Understanding the Key Factors in PCB Manufacturing Costs
When it comes to PCB manufacturing, cost is a critical factor for businesses and individuals alike. By understanding the various elements that contribute to PCB manufacturing costs, you can make informed decisions and maximize your cost savings. In this article, we will break down the main components of PCB manufacturing costs and provide insights on how to optimize your expenses.
Key Cost Drivers in PCB Manufacturing
- Raw Materials
- PCB Design Complexity
- Manufacturing Process
- Quality Control and Testing
- Economies of Scale
Raw Materials
The cost of raw materials is a significant factor in PCB manufacturing. The primary materials used in PCB production include:
- Substrate (typically FR-4)
- Copper foil
- Solder mask
- Silkscreen
The price of these materials can fluctuate based on market conditions and supplier availability. To minimize costs, consider the following:
- Opt for standard material sizes and thicknesses
- Choose cost-effective substrate materials that meet your requirements
- Negotiate with suppliers for bulk purchases
PCB Design Complexity
The complexity of your PCB design directly impacts manufacturing costs. More complex designs require additional processing steps, which increase production time and expenses. To optimize your design for cost-effectiveness:
- Minimize the number of layers
- Reduce the number of holes and vias
- Opt for larger component sizes and pitch
- Avoid non-standard shapes and features
Design Complexity | Relative Cost Impact |
---|---|
Simple (1-2 layers) | Low |
Moderate (4-6 layers) | Medium |
Complex (8+ layers) | High |
Manufacturing Process
The manufacturing process itself contributes to the overall cost of PCB production. The main steps include:
- Fabrication
- Assembly
- Finishing
Fabrication involves creating the bare PCB, while assembly focuses on populating the board with components. Finishing includes applying solder mask, silkscreen, and surface finishes. To reduce manufacturing costs:
- Choose standard fabrication techniques
- Opt for machine assembly over manual assembly
- Select cost-effective surface finishes (e.g., HASL instead of ENIG)
Quality Control and Testing
Quality control and testing are essential to ensure the reliability and functionality of your PCBs. However, extensive testing can increase manufacturing costs. To strike a balance:
- Define clear quality standards and acceptance criteria
- Implement statistical process control (SPC) to minimize defects
- Opt for automated testing when possible
- Collaborate with your manufacturer to develop an efficient testing plan
Economies of Scale
Producing PCBs in larger quantities can significantly reduce the per-unit cost. This is due to the fixed costs associated with setup, tooling, and non-recurring engineering (NRE) being spread across more units. To leverage economies of scale:
- Consolidate your PCB designs to maximize panel utilization
- Order in bulk quantities when possible
- Consider long-term agreements with manufacturers for consistent pricing
Strategies for Cost Optimization
Design for Manufacturing (DFM)
Designing your PCBs with manufacturing in mind can help reduce costs and improve production efficiency. DFM principles include:
- Adhering to standard design rules and guidelines
- Minimizing the use of non-standard components
- Optimizing component placement for ease of assembly
- Incorporating testability features
Supplier Selection and Management
Choosing the right PCB manufacturer and managing your supplier relationships can have a significant impact on costs. Consider the following:
- Evaluate multiple suppliers based on capabilities, quality, and pricing
- Establish clear communication channels and expectations
- Regularly review supplier performance and negotiate prices
- Explore offshore manufacturing options for potential cost savings
Inventory Management
Effective inventory management can help reduce costs associated with excess stock and obsolescence. Strategies include:
- Implementing just-in-time (JIT) inventory practices
- Regularly reviewing and adjusting inventory levels based on demand
- Collaborating with suppliers for efficient lead times and delivery schedules
- Utilizing inventory management software for better visibility and control
Case Studies
Company A: Design Optimization
Company A, a consumer electronics manufacturer, redesigned their flagship product’s PCB to reduce complexity and optimize for manufacturing. By consolidating components, reducing the number of layers, and adhering to DFM principles, they achieved a 25% reduction in manufacturing costs without compromising functionality.
Company B: Strategic Sourcing
Company B, an automotive supplier, conducted a comprehensive review of their PCB suppliers and identified opportunities for cost savings. By negotiating long-term agreements, consolidating their supplier base, and leveraging offshore manufacturing, they reduced their PCB procurement costs by 15% while maintaining quality standards.
