Introduction to Medical PCB prototypes
The medical industry has been experiencing a rapid growth in the demand for advanced electronic devices and equipment. This has led to an increasing need for the fabrication and build out of medical PCB (Printed Circuit Board) prototypes. PCB prototypes play a crucial role in the development and testing of medical devices, ensuring their reliability, safety, and effectiveness.
What are Medical PCB Prototypes?
Medical PCB prototypes are custom-designed circuit boards that are used in the development and testing of medical devices. These prototypes are created to meet the specific requirements of the medical industry, such as high reliability, accuracy, and safety standards. They are used to validate the design and functionality of the medical device before mass production.
Importance of Medical PCB Prototypes
Medical PCB prototypes are essential for the following reasons:
-
Design Validation: PCB prototypes allow medical device manufacturers to validate the design of their devices before mass production. This helps to identify any design flaws or issues early in the development process, saving time and money.
-
Functionality Testing: PCB prototypes enable manufacturers to test the functionality of their devices under various conditions. This helps to ensure that the device works as intended and meets the required specifications.
-
Regulatory Compliance: Medical devices are subject to strict regulatory requirements, such as FDA (Food and Drug Administration) regulations. PCB prototypes help manufacturers to ensure that their devices comply with these regulations before mass production.
-
Cost Savings: PCB prototypes allow manufacturers to identify and fix any issues early in the development process, which can save significant costs in the long run. This is because fixing issues during mass production can be much more expensive than fixing them during the prototype stage.
Growing Demand for Medical PCB Prototypes
The demand for medical PCB prototypes has been growing rapidly in recent years. This growth can be attributed to several factors, including:
Technological Advancements
The medical industry has been experiencing rapid technological advancements in recent years. This has led to the development of more advanced and sophisticated medical devices, such as wearable devices, implantable devices, and diagnostic equipment. These devices require high-quality PCB prototypes to ensure their reliability and effectiveness.
Aging Population
The aging population has been driving the demand for medical devices and equipment. As people live longer, they are more likely to experience age-related health issues, such as chronic diseases and disabilities. This has led to an increased demand for medical devices and equipment, which in turn has driven the demand for medical PCB prototypes.
Increasing Prevalence of Chronic Diseases
The increasing prevalence of chronic diseases, such as diabetes, cardiovascular diseases, and cancer, has been driving the demand for medical devices and equipment. These devices are used for diagnosis, monitoring, and treatment of chronic diseases, and require high-quality PCB prototypes to ensure their accuracy and reliability.
COVID-19 Pandemic
The COVID-19 pandemic has also been driving the demand for medical devices and equipment, such as ventilators, oxygen concentrators, and diagnostic tests. This has led to an increased demand for medical PCB prototypes to support the development and production of these devices.
Challenges in Medical PCB Prototype Fabrication
Despite the growing demand for medical PCB prototypes, there are several challenges that manufacturers face in their fabrication and build out. These challenges include:
Strict Regulatory Requirements
Medical devices are subject to strict regulatory requirements, such as FDA regulations, which govern their design, manufacture, and use. These regulations can be complex and time-consuming to navigate, and require manufacturers to ensure that their PCB prototypes meet all the necessary requirements.
High Reliability and Safety Standards
Medical devices require high levels of reliability and safety to ensure patient safety and effective treatment. This requires manufacturers to use high-quality materials and components in their PCB prototypes, and to follow strict quality control processes to ensure that the prototypes meet the required standards.
Complex Designs
Medical devices are often complex and require intricate PCB designs to ensure their functionality and effectiveness. This can be challenging for manufacturers, as it requires specialized knowledge and expertise in PCB design and fabrication.
Rapid Technological Advancements
The medical industry is constantly evolving, with new technologies and advancements being introduced at a rapid pace. This requires manufacturers to stay up-to-date with the latest trends and technologies in PCB design and fabrication, and to adapt their processes and capabilities accordingly.
