Introduction
Printed Circuit Board (PCB) prototyping is a crucial step in the development of electronic devices. It allows engineers to test and refine their designs before moving into mass production. However, the process of creating a PCB Prototype can be time-consuming and costly, especially if multiple revisions (or “spins”) are required. In this article, we will explore five effective ways to reduce the number of PCB prototype spins, saving time and money in the development process.
1. Thorough Design Review
1.1 Schematic Review
The first step in reducing PCB prototype spins is conducting a thorough design review. This begins with a comprehensive review of the schematic. The schematic represents the electrical connections and components of the PCB. It is essential to ensure that the schematic is accurate and complete before moving on to the PCB layout.
During the schematic review, consider the following:
- Check for proper component selection and ratings
- Verify that all necessary components are included
- Ensure that the power distribution is adequate and properly regulated
- Review the signal integrity and consider any necessary protection circuits
- Confirm that the schematic matches the intended functionality of the device
1.2 PCB Layout Review
Once the schematic is finalized, the next step is to review the PCB layout. The PCB layout determines the physical placement of components and the routing of traces on the board. A well-designed PCB layout is crucial for proper functionality, manufacturability, and reliability.
During the PCB layout review, consider the following:
- Verify that the component placement is optimal for signal integrity and manufacturability
- Check for proper trace widths and spacing based on the current requirements and PCB fabrication capabilities
- Ensure that the power and ground planes are properly designed and connected
- Review the layer stackup and confirm that it meets the necessary electrical and mechanical requirements
- Check for any potential manufacturing issues, such as acid traps or insufficient clearances
By conducting a thorough design review, potential issues can be identified and resolved before sending the PCB design for prototyping. This can significantly reduce the number of revisions required, saving time and cost in the long run.
2. Design for Manufacturability (DFM)
2.1 Understanding PCB Fabrication Capabilities
To reduce PCB prototype spins, it is essential to design the PCB with manufacturability in mind. This involves understanding the capabilities and limitations of the PCB fabrication process. Different PCB manufacturers may have varying capabilities in terms of minimum trace widths, hole sizes, and layer counts.
When designing the PCB, consider the following DFM guidelines:
- Use standard trace widths and spacing that are compatible with the selected PCB manufacturer
- Avoid using unnecessarily small component footprints or pitch sizes
- Ensure that the minimum hole sizes and annular rings are within the manufacturer’s capabilities
- Consider the maximum number of layers supported by the manufacturer and design accordingly
2.2 Adhering to Design Rules
In addition to understanding the PCB fabrication capabilities, it is crucial to adhere to the design rules specified by the manufacturer. These design rules outline the minimum requirements for various aspects of the PCB design, such as trace widths, spacing, and clearances.
Adhering to the design rules helps ensure that the PCB can be manufactured reliably and with high yield. Violating these rules can lead to manufacturing issues, requiring additional prototype spins to resolve.
Most PCB design software includes built-in design rule checks (DRCs) that can automatically verify the PCB layout against the specified design rules. Running DRCs regularly during the design process can help identify and resolve any rule violations early on.
