What is a PCB Prototype?
A PCB prototype, also known as a printed circuit board prototype, is the initial version of a PCB design used for testing and validation before mass production. It allows engineers and designers to physically test the functionality, performance, and reliability of their PCB design in real-world conditions.
PCB prototypes are essential in the development process of electronic devices, as they help identify and resolve any design flaws or issues early on, saving time and money in the long run. They also provide an opportunity to optimize the design for manufacturability and cost-effectiveness.
Types of PCB Prototypes
There are several types of PCB prototypes, each with its own purpose and characteristics:
-
Breadboard Prototype: A breadboard is a simple, reusable prototyping board that allows for quick and easy assembly of electronic components without soldering. It is often used for initial circuit testing and proof-of-concept.
-
Stripboard Prototype: A stripboard, also known as a veroboard, is a pre-fabricated board with a grid of copper strips on one side. Components are soldered onto the stripboard to create the circuit. Stripboards are more durable than breadboards and are suitable for more complex circuits.
-
PCB Prototype: A PCB prototype is a custom-designed and fabricated board that closely resembles the final product. It is made using the same materials and processes as the final PCB but in smaller quantities. PCB prototypes are used for thorough testing and validation before mass production.
Prototype Type | Advantages | Disadvantages |
---|---|---|
Breadboard | – Quick and easy assembly – Reusable – No soldering required |
– Limited complexity – Not durable – Prone to loose connections |
Stripboard | – More durable than breadboards – Suitable for more complex circuits – Low cost |
– Requires soldering – Limited flexibility in layout – Not as professional-looking as PCB prototypes |
PCB Prototype | – Custom-designed – Closely resembles final product – Suitable for thorough testing and validation |
– Higher cost than breadboards and stripboards – Longer lead time – Requires CAD skills for design |
Why You Need a PCB Prototype
1. Test and Validate Your Design
The primary reason for creating a PCB prototype is to test and validate your design before committing to mass production. A prototype allows you to physically test the functionality, performance, and reliability of your PCB in real-world conditions. This helps identify any design flaws or issues early on, saving time and money in the long run.
Some of the key aspects that can be tested with a PCB prototype include:
- Functionality: Ensure that the PCB performs as intended and meets the design specifications.
- Signal Integrity: Verify that the signals are propagating correctly through the board without distortion or interference.
- Power Integrity: Confirm that the power distribution network is stable and provides the required voltage and current to all components.
- Thermal Management: Assess the thermal performance of the PCB and ensure that the components operate within their specified temperature ranges.
- Mechanical Fit: Check that the PCB fits correctly in the enclosure and interfaces properly with other components.
2. Optimize for Manufacturability
Creating a PCB prototype allows you to optimize your design for manufacturability. This involves making sure that the PCB can be efficiently and reliably produced in large quantities. Some of the aspects to consider for manufacturability include:
- Component Placement: Ensure that the components are placed in a way that facilitates automated assembly and minimizes the risk of defects.
- Routing: Optimize the routing of traces to minimize the board size, reduce signal interference, and improve manufacturability.
- Design Rule Check (DRC): Verify that the PCB design adheres to the manufacturing guidelines and constraints, such as minimum trace width, clearance, and hole size.
- Testability: Incorporate test points and other features that facilitate automated testing and inspection during production.
By optimizing your design for manufacturability with a PCB prototype, you can reduce production costs, improve yields, and ensure a smooth transition to mass production.
3. Evaluate Cost and Feasibility
Creating a PCB prototype allows you to evaluate the cost and feasibility of your design before investing in mass production. This helps you make informed decisions about the viability of your product and identify opportunities for cost optimization.
Some of the cost factors to consider when evaluating a PCB prototype include:
- Material Costs: Assess the cost of the PCB materials, such as the substrate, copper, solder mask, and silkscreen.
- Component Costs: Evaluate the cost of the electronic components used in the design and consider alternative components if necessary.
- Manufacturing Costs: Estimate the cost of fabricating and assembling the PCB in various quantities, taking into account setup costs, tooling, and labor.
- Testing and Certification Costs: Consider the cost of testing and certifying the PCB to ensure compliance with industry standards and regulations.
By evaluating the cost and feasibility of your PCB prototype, you can make informed decisions about the commercial viability of your product and identify opportunities for cost optimization.
How to Create a PCB Prototype
Creating a PCB prototype involves several steps, from design to fabrication and assembly. Here is a general overview of the process:
1. Design the PCB
The first step in creating a PCB prototype is to design the board using a PCB design software, such as Altium Designer, Eagle, or KiCad. This involves creating a schematic diagram of the circuit, selecting the appropriate components, and laying out the board.
When designing the PCB, consider the following factors:
- Schematic Design: Create a schematic diagram of the circuit, ensuring that all components are correctly connected and the design meets the functional requirements.
