What is PCB Stackup?
PCB stackup refers to the arrangement of layers within a multi-layer printed circuit board. It involves the strategic placement of conductive layers, insulating layers, and various materials to ensure optimal electrical performance, signal integrity, and mechanical stability. A well-designed PCB stackup is crucial for the proper functioning and reliability of complex electronic devices.
The Anatomy of a Multi-Layer PCB
A typical multi-layer PCB consists of the following components:
-
Conductive layers: These are the layers that carry electrical signals and power. They are usually made of copper and can be either signal layers or power/ground planes.
-
Insulating layers: Also known as dielectric layers, these are the non-conductive layers that separate the conductive layers. They provide electrical isolation and help maintain signal integrity.
-
Prepreg (pre-impregnated) layers: These are thin sheets of fiberglass impregnated with a partially cured resin. They are used to bond the conductive and insulating layers together during the lamination process.
-
Solder mask: This is a protective coating applied to the outer layers of the PCB to prevent short circuits and provide insulation.
-
Silkscreen: This is a printed layer on top of the solder mask that contains text, logos, and component outlines for easy identification and assembly.
Benefits of Multi-Layer PCBs
Multi-layer PCBs offer several advantages over single-layer or double-layer boards:
-
Increased component density: With multiple layers, designers can accommodate more components and complex circuitry in a smaller footprint.
-
Improved signal integrity: By separating signal layers with ground and power planes, multi-layer PCBs can reduce crosstalk, electromagnetic interference (EMI), and signal reflections.
-
Enhanced power distribution: Dedicated power and ground planes provide low-impedance paths for power distribution, minimizing voltage drops and ensuring stable power delivery to components.
-
Better thermal management: Multi-layer PCBs can dissipate heat more effectively by incorporating thermal vias and distributing heat across multiple layers.
-
Mechanical stability: The laminated structure of multi-layer PCBs provides increased mechanical strength and rigidity, making them more resistant to vibration and physical stress.
Designing a PCB Stackup
Creating an effective PCB stackup requires careful consideration of various factors, including the number of layers, the arrangement of signal and power/ground layers, the selection of materials, and the manufacturing process. Let’s explore these aspects in more detail.
Determining the Number of Layers
The number of layers in a PCB stackup depends on the complexity of the circuit, the required component density, and the desired performance characteristics. A typical multi-layer PCB can have anywhere from 4 to 16 layers, although some high-end applications may require even more. The decision to use a specific number of layers should be based on a thorough analysis of the circuit requirements and a balance between cost and performance.
Signal Layer Arrangement
The arrangement of signal layers in a PCB stackup is crucial for maintaining signal integrity and minimizing crosstalk. Some common practices include:
-
Alternating signal layers: Signal layers are placed on opposite sides of a power or ground plane to minimize crosstalk between adjacent signal traces.
-
Orthogonal routing: Signal traces on adjacent layers are routed perpendicular to each other to reduce electromagnetic coupling.
-
Stripline and microstrip: Stripline traces are sandwiched between two ground planes, while microstrip traces are placed on the outer layers with a single ground plane beneath them. These configurations help control impedance and reduce EMI.
Power and Ground Planes
Dedicated power and ground planes serve several important functions in a multi-layer PCB:
-
Low-impedance power distribution: By providing a continuous and uninterrupted path for power, these planes ensure stable voltage levels across the board.
-
Reduced EMI: Power and ground planes act as shields, reducing electromagnetic interference between signal layers.
-
Improved signal integrity: By providing a consistent reference plane for signals, power and ground planes help maintain signal quality and minimize reflections.
Material Selection
The choice of materials for a PCB stackup depends on the electrical, thermal, and mechanical requirements of the application. Some common materials include:
-
FR-4: A flame-retardant glass-reinforced epoxy laminate, widely used for its good electrical and mechanical properties, and low cost.
-
High-frequency laminates: Materials like Rogers RO4000 series or Isola I-Tera MT40 offer superior high-frequency performance and low dielectric loss for applications like RF and microwave circuits.
-
Metal-core PCBs: These incorporate a metal core (usually aluminum) for enhanced thermal dissipation in power-dense applications.
-
Flexible PCBs: Made with flexible substrates like polyimide, these PCBs can bend and conform to various shapes, making them suitable for wearable electronics and space-constrained designs.
Manufacturing Considerations
The manufacturing process for multi-layer PCBs involves several steps, including:
-
Layer stackup design: The arrangement of layers and materials is defined in a stackup diagram, which specifies the thickness, material type, and copper weight for each layer.
-
Layer fabrication: Each conductive layer is patterned using photolithography and etching processes.
-
Lamination: The layers are aligned, stacked, and bonded together under high pressure and temperature using prepreg layers.
-
Drilling and plating: Holes are drilled through the board for vias and component mounting, and then plated with copper to establish electrical connections between layers.
-
Solder mask and silkscreen application: The outer layers are coated with a solder mask and printed with a silkscreen for component placement and identification.
Designers must work closely with PCB manufacturers to ensure that the stackup design is compatible with the chosen fabrication process and meets the required tolerances and specifications.
Best Practices for PCB Stackup Design
To create a reliable and high-performance multi-layer PCB, designers should follow these best practices:
-
Plan the stackup early: Consider the stackup design from the beginning of the project, taking into account the circuit requirements, component placement, and routing constraints.
-
Use a symmetrical stackup: A symmetrical arrangement of layers helps balance the mechanical stress and prevent warping during the manufacturing process.
