What is PCB Manufacturing?
PCB manufacturing is the process of creating printed circuit boards (PCBs) that are used in various electronic devices. PCBs are the backbone of modern electronics, providing a platform for electronic components to be mounted and interconnected. The manufacturing process involves several steps, including design, fabrication, assembly, and testing.
PCB Design
The first step in PCB manufacturing is the design phase. This involves creating a schematic diagram and a layout of the PCB using specialized software. The schematic diagram shows the electrical connections between components, while the layout shows the physical placement of components on the board. The design must take into account factors such as signal integrity, power distribution, and thermal management.
PCB Fabrication
Once the design is complete, the next step is fabrication. This involves creating the physical PCB using a variety of processes, including:
- Etching: The copper layer on the PCB is selectively removed to create the desired circuit pattern.
- Drilling: Holes are drilled into the PCB to allow for the mounting of components and the creation of vias (connections between layers).
- Plating: The holes and exposed copper areas are plated with a conductive material, such as copper or gold, to improve conductivity and protect against corrosion.
- Solder Mask Application: A protective layer is applied to the PCB to prevent short circuits and protect against environmental factors.
- Silkscreen Printing: Labels and other markings are printed on the PCB to aid in assembly and identification.
PCB Assembly
After the PCB is fabricated, the next step is assembly. This involves mounting the electronic components onto the board and soldering them in place. There are two main methods of PCB assembly:
- Through-Hole Assembly: Components with long leads are inserted through holes in the PCB and soldered in place on the opposite side.
- Surface Mount Assembly: Components with short leads or no leads are placed directly onto pads on the surface of the PCB and soldered in place.
PCB Testing
The final step in PCB manufacturing is testing. This involves verifying that the PCB functions as intended and meets all specified requirements. Testing can include:
- Visual Inspection: The PCB is visually inspected for defects such as incorrect component placement, solder bridges, or damaged components.
- Automated Optical Inspection (AOI): An automated system uses cameras and image processing software to detect defects on the PCB.
- In-Circuit Testing (ICT): The PCB is connected to a test fixture that applies electrical signals to various points on the board to verify functionality.
- Functional Testing: The PCB is tested in its final application to ensure that it performs as expected.
Types of PCBs
There are several types of PCBs, each with its own unique characteristics and applications. The most common types of PCBs are:
Single-Sided PCBs
Single-sided PCBs have components and traces on only one side of the board. They are the simplest and cheapest type of PCB, but they have limitations in terms of circuit complexity and density.
Double-Sided PCBs
Double-sided PCBs have components and traces on both sides of the board, allowing for more complex circuits and higher component density. They require additional fabrication steps, such as drilling and plating, to create connections between the two sides.
Multi-Layer PCBs
Multi-layer PCBs have multiple layers of copper traces separated by insulating material. They allow for even higher circuit complexity and density than double-sided PCBs, but they are more expensive and difficult to manufacture.
Flexible PCBs
Flexible PCBs are made from flexible materials, such as polyimide, that allow the board to bend and flex without breaking. They are commonly used in applications where space is limited or where the PCB needs to conform to a specific shape.
Rigid-Flex PCBs
Rigid-flex PCBs combine rigid and flexible sections on the same board. The rigid sections provide stability and support for components, while the flexible sections allow the board to bend and fold as needed.
PCB Manufacturing Materials
PCBs are made from a variety of materials, each with its own unique properties and benefits. The most common PCB materials are:
FR-4
FR-4 is a glass-reinforced epoxy laminate that is the most widely used material for PCBs. It has good mechanical and electrical properties, as well as excellent heat resistance and dimensional stability.
Polyimide
Polyimide is a high-performance polymer that is used in flexible PCBs and high-temperature applications. It has excellent thermal and chemical resistance, as well as good electrical properties.
CEM-1
CEM-1 is a composite material made from cotton paper and epoxy resin. It is a lower-cost alternative to FR-4 for less demanding applications.
Aluminum
Aluminum PCBs are used in high-power applications where heat dissipation is a concern. The aluminum substrate provides excellent thermal conductivity and helps to keep components cool.