- Component Selection: Choose the appropriate components for your design, considering factors such as performance, cost, and availability.
- Board Layout: Lay out the components and traces on the board, following best practices for signal integrity, power integrity, and manufacturability.
- Design Rule Check: Verify that the PCB design adheres to the manufacturing guidelines and constraints, such as minimum trace width, clearance, and hole size.
2. Generate Gerber Files
Once the PCB design is complete, generate the Gerber files, which are the industry-standard format for PCB fabrication. Gerber files contain all the necessary information for manufacturing the PCB, including the copper layers, solder mask, silkscreen, and drill data.
Most PCB design software can generate Gerber files automatically, but it is important to review the files to ensure that they are accurate and complete.
3. Choose a PCB Manufacturer
Choose a reputable PCB manufacturer to fabricate your prototype. Consider factors such as manufacturing capabilities, turnaround time, cost, and quality when selecting a manufacturer.
Many PCB manufacturers offer online quoting and ordering, allowing you to upload your Gerber files and receive a quote quickly. Some popular PCB Prototype Manufacturers include:
- JLCPCB: Offers low-cost, high-quality PCB prototypes with quick turnaround times.
- PCBWay: Provides a wide range of PCB fabrication and assembly services, including prototypes and low-volume production.
- OSH Park: Specializes in small-batch PCB fabrication, offering high-quality boards at competitive prices.
4. Fabricate and Assemble the PCB
Once you have selected a manufacturer and placed your order, the PCB will be fabricated and assembled according to your specifications. The fabrication process typically involves the following steps:
- Film Generation: The Gerber files are used to create photographic films of each layer of the PCB.
- Copper Etching: The films are used to selectively etch away unwanted copper from the substrate, leaving the desired circuit pattern.
- Lamination: The etched layers are laminated together to form the complete PCB.
- Drilling: Holes are drilled in the PCB for through-hole components and vias.
- Solder Mask and Silkscreen: A solder mask is applied to protect the copper traces, and a silkscreen is added for component labeling and identification.
After fabrication, the PCB is assembled with the specified components, either by hand or using automated assembly equipment.
5. Test and Validate the Prototype
Once the PCB prototype is fabricated and assembled, it is important to thoroughly test and validate its functionality, performance, and reliability. This involves conducting various tests, such as:
- Continuity Test: Verify that all connections are properly made and there are no short circuits or open circuits.
- Power-On Test: Apply power to the board and ensure that it functions as expected without any smoke, sparks, or overheating.
- Functional Test: Test the various functions of the board, such as input/output, communication, and data processing, to ensure that they meet the design specifications.
- Signal Integrity Test: Analyze the signal quality and integrity using an oscilloscope or other testing equipment to ensure that the signals are clean and free from distortion or interference.
- Environmental Test: Subject the PCB to various environmental conditions, such as temperature, humidity, and vibration, to assess its durability and reliability.
By thoroughly testing and validating the PCB prototype, you can identify and resolve any issues before proceeding to mass production.
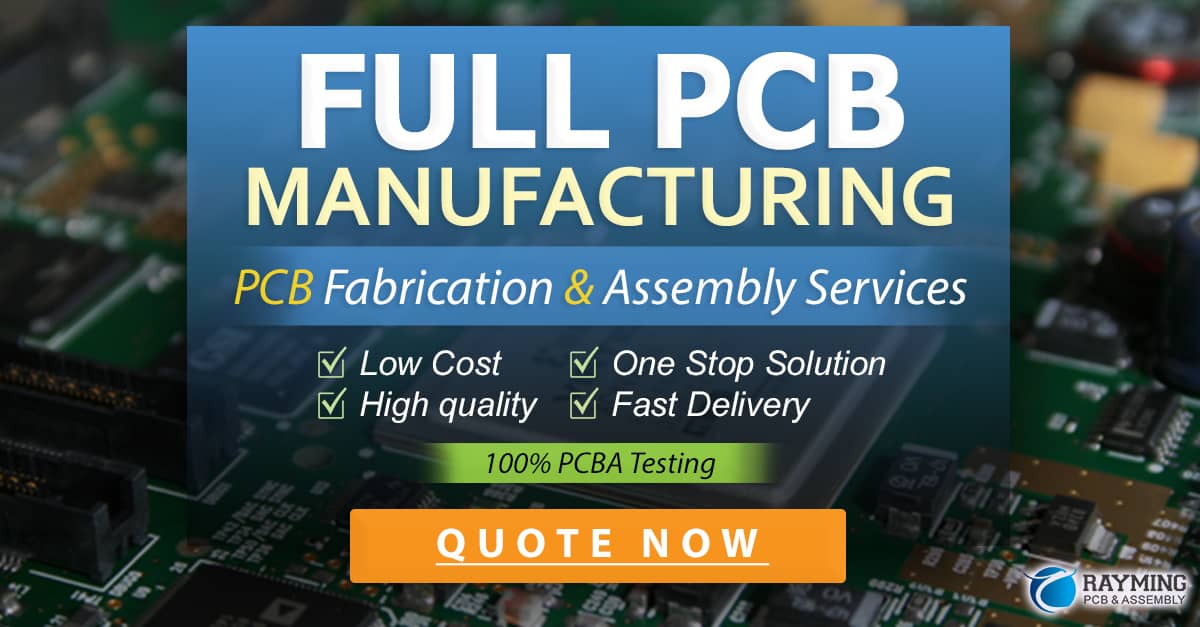
Frequently Asked Questions (FAQ)
