Introduction to Plated-through Holes (PTHs)
Plated-through holes (PTHs) are an essential feature of modern printed circuit boards (PCBs). These holes, which are drilled through the PCB and then plated with a conductive material, serve as electrical connections between different layers of the board. PTHs enable the creation of complex, multi-layer PCBs that can accommodate a high density of components and circuitry.
What are Plated-through Holes?
Plated-through holes are holes that are drilled through a PCB and then plated with a conductive material, typically copper. The plating process creates an electrical connection between the different layers of the PCB, allowing signals and power to be routed vertically through the board.
PTHs are used for several purposes in PCB design:
- To mount through-hole components, such as resistors, capacitors, and connectors
- To create vias, which are used to route signals between different layers of the board
- To provide mechanical strength and stability to the PCB
The PTH Manufacturing Process
The creation of plated-through holes involves several steps, each of which must be carefully controlled to ensure the quality and reliability of the final product.
Step 1: Drilling
The first step in creating PTHs is to drill holes through the PCB substrate. This is typically done using a computer-controlled drilling machine, which can drill holes with a diameter as small as 0.1 mm. The drilling process must be precise to ensure that the holes are positioned correctly and have the correct diameter.
Step 2: Deburring and Cleaning
After drilling, the holes must be deburred to remove any rough edges or debris that could interfere with the plating process. This is typically done using a mechanical deburring machine or a chemical etching process. The holes are then thoroughly cleaned to remove any remaining debris and prepare the surface for plating.
Step 3: Electroless Copper Deposition
The next step is to deposit a thin layer of copper onto the walls of the holes using an electroless plating process. This involves immersing the PCB in a bath of copper sulfate solution and adding a reducing agent, which causes the copper to deposit onto the surface of the holes. The electroless copper layer serves as a conductive base for the subsequent electrolytic plating process.
Step 4: Electrolytic Copper Plating
After the electroless copper layer has been deposited, the PCB is placed in an electrolytic plating bath, where a thicker layer of copper is deposited onto the walls of the holes. This process involves applying an electric current to the PCB, which causes the copper ions in the plating solution to be attracted to the surface of the holes. The thickness of the copper plating can be controlled by adjusting the current and the duration of the plating process.
Step 5: Inspection and Testing
Once the plating process is complete, the PCB must be inspected and tested to ensure that the PTHs meet the required specifications. This typically involves using an automated optical inspection (AOI) machine to check the diameter, position, and plating thickness of each hole. Electrical testing may also be performed to verify the continuity and resistance of the PTHs.
PTH Design Considerations
When designing a PCB with plated-through holes, there are several factors that must be taken into account to ensure the reliability and performance of the final product.
Hole Diameter and Aspect Ratio
The diameter of the PTHs and the thickness of the PCB substrate determine the aspect ratio of the holes. The aspect ratio is defined as the ratio of the hole depth to the hole diameter. In general, a higher aspect ratio makes it more difficult to achieve uniform plating thickness and can increase the risk of voids or other defects in the plating.
PCB Thickness (mm) | Minimum Hole Diameter (mm) | Maximum Aspect Ratio |
---|---|---|
0.4 | 0.2 | 8:1 |
0.8 | 0.3 | 10:1 |
1.6 | 0.4 | 12:1 |
2.4 | 0.5 | 14:1 |
Table 1: Recommended maximum aspect ratios for different PCB thicknesses and hole diameters.
To minimize the risk of plating defects, it is generally recommended to keep the aspect ratio below 10:1 for standard PCBs and below 8:1 for high-reliability applications.
Pad Size and Annular Ring
The pad size and annular ring are critical design parameters for PTHs. The pad is the copper area surrounding the hole on the outer layers of the PCB, while the annular ring is the width of the copper area between the edge of the hole and the edge of the pad.
Hole Diameter (mm) | Minimum Pad Diameter (mm) | Minimum Annular Ring (mm) |
---|---|---|
0.2 | 0.6 | 0.15 |
0.3 | 0.7 | 0.15 |
0.4 | 0.8 | 0.2 |
0.5 | 0.9 | 0.2 |
0.6 | 1.0 | 0.2 |
Table 2: Recommended minimum pad diameters and annular rings for different hole diameters.