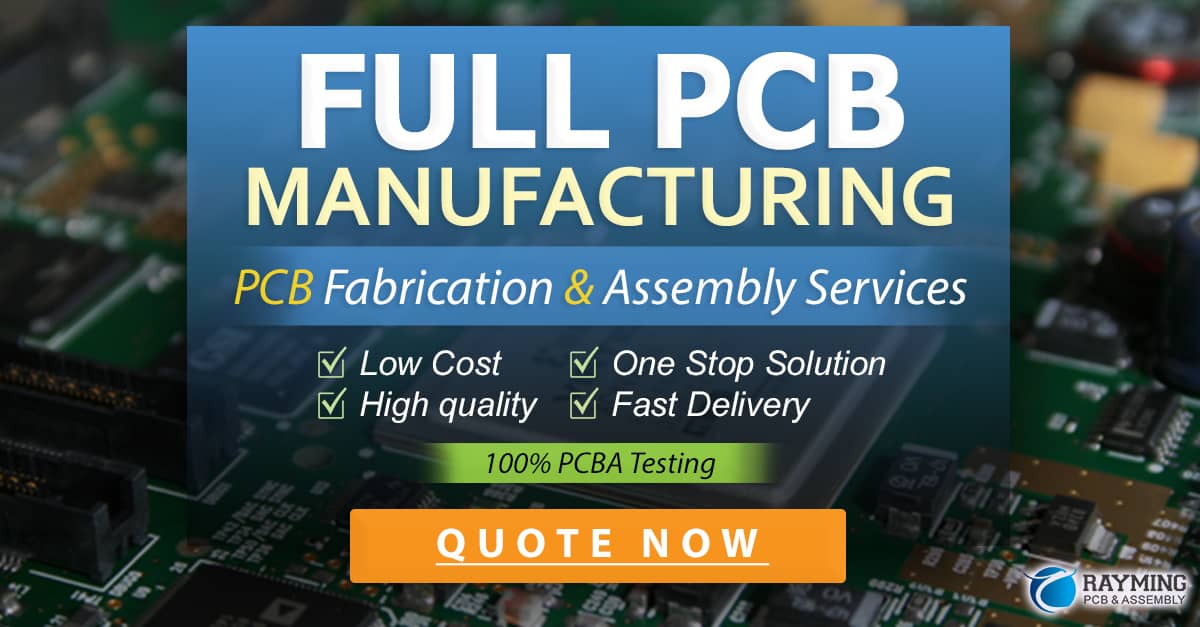
3. Component Selection and Availability
3.1 Selecting Readily Available Components
Component selection plays a significant role in reducing PCB prototype spins. One of the key considerations is the availability of the selected components. Using components that are readily available from multiple suppliers can help avoid delays due to component shortages or long lead times.
When selecting components, consider the following:
- Choose components that are actively manufactured and have a long product lifecycle
- Opt for components with multiple sourcing options to mitigate the risk of supply chain disruptions
- Consider the minimum order quantities (MOQs) and lead times for each component
- Verify that the selected components are compatible with the intended operating conditions and environment
3.2 Managing Component Libraries
To streamline the component selection process and ensure consistency across designs, it is helpful to maintain a well-organized component library. A component library is a centralized database that contains information about the components used in PCB designs, including their symbols, footprints, and parametric data.
Managing a component library involves the following:
- Standardizing component symbols and footprints to ensure compatibility and consistency
- Regularly updating the library with new components and removing obsolete ones
- Documenting component specifications, sourcing information, and any specific application notes
- Collaborating with the procurement team to ensure that the selected components are approved and available
By selecting readily available components and managing a comprehensive component library, designers can reduce the risk of component-related issues that may require additional prototype spins.
4. Simulation and Analysis
4.1 Signal Integrity Simulation
Simulating the PCB design before prototyping can help identify and resolve potential signal integrity issues. Signal integrity refers to the quality of the electrical signals transmitted through the PCB. Poor signal integrity can lead to functional problems, such as signal distortion, crosstalk, and reflections.
Signal integrity simulation involves analyzing the PCB design to ensure that the signals maintain their integrity throughout the board. This includes considering factors such as trace impedance, termination, and coupling.
Some common signal integrity simulation techniques include:
- Time-domain reflectometry (TDR) analysis to identify impedance discontinuities
- Crosstalk analysis to evaluate the coupling between adjacent traces
- Eye diagram analysis to assess the quality of high-speed digital signals
- Electromagnetic interference (EMI) analysis to identify potential sources of interference
By performing signal integrity simulations early in the design process, designers can identify and mitigate potential issues before prototyping, reducing the need for additional spins.
4.2 Thermal Analysis
Thermal analysis is another important aspect of PCB simulation. It involves evaluating the thermal performance of the PCB and ensuring that the components operate within their specified temperature ranges.
