Introduction to Metal Core PCB
Metal Core Printed Circuit Boards (MCPCBs) have gained significant popularity in the LED industry due to their unique properties and advantages over traditional PCBs. These specialized circuit boards feature a metal core, typically aluminum, which serves as a heat sink and provides excellent thermal management capabilities. In this article, we will explore the reasons behind the widespread use of Metal Core PCBs in LED products and how they contribute to the performance, reliability, and longevity of LED lighting solutions.
What is a Metal Core PCB?
A Metal Core PCB is a type of printed circuit board that consists of a metal base layer, usually aluminum, sandwiched between a thin layer of dielectric material and a copper circuit layer. The metal core acts as a heat spreader, efficiently dissipating heat generated by the mounted components, such as LEDs. This unique construction sets MCPCBs apart from standard FR-4 PCBs, which rely on copper traces and planes for heat dissipation.
Advantages of Metal Core PCBs in LED Applications
- Enhanced Thermal Management
- Improved Electrical Performance
- Increased Reliability and Longevity
- Design Flexibility
- Cost-Effectiveness
Thermal Management: The Key to LED Performance
Understanding the Importance of Heat Dissipation in LEDs
LEDs are highly sensitive to temperature fluctuations, and excessive heat can significantly impact their performance, color accuracy, and lifespan. As LEDs convert electrical energy into light, a portion of that energy is released as heat. If this heat is not effectively dissipated, it can cause the LED junction temperature to rise, leading to a phenomenon known as thermal runaway. Thermal runaway can result in reduced light output, color shifts, and premature failure of the LED.
How Metal Core PCBs Excel in Thermal Management
Metal Core PCBs are designed to address the thermal challenges associated with LED applications. The metal core, typically made of aluminum, has a high thermal conductivity, allowing it to quickly and efficiently transfer heat away from the LED components. The dielectric layer between the metal core and the copper circuit layer provides electrical insulation while minimizing thermal resistance.
Property | Metal Core PCB | FR-4 PCB |
---|---|---|
Thermal Conductivity (W/mK) | 1.0 – 3.0 | 0.3 – 0.4 |
Thermal Resistance (°C/W) | 0.5 – 1.5 | 8 – 10 |
Heat Spreading Capability | Excellent | Poor |
As evident from the table above, Metal Core PCBs offer significantly higher thermal conductivity and lower thermal resistance compared to traditional FR-4 PCBs. This enables MCPCBs to efficiently dissipate heat, maintaining lower LED junction temperatures and ensuring optimal performance.
Electrical Performance and Reliability
Improved Electrical Performance with Metal Core PCBs
In addition to their thermal management capabilities, Metal Core PCBs also contribute to improved electrical performance in LED applications. The metal core provides a low-impedance ground plane, reducing electromagnetic interference (EMI) and improving signal integrity. This is particularly important in LED lighting systems, where high-frequency switching and pulse-width modulation (PWM) are commonly used for dimming and color control.
Increased Reliability and Longevity
By effectively managing heat and maintaining lower LED junction temperatures, Metal Core PCBs play a crucial role in enhancing the reliability and longevity of LED products. Elevated temperatures can cause premature degradation of LED packages, leading to reduced light output and color shifts over time. MCPCBs help mitigate these issues by keeping the LEDs within their optimal temperature range, extending their lifespan and maintaining consistent performance throughout their operational life.
LED Junction Temperature | Lifetime (L70) |
---|---|
85°C | 50,000 hours |
105°C | 25,000 hours |
125°C | 12,500 hours |
The table above illustrates the impact of LED junction temperature on the expected lifetime of an LED. By maintaining lower junction temperatures, Metal Core PCBs can significantly extend the lifespan of LED products, reducing maintenance and replacement costs.