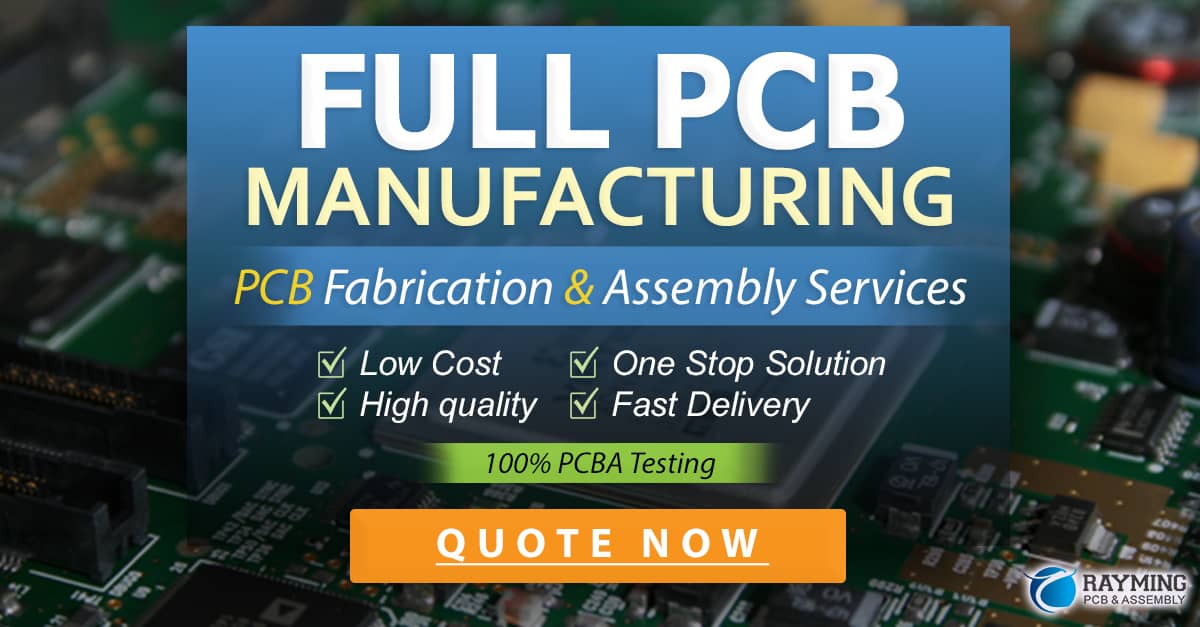
Frequently Asked Questions (FAQ)
-
Q: How can I estimate the cost of my PCB project?
A: To estimate the cost of your PCB project, consider factors such as design complexity, material selection, quantity, and manufacturing process. Many PCB manufacturers offer online quoting tools that can provide a rough estimate based on your specifications. -
Q: What are the most common cost-saving strategies in PCB manufacturing?
A: Common cost-saving strategies include optimizing PCB design for manufacturability, leveraging economies of scale through bulk ordering, selecting cost-effective materials and processes, and implementing efficient inventory management practices. -
Q: How do I balance cost and quality in PCB manufacturing?
A: To balance cost and quality, define clear quality standards and acceptance criteria, collaborate with your manufacturer to develop efficient testing plans, and implement statistical process control (SPC) to minimize defects. Regularly review supplier performance and negotiate prices while maintaining quality expectations. -
Q: What are the benefits of offshore PCB manufacturing?
A: Offshore PCB manufacturing can offer cost savings due to lower labor costs, access to a broader supplier base, and potential economies of scale. However, it is essential to carefully evaluate offshore manufacturers based on their capabilities, quality, and communication to ensure a successful partnership. -
Q: How can I ensure the reliability of my PCBs while controlling costs?
A: To ensure PCB reliability while controlling costs, implement robust design for manufacturing (DFM) practices, select high-quality materials that meet your requirements, and establish clear quality control and testing procedures. Regularly monitor and analyze field failures to identify areas for improvement and cost optimization.
Conclusion
By understanding the key factors that influence PCB manufacturing costs and implementing cost-saving strategies, you can maximize your cost savings without compromising quality or functionality. Optimize your PCB design, select the right manufacturing partners, leverage economies of scale, and continuously monitor and improve your processes to achieve the best results. With a proactive approach to cost management, you can stay competitive in today’s dynamic market while delivering high-quality PCB products to your customers.
0 Comments