Thermal analysis typically includes the following:
- Identifying hot spots on the PCB where components may experience excessive temperatures
- Evaluating the effectiveness of the PCB’s thermal management strategies, such as heatsinks and thermal vias
- Analyzing the impact of ambient temperature and airflow on the PCB’s thermal performance
- Considering the power dissipation of components and their thermal resistance
By conducting thermal analysis simulations, designers can optimize the PCB layout and thermal management strategies to ensure reliable operation and reduce the risk of temperature-related failures that may require additional prototype spins.
5. Prototype Testing and Validation
5.1 Comprehensive Test Plan
Once the PCB prototype is fabricated, it is crucial to have a comprehensive test plan in place to validate its functionality and performance. A well-defined test plan should cover all aspects of the PCB’s intended operation, including power-up, communication interfaces, sensor inputs, and control outputs.
The test plan should include the following:
- Test cases that cover all functional requirements of the PCB
- Expected results for each test case and acceptance criteria
- Setup and configuration instructions for the test environment
- Procedures for capturing and analyzing test data
- Contingency plans for handling any issues that may arise during testing
By having a comprehensive test plan, designers can systematically validate the PCB prototype and identify any issues that need to be addressed in subsequent revisions.
5.2 Iterative Testing and Debugging
During the prototype testing phase, it is important to approach the process iteratively. This involves testing the PCB in stages, starting with basic functionality and progressively moving to more complex scenarios.
Iterative testing allows designers to identify and isolate issues more effectively. If a problem is encountered during testing, designers can use debugging techniques to pinpoint the root cause and develop a targeted solution.
Some common debugging techniques include:
- Visual inspection of the PCB for any obvious defects or assembly issues
- Using oscilloscopes or logic analyzers to capture and analyze signal waveforms
- Employing in-circuit debugging tools to access and modify firmware or software
- Performing boundary scan tests to verify the connectivity and functionality of components
By adopting an iterative testing and debugging approach, designers can systematically resolve issues and minimize the number of prototype spins required.
Conclusion
Reducing PCB prototype spins is essential for accelerating time-to-market and minimizing development costs. By following the five effective ways outlined in this article – thorough design review, design for manufacturability, component selection and availability, simulation and analysis, and prototype testing and validation – designers can significantly improve the chances of achieving a successful PCB prototype on the first or second spin.
Remember, investing time and effort in the early stages of PCB design can pay off in the long run by reducing the need for multiple revisions. By adopting best practices and leveraging the right tools and techniques, designers can streamline the PCB prototyping process and bring their products to market faster and more efficiently.
Frequently Asked Questions (FAQ)
1. What is a PCB prototype spin?
A PCB prototype spin refers to a revision or iteration of the PCB design. Each spin involves making changes to the PCB layout, schematic, or component selection based on the results of testing and validation. Multiple spins may be required to achieve a fully functional and reliable PCB prototype.
2. Why is it important to reduce PCB prototype spins?
Reducing PCB prototype spins is important because each additional spin adds time and cost to the development process. Multiple revisions can delay the product’s time-to-market and increase the overall project budget. By minimizing the number of spins, designers can accelerate the development cycle and bring their products to market faster and more cost-effectively.
3. What are some common reasons for PCB prototype spins?
Some common reasons for PCB prototype spins include:
- Design errors or oversights in the schematic or PCB layout
- Component availability issues or changes in component specifications
- Manufacturing issues, such as incorrect footprints or design rule violations
- Signal integrity or thermal management problems identified during simulation or testing
- Functional issues discovered during prototype testing and validation
4. How can simulation and analysis help reduce PCB prototype spins?
Simulation and analysis techniques, such as signal integrity simulation and thermal analysis, can help identify potential issues in the PCB design before prototyping. By analyzing the design virtually, designers can identify and resolve problems related to signal quality, electromagnetic compatibility, and thermal performance. This can help reduce the number of physical prototype spins required, saving time and cost.
5. What role does component selection play in reducing PCB prototype spins?
Component selection plays a crucial role in reducing PCB prototype spins. By choosing components that are readily available, have a long product lifecycle, and are compatible with the intended application, designers can minimize the risk of component-related issues that may require design revisions. Maintaining an up-to-date component library and collaborating with the procurement team can help ensure that the selected components are approved and available for prototyping and production.
0 Comments