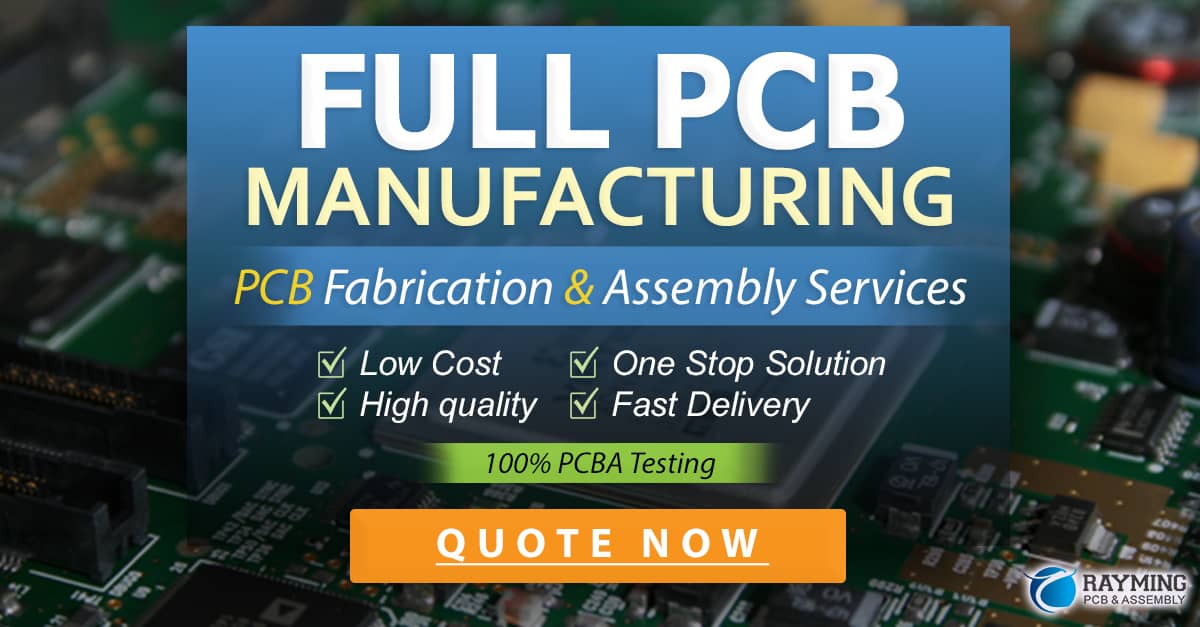
PCB Manufacturing Process Flow
The PCB manufacturing process involves several steps, each of which is critical to the quality and reliability of the final product. The typical process flow for PCB manufacturing is as follows:
- Design: The PCB is designed using specialized software, taking into account factors such as component placement, signal integrity, and power distribution.
- Fabrication: The physical PCB is created using processes such as etching, drilling, plating, and solder mask application.
- Assembly: Electronic components are mounted onto the PCB and soldered in place using either through-hole or surface mount assembly methods.
- Testing: The assembled PCB is tested for functionality and defects using methods such as visual inspection, automated optical inspection, in-circuit testing, and functional testing.
- Finishing: The PCB may undergo additional finishing processes, such as conformal coating or potting, to protect against environmental factors and improve reliability.
PCB Manufacturing Standards
PCB manufacturing is subject to various standards and regulations to ensure quality and reliability. Some of the most important PCB manufacturing standards are:
IPC Standards
The IPC (Association Connecting Electronics Industries) is a global trade association that develops standards for the electronics industry. Some of the most important IPC standards for PCB manufacturing include:
- IPC-6012: Qualification and Performance Specification for Rigid Printed Boards
- IPC-A-600: Acceptability of Printed Boards
- IPC-A-610: Acceptability of Electronic Assemblies
UL Standards
Underwriters Laboratories (UL) is a global safety certification company that develops standards for the electronics industry. Some of the most important UL standards for PCB manufacturing include:
- UL 94: Standard for Safety of Flammability of Plastic Materials for Parts in Devices and Appliances
- UL 796: Standard for Safety of Printed-Wiring Boards
RoHS Directive
The Restriction of Hazardous Substances (RoHS) Directive is a European Union regulation that restricts the use of certain hazardous substances in electrical and electronic equipment. PCBs manufactured for sale in the EU must comply with RoHS requirements.
Advantages of Using a PCB Manufacturing Service
Using a PCB manufacturing service offers several advantages over in-house PCB fabrication, including:
Expertise
PCB manufacturing services have specialized knowledge and experience in PCB design, fabrication, and assembly. They can provide guidance and support throughout the manufacturing process to ensure the best possible outcome.
Equipment
PCB manufacturing services have access to specialized equipment and facilities that may not be available in-house. This includes high-precision etching and drilling machines, automated assembly lines, and advanced testing equipment.
Cost Savings
Outsourcing PCB manufacturing can be more cost-effective than investing in in-house equipment and personnel. PCB manufacturing services can offer economies of scale and lower material costs due to their high volume of production.
