History of Surface Mount Technology
The origins of SMT can be traced back to the 1960s when IBM introduced the first surface mount components for their mainframe computers. However, it wasn’t until the 1980s that SMT gained widespread adoption in the electronics industry. The introduction of smaller, more reliable components and the increasing demand for portable electronic devices drove the transition from through-hole technology (THT) to SMT.
Advantages of Surface Mount Technology
Miniaturization
One of the primary advantages of SMT is its ability to facilitate the miniaturization of electronic devices. Surface mount components are significantly smaller than their through-hole counterparts, allowing for more components to be placed on a single PCB. This increased component density enables the production of compact and lightweight electronic devices, such as smartphones, tablets, and wearables.
Improved Performance
SMT components offer improved electrical performance compared to through-hole components. The shorter lead lengths and smaller package sizes of SMT components reduce parasitic capacitance and inductance, resulting in faster signal propagation and lower signal distortion. This enhanced performance is particularly important in high-frequency applications, such as wireless communication devices and high-speed digital circuits.
Cost-Effectiveness
The adoption of SMT has led to significant cost savings in the Electronics Manufacturing industry. The automated nature of the SMT Assembly process reduces labor costs and increases production throughput. Additionally, the smaller size of SMT components allows for more efficient use of PCB real estate, reducing material costs and enabling the production of more devices per PCB panel.
Surface Mount Technology