Introduction to LED PCB
Light-emitting diode (LED) technology has revolutionized the lighting industry, offering energy-efficient, long-lasting, and versatile solutions for various applications. At the heart of every LED light lies a printed circuit board (PCB) that serves as the foundation for the electronic components and circuitry. In this article, we will delve into the world of LED PCB fabrication and assembly, exploring the key aspects, processes, and best practices involved in creating high-quality LED light PCBs.
Understanding LED PCB Design
PCB Material Selection
When designing an LED PCB, the choice of PCB material is crucial. The most commonly used materials for LED PCBs are:
- FR-4: A flame-retardant, glass-reinforced epoxy laminate that offers good mechanical and electrical properties.
- Metal Core PCB (MCPCB): A PCB with a metal core, typically aluminum, that provides excellent thermal conductivity for heat dissipation.
- Ceramic PCB: A high-performance substrate that offers superior thermal management and electrical insulation properties.
The selection of PCB material depends on factors such as the LED power requirements, operating environment, and cost considerations.
Thermal Management Considerations
LEDs generate heat during operation, which can affect their performance and lifespan if not properly managed. Effective thermal management is essential in LED PCB design. Some key considerations include:
- Thermal vias: Incorporating thermal vias in the PCB design helps dissipate heat from the LED components to the PCB’s backside or heatsink.
- Copper thickness: Increasing the copper thickness of the PCB traces improves thermal conductivity and heat dissipation.
- Heatsinks and thermal interface materials: Using heatsinks and thermal interface materials (TIMs) helps transfer heat away from the LED components and PCB.
Circuit Design and Layout
The circuit design and layout of an LED PCB play a vital role in ensuring optimal performance and reliability. Key aspects to consider include:
- Current and voltage requirements: Designing the circuit to provide the appropriate current and voltage to the LEDs based on their specifications.
- Series and parallel connections: Arranging LEDs in series or parallel configurations to achieve the desired voltage and current distribution.
- Trace width and spacing: Ensuring proper trace width and spacing to minimize voltage drop and prevent short circuits.
- Component placement: Optimizing component placement for efficient routing, thermal management, and manufacturability.
LED PCB Fabrication Process
PCB Fabrication Steps
The LED PCB fabrication process involves several key steps:
- PCB design and layout: Creating the PCB design using electronic design automation (EDA) software.
- PCB manufacturing: Fabricating the PCB substrate using processes such as etching, drilling, and plating.
- Solder mask application: Applying a solder mask layer to protect the PCB traces and prevent short circuits.
- Silkscreen printing: Adding silkscreen labels and markings for component placement and identification.
- Surface finish application: Applying a surface finish, such as HASL, ENIG, or OSP, to protect the exposed copper and enhance solderability.
Quality Control and Inspection
Ensuring the quality of LED PCBs during fabrication is essential. Various inspection and testing methods are employed, including:
- Visual inspection: Checking for defects, such as scratches, contamination, or misalignment, using automated optical inspection (AOI) or manual inspection.
- Electrical testing: Performing continuity, isolation, and functionality tests to verify the PCB’s electrical integrity.
- Thermal imaging: Using thermal imaging cameras to identify hot spots and ensure proper thermal management.
- X-ray inspection: Detecting internal defects, such as voids or delamination, using X-ray imaging techniques.
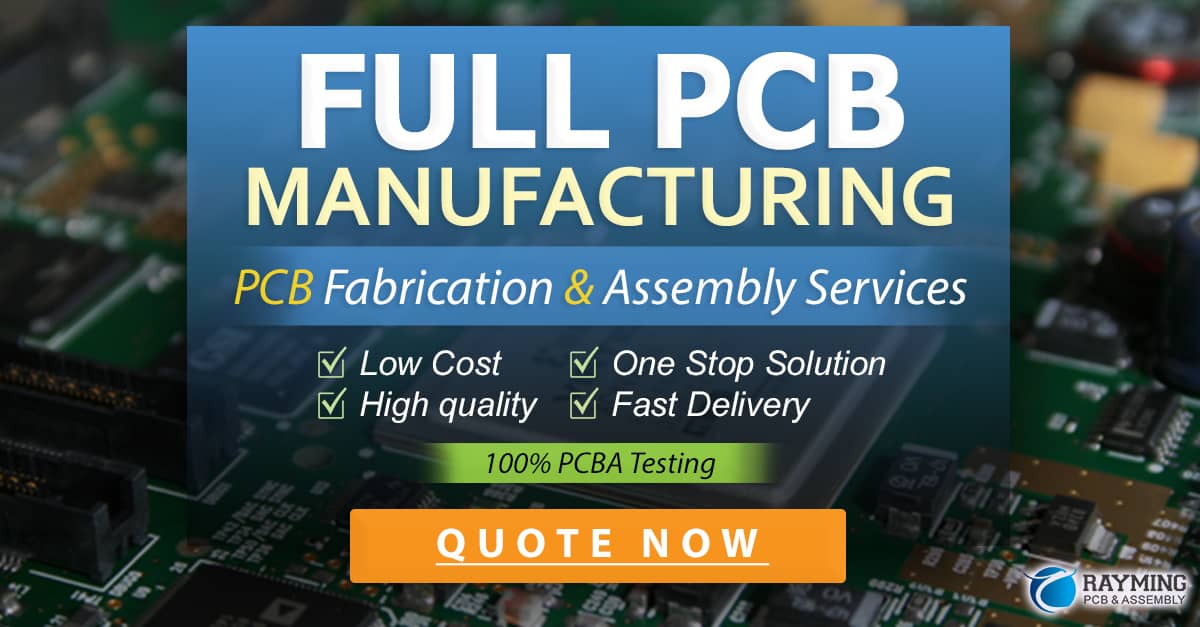
LED PCB Assembly Process
SMT Assembly
Surface mount technology (SMT) is the most common method for assembling LED PCBs. The SMT assembly process involves:
- Solder Paste Printing: Applying solder paste onto the PCB pads using a stencil or screen printing process.
