Surface mount technology (SMT) has revolutionized the electronics manufacturing industry. SMT enables the production of smaller, lighter, and more reliable printed circuit boards (PCBs) by mounting components directly onto the surface of the board rather than using through-hole technology. As products continue getting smaller and more complex, the demand for SMT capabilities is growing exponentially. For electronic device manufacturers looking to bring PCB production in-house, setting up an SMT factory is a major endeavor that requires careful planning and investment. This article will provide an overview of key considerations when establishing an SMT factory.
Facility and Layout
Location
One of the first steps is determining the ideal location for the SMT factory. Key factors to consider include:
- Proximity to customers and suppliers: Locating close to major customers will reduce shipping costs and lead times. Proximity to component suppliers can also facilitate just-in-time delivery.
- Access to skilled labor: Ensure there is sufficient local talent available to staff manufacturing roles and engineering positions. This may influence site selection significantly.
- Utility infrastructure: The facility will require stable power, clean water, waste disposal, etc. Make sure required utilities are available.
- Transportation infrastructure: Convenient access to interstates, airports, rail, and shipping ports will be advantageous.
Facility Design
Once a location is selected, the facility must be designed to optimize SMT production workflow. Key design elements include:
- Production floor layout: The floor plan should streamline movement of materials and components from receiving to finished goods shipping. Common configurations include functional cell layouts or process layouts.
- Environmental controls: Stringent temperature and humidity control is vital for protecting sensitive components. HVAC systems must be sized appropriately.
- Power systems: Uninterruptible power supply (UPS) systems and power conditioning units should be incorporated to protect against surges, spikes, and outages.
- ESD controls: Static dissipative flooring, ESD-safe workstations, ionization, etc. must be implemented to prevent electrostatic discharge events.
- Clean room controls: The assembly area may need higher levels of cleanliness depending on the products and components being handled. Clean room infrastructure can be added during construction.
Production Equipment
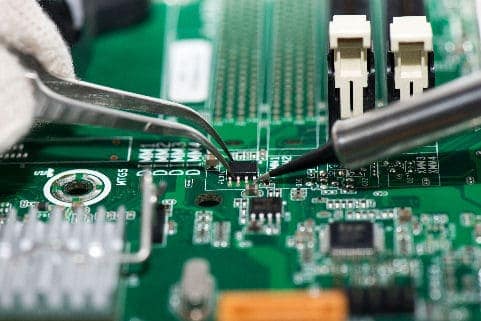
SMT production relies heavily on machinery for faster, more reliable processes than manual assembly. Major equipment categories include:
SMT Mounting Lines
SMT mounting lines automate the process of mounting and soldering surface mount components onto PCBs. They consist of:
- SMT pick-and-place machine – Uses precision robotic movements to pick components from feeders and accurately place them on PCBs. High-end pick-and-place machines can place over 100,000 components per hour.
- SMT reflow oven – Solder paste is first applied to PCB pads. The boards pass through the reflow oven to heat solder paste deposits, causing them to melt and making solder joints. Different heating methods include IR, convection, or vapor phase.
- Solder paste printer – Used to deposit tiny amounts of solder paste on PCB pads prior to component placement. Ensures consistent solder application.
- Inspection machine – Checks PCBs after soldering to identify defects like missing components, poor alignments, solder bridging, etc. Can be automated optical inspection (AOI) or automated x-ray inspection (AXI).
Equipment | Key Factors |
---|---|
SMT Pick-and-Place | Feeder capacity, placement speed and accuracy, vision systems, rotational capability |
SMT Reflow Oven | Heating method, number of zones, convection control, max PCB size |
Solder Paste Printer | Print speed, stencil size, automated monitoring |
Inspection System | 2D vs. 3D, false call rate, throughput speed |
Other Supporting Equipment
To complement the SMT lines, factories also require:
- Reflow soldering – For manual soldering of through-hole components
- Conformal coating – Automated systems for applying protective coatings to PCB assemblies
- Testing systems – For verifying board functionality like in-circuit testers, flying probe testers, boundary scan testing
- Programming & burning systems – For loading firmware onto boards and programming components
- Depaneling systems – For singulating individual PCBs from larger panels
- X-ray inspection – For detecting defects like shorts, opens, foreign objects, or missing connections
- Product traceability systems – For tracking boards and components throughout the production process
Investing in high-quality equipment and keeping it properly maintained is crucial for maximizing factory throughput and yield.
