Flexible printed circuits (FPCs) have become essential components in modern electronics. As devices continue getting smaller and more complex, FPCs provide many advantages over traditional rigid PCBs. FPC manufacturers play a crucial role in supplying these vital parts to electronics companies.
What Are FPCs and Why Are They Important?
An FPC, also known as a flex circuit, is a type of printed circuit board made from flexible polymer substrates like polyimide or polyester. The conductive traces are printed or laminated onto the substrate, allowing the FPC to bend and flex.
Here are some of the key benefits of FPCs:
- Space savings – FPCs can fold and bend, allowing them to fit into tight spaces where rigid boards won’t work. This makes them ideal for small consumer electronics.
- Weight reduction – FPC substrates are extremely lightweight, reducing the overall weight of products.
- Reliability – FPCs are resistant to vibration and thermal stresses that can damage rigid boards.
- Design flexibility – FPCs allow for creative industrial design features like hinges, sliding mechanisms, and 3D shapes.
As electronics become more compact and complex, FPCs become more necessary. Phone and laptop manufacturers rely on FPCs to interconnect components efficiently in tight spaces. Without FPC manufacturers, many of today’s sleek gadgets would not be possible.
The FPC Manufacturing Process
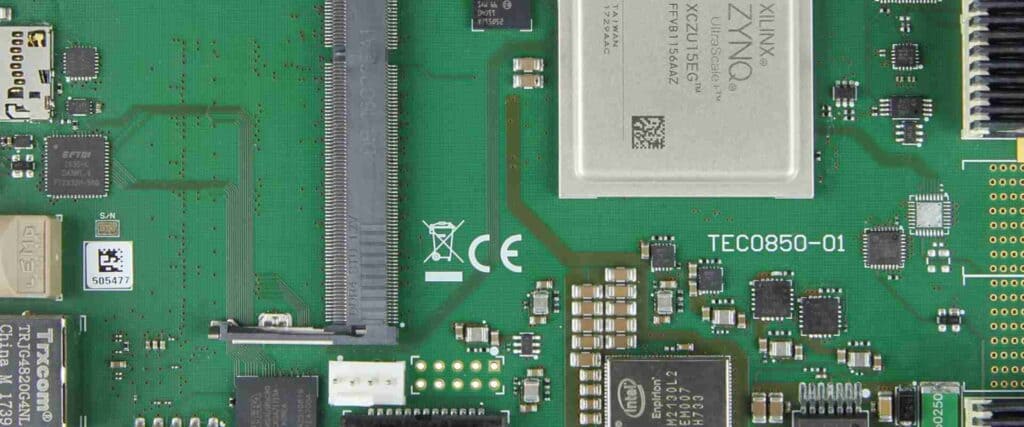
Producing high-quality FPCs requires advanced manufacturing techniques and specialized equipment. Here is an overview of the typical FPC fabrication process:
1. Base Material Preparation
FPC production starts with bare flexible copper-clad laminates made of materials like polyimide. The material comes in large rolls which are slit into desired widths for different circuit sizes.
2. Photolithography
Next, a photoresist coating is applied to the substrate. An image of the desired circuit layout is transferred to the material using UV light exposure through a photomask. Photolithography techniques are used to achieve the intricate trace patterns and thin trace widths required.
3. Etching
The photoresist is developed, leaving exposed copper regions unprotected. These areas are dissolved away with etching chemicals, isolating the traces of the circuit.
4. Photoresist Stripping
Once etching is complete, the remaining photoresist is stripped away, leaving just the bare copper traces on the substrate.
5. Die Cutting
The large circuit panels are precisely die cut into individual FPCs of the correct size and shape.
6. Connector Attachment
Connectors are attached to contact pads at the ends of traces to allow electrical connections.
7. Final Testing
Finished FPCs go through rigorous electrical testing before being shipped out to customers.
Key Capabilities of FPC Manufacturers
Building flex circuits requires extensive in-house capabilities and expertise:
- Design support – Work with customers on flex circuit design to ensure manufacturability.
- Precision photolithography – Produce intricate conductors, thin traces, and fine line spacing.
- Etching – In-house chemical etching for high-quality trace formation.