- Component placement: Placing LED components and other SMD components onto the PCB using pick-and-place machines.
- Reflow soldering: Passing the PCB through a reflow oven to melt the solder paste and form reliable solder joints.
- Inspection and testing: Verifying the assembled PCB for proper component placement, solder joint quality, and functionality.
Through-Hole Assembly
Some LED PCBs may require through-hole components, such as connectors or large capacitors. The through-hole assembly process involves:
- Component insertion: Manually or automatically inserting through-hole components into the PCB’s drilled holes.
- Wave soldering: Passing the PCB over a wave soldering machine to form solder joints on the component leads.
- Inspection and testing: Verifying the assembled PCB for proper component placement, solder joint quality, and functionality.
Conformal Coating and Potting
In certain applications, LED PCBs may require additional protection against environmental factors such as moisture, dust, or vibration. Conformal coating and potting are two methods used to provide this protection:
- Conformal coating: Applying a thin layer of protective material, such as acrylic, silicone, or urethane, over the assembled PCB.
- Potting: Encapsulating the PCB and components in a resin or epoxy compound to provide mechanical and environmental protection.
Best Practices for LED PCB FAB & Assembly
To ensure the success of LED PCB fabrication and assembly, consider the following best practices:
- Design for manufacturability (DFM): Incorporate DFM principles in the PCB design to minimize fabrication and assembly challenges.
- Component selection: Choose high-quality LED components from reputable suppliers to ensure reliability and performance.
- Thermal management: Implement effective thermal management strategies to ensure optimal LED performance and longevity.
- Quality control: Establish rigorous quality control processes throughout the fabrication and assembly stages to identify and address any issues.
- Collaboration and communication: Foster open communication and collaboration between the design, fabrication, and assembly teams to streamline the process and resolve any challenges.
Frequently Asked Questions (FAQ)
1. What is the difference between an LED PCB and a regular PCB?
An LED PCB is specifically designed to support and power LED components, often requiring specialized features such as thermal management and current regulation. Regular PCBs, on the other hand, are designed for general-purpose electronic circuits and may not have the specific requirements needed for LED applications.
2. What are the advantages of using Metal Core PCBs (MCPCBs) for LED applications?
MCPCBs offer excellent thermal conductivity due to their metal core, typically aluminum. This helps dissipate heat generated by the LEDs more effectively, improving LED performance and lifespan. MCPCBs are particularly suitable for high-power LED applications where thermal management is critical.
3. How do I choose the right LED components for my PCB design?
When selecting LED components, consider factors such as:
– LED power and brightness requirements
– Color temperature and color rendering index (CRI)
– Forward voltage and current specifications
– Viewing angle and beam pattern
– Reliability and lifetime ratings
– Compatibility with the PCB design and other components
It’s essential to choose high-quality LED components from reputable suppliers to ensure optimal performance and reliability.
4. What are the common challenges encountered during LED PCB assembly?
Some common challenges in LED PCB assembly include:
– Ensuring proper thermal management to prevent overheating
– Achieving consistent and reliable solder joints
– Handling and placing small LED components accurately
– Preventing electrostatic discharge (ESD) damage to sensitive components
– Ensuring proper polarity and orientation of LED components
– Managing the different height profiles of LED components and other components on the PCB
Addressing these challenges requires careful planning, appropriate equipment, and skilled assembly techniques.
5. How can I ensure the long-term reliability of my LED PCB?
To ensure the long-term reliability of your LED PCB, consider the following:
– Implement robust thermal management techniques to prevent overheating and thermal stress
– Use high-quality components and materials that can withstand the expected operating conditions
– Follow best practices for PCB design, fabrication, and assembly to minimize defects and failures
– Conduct thorough testing and quality control measures to identify and address any issues early on
– Consider using conformal coating or potting to protect the PCB from environmental factors
– Provide appropriate driving and control circuitry to regulate the current and voltage supplied to the LEDs
– Regularly monitor and maintain the LED PCB system to detect and address any potential problems
Conclusion
LED PCB fabrication and assembly are critical processes in creating high-quality, reliable, and efficient LED lighting solutions. By understanding the key aspects of LED PCB design, fabrication, and assembly, designers and manufacturers can make informed decisions and implement best practices to ensure the success of their LED projects.
From selecting the right PCB materials and components to implementing effective thermal management strategies and quality control measures, each step of the LED PCB FAB and assembly process requires careful consideration and expertise.
As LED technology continues to advance and find new applications across various industries, the demand for high-quality LED PCBs will only continue to grow. By staying informed about the latest trends, techniques, and best practices in LED PCB FAB and assembly, manufacturers can remain competitive and deliver cutting-edge LED lighting solutions to meet the evolving needs of their customers.
0 Comments