PCB Design and CAM
To effectively set up production processes, engineering collaboration with customers during PCB design is helpful. Design for manufacturability guidelines can be provided to optimize designs for SMT assembly.
Key areas to address include:
- Component selection – Preference for surface mount over through-hole, standardizing on preferred component packages and lead configs.
- PCB layout – Allowing adequate clearance between components and observing design rules to enable high-yield assembly.
- Footprint creation – Developing footprints suited to capabilities of SMT equipment.
- Test points – Incorporating sufficient test points for verification during and after assembly.
Computer-aided manufacturing (CAM) software also plays a critical role in programming the SMT machines through:
- CAD data import – Converting PCB design data into manufacturing data models
- Solder paste stencils – Creating aperture openings optimized for applying paste precisely
- Pick-and-place programming – Mapping component placements and feeder setups
- Inspection programming – Teaching inspection systems board-specific checking criteria
Close cross-functional collaboration between engineering and manufacturing teams in these areas helps accelerate production ramp-up.
Supply Chain Management
Managing the sourcing, procurement, and stocking of thousands of component parts is a complex endeavor. Strategic approaches are needed in inventory planning, logistics, and supplier relationship management.
Strategic Sourcing
- Supplier qualification – Vetting and approving suppliers based on quality, reliability, capabilities, and cost. Typically involves site visits and audits.
- Risk management – Dual-sourcing critical components, understanding supplier contingencies, and monitoring market conditions. Avoiding over-dependence on single sources.
- Cost optimization – Negotiating pricing based on order volumes, leveraging preferred suppliers, and economic order quantities.
Inventory Management
- Forecasting demand – Using historical data, sales pipeline, and market factors to estimate component requirements.
- Setting reorder points – Triggering replenishment orders when stock levels reach predetermined quantities.
- Managing shelf life – Monitoring age-sensitive materials like solder paste and adhesives. First-in-first-out (FIFO) stock rotation.
- Kitting for production – Pre-organizing components into kits to fulfill specific build requirements. Enables just-in-time material flow.
Logistics
- Warehousing – Providing climate-controlled, ESD-safe storage close to production lines. Racking, bin systems, etc.
- Incoming inspections – Verifying incoming materials meet specifications before accepting into stock.
- Traceability – Lot control, serial numbers, date codes, and labelling schemes for tracking components.
- Materials handling – Automation like feeder racks, tape-and-reel, vibratory bowls support efficient component supply to lines.
Careful attention to supply chain factors is essential for maintaining responsive, uninterrupted manufacturing.
Quality Management
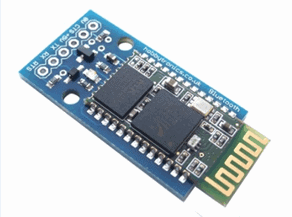
A robust quality management system is a prerequisite for any SMT factory. Key initiatives include:
Process Control
- Statistical process control monitoring, control charts, capability indices
- Error-proofing methods like poka-yoke to prevent and detect defects
- Standard operating procedures, operator instructions, training programs
- Equipment maintenance programs and change management protocols
Inspection and Testing
- In-process inspections at critical points in assembly process
- AOI and other automated testing to catch errors early
- Reliability testing like HALT/HASS, burn-in, environmental stress screening
- Outgoing quality control and final audits before shipment
Continuous Improvement
- Lean tools like 5S, kaizen events, problem-solving methodologies
- Data collection and analysis to identify root causes
- Corrective and preventive actions like DMAIC projects
- Management review with goals and metrics monitoring
Certifications
- Earning IATF 16949, ISO 13485 for medical devices, AS9100 for aerospace, or ISO 9001 certifications to verify quality system effectiveness
- Compliance with regulatory requirements like RoHS, REACH, and UL standards.
A culture focused on quality will enable consistently executing complex SMT assembly to the highest standards.
Staffing and Training
The key resource of any manufacturing facility is its people. Building a talented team is crucial for SMT factory success.
Recruiting
- Partnering with local technical colleges and training programs to recruit skilled production workers, technicians, and engineers.
- Developing relationships with SMT equipment vendors for specialist technical training and support.
- Offering competitive pay, benefits, career advancement opportunities, and good working conditions.
Onboarding and Development
- Extensive on-the-job training for machine operation, maintenance, and repair.
- Classroom and hands-on skills training on safety procedures, ESD control, quality systems, equipment troubleshooting, and more.
