PCB Design Complexity
One of the primary factors affecting PCB Assembly Cost is the complexity of the board design. The more intricate and sophisticated the design, the higher the manufacturing costs will be. Here are some aspects of PCB design complexity that can impact assembly costs:
Number of Layers
multilayer pcbs are more expensive to manufacture than single or double-sided boards. Each additional layer requires more materials, processing time, and specialized equipment, resulting in higher costs. The table below illustrates the typical cost increase associated with adding more layers to a PCB:
Number of Layers | Cost Multiplier |
---|---|
1-2 | 1x |
4 | 1.5x |
6 | 2x |
8 | 2.5x |
10+ | 3x+ |
Component Density
The number and type of components placed on the PCB also significantly affect assembly costs. High-density designs with numerous small components, such as ball grid arrays (BGAs) or chip-scale packages (CSPs), require precise placement and specialized equipment, leading to increased assembly time and costs.
Trace Width and Spacing
Narrower trace widths and tighter spacing between components demand higher precision during the manufacturing process. This requires advanced equipment and skilled technicians, which can drive up assembly costs. The following table shows how trace width and spacing impact manufacturing costs:
Trace Width/Spacing | Cost Impact |
---|---|
≥ 8 mil/8 mil | Low |
6 mil/6 mil | Medium |
≤ 4 mil/4 mil | High |
Material Selection
The choice of materials used in PCB fabrication and assembly also plays a significant role in determining costs. Some key material considerations include:
PCB Substrate Material
The most common PCB substrate materials are FR-4, which is a fiberglass-reinforced epoxy laminate, and high-frequency materials like Rogers or Isola. Specialty substrate materials designed for high-temperature, high-frequency, or high-reliability applications are generally more expensive than standard FR-4.
Copper Thickness
PCBs with thicker copper layers are more costly to produce due to the increased material cost and processing time. However, thicker copper may be necessary for high-current applications or to improve signal integrity.
Surface Finishes
The choice of surface finish for the PCB can also affect assembly costs. Some common surface finishes include:
- Hot Air Solder Leveling (HASL)
- Organic Solderability Preservative (OSP)
- Electroless Nickel Immersion Gold (ENIG)
- Immersion Silver (IAg)
- Immersion Tin (ISn)
HASL and OSP are generally the most cost-effective options, while ENIG, IAg, and ISn offer improved solderability and durability at a higher cost.
Manufacturing Volume
The volume of PCBs being assembled is another critical factor in determining assembly costs. Higher production volumes often result in lower per-unit costs due to economies of scale. This is because fixed costs, such as setup times and tooling, can be spread across a larger number of units. The table below demonstrates how production volume can affect per-unit costs:
Production Volume | Per-Unit Cost |
---|---|
Prototype (1-10) | $$$$$ |
Low (11-100) | $$$$ |
Medium (101-1000) | $$$ |
High (1000+) | $$ |
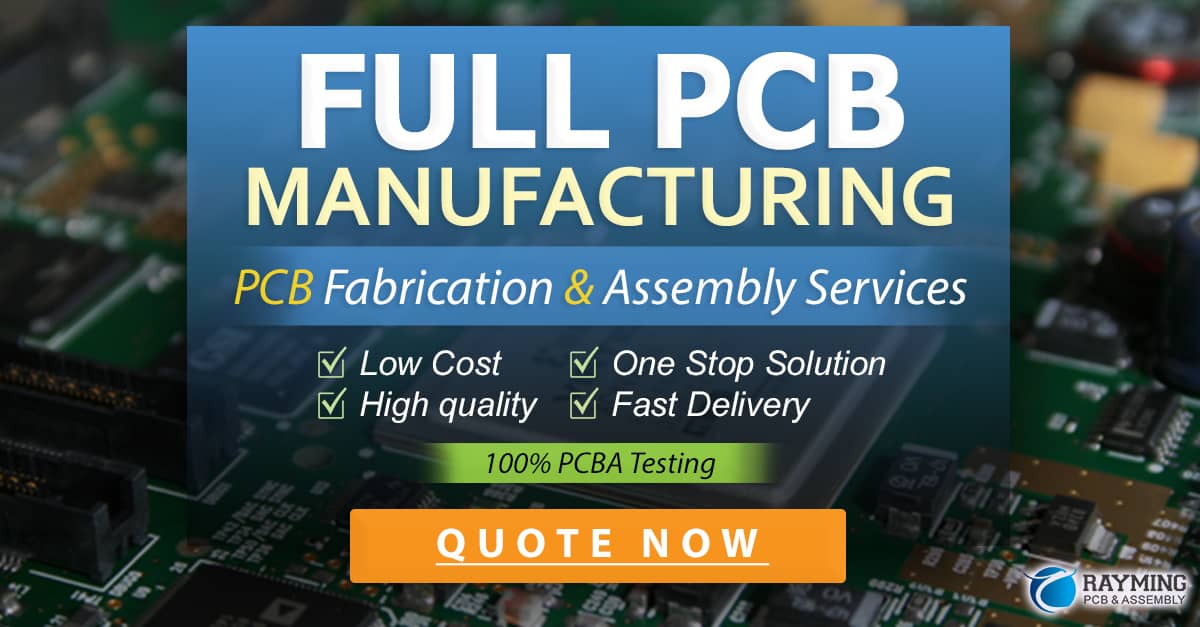
Assembly Processes
The specific assembly processes required for a given PCB design can also significantly impact costs. Some factors to consider include:
Manual vs. Automated Assembly
Manual assembly, where components are placed and soldered by hand, is generally more expensive than automated assembly for high-volume production. However, for low-volume or prototype builds, manual assembly may be more cost-effective due to lower setup costs and tooling requirements.