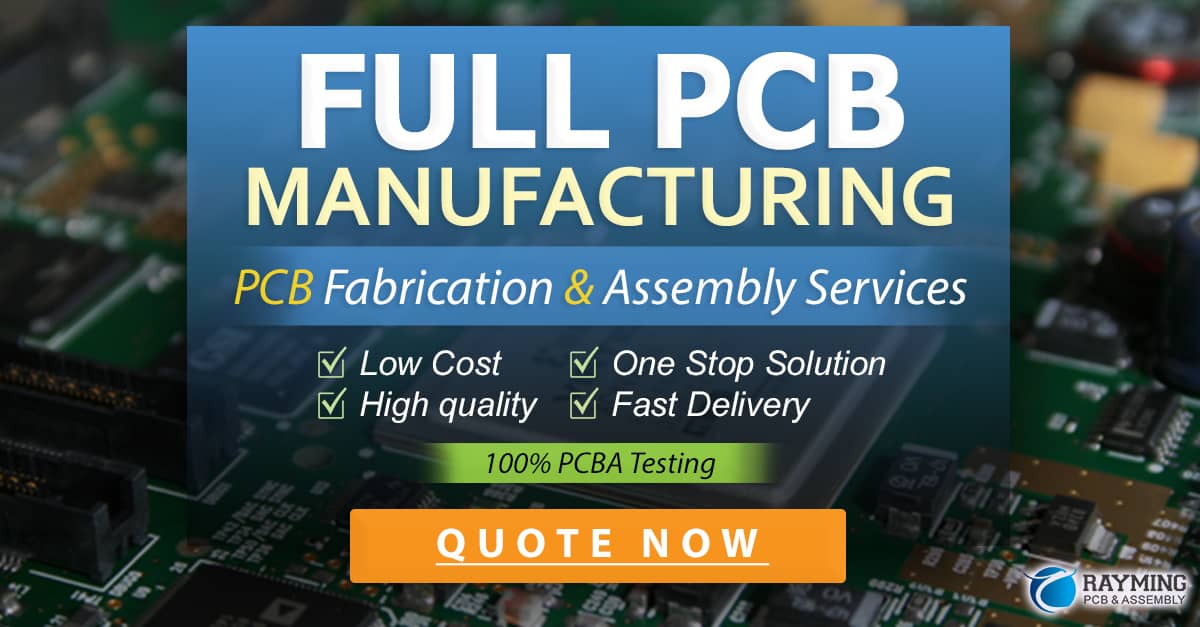
Best Practices in Medical PCB Prototype Fabrication
To overcome these challenges and ensure the successful fabrication and build out of medical PCB prototypes, manufacturers should follow best practices such as:
Choosing the Right PCB Fabrication Partner
Choosing the right PCB fabrication partner is crucial for the success of medical PCB prototype projects. Manufacturers should look for partners with experience in the medical industry, a proven track record of quality and reliability, and the necessary certifications and accreditations.
Ensuring Regulatory Compliance
Manufacturers should ensure that their PCB prototypes comply with all the necessary regulatory requirements, such as FDA regulations. This requires a deep understanding of the regulatory landscape and the ability to navigate complex requirements and standards.
Implementing Strict Quality Control Processes
Manufacturers should implement strict quality control processes to ensure that their PCB prototypes meet the required reliability and safety standards. This includes testing and validation at every stage of the fabrication process, as well as thorough documentation and traceability.
Investing in Advanced Technologies and Equipment
Manufacturers should invest in advanced technologies and equipment to support the fabrication and build out of medical PCB prototypes. This includes state-of-the-art PCB design software, high-precision manufacturing equipment, and advanced testing and validation tools.
Collaborating with Medical Device Manufacturers
Manufacturers should collaborate closely with medical device manufacturers to ensure that their PCB prototypes meet the specific requirements and specifications of the device. This requires open communication, flexibility, and a willingness to adapt to changing needs and requirements.
Future Trends in Medical PCB Prototype Fabrication
As the medical industry continues to evolve and advance, there are several future trends that are likely to shape the fabrication and build out of medical PCB prototypes. These trends include:
Miniaturization
There is a growing trend towards miniaturization in the medical industry, with devices becoming smaller, more compact, and more portable. This requires manufacturers to develop PCB prototypes that are smaller, more complex, and more densely packed with components.
Wearable Devices
Wearable devices, such as smartwatches and fitness trackers, are becoming increasingly popular in the medical industry. These devices require PCB prototypes that are flexible, lightweight, and able to withstand the rigors of daily wear and tear.
Wireless Connectivity
Wireless connectivity is becoming increasingly important in the medical industry, with devices requiring the ability to communicate with each other and with healthcare providers. This requires PCB prototypes that are able to support wireless technologies such as Bluetooth and Wi-Fi.
Artificial Intelligence and Machine Learning
Artificial intelligence and machine learning are emerging as key technologies in the medical industry, with the potential to revolutionize diagnosis, treatment, and patient care. This requires PCB prototypes that are able to support complex algorithms and processing capabilities.
The Importance of Medical PCB Prototypes Fabrication
Medical PCB prototypes fabrication is a critical component in developing medical devices across the world. Here are some of the key reasons why medical PCB prototype fabrication is so important:
-
Developing new technology: Medical PCB prototypes are essential in developing new medical technology that improves patient care and reduces healthcare costs. By creating prototypes, medical device manufacturers can test out new ideas and innovations before bringing them to market. This allows for refinements and improvements to be made to the device before it is mass-produced and sold to customers.