Time Savings
PCB manufacturing services can often produce PCBs faster than in-house fabrication due to their streamlined processes and specialized equipment. This can help to reduce time-to-market and meet tight deadlines.
Quality Control
PCB manufacturing services have rigorous quality control processes in place to ensure that every PCB meets the highest standards of quality and reliability. This includes automated optical inspection, in-circuit testing, and functional testing.
Choosing a PCB Manufacturing Service
When choosing a PCB manufacturing service, there are several factors to consider to ensure the best possible outcome for your project. Some of the most important factors to consider include:
Experience
Look for a PCB manufacturing service with extensive experience in PCB design, fabrication, and assembly. Experienced manufacturers will have a deep understanding of the manufacturing process and can provide valuable guidance and support.
Capabilities
Consider the capabilities of the PCB manufacturing service, including their ability to handle different types of PCBs, such as multi-layer or flexible PCBs. Also consider their ability to meet your specific requirements, such as tight tolerances or high-volume production.
Quality Control
Look for a PCB manufacturing service with robust quality control processes in place. This should include automated optical inspection, in-circuit testing, and functional testing to ensure that every PCB meets the highest standards of quality and reliability.
Turnaround Time
Consider the turnaround time offered by the PCB manufacturing service. Fast turnaround times can be critical for meeting tight deadlines and getting products to market quickly.
Cost
Consider the cost of the PCB manufacturing service, including both the initial cost and any ongoing costs for support and maintenance. Look for a service that offers competitive pricing without compromising on quality or reliability.
Frequently Asked Questions (FAQ)
1. What is the typical turnaround time for PCB manufacturing?
The typical turnaround time for PCB manufacturing depends on several factors, including the complexity of the design, the type of PCB, and the volume of production. In general, simple single-sided or double-sided PCBs can be manufactured in as little as 24-48 hours, while more complex multi-layer or flexible PCBs may take several days or weeks.
2. What is the minimum order quantity for PCB manufacturing?
The minimum order quantity for PCB manufacturing varies depending on the manufacturer and the type of PCB. Some manufacturers may have no minimum order quantity, while others may require a minimum of 5, 10, or even 100 pieces. In general, higher minimum order quantities may be required for more complex or custom PCBs.
3. What file formats are required for PCB manufacturing?
The file formats required for PCB manufacturing depend on the specific manufacturer and their software requirements. In general, the most common file formats for PCB design include Gerber files (RS-274X), ODB++ files, and IPC-2581 files. It is important to check with the manufacturer for their specific file format requirements.
4. How much does PCB Manufacturing Cost?
The cost of PCB manufacturing depends on several factors, including the complexity of the design, the type of PCB, the volume of production, and the turnaround time. In general, simple single-sided or double-sided PCBs may cost as little as a few dollars per piece, while more complex multi-layer or flexible PCBs may cost several hundred dollars or more per piece.
5. What certifications should I look for in a PCB manufacturing service?
When choosing a PCB manufacturing service, it is important to look for certifications that demonstrate their commitment to quality and reliability. Some of the most important certifications to look for include:
- ISO 9001: Quality Management Systems
- IPC-A-600: Acceptability of Printed Boards
- IPC-A-610: Acceptability of Electronic Assemblies
- UL Certification: Safety and Performance Standards
Conclusion
PCB manufacturing is a complex and critical process that requires specialized knowledge, equipment, and processes. Using a PCB manufacturing service can offer several advantages over in-house fabrication, including expertise, equipment, cost savings, time savings, and quality control.
When choosing a PCB manufacturing service, it is important to consider factors such as experience, capabilities, quality control, turnaround time, and cost. By carefully evaluating these factors and choosing a reputable and reliable manufacturer, you can ensure the best possible outcome for your PCB project.
PCB Type | Advantages | Disadvantages |
---|---|---|
Single-Sided | Simple, low cost | Limited complexity and density |
Double-Sided | Higher complexity and density | More expensive, requires additional fabrication steps |
Multi-Layer | Highest complexity and density | Most expensive, difficult to manufacture |
Flexible | Can bend and flex without breaking | Limited component density, more expensive |
Rigid-Flex | Combines rigid and flexible sections | Most complex and expensive to manufacture |
As the demand for electronic devices continues to grow, the importance of PCB manufacturing will only continue to increase. By understanding the PCB manufacturing process, materials, standards, and advantages of using a manufacturing service, you can make informed decisions and ensure the success of your PCB projects.
0 Comments