The pad size and annular ring must be large enough to provide sufficient mechanical strength and electrical conductivity, while also allowing for manufacturing tolerances. In general, the minimum annular ring should be at least 0.15 mm for standard PCBs and 0.2 mm for high-reliability applications.
Hole-to-Hole Spacing
The spacing between PTHs is another important design consideration, as it affects the manufacturability and reliability of the PCB. If the holes are too close together, there is a risk of drilling or plating defects, as well as electrical shorts between adjacent holes.
PCB Thickness (mm) | Minimum Hole-to-Hole Spacing (mm) |
---|---|
0.4 | 0.5 |
0.8 | 0.6 |
1.6 | 0.8 |
2.4 | 1.0 |
Table 3: Recommended minimum hole-to-hole spacing for different PCB thicknesses.
The minimum hole-to-hole spacing depends on the thickness of the PCB and the diameter of the holes. In general, a spacing of at least 0.5 mm is recommended for standard PCBs, while high-reliability applications may require a spacing of 1.0 mm or more.
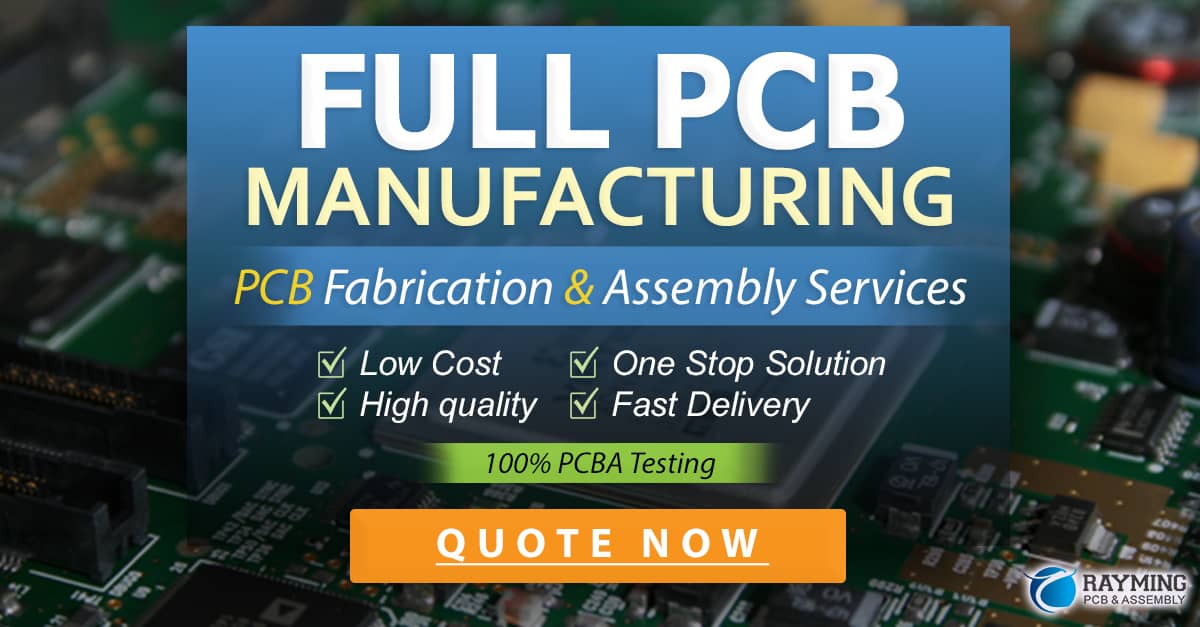
PTH Reliability and Failure Modes
Plated-through holes are critical components of PCBs, and their reliability is essential for the overall performance and longevity of the final product. There are several failure modes that can affect PTHs, each of which must be carefully managed through proper design and manufacturing practices.
Barrel Cracking
Barrel cracking is a common failure mode for PTHs, particularly in high-reliability applications such as aerospace and military electronics. This type of failure occurs when the copper plating in the hole develops cracks or fissures, which can lead to electrical opens or intermittent connections.
Barrel cracking is typically caused by thermal stress, which can occur during soldering or during temperature cycling in the field. To minimize the risk of barrel cracking, it is important to use a high-quality plating process and to design the PCB with sufficient thermal relief around the PTHs.