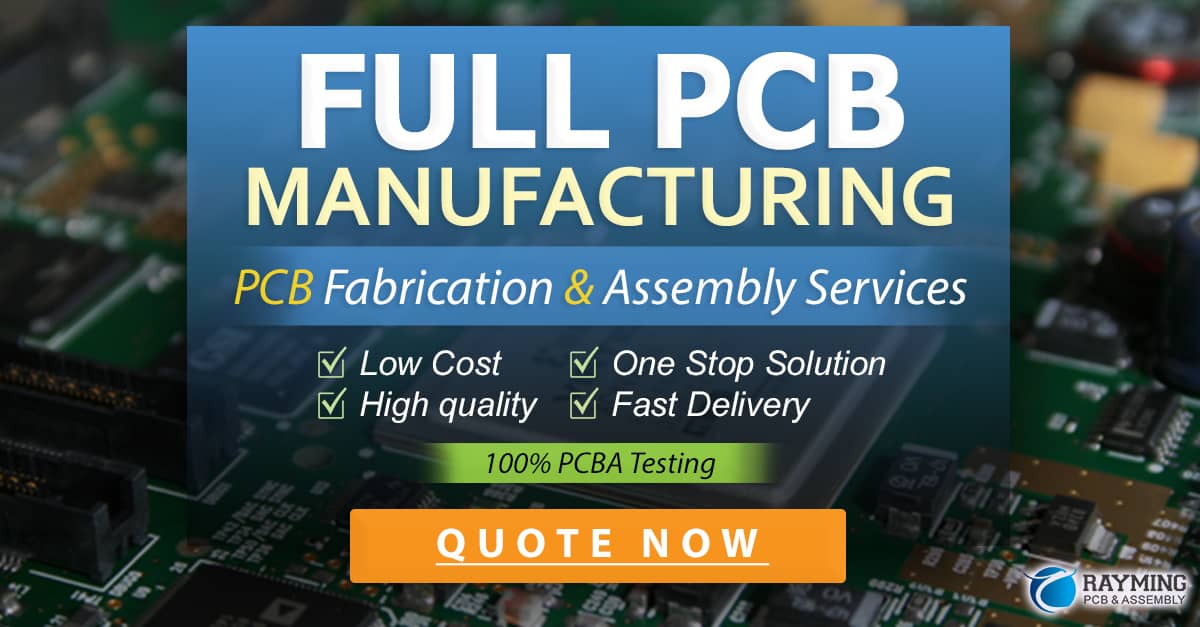
Design Flexibility and Cost-Effectiveness
Versatile Design Options with Metal Core PCBs
Metal Core PCBs offer designers a wide range of options to create efficient and compact LED lighting solutions. The ability to mount LEDs directly on the metal core allows for higher component density and minimizes the need for additional heat sinks. This enables the development of slim and lightweight LED fixtures, expanding the range of applications where LED lighting can be used.
MCPCBs also support various LED package types, including surface-mount devices (SMD), chip-on-board (COB), and high-power LEDs. This versatility allows designers to select the most suitable LED package for their specific application, optimizing performance and cost.
Cost-Effectiveness in the Long Run
While Metal Core PCBs may have a higher initial cost compared to traditional FR-4 PCBs, they offer long-term cost benefits in LED applications. The enhanced thermal management and increased reliability provided by MCPCBs result in extended LED lifespan, reducing the frequency of replacements and associated maintenance costs.
Moreover, the improved thermal performance of Metal Core PCBs allows for the use of higher-power LEDs, enabling designers to achieve the desired luminous output with fewer LED packages. This can lead to cost savings in terms of component count and overall system complexity.
Conclusion
The widespread adoption of Metal Core PCBs in LED products is a testament to their superior thermal management capabilities, improved electrical performance, and enhanced reliability. By effectively dissipating heat and maintaining lower LED junction temperatures, MCPCBs ensure optimal performance, color accuracy, and extended lifespan of LED lighting solutions.
The design flexibility offered by Metal Core PCBs, along with their long-term cost-effectiveness, make them an attractive choice for LED manufacturers and lighting designers. As the demand for high-performance and energy-efficient lighting continues to grow, the role of Metal Core PCBs in the LED industry is expected to become even more prominent.
Frequently Asked Questions (FAQ)
1. Can Metal Core PCBs be used with other components besides LEDs?
Yes, Metal Core PCBs can be used with other heat-generating components, such as power transistors, voltage regulators, and high-performance processors. The excellent thermal management properties of MCPCBs make them suitable for applications where efficient heat dissipation is crucial.
2. Are there any limitations to using Metal Core PCBs?
One limitation of Metal Core PCBs is their reduced electrical insulation compared to FR-4 PCBs. The thin dielectric layer between the metal core and the copper circuit layer requires careful design considerations to ensure proper electrical isolation. Additionally, MCPCBs may have limitations in terms of minimum trace width and spacing due to the thermal expansion of the metal core.
3. How does the thermal conductivity of the dielectric layer affect the performance of Metal Core PCBs?
The thermal conductivity of the dielectric layer is an important factor in the overall thermal performance of Metal Core PCBs. A dielectric material with higher thermal conductivity allows for more efficient heat transfer from the copper circuit layer to the metal core. This helps in maintaining lower LED junction temperatures and enhances the overall thermal management of the system.
4. Can Metal Core PCBs be manufactured with multiple copper layers?
Yes, Metal Core PCBs can be manufactured with multiple copper layers, depending on the specific requirements of the application. However, the number of copper layers is typically limited compared to traditional FR-4 PCBs due to the presence of the metal core. The additional copper layers can be used for signal routing, power distribution, or as additional thermal planes.
5. Are there any special considerations for soldering components on Metal Core PCBs?
Soldering components on Metal Core PCBs requires careful temperature control and appropriate soldering techniques. The metal core can dissipate heat quickly, which may affect the soldering process. It is important to use soldering methods that can accommodate the thermal characteristics of MCPCBs, such as reflow soldering or selective soldering. Additionally, the choice of solder paste and flux should be compatible with the dielectric material and the metal core to ensure reliable solder joints.
0 Comments