Glass Transition Temperature of Rogers materials varies depending on the specific product, but typically ranges from 280°C to 330°C.
Property | RO4003 | RO4350B |
---|---|---|
Dielectric Constant (at 10 GHz) | 3.38 | 3.48 |
Dissipation Factor (at 10 GHz) | 0.0027 | 0.0037 |
Thermal Conductivity | 0.71 W/m·K | 0.62 W/m·K |
Coefficient of Thermal Expansion (CTE) | 11 ppm/°C | 30 ppm/°C |
Glass Transition Temperature (Tg) | >280°C | >280°C |
Factors Affecting Glass Transition Temperature (Tg) in PCB Materials
Several factors can influence the Glass Transition Temperature of PCB materials, including:
Chemical Composition
The chemical composition of a PCB material, particularly the type and proportion of resin and reinforcement used, has a significant impact on its Tg. Different resins, such as epoxy, polyimide, or PTFE, have inherently different Glass Transition Temperatures. The addition of fillers, modifiers, or other additives can also alter the Tg of the material.
Manufacturing Process
The manufacturing process used to produce a PCB material can affect its Glass Transition Temperature. Factors such as the curing temperature, pressure, and duration can influence the degree of crosslinking in the resin, which in turn affects the Tg. Variations in the manufacturing process can lead to inconsistencies in the Tg of the final product.
Environmental Conditions
Exposure to environmental conditions, such as temperature, humidity, and chemical agents, can impact the Glass Transition Temperature of a PCB material over time. Prolonged exposure to high temperatures or moisture can lead to degradation of the resin, resulting in a decrease in Tg. Chemical exposure can also cause changes in the material’s structure, affecting its thermal and mechanical properties.
Aging and Thermal History
The aging and thermal history of a PCB material can influence its Glass Transition Temperature. Repeated thermal cycling, exposure to elevated temperatures, or long-term storage can cause changes in the material’s structure and properties. These changes can result in a shift in the Tg, either increasing or decreasing depending on the specific material and conditions.
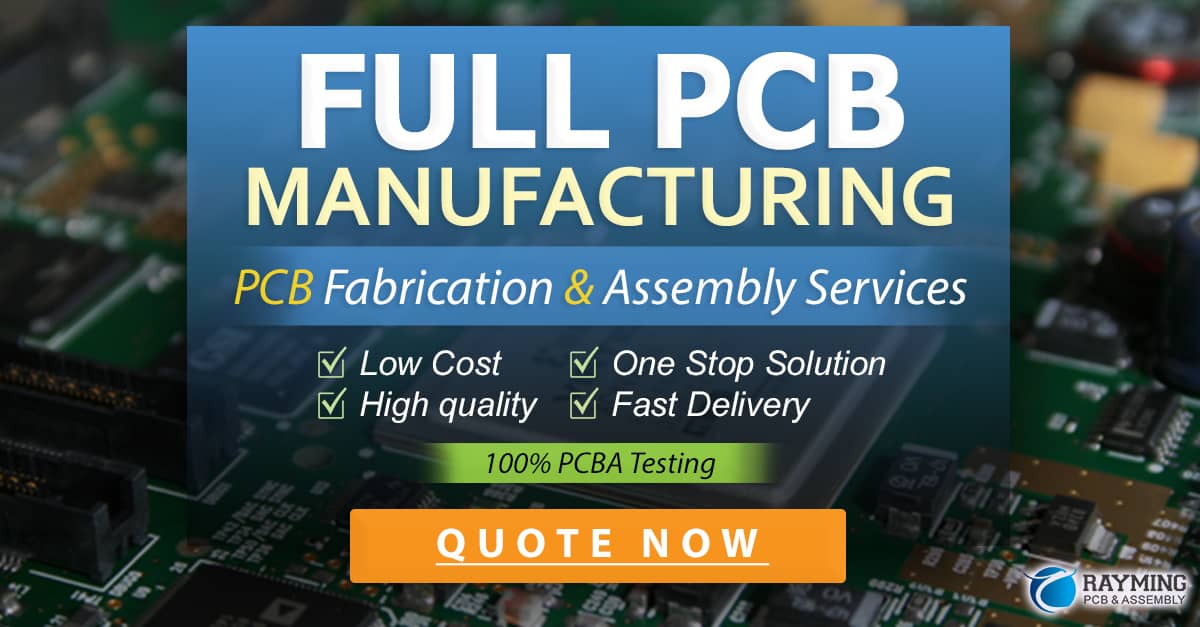
Measuring Glass Transition Temperature (Tg) in PCB Materials
There are several methods used to measure the Glass Transition Temperature of PCB materials, including:
Differential Scanning Calorimetry (DSC)
Differential Scanning Calorimetry (DSC) is a widely used technique for measuring the Tg of polymeric materials, including PCB substrates. In this method, a small sample of the material is heated at a controlled rate while the heat flow into or out of the sample is measured. The Tg is identified as a step change in the heat flow curve, indicating a change in the material’s heat capacity.