Interfacial Separation
Interfacial separation is another failure mode that can affect PTHs. This occurs when the copper plating separates from the walls of the hole, creating a gap or void that can disrupt the electrical connection.
Interfacial separation can be caused by a variety of factors, including poor adhesion between the copper plating and the hole walls, contamination or debris in the holes, and mechanical stress during assembly or use. To minimize the risk of interfacial separation, it is important to use a high-quality cleaning and deburring process, as well as a plating process that promotes good adhesion.
Plating Voids
Plating voids are another common defect that can affect the reliability of PTHs. These are areas where the copper plating is thin or missing, creating a gap or void in the electrical connection.
Plating voids can be caused by a variety of factors, including air bubbles or debris in the plating solution, inadequate agitation or filtration of the plating bath, and variations in the hole geometry or surface finish. To minimize the risk of plating voids, it is important to use a high-quality plating process with appropriate process controls and quality assurance measures.
Testing and Inspection of PTHs
To ensure the reliability and performance of PTHs, it is important to perform thorough testing and inspection at various stages of the manufacturing process.
Visual Inspection
Visual inspection is the first line of defense against PTH defects. This involves using a microscope or other optical inspection equipment to examine the holes for any visible defects, such as drilling or plating errors, debris or contamination, or damage to the copper plating.
Visual inspection is typically performed after drilling, deburring, and plating, as well as after any subsequent processing steps such as solder mask application or final assembly.
Automated Optical Inspection (AOI)
Automated optical inspection (AOI) is a more advanced form of visual inspection that uses computer vision and image analysis techniques to detect and classify defects in PTHs and other PCB features.
AOI systems can quickly and accurately inspect large numbers of holes and identify defects such as plating voids, barrel cracks, and interfacial separation. AOI is typically used in high-volume production environments where manual inspection is not practical or cost-effective.
Electrical Testing
Electrical testing is another important method for verifying the reliability and performance of PTHs. This involves measuring the electrical continuity and resistance of the holes using specialized test equipment such as a four-wire Kelvin probe or a flying probe tester.
Electrical testing can detect defects such as open circuits, short circuits, and high-resistance connections that may not be visible through visual inspection alone. Electrical testing is typically performed after final assembly and before shipping the PCB to the customer.
Frequently Asked Questions (FAQ)
What is the difference between a through-hole and a blind or buried via?
A through-hole is a hole that goes all the way through the PCB, while a blind via only goes through some of the layers and a buried via is completely internal to the board and does not extend to either surface.
Can PTHs be used for high-frequency signals?
Yes, PTHs can be used for high-frequency signals, but the design must take into account factors such as the dielectric constant and loss tangent of the PCB material, the geometry and spacing of the holes, and the thickness and uniformity of the copper plating. In general, smaller holes with thicker plating and tighter spacing will have better high-frequency performance.
What is the minimum hole size that can be reliably plated?
The minimum hole size that can be reliably plated depends on the capabilities of the PCB manufacturer and the specific plating process used. In general, holes as small as 0.2 mm in diameter can be plated with good reliability, but smaller holes may require specialized equipment and processes.
How can PTH reliability be improved in harsh environments?
To improve PTH reliability in harsh environments, such as those with high temperatures, vibration, or corrosive chemicals, several strategies can be used:
- Use a high-quality base material with good thermal and mechanical properties, such as polyimide or PTFE.
- Use a thicker copper plating, typically 25 µm or more, to provide additional strength and conductivity.
- Use a conformal coating or encapsulation to protect the PTHs from environmental factors.
- Use a strain relief or underfill material to reduce mechanical stress on the PTHs during assembly and use.
What are the most common causes of PTH failures?
The most common causes of PTH failures include:
- Thermal stress during soldering or temperature cycling, leading to barrel cracking or interfacial separation.
- Mechanical stress during assembly or use, leading to pad lifting or hole wall damage.
- Contamination or debris in the holes, leading to plating voids or poor adhesion.
- Inadequate plating thickness or uniformity, leading to high resistance or open circuits.
- Manufacturing defects such as drilling errors, over-deburring, or improper cleaning.
By understanding these failure modes and implementing appropriate design and manufacturing controls, the reliability and performance of PTHs can be maximized for a wide range of applications.
0 Comments