-
Ensuring quality and reliability: Medical PCB prototypes are used to test and validate the design and functionality of medical devices before they are released to the market. This ensures that the device meets all necessary quality and reliability standards, which is essential for patient safety and effective treatment. By thoroughly testing prototypes, manufacturers can identify and address any issues or defects before the device goes into mass production.
-
Meeting regulatory requirements: Medical devices are subject to strict regulatory requirements, such as those set by the FDA in the United States. Medical PCB prototypes are used to demonstrate that the device meets these regulatory requirements, which is necessary for obtaining approval to sell the device on the market. By creating prototypes that meet regulatory standards, manufacturers can avoid costly delays and setbacks in bringing their products to market.
-
Reducing costs: Medical PCB prototypes can help reduce the overall cost of developing and producing medical devices. By identifying and addressing issues early in the development process, manufacturers can avoid costly mistakes and rework later on. Additionally, by thoroughly testing and validating prototypes, manufacturers can ensure that the final product is of high quality and reliability, which can reduce warranty claims and other costs associated with defective devices.
Overall, medical PCB prototypes are a critical component in the development and production of medical devices. They allow manufacturers to innovate, ensure quality and reliability, meet regulatory requirements, and reduce costs. As the demand for medical devices continues to grow, the importance of medical PCB prototype fabrication will only continue to increase.
FAQs
1. What are the key considerations when selecting a PCB fabrication partner for medical devices?
When selecting a PCB fabrication partner for medical devices, there are several key considerations to keep in mind:
- Experience and expertise in the medical industry
- Quality control processes and certifications (e.g. ISO 13485)
- Ability to meet regulatory requirements (e.g. FDA)
- Advanced manufacturing capabilities and equipment
- Flexibility and responsiveness to changing needs and requirements
2. What are some common challenges in medical PCB prototype fabrication?
Some common challenges in medical PCB prototype fabrication include:
- Strict regulatory requirements and standards
- High reliability and safety requirements
- Complex and specialized designs
- Rapid technological advancements and changing requirements
- Cost and time constraints
3. How can manufacturers ensure the quality and reliability of medical PCB prototypes?
To ensure the quality and reliability of medical PCB prototypes, manufacturers can:
- Implement strict quality control processes and testing procedures
- Use high-quality materials and components
- Follow best practices in PCB design and fabrication
- Work with experienced and certified PCB fabrication partners
- Thoroughly document and track the fabrication process
4. What are some emerging trends in medical PCB prototype fabrication?
Some emerging trends in medical PCB prototype fabrication include:
- Miniaturization and increased complexity of designs
- Use of flexible and wearable PCB materials
- Wireless connectivity and Internet of Things (IoT) integration
- Artificial intelligence and machine learning capabilities
- Sustainability and eco-friendly manufacturing processes
5. How can medical device manufacturers collaborate effectively with PCB fabrication partners?
To collaborate effectively with PCB fabrication partners, medical device manufacturers can:
- Clearly communicate requirements and specifications
- Provide detailed documentation and design files
- Work closely with the fabrication team to address any issues or challenges
- Establish clear timelines and milestones
- Foster a collaborative and transparent relationship based on trust and mutual understanding
Conclusion
The fabrication and build out of medical PCB prototypes is a critical process in the development and production of medical devices. As the demand for these devices continues to grow, driven by factors such as technological advancements, an aging population, and the increasing prevalence of chronic diseases, the importance of medical PCB prototypes will only continue to increase.
However, the fabrication of medical PCB prototypes also presents several challenges, including strict regulatory requirements, high reliability and safety standards, complex designs, and rapid technological advancements. To overcome these challenges and ensure the successful fabrication of medical PCB prototypes, manufacturers must follow best practices such as choosing the right PCB fabrication partner, ensuring regulatory compliance, implementing strict quality control processes, investing in advanced technologies and equipment, and collaborating closely with medical device manufacturers.
Looking to the future, there are several trends that are likely to shape the fabrication and build out of medical PCB prototypes, including miniaturization, wearable devices, wireless connectivity, and artificial intelligence and machine learning. As these trends continue to evolve and mature, manufacturers will need to adapt their processes and capabilities to stay ahead of the curve and meet the changing needs of the medical industry.
In conclusion, the fabrication and build out of medical PCB prototypes is a critical process that plays a vital role in the development and production of medical devices. As the demand for these devices continues to grow, manufacturers must be prepared to meet the challenges and opportunities presented by this rapidly evolving industry, and to deliver high-quality, reliable, and safe PCB prototypes that meet the needs of patients and healthcare providers around the world.
0 Comments