What is a PCB Inductor?
A PCB inductor, also known as a printed circuit board inductor, is a passive electronic component that stores energy in a magnetic field when an electric current flows through it. It consists of a coil of conductive material, usually copper, wound around a core or formed into a specific pattern on a PCB. Inductors are essential components in various electronic circuits, such as filters, oscillators, and power supplies.
Key Characteristics of PCB Inductors
-
Inductance: The primary characteristic of an inductor is its inductance, measured in henries (H). Inductance represents the inductor’s ability to store energy in its magnetic field.
-
Quality Factor (Q): The quality factor is a measure of an inductor’s efficiency. It is the ratio of the inductor’s reactance to its resistance at a given frequency. Higher Q values indicate lower losses and better performance.
-
Self-Resonant Frequency (SRF): The self-resonant frequency is the frequency at which the inductor’s capacitance cancels out its inductance, causing the inductor to behave like a resistor. It is important to choose an inductor with an SRF higher than the operating frequency of the circuit.
-
Current Rating: The current rating specifies the maximum current that can flow through the inductor without causing damage or significant performance degradation.
-
DC Resistance (DCR): The DC resistance is the resistance of the inductor’s winding material to direct current. Lower DCR values result in lower power losses and better efficiency.
Methods of Computing Inductance Value
There are several methods for computing the inductance value of a PCB inductor, depending on its geometry and construction. Here are some common methods:
1. Inductance Formulas for Simple Geometries
For simple inductor geometries, such as straight wire or circular loop inductors, the inductance can be calculated using closed-form equations.
Straight Wire Inductor
The inductance of a straight wire inductor can be approximated using the following formula:
L = (μ₀ × l / (2π)) × [ln(2l / r) – 0.75]
Where:
– L is the inductance in henries (H)
– μ₀ is the permeability of free space (4π × 10⁻⁷ H/m)
– l is the length of the wire in meters (m)
– r is the radius of the wire in meters (m)
Circular Loop Inductor
The inductance of a circular loop inductor can be calculated using the following formula:
L = μ₀ × r × [ln(8r / a) – 2]
Where:
– L is the inductance in henries (H)
– μ₀ is the permeability of free space (4π × 10⁻⁷ H/m)
– r is the radius of the loop in meters (m)
– a is the radius of the wire in meters (m)
2. Inductance Calculation for Complex Geometries
For more complex inductor geometries, such as spiral or meander inductors, closed-form equations become less accurate. In these cases, numerical methods or simulation tools are used to compute the inductance value.
Greenhouse Method
The Greenhouse method is a widely used analytical approach for calculating the inductance of planar spiral inductors. It considers the inductor as a series of concentric circular rings and calculates the total inductance by summing the self-inductance of each ring and the mutual inductance between pairs of rings.
The self-inductance of each ring is given by:
L_self = μ₀ × r × [ln(8r / w) – 0.5 + (w / (24r))]
Where:
– L_self is the self-inductance of the ring in henries (H)
– μ₀ is the permeability of free space (4π × 10⁻⁷ H/m)
– r is the mean radius of the ring in meters (m)
– w is the width of the ring in meters (m)
The mutual inductance between two rings is given by:
M = 2 × μ₀ × √(r_i × r_j) × [(1 – k² / 2) × K(k) – E(k)]
Where:
– M is the mutual inductance between rings i and j in henries (H)
– μ₀ is the permeability of free space (4π × 10⁻⁷ H/m)
– r_i and r_j are the mean radii of rings i and j, respectively, in meters (m)
– k is the coupling coefficient, given by k² = 4 × r_i × r_j / [(r_i + r_j)² + d²]
– d is the center-to-center distance between rings i and j in meters (m)
– K(k) and E(k) are complete elliptic integrals of the first and second kind, respectively
The total inductance of the spiral inductor is then calculated by summing the self-inductances and mutual inductances:
L_total = ∑L_self + ∑∑M
Simulation Tools
For highly complex inductor geometries or when considering the effects of the PCB substrate and other components, electromagnetic simulation tools like Ansys HFSS, Keysight ADS, or Sonnet Software can provide accurate inductance values. These tools use numerical methods, such as the finite element method (FEM) or the method of moments (MoM), to solve Maxwell’s equations and calculate the inductance based on the inductor’s geometry and surrounding environment.
Factors Affecting PCB Inductor Performance
Several factors can affect the performance of PCB inductors:
-
Geometry: The inductor’s shape, size, and number of turns directly influence its inductance value and Q factor. Optimizing the geometry can help achieve the desired inductance while minimizing losses.
-
Material Properties: The choice of materials for the inductor’s winding and core significantly impacts its performance. Using high-conductivity materials like copper for the winding and high-permeability materials for the core can improve the inductor’s Q factor and reduce losses.
-
Frequency: The inductor’s performance varies with frequency due to skin effect, proximity effect, and self-resonance. It is essential to design the inductor for the intended operating frequency range to ensure optimal performance.
-
PCB Substrate: The PCB substrate’s Dielectric Constant and loss tangent can affect the inductor’s performance. High-frequency substrates with low dielectric constants and loss tangents are preferred for high-performance inductors.
-
Shielding: Electromagnetic interference (EMI) from nearby components can couple with the inductor and degrade its performance. Proper shielding techniques, such as ground planes or Faraday shields, can help mitigate EMI effects.