- Die cutting – Cut flex circuits precisely to customer specifications.
- Connector attachment – Have capabilities to attach various connector types like ZIF and FFC.
- Testing – Test all electrical parameters to guarantee full performance.
- Materials expertise – Knowledge of flexible substrate materials properties and processing requirements.
- Quality systems – Robust quality control and inspection processes.
- Prototyping – Fast prototype fabrication abilities.
- Volume production – Able to scale to high-volume manufacturing.
FPC manufacturers with these capabilities deliver products that meet the challenging demands of the electronics industry.
Major Applications of FPCs
FPCs have many uses across consumer and industrial electronics. Here are some of the top applications:
Consumer Electronics
Phones, laptops, tablets, wearables, game systems, and other mobile consumer devices all make extensive use of FPCs:
- Displays – FPCs connect LCD/OLED displays to mainboards. The folding allows for slim, compact designs.
- Cameras – In smartphone cameras, FPCs connect the small image sensor to the main logic board.
- Hinges – FPC “flexible spine” boards allow flipping and rotating display hinges.
- Buttons – FPCs connect the flat membrane switch panels under buttons.
Automotive
Vehicles utilize FPCs in engine control units, sensors, lighting, in-car entertainment, and other applications where flexibility and reliability are required.
Medical
Hearing aids, imaging devices, wearable monitors, and other medical electronics leverage FPC capabilities to interconnect tiny complex components.
Industrial
FPCs are found in robots, automation, VR headsets, instrumentation, and IoT devices for industrial environments.
Some examples of FPC applications:
Application | Use of FPC |
---|---|
Smartphones | Display connection, camera connection, button pads |
Laptops | Display and keyboard connection, touchpad flex circuits |
Wearables | Interconnect for smartwatch components |
Automotive | Flex circuits for engine sensors and control modules |
Hearing aids | Interconnects within the compact casing |
This table shows a few examples of how FPCs are used across products in major industries. Their unique properties make them a vital manufacturing component enabling the electronics revolution.
Leading Global FPC Manufacturers
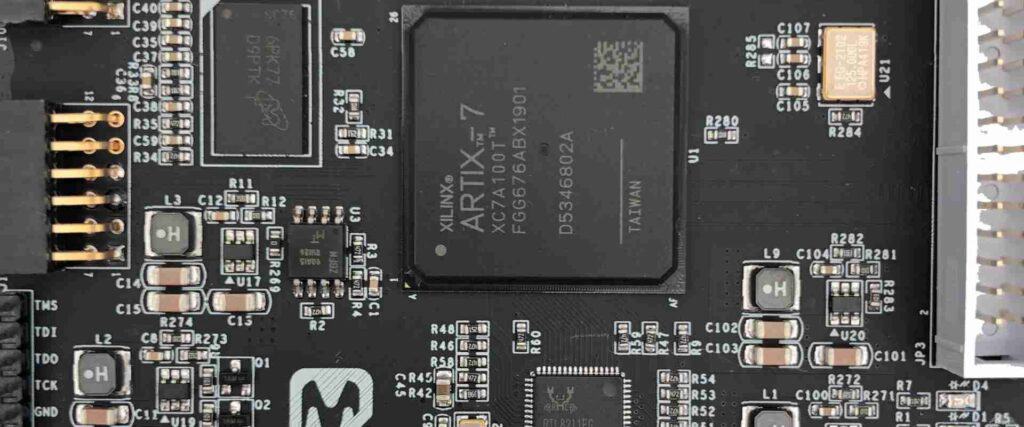
There are a number of large suppliers providing FPCs to major electronics brands worldwide. Here are some of the top FPC manufacturers:
- Career Technologies – Taiwanese company that is one of the leading FPC makers, they provide advanced HDI flex circuits.
- Flexium Interconnect – Another major Taiwan-based FPC company, their products appear in many consumer devices.
- MFLEX – USA flex circuit producer with facilities globally, they provide expertise in challenging niche applications.
- SIFLEX – Singapore flex circuit company focused on high-mix, low-volume flex manufacturing.
- Multi-Fineline Electronix (MFLEX) – Large global FPC company with plants in China and other Asian countries.