Thermomechanical Analysis (TMA)
Thermomechanical Analysis (TMA) is another method for determining the Tg of PCB materials. In this technique, a sample is subjected to a constant mechanical load while being heated at a controlled rate. The Tg is identified as a change in the sample’s dimensional stability, typically a sharp increase in the coefficient of thermal expansion (CTE).
Dynamic Mechanical Analysis (DMA)
Dynamic Mechanical Analysis (DMA) is a technique that measures the mechanical properties of a material as a function of temperature. A sample is subjected to a sinusoidal mechanical stress while being heated at a controlled rate. The Tg is identified as a peak in the tan delta curve, which represents the ratio of the loss modulus to the storage modulus of the material.
Designing PCBs with Glass Transition Temperature (Tg) in Mind
When designing PCBs, it is crucial to consider the Glass Transition Temperature of the materials being used and how it relates to the intended application and operating environment. Some key considerations include:
Selecting the Appropriate Material
Choose a PCB material with a Tg that is suitable for the expected operating temperature range and environmental conditions of the application. For example, high-temperature applications may require materials with a higher Tg, such as polyimide or certain Rogers materials, while less demanding applications may be able to use lower-cost materials like FR-4.
Thermal Management
Design the PCB with proper thermal management in mind, including the use of heat sinks, thermal vias, and other techniques to dissipate heat and prevent localized hot spots. This can help to minimize the risk of the PCB material reaching or exceeding its Tg, which could lead to deformation or failure.
Dimensional Stability
Consider the coefficient of thermal expansion (CTE) of the PCB material in relation to the Tg. Materials with a higher Tg generally have a lower CTE, which can help to maintain dimensional stability over a wider temperature range. This is particularly important for applications with tight tolerances or high-density components.
Manufacturing Process Optimization
Work closely with the PCB manufacturer to optimize the production process for the specific material being used. This may involve adjusting parameters such as the curing temperature, pressure, and duration to ensure that the material achieves its desired Tg and other properties consistently.
Frequently Asked Questions (FAQ)
- What is the difference between Glass Transition Temperature (Tg) and Melting Temperature (Tm)?
-
Glass Transition Temperature (Tg) is the temperature at which a material transitions from a hard, glassy state to a soft, rubbery state. Melting Temperature (Tm) is the temperature at which a material transitions from a solid to a liquid state. Tg occurs before Tm and is a reversible process, while melting is an irreversible phase change.
-
How does the Glass Transition Temperature (Tg) affect the performance of a PCB?
-
The Tg of a PCB material determines its thermal stability and ability to maintain its mechanical and electrical properties at elevated temperatures. Materials with a higher Tg are less prone to deformation, warping, or degradation when exposed to high temperatures, making them more suitable for demanding applications.
-
Can the Glass Transition Temperature (Tg) of a PCB material change over time?
-
Yes, the Tg of a PCB material can change over time due to factors such as aging, thermal history, and environmental exposure. Prolonged exposure to high temperatures, moisture, or chemical agents can cause changes in the material’s structure, leading to a shift in its Tg.
-
What are some common methods for measuring the Glass Transition Temperature (Tg) of PCB materials?
-
Common methods for measuring the Tg of PCB materials include Differential Scanning Calorimetry (DSC), Thermomechanical Analysis (TMA), and Dynamic Mechanical Analysis (DMA). Each technique measures different properties of the material to identify the Tg, such as changes in heat capacity, dimensional stability, or mechanical properties.
-
How do I choose the right PCB material based on its Glass Transition Temperature (Tg)?
- When selecting a PCB material based on its Tg, consider the intended application and operating environment. High-temperature applications or harsh environments may require materials with a higher Tg, such as polyimide or certain Rogers materials. Less demanding applications may be able to use lower-cost materials like FR-4. It is essential to consult with the PCB manufacturer and material suppliers to determine the most suitable material for a given application.
Conclusion
Glass Transition Temperature (Tg) is a crucial property for materials used in the manufacturing of Printed Circuit Boards (PCBs). It determines the temperature at which a material transitions from a hard, glassy state to a soft, rubbery state, and significantly impacts the material’s mechanical and electrical properties. Understanding and considering the Tg of PCB materials is essential for designers and manufacturers to ensure the reliability, performance, and longevity of electronic devices.
Common PCB materials, such as FR-4, polyimide, PTFE, and Rogers materials, exhibit a wide range of Glass Transition Temperatures, each with its own set of advantages and limitations. Factors such as chemical composition, manufacturing process, environmental conditions, and aging can influence the Tg of these materials.
When designing PCBs, it is crucial to select materials with a Tg that is suitable for the intended application and operating environment. Proper thermal management, dimensional stability, and manufacturing process optimization should also be considered to ensure the best possible performance and reliability of the final product.
By understanding the importance of Glass Transition Temperature in PCB materials and designing with this property in mind, engineers and manufacturers can create more robust, reliable, and high-performance electronic devices that can withstand the demands of today’s increasingly complex applications.
0 Comments