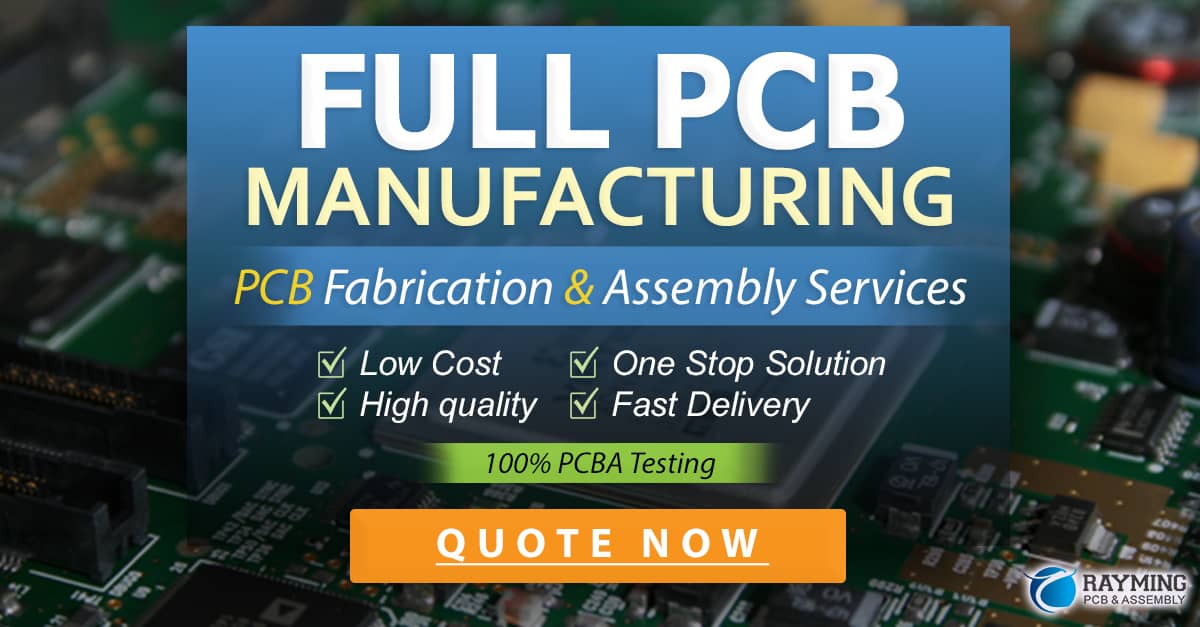
Applications of PCB Inductors
PCB inductors find applications in various electronic circuits, including:
-
Power Supplies: Inductors are used in switching power supplies, such as buck or Boost Converters, to store and release energy, enabling efficient voltage regulation.
-
Filters: Inductors are essential components in filters, such as low-pass, high-pass, or band-pass filters, used to selectively attenuate or pass specific frequency ranges.
-
Oscillators: Inductors are used in LC Oscillators, along with capacitors, to generate sinusoidal signals at a specific resonant frequency.
-
Impedance Matching: Inductors can be used for impedance matching networks to maximize power transfer between stages or to minimize reflections in high-frequency circuits.
-
EMI Suppression: Inductors can be used as chokes to suppress electromagnetic interference (EMI) by blocking high-frequency noise while allowing desired signals to pass through.
FAQ
- What is the difference between an inductor and a transformer?
-
An inductor is a single winding component that stores energy in a magnetic field, while a transformer consists of two or more coupled windings and is used to transfer energy between circuits or change voltage levels.
-
Can I use a PCB inductor for high-current applications?
-
PCB inductors are generally suitable for low to moderate current applications. For high-current applications, wire-wound or ferrite core inductors may be more appropriate due to their higher current handling capacity and lower DC resistance.
-
How does inductor size affect its performance?
-
Generally, larger inductors have higher inductance values and higher Q factors but also have lower self-resonant frequencies and occupy more PCB space. Smaller inductors have lower inductance and Q but can operate at higher frequencies and are suitable for space-constrained designs.
-
What is the purpose of an inductor in a filter circuit?
-
In a filter circuit, inductors are used in combination with capacitors to selectively pass or attenuate specific frequency ranges. For example, in a low-pass filter, the inductor blocks high-frequency signals while allowing low-frequency signals to pass through.
-
How do I choose the right inductor for my application?
- When selecting an inductor, consider the following factors:
- Required inductance value
- Operating frequency range
- Current rating
- Q factor
- Self-resonant frequency
- DC resistance
- PCB space constraints
- Environmental factors (temperature, humidity, etc.)
It is essential to refer to the inductor manufacturer’s datasheet and application notes to ensure the chosen inductor meets the specific requirements of your application.
Conclusion
PCB inductors are essential components in many electronic circuits, providing energy storage, filtering, and impedance matching capabilities. Understanding the key characteristics, methods for computing inductance values, and factors affecting inductor performance is crucial for designing reliable and efficient PCB-based systems.
By selecting the appropriate inductor geometry, materials, and design techniques, engineers can optimize inductor performance for their specific applications. Additionally, using closed-form equations, analytical methods, or simulation tools, engineers can accurately compute the inductance value of PCB inductors, enabling them to make informed design decisions.
As electronic systems continue to evolve and push the boundaries of performance, the development of advanced PCB inductor designs and materials will play a vital role in enabling the next generation of innovative and efficient electronic devices.
0 Comments