Board Size and Complexity
The size and complexity of a PCB are among the most significant factors that influence its manufacturing cost. Larger boards require more material, which increases the overall cost. Additionally, complex designs with intricate routing, multiple layers, and high component density are more challenging to manufacture and therefore more expensive.
Board Size | Relative Cost |
---|---|
Small | Low |
Medium | Moderate |
Large | High |
Number of Layers
The number of layers in a PCB also plays a crucial role in determining its manufacturing cost. Each additional layer increases the complexity of the manufacturing process, requiring more materials and labor. As a result, multi-layer PCBs are generally more expensive than single or double-layer boards.
Number of Layers | Relative Cost |
---|---|
1-2 | Low |
4 | Moderate |
6-8 | High |
10+ | Very High |
Component Density
The number and density of components on a PCB also affect its manufacturing cost. Boards with a high component density require more precise placement and routing, which increases the manufacturing complexity and cost. Additionally, boards with a mix of surface-mount and through-hole components may require multiple assembly processes, further increasing the cost.
Material Selection
The choice of materials used in PCB manufacturing has a significant impact on the overall cost. The most common materials used for PCB substrates are FR-4, which is a glass-reinforced epoxy laminate, and polyimide, which is a high-performance polymer.
FR-4
FR-4 is the most widely used material for PCB substrates due to its excellent electrical and mechanical properties, as well as its relatively low cost. It is suitable for a wide range of applications, from consumer electronics to industrial control systems.
Polyimide
Polyimide is a high-performance material that offers superior thermal stability, chemical resistance, and mechanical strength compared to FR-4. However, it is also more expensive, making it more suitable for demanding applications such as aerospace, military, and medical devices.
Material | Relative Cost |
---|---|
FR-4 | Low |
Polyimide | High |
Surface Finish
The surface finish of a PCB is another factor that influences its manufacturing cost. The most common surface finishes are Hot Air Solder Leveling (HASL), Organic Solderability Preservative (OSP), and Electroless Nickel Immersion Gold (ENIG).
HASL
HASL is a cost-effective surface finish that involves dipping the PCB in a molten solder bath and then leveling the surface with hot air. It provides good solderability and is suitable for most applications.
OSP
OSP is a thin, organic coating that is applied to the copper traces on a PCB to prevent oxidation and maintain solderability. It is a low-cost option that is suitable for short-term storage and quick assembly.
ENIG
ENIG is a high-performance surface finish that involves depositing a layer of nickel followed by a thin layer of gold on the copper traces. It provides excellent solderability, corrosion resistance, and durability, making it suitable for high-reliability applications. However, it is also more expensive than HASL and OSP.
Surface Finish | Relative Cost |
---|---|
HASL | Low |
OSP | Low |
ENIG | High |
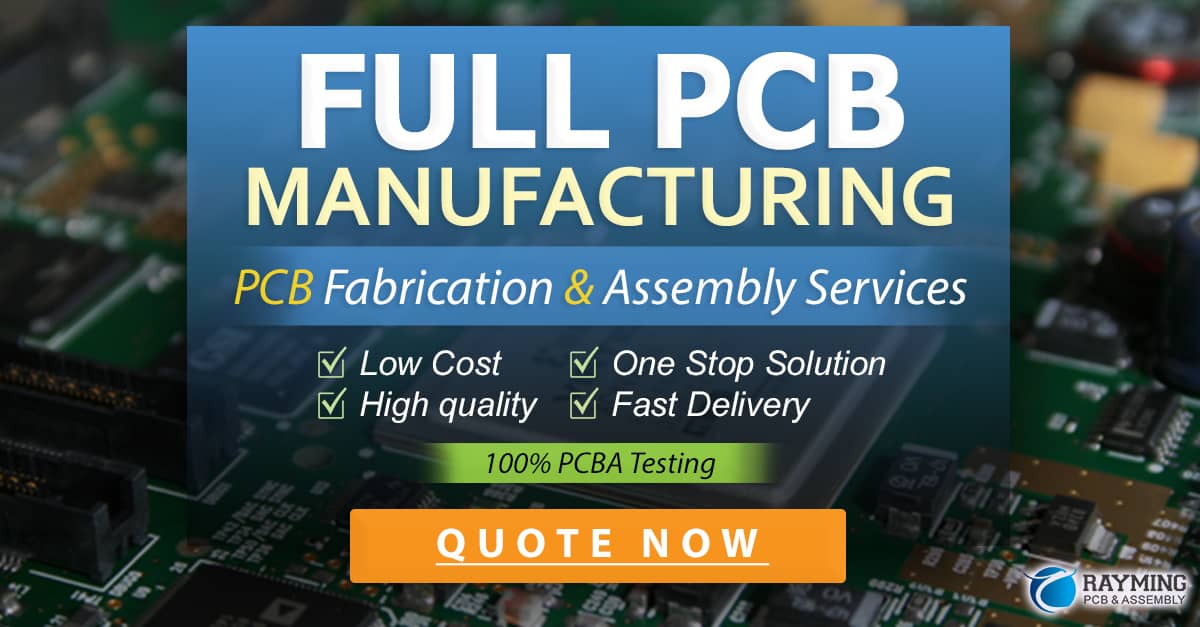
Order Quantity and Turnaround Time
The order quantity and turnaround time are also significant factors that affect PCB Manufacturing Cost. Larger order quantities typically result in lower per-unit costs due to economies of scale. However, this must be balanced against the need for inventory management and the risk of obsolescence.