Soldering Techniques
The choice of soldering technique can also affect assembly costs. The three main methods are:
- Wave Soldering: Best suited for through-hole components and generally the most cost-effective option for high-volume production.
- Reflow Soldering: Used for surface-mount components and offers a good balance of cost and quality for medium to high-volume production.
- Selective Soldering: A specialized process for boards with a mix of through-hole and surface-mount components, which can be more expensive than wave or reflow soldering.
Inspection and Testing
Thorough inspection and testing are crucial for ensuring PCB quality and reliability. However, these processes can also add to assembly costs. Common inspection and testing methods include:
- Automated Optical Inspection (AOI)
- X-ray Inspection
- In-Circuit Testing (ICT)
- Functional Testing
Balancing the need for comprehensive quality control with cost considerations is essential for optimizing the overall assembly process.
Turnaround Time
The required turnaround time for PCB assembly can also impact costs. Rush orders or expedited production schedules often incur additional fees due to the need for overtime labor, expedited shipping, and resource prioritization. Providing ample lead time for assembly can help minimize these additional costs.
Frequently Asked Questions (FAQ)
-
What is the most significant factor affecting PCB assembly costs?
The most significant factor affecting PCB assembly costs is typically the complexity of the board design. More complex designs with higher layer counts, dense component placement, and fine trace widths and spacing will generally be more expensive to assemble. -
How can I reduce PCB assembly costs without sacrificing quality?
To reduce PCB assembly costs without compromising quality, consider the following strategies: - Optimize your board design for manufacturability
- Choose cost-effective materials that meet your performance requirements
- Leverage economies of scale by increasing production volumes
- Provide ample lead time to avoid rush fees
-
Work closely with your assembly partner to identify cost-saving opportunities
-
What are the benefits of automated assembly versus manual assembly?
Automated assembly offers several advantages over manual assembly, including: - Lower per-unit costs for high-volume production
- Improved consistency and accuracy
- Faster production times
-
Reduced human error
However, for low-volume or prototype builds, manual assembly may be more cost-effective due to lower setup costs and tooling requirements. -
How do I choose the right surface finish for my PCB?
When selecting a surface finish for your PCB, consider factors such as: - Solderability and ease of assembly
- Durability and shelf life
- Compatibility with the selected components and assembly processes
-
Cost constraints
HASL and OSP are generally the most cost-effective options, while ENIG, IAg, and ISn offer improved performance at a higher cost. -
What steps can I take to ensure the quality and reliability of my assembled PCBs?
To ensure the quality and reliability of your assembled PCBs, consider implementing the following measures: - Conduct thorough design reviews to identify and address potential issues early in the process
- Choose a reputable assembly partner with a proven track record of quality and reliability
- Implement comprehensive inspection and testing processes, such as AOI, X-ray, ICT, and functional testing
- Establish clear quality control standards and communication channels with your assembly partner
- Regularly review and analyze quality metrics to identify areas for improvement
In conclusion, understanding the key manufacturing factors that affect PCB assembly costs is essential for businesses looking to optimize their assembly processes and manage expenses effectively. By carefully considering factors such as design complexity, material selection, manufacturing volume, assembly processes, and turnaround time, businesses can make informed decisions that balance cost, quality, and performance requirements. Partnering with an experienced and reputable PCB assembly provider can also help navigate these challenges and ensure the successful production of high-quality, reliable PCBs.
0 Comments