- Apprenticeship-style programs to develop well-rounded expertise.
- Incentivizing employees to continue education and maintain relevant certifications.
Organization
- Clear roles and reporting structures. Production teams grouped by function or production line.
- Lean manufacturing principles like cellular manufacturing, visual controls, etc.
- Effective intra-department communication mechanisms between shifts and across functions.
Culture
- Emphasizing safety, quality, delivery, cost, and morale as core values.
- Developing strong technical community through collaboration, knowledge sharing, and team building.
- Promoting transparency, recognizing contributions, and empowering employees.
Investing in human capital gives the SMT factory its true competitive advantage. An environment where people want to build a career enables sustainable success.
Facilities Management
Ongoing facilities management ensures the SMT factory remains optimized for performance, safety, compliance, and longevity. This involves:
- Proactive maintenance programs on buildings, production equipment, and utilities.
- Calibration and certification of inspection tools, test systems, and environmental monitoring devices.
- Managing spare parts inventory for maintenance and machine repairs.
- Coordinating with vendors and suppliers for equipment service needs.
- Monitoring facility condition and addressing potential risks proactively.
- Ensuring compliance with safety regulations and certifications through regular audits and inspections.
- Tracking and reporting on energy usage, waste generation, and other sustainability metrics.
- Planning and budgeting for future facility upgrades and expansions.
With constant vigilance in these areas, the physical factory can support production at the pace demanded by the electronics market.
Financial Planning
Significant capital investment is required when first establishing an SMT production facility. Careful financial planning is imperative.
Key Cost Centers
- Facility acquisition/construction – Purchase or building costs, site development, permitting, utilities installation.
- Production equipment – SMT machines, inspection systems, test equipment. Millions in startup capex.
- Tooling and setup – Solder paste stencils, feeders, component tapes, Cam programming.
- Inventory – Building raw material and component part inventories.
- Staffing – Salaries, training, benefits, payroll taxes.
Funding Options
- Self-funded – For well-capitalized manufacturers able to finance the investment internally.
- Loans – Bank financing, bonds, or government small business loans. Requires demonstrating repayment ability.
- Private equity – Selling partial ownership and control in exchange for capital injection.
- Venture capital – Giving up equity share to outside investors who take on risk.
Each funding path involves tradeoffs and implications for ownership structure.
Cost Analysis
- Payback period – Simple analysis of years required to recover initial outlay through profits
- Net present value – Comparing discounted cash flows against initial investment.
- Internal rate of return – ROI calculation considering cost of capital and time value of money.
- Sensitivity analysis – Testing viability under different scenarios like sales estimates, costs.
Detailed financial modeling provides greater confidence in the significant undertaking.
FAQ
What are some key steps for choosing an SMT factory location?
Some key factors in choosing a location include proximity to customers and suppliers, availability of skilled labor, transportation infrastructure, utility infrastructure, construction and operating costs, and state/local business incentives. Weigh each element carefully as part of a site selection analysis.
What is the typical cost range for setting up an SMT line?
The total cost of setting up an SMT line varies considerably based on production volumes and the capabilities of the equipment chosen. A basic line could cost ~$500,000 to $1 million. High-end SMT lines with the latest automation and inspection can cost $2 million to $5 million+
What are important considerations in designing an SMT floor plan?
Important SMT floor plan considerations include material flow, minimizing work in process (WIP), equipment ergonomics, operator safety, eliminating redundant motion, compliance with ESD guidelines, accommodating inventory, isolating vibration-sensitive processes, utility access, and allowing for future expansion.
How can ESD risks be mitigated in an SMT factory?
Mitigating ESD risks involves using ESD-safe flooring, grounding all equipment, dissipative table mats, ionization systems, humidity control, conductive packaging and tubes for parts, wrist straps, ESD-safe footwear, grounding personnel prior to entry, ESD-safe signage, and employee training.
What types of testing are commonly performed on SMT assemblies?
Common SMT testing methods include flying probe testing, boundary scan testing, automated optical inspection, x-ray inspection, in-circuit testing, bed of nails testing, functional testing, and environmental stress testing.
What are some examples of SMT industry certifications?
Some common SMT-related certifications include IPC J-STD-001, IPC-A-610 Acceptability of Electronic Assemblies, IPC 7711/7721 Rework and Repair, IPC-WHMA-A-620 for wire harness assembly, and various soldering certifications from IPC. Many roles also require ESD training certification.
0 Comments