Faster turnaround times generally incur higher costs, as they require prioritized production and expedited shipping. Businesses must weigh the trade-off between cost and time-to-market when deciding on turnaround times.
Order Quantity | Relative Cost per Unit |
---|---|
Low | High |
Medium | Moderate |
High | Low |
Turnaround Time | Relative Cost |
---|---|
Standard | Low |
Expedited | High |
Design for Manufacturability (DFM)
Design for Manufacturability (DFM) is a crucial aspect of PCB design that can significantly impact manufacturing costs. DFM involves designing PCBs with manufacturing constraints and best practices in mind to minimize potential issues and optimize production efficiency.
Some key DFM considerations include:
- Maintaining appropriate trace widths and clearances
- Avoiding acute angles and unnecessary vias
- Using standard component sizes and footprints
- Providing clear and accurate documentation
By adhering to DFM principles, designers can help reduce manufacturing costs and improve overall product quality.
Testing and Quality Control
Testing and quality control are essential aspects of PCB manufacturing that contribute to the overall cost. Rigorous testing is necessary to ensure that PCBs meet the required specifications and performance standards. Common testing methods include:
- In-circuit testing (ICT)
- Flying probe testing
- Functional testing
- Burn-in testing
The extent and complexity of testing required depend on the application and the criticality of the PCB. Higher-reliability applications, such as those in the aerospace and medical industries, typically require more extensive testing, which increases the overall manufacturing cost.
Frequently Asked Questions (FAQ)
1. What is the most significant factor that affects PCB manufacturing cost?
The most significant factor that affects PCB manufacturing cost is the board size and complexity. Larger and more complex boards require more materials, labor, and processing time, which increases the overall cost.
2. Can I reduce PCB manufacturing costs by using cheaper materials?
While using cheaper materials, such as FR-4 instead of polyimide, can reduce PCB manufacturing costs, it is essential to consider the specific requirements of your application. Using inferior materials may compromise the performance and reliability of the final product, leading to higher costs in the long run.
3. How can I optimize my PCB design for manufacturability?
To optimize your PCB design for manufacturability, follow DFM best practices such as maintaining appropriate trace widths and clearances, avoiding acute angles and unnecessary vias, using standard component sizes and footprints, and providing clear and accurate documentation.
4. Is it always cheaper to order larger quantities of PCBs?
While ordering larger quantities of PCBs can lead to lower per-unit costs due to economies of scale, it is important to balance this against the need for inventory management and the risk of obsolescence. It may not always be cost-effective to order large quantities, especially for rapidly evolving or low-volume products.
5. How can I balance the cost and speed of PCB manufacturing?
Balancing the cost and speed of PCB manufacturing involves making trade-offs between turnaround time and cost. If time-to-market is a critical factor, it may be necessary to accept higher costs for expedited production and shipping. However, if cost is the primary concern, opting for standard turnaround times can help minimize expenses.
In conclusion, PCB manufacturing cost is influenced by a complex interplay of factors, including board size and complexity, material selection, surface finish, order quantity, turnaround time, design for manufacturability, and testing requirements. By understanding these factors and making informed decisions based on the specific needs of their application, businesses can optimize their PCB manufacturing costs and ensure the success of their products in the market.
0 Comments