- Interflex – Japanese FPC giant that produces very high-quality flex circuits.
- Nitto Denko – Diversified Japanese material supplier that offers FPC production capabilities.
Most of these large FPC makers have multiple plants located strategically around the world. This allows them to support customers with volume production regionally. They continue to invest in advanced technologies and skills to improve capabilities.
Best Practices for Working with an FPC Partner
Electronics companies looking to leverage FPC technology in their products should follow these best practices when selecting an FPC manufacturing partner:
- Do research – Thoroughly research potential suppliers and audit their capabilities, expertise, quality systems, and manufacturing processes.
- Get samples – Have candidate FPC companies provide samples to test their work quality.
- Evaluate prototyping – Assess how well they handle prototype design support and fast prototype fabrication.
- Discuss capabilities – Have in-depth technical conversations about their production abilities for your specific application.
- Review certifications – Look for relevant quality certifications like ISO 9001, IATF 16949 in the automotive segment.
- Go on site – Tour candidate facilities in person to inspect their equipment, processes, and culture.
- Check references – Speak to other customers about their experiences working with the FPC partner.
- Ensure security – Verify they have strong IT security and protections for your intellectual property.
- Test volume abilities – Validate their skill in scaling up for high-volume manufacturing.
Selecting the right FPC manufacturing partner provides assurance of high product quality and reliable supply of this essential component.
The Future of Flex Circuits and FPC Manufacturing
The FPC industry expects continued strong growth as flexible interconnects become more pervasive across electronics. Here are some of the projections:
- Global FPC market projected to grow at 11% CAGR from 2020-2027.
- Expect high growth in FPCs for auto, industrial, and medical applications.
- Advances in flexible substrate materials enabling thinner, higher density circuits.
- Rising demand for high-speed, high-frequency FPCs.
- Growth of flexible hybrid electronics, integrating interconnection with flexible semiconductors.
- Demand for higher sophistication, integration, and miniaturization from FPCs.
- Technologies like printed electronics emerging for innovative flexible circuits.
FPC manufacturers will need to keep pace with rising volume demands while also upskilling to meet the need for continually advancing FPC technology. Companies that collaborate closely with leading FPC producers will benefit from access to cutting-edge flexible interconnect solutions.
Frequently Asked Questions About FPC Manufacturers
Here are some common questions about FPC manufacturers and working with FPC suppliers:
What are the key capabilities to look for in an FPC manufacturer?
Look for expertise in high-mix, low volume production. Seek manufacturers with strong design engineering support, prototyping abilities, high-precision manufacturing processes, and advanced quality controls. They should be knowledgeable about the latest flexible materials and technologies.
What certifications should an FPC company have?
Relevant quality certifications include ISO 9001, IATF 16949, ISO 13485 (for medical), AS9100 (aerospace), and ISO 14001 (environmental). These validate their quality management and capabilities.
Can FPC manufacturers scale to high production volumes?
The leading FPC suppliers have multiple international facilities and experience supporting high-volume consumer electronics manufacturing. However, it’s important to validate this by visiting their production lines.
Should I work with local or overseas FPC manufacturers?
Both options have pros and cons. Local suppliers allow easier communication and visits. Overseas partners can offer lower costs but need more coordination. Evaluate each based on capabilities, quality, communication, costs, and other factors.
How can FPC companies protect my intellectual property?
Reputable manufacturers have secure IT systems, facility access controls, and NDAs to protect customer IP and data. But you should still be careful about sharing sensitive design information unnecessarily.
What support do FPC companies provide during design and prototyping?
They should provide design for manufacturing rules and recommendations. Expect engineering reviews of circuit designs, material selection advice, and feedback to improve reliability. They also support prototyping iterations to refine the design.
How long does it take to get FPC prototypes?
With an existing design, prototypes can be delivered in around 2 weeks. The first prototypes may go through several revisions, which can be turned around in a few days by a good manufacturer.
What are signs of a good FPC manufacturer?
Quality products delivered consistently on time, responsiveness to problems, continuous improvement efforts, sophisticated capabilities relative to peers, transparency about processes, and a collaborative working relationship.
0 Comments