-
Minimize the number of layers: Use the minimum number of layers required to achieve the desired functionality and performance, as additional layers increase cost and complexity.
-
Provide adequate spacing: Ensure sufficient spacing between signal traces, components, and vias to minimize crosstalk and interference.
-
Control impedance: Use controlled-impedance design techniques, such as adjusting trace width and dielectric thickness, to maintain consistent impedance throughout the board.
-
Optimize power distribution: Place power and ground planes close to the components they serve to minimize voltage drops and ensure stable power delivery.
-
Use ground planes effectively: Incorporate ground planes between signal layers to provide shielding and reduce EMI.
-
Consider thermal management: Use thermal vias and metal-core substrates to dissipate heat from power-dense components and prevent overheating.
-
Collaborate with manufacturers: Work closely with PCB manufacturers to ensure that the stackup design is feasible and optimized for the chosen fabrication process.
-
Perform simulations and testing: Use electromagnetic simulation tools to analyze signal integrity, power distribution, and thermal performance, and conduct thorough testing to validate the design before production.
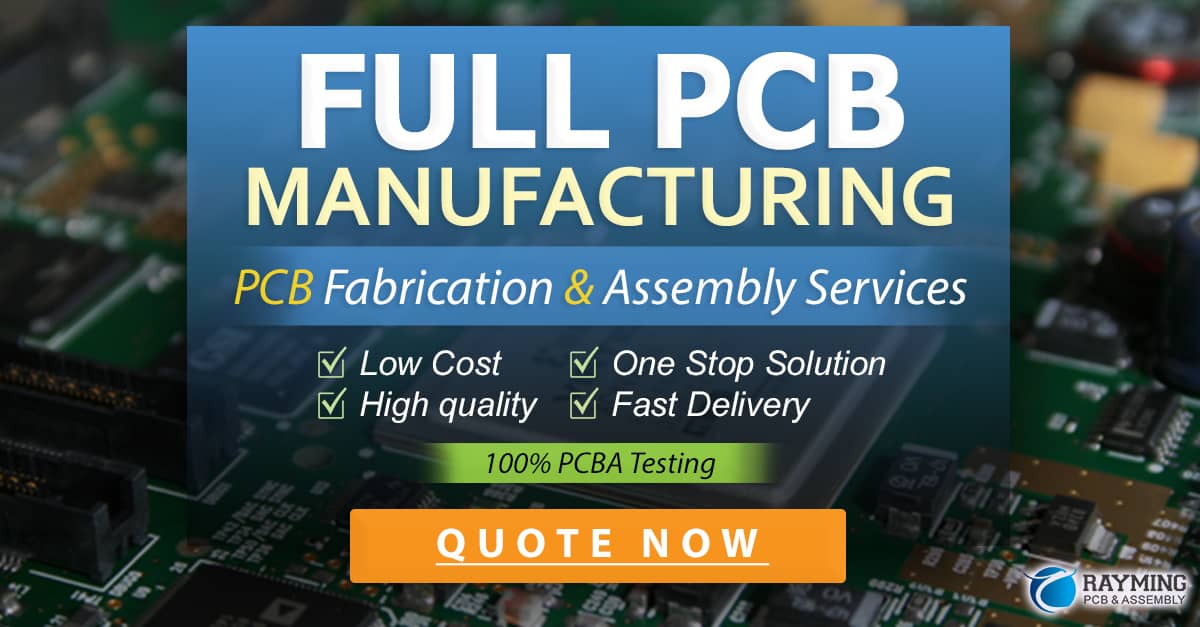
Conclusion
PCB stackup is a critical aspect of designing multi-layer circuits for complex electronic devices. By understanding the principles of layer arrangement, material selection, and manufacturing processes, designers can create PCBs that deliver optimal performance, reliability, and cost-effectiveness. As technology continues to advance, the importance of well-designed PCB stackups will only grow, enabling the development of increasingly sophisticated and compact electronic systems.
Frequently Asked Questions (FAQ)
-
What is the difference between a single-layer and a multi-layer PCB?
A single-layer PCB has only one conductive layer, while a multi-layer PCB has two or more conductive layers separated by insulating layers. Multi-layer PCBs offer higher component density, better signal integrity, and improved power distribution compared to single-layer boards. -
How do I determine the number of layers needed for my PCB?
The number of layers required depends on factors such as the complexity of the circuit, the number and type of components, the required signal integrity, and the available space. Designers should carefully analyze these factors and consult with PCB manufacturers to determine the optimal number of layers for their specific application. -
What materials are commonly used in PCB stackups?
Common materials used in PCB stackups include FR-4 (a flame-retardant glass-reinforced epoxy laminate), high-frequency laminates like Rogers RO4000 series or Isola I-Tera MT40, metal-core substrates for enhanced thermal dissipation, and flexible substrates like polyimide for flexible PCBs. -
How does the arrangement of signal layers affect PCB performance?
The arrangement of signal layers in a PCB stackup is crucial for maintaining signal integrity and minimizing crosstalk. Best practices include alternating signal layers on opposite sides of power or ground planes, using orthogonal routing for adjacent layers, and employing stripline or microstrip configurations to control impedance and reduce EMI. -
What are some best practices for designing a reliable and high-performance PCB stackup?
Some best practices for PCB stackup design include planning the stackup early, using a symmetrical arrangement of layers, minimizing the number of layers, providing adequate spacing between components and traces, controlling impedance, optimizing power distribution, using ground planes effectively, considering thermal management, collaborating with manufacturers, and performing simulations and testing to validate the design.
0 Comments