What is PCB Assembly?
PCB assembly is the process of soldering or mounting electronic components onto a printed circuit board (PCB). A PCB mechanically supports and electrically connects electronic components using conductive tracks, pads and other features etched from one or more sheet layers of copper laminated onto and/or between sheet layers of a non-conductive substrate.
PCBs can be single sided (one copper layer), double sided (two copper layers on both sides of one substrate layer), or multi-layer (outer and inner layers). Conductors on different layers are connected with Plated-through Holes called vias. Advanced PCBs may contain components – capacitors, resistors or active devices – embedded in the substrate.
PCB Assembly Process
The PCB assembly process consists of several steps:
-
Solder Paste Stenciling – Solder paste is applied to the PCB pads where components will be mounted. A stainless-steel stencil is used to apply the solder paste in the desired locations.
-
Pick and Place – The electronic components are picked up from tape reels or trays and placed onto the PCB at their designated locations. This is done by automated pick-and-place machines for high volume or by hand for low volume.
-
Reflow Soldering – The PCB with components placed goes through a reflow oven. The solder paste melts in a controlled way, creating permanent solder joints between component leads and PCB pads.
-
Inspection – The assembled PCB is visually inspected for any defects like solder bridges, missing components, misaligned components, etc. Automated optical inspection (AOI) systems are commonly used.
-
Through-Hole Component Insertion – If the PCB has through-hole components, these are inserted by hand or by machine into drilled holes on the PCB.
-
Wave Soldering – For through-hole components, the PCB goes through a wave soldering machine. A wave of molten solder washes over the bottom side of the PCB, soldering the leads in place.
-
Final Inspection and Test – The fully assembled PCB goes through final visual inspection and functional test to ensure it performs as intended before being shipped.
Types of PCB Assembly
There are three main types of PCB assembly:
Through-Hole Assembly (THA)
Through-hole components have long metal leads that are inserted into drilled holes on the PCB. The leads are then soldered to pads on the opposite side of the board. Through-hole assembly is sturdy and reliable but requires drilling holes and takes up more space compared to surface mount.
Surface Mount Assembly (SMA)
Surface mount components are soldered directly onto pads on the surface of the PCB. No drilled holes are required. Components are much smaller and mounting is more automated compared to through-hole. Surface mount is the most common PCB assembly method today.
Mixed Assembly
Many PCB designs use a mix of through-hole and surface mount components. Through-hole is used for large components like connectors and electrolytic capacitors, while surface mount is used for smaller components. Mixed assembly gives the benefits of both techniques.
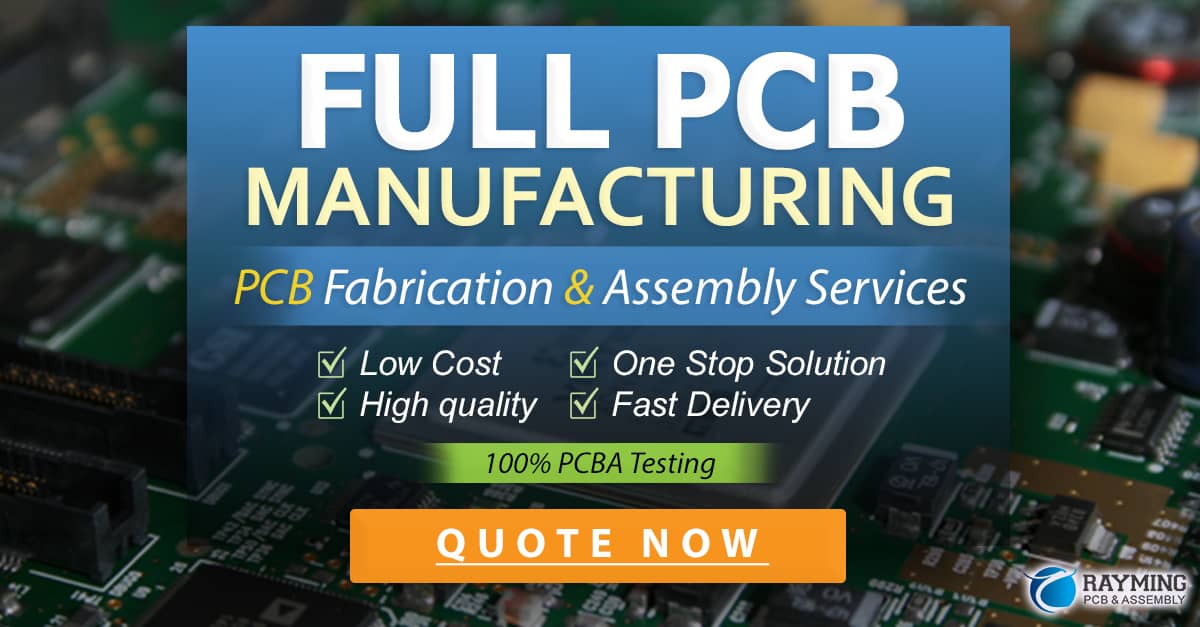
PCB Assembly Equipment and Machines
Various equipment and machines are used in the PCB assembly process:
Equipment | Description |
---|---|
Solder Paste Printer | Applies solder paste onto PCB pads through a laser-cut stainless steel stencil. |
Pick and Place Machine | Automatically picks electronic components from feeders and places them onto their designated locations on the PCB. |
Reflow Oven | Passes PCB through a controlled heating process to melt the solder paste, permanently attaching components. |
Wave Soldering Machine | Washes a wave of molten solder over the bottom of the PCB to solder through-hole component leads. |
Automated Optical Inspection (AOI) | Uses cameras and image analysis software to automatically inspect assembled PCBs for defects. |
In-Circuit Test (ICT) Equipment | Makes electrical contact with test points on the PCB to verify correct assembly and detect shorts, opens, missing components, etc. |
Functional Test Equipment | Powers up the assembled PCB and runs tests to verify it functions as intended in the end application. |
Other ancillary equipment include board handling conveyors, board cleaners, rework and repair stations, fume extraction, anti-static control, and more.
