Introduction to Surface Mount Technology
Surface mount technology (SMT) revolutionized the production of printed circuit boards (PCBs) and electronic components in the late 20th century. SMT uses solder pads or conductive adhesive to attach electronic components directly to the surface of a PCB instead of through holes. This allows for miniaturized components and greater component density on circuit boards.
SMT was developed as an alternative to through-hole technology, which required drilling holes in a PCB to mount components with leads. SMT enabled further miniaturization of electronics by eliminating the need for these holes and allowing components to be packed closer together. It also automated much of the assembly process through pick-and-place machines and solder reflow ovens.
Benefits of SMT
SMT provides a number of advantages over through-hole technology:
- Smaller components: SMT components can be up to 75% smaller than their leaded counterparts. This allows for miniaturization of electronic devices.
- Higher density: With no holes required to mount components, SMT boards can fit more components in the same footprint. This enables more compact PCB designs.
- Automated assembly: SMT is optimized for automated assembly with pick-and-place machines, solder paste, and reflow soldering. This reduces labor costs and speeds up production.
- Improved performance: Eliminating leads reduces parasitic capacitance and inductance, allowing SMT circuits to operate at higher frequencies.
- Lower costs: Smaller board sizes, fewer holes to drill, and automated assembly all reduce costs compared to through-hole assembly.
SMT Components
Many different types of electronic components are made in surface mount packages suitable for SMT assembly. Some of the most common include:
- Resistors and capacitors: The most prevalent SMT components, available in standardized package sizes, like 0201, 0402, 0603, etc. based on dimensions in inches.
- Integrated circuits (ICs): From simple amplifiers to complex microprocessors, ICs come in leaded and leadless SMT packages. Common options include quad flat pack (QFP), ball grid array (BGA), and small outline IC (SOIC).
- Light emitting diodes (LEDs): LEDs designed for direct SMT mounting provide compact, efficient, and automated assembly of lighting.
- SMT connectors: Board-to-board, board-to-cable, and other interconnects eliminate wired leads with direct SMT mounting. Common types include card edge, HDMI, USB, etc.
Table 1: Common SMT Components
Component | Description | Example Packages |
---|---|---|
Resistor/Capacitor | Most prevalent components | 0201, 0402, 0603, 1206 |
Integrated Circuit (IC) | Microchips | QFP, BGA, SOIC |
LED | Lighting | SMT LEDs |
Connector | Interconnects | Card edge, HDMI |
SMT Assembly Process
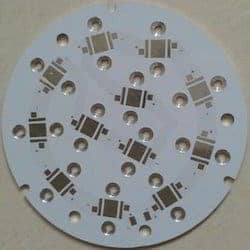
Assembling a board with SMT involves carefully soldering all components in the right locations. This is typically an automated process consisting of three main steps:
SMT Assembly Steps
- Solder Paste Application – Solder paste is applied to all solder pads on the PCB. This provides the solder for mounting the components.
- Component Placement – Robotic pick-and-place machines precisely place each component on its designated solder pads.
- Reflow Soldering – The board passes through a reflow oven melting the solder paste to form solder joints and permanently attach the components.
Quality Control in SMT Assembly
To ensure high quality and reliable solder joints, SMT assembly uses inspection and testing:
- Automated Optical Inspection (AOI) checks component placement and solder joints after reflow.
- In-Circuit Testing (ICT) confirms electrical connectivity and function after population.
- X-Ray Inspection thoroughly examines internal solder joints of BGA packages.
This rigorous quality control minimizes defects and avoids costly rework of defective assemblies.
Impact of SMT on Electronics
The transition to SMT manufacturing enabled the electronics revolution of ever-smaller, more powerful, and feature-rich devices like:
- Mobile phones
- Laptops, tablets, and other portable electronics
- High density servers and data centers
- Compact consumer devices like digital cameras
Without SMT manufacturing, none of these ubiquitous devices would be feasible or economical to produce. SMT will continue enabling cutting edge electronics in the future.
Frequently Asked Questions
Here are some common FAQs about SMT manufacturing:
What are the key advantages of SMT?
The main advantages of SMT are smaller components, increased density, automated assembly, improved performance, and lower costs. It enables electronics miniaturization and superior designs.
How is SMT different from through-hole assembly?
SMT attaches components directly to the surface rather than inserting leads into holes. This eliminates drilled holes and allows higher density component mounting.
What types of components are used in SMT?
All standard electronic components like resistors, capacitors, ICs, LEDs, and connectors are available in surface mount packages suitable for SMT.
How are components attached in SMT assembly?
Solder paste and a reflow oven are used to form solder joints to electrically and mechanically attach components to PCB pads.
Why is quality control important for SMT?
Inspection and testing ensures reliable solder joints and confirms component placement and electrical function. This prevents defects and avoids rework.
0 Comments