1. How much does it cost to create a PCB prototype?
The cost of creating a PCB prototype varies depending on factors such as the size and complexity of the board, the number of layers, the quantity ordered, and the turnaround time. On average, a simple 2-layer PCB prototype can cost anywhere from $50 to $500, while a more complex multi-layer board can cost several thousand dollars.
Many PCB manufacturers offer online quoting tools that allow you to upload your Gerber files and receive an instant quote based on your specifications.
2. How long does it take to create a PCB prototype?
The turnaround time for creating a PCB prototype depends on the complexity of the board and the manufacturer’s workload. On average, a simple PCB prototype can be fabricated and assembled in 1-2 weeks, while a more complex board may take 3-4 weeks or longer.
Some PCB manufacturers offer expedited services for an additional fee, allowing you to receive your prototype in as little as 24-48 hours.
3. What factors should I consider when choosing a PCB manufacturer?
When choosing a PCB manufacturer for your prototype, consider the following factors:
- Manufacturing Capabilities: Ensure that the manufacturer has the necessary equipment and expertise to fabricate your PCB according to your specifications.
- Turnaround Time: Consider the manufacturer’s standard turnaround time and whether they offer expedited services if needed.
- Cost: Compare the prices of different manufacturers and ensure that they are competitive and within your budget.
- Quality: Look for manufacturers with a reputation for producing high-quality PCBs and who have strict quality control processes in place.
- Customer Support: Choose a manufacturer with responsive and knowledgeable customer support to assist you throughout the prototyping process.
4. Can I assemble the PCB prototype myself?
Yes, it is possible to assemble the PCB prototype yourself if you have the necessary skills, tools, and equipment. However, hand assembly can be time-consuming and prone to errors, especially for complex boards with many components.
If you choose to assemble the prototype yourself, ensure that you have the following:
- Soldering Equipment: You will need a soldering iron, solder, and other soldering tools to attach the components to the board.
- Component Inventory: Ensure that you have all the necessary components on hand and that they are the correct values and package sizes.
- Magnification and Lighting: Use a magnifying lens or microscope and adequate lighting to ensure precise placement and soldering of small components.
- Static Protection: Use an anti-static mat and wrist strap to protect sensitive components from electrostatic discharge (ESD) during handling.
If you are not confident in your assembly skills or if the board is too complex, it is recommended to have the PCB assembled by a professional assembly service.
5. What are the advantages of using a PCB prototype service?
Using a PCB prototype service offers several advantages, including:
- Time Savings: PCB prototype services have streamlined processes and automated equipment that can fabricate and assemble your board much faster than doing it yourself.
- Cost Savings: Prototype services can often produce PCBs at a lower cost than in-house fabrication due to economies of scale and bulk purchasing of materials.
- Quality Assurance: Professional prototype services have strict quality control processes in place to ensure that your PCB meets the highest standards of quality and reliability.
- Design Support: Many prototype services offer design review and feedback to help you optimize your PCB design for manufacturability and cost-effectiveness.
- Flexibility: Prototype services can accommodate a wide range of PCB specifications and requirements, from simple single-layer boards to complex multi-layer designs.
By using a PCB prototype service, you can save time and money while ensuring that your PCB is of the highest quality and ready for mass production.
Conclusion
In conclusion, a PCB prototype is an essential tool in the development process of electronic devices, allowing engineers and designers to test, validate, and optimize their designs before committing to mass production. Creating a PCB prototype involves several steps, from design to fabrication and assembly, and requires careful consideration of factors such as functionality, manufacturability, and cost.
By thoroughly testing and validating the PCB prototype, you can identify and resolve any issues early on, saving time and money in the long run. When choosing a PCB manufacturer for your prototype, consider factors such as manufacturing capabilities, turnaround time, cost, quality, and customer support to ensure the best possible outcome.
Whether you choose to assemble the PCB prototype yourself or use a professional prototype service, the benefits of creating a prototype are clear. By investing in a PCB prototype, you can bring your electronic device to market faster, with higher quality and reliability, and at a lower overall cost.
0 Comments