PCB Assembly Materials
The main materials used in PCB assembly are:
Printed Circuit Board (PCB)
The bare PCB is the foundation for the assembly. It is made of layers of copper conductors bonded to an insulating substrate material. The copper is etched to form the circuit connections. PCBs can be rigid (FR-4), flexible, rigid-flex, or metal core.
Solder Paste
Solder paste is a mixture of tiny solder balls (spheres of tin, silver, and copper), flux, and other additives. It is a gray, putty-like material that is printed onto the PCB pads. When heated, the solder melts to form the solder joints.
Surface Mount Components
Surface mount components come in many small package types like chip resistors, chip capacitors, small outline transistors (SOT), quad flat packs (QFP), ball grid arrays (BGA) and more. Components are supplied on tape reels or trays for automated placement.
Through-Hole Components
Through-hole components have long metal leads for insertion into drilled holes. They tend to be larger than surface mount types. Examples are large electrolytic capacitors, connectors, transformers, and some integrated circuit packages like dual inline package (DIP).
PCB Assembly Design Considerations
To ensure a smooth and successful PCB assembly, several design considerations must be taken into account:
Component Placement
Components should be placed in a logical way that facilitates assembly and minimizes crossing of traces. Adequate space must be left between components for the assembly machines to access.
Solder Pad Design
Solder pads must be the correct size and shape for the component leads or contacts. Pad size affects the amount of solder paste deposited.
Solder Mask
The solder mask is the green coating over the PCB that prevents solder bridges from forming between closely spaced pads. Solder mask openings must be the right size.
Silkscreen
The white silkscreen legend on the PCB is important for showing component reference designators and polarity marks. The silkscreen must not overlap solder pads.
Panelization
PCBs are often assembled in panels of multiple boards to save time. Fiducial marks and tooling holes must be added for the assembly machines to orient the panels.
Design for Manufacturing (DFM)
The PCB design should follow the manufacturing capabilities of the assembly shop. This includes minimum pitch, pad sizes, space between components, etc. Following DFM rules makes assembly easier and reduces defects.
PCB Assembly Quality Control
Quality control is critical in PCB assembly to detect and prevent defects. Common quality control steps are:
Automated Optical Inspection (AOI)
AOI machines automatically scan the assembled PCB using cameras and image analysis software. They compare the actual assembly to the expected appearance from CAD data and highlight any anomalies like missing components, skewed components, solder defects, etc.
X-Ray Inspection
X-ray machines are used to inspect solder joints hidden under components like BGAs. They can detect voids, bridges, insufficient solder, and other defects not visible to optical inspection.
In-Circuit Test (ICT)
ICT equipment makes electrical contact with test points on the PCB via a bed-of-nails fixture. It measures for shorts, opens, component values, and other parameters to verify the assembly. ICT programming is derived from the PCB netlists.
Functional Test
Functional test applies power to the assembled PCB and tests its functionality as it would perform in the end product. Test code is written to exercise the various subfunctions of the board. Functional test detects defects that would impact the end user.
Flying Probe Test
Flying probe testers use moving test probes to make contact with test points, vias, and component leads on the PCB. They are an alternative to ICT when test fixtures are not practical. Flying probe is slower than ICT but requires no custom fixturing.
FAQ
What is the difference between PCB fabrication and PCB assembly?
PCB fabrication is the manufacturing of the bare printed circuit board only. PCB assembly is the process of soldering the components onto the fabricated PCB. PCB assembly turns the bare board into a functional circuit assembly.
What is the most common type of PCB assembly?
Surface mount assembly (SMT) is the most common assembly method today. Surface mount components are much smaller than through-hole and are soldered directly to the surface of the PCB without needing drilled holes. SMT allows for denser assemblies and more automated processing.
How much does PCB Assembly Cost?
PCB assembly cost depends on many factors like the size of the PCB, number of components, types of components (surface mount or through-hole), volume of production, and any special requirements. In general, setup and labor costs are higher for through-hole assembly, while material costs are higher for surface mount assembly. It’s best to get quotes from several PCB assembly shops based on the specific design and quantity needed.
What are some common PCB assembly defects?
Common PCB assembly defects include:
– Solder bridges – Unintended solder connections between adjacent pads
– Cold solder joints – Dull and cracked solder joints from improper soldering temperature
– Tombstoning – Chip components standing on end due to uneven solder reflow
– Missing components – Components not placed by the pick-and-place machine
– Skewed components – Components rotated or misaligned from their pads
– Insufficient solder – Not enough solder applied to the joint
– Solder balls – Tiny spheres of solder that can cause short circuits
What certifications are important for PCB assembly?
Some key certifications for PCB assembly include:
– IPC-A-610 – Acceptability of Electronic Assemblies
– J-STD-001 – Requirements for Soldered Electrical and Electronic Assemblies
– ISO 9001 – Quality Management Systems
– ISO 14001 – Environmental Management Systems
– UL – Product Safety Certification
– RoHS – Restriction of Hazardous Substances Directive
PCB assembly shops with these certifications have demonstrated their processes and products meet the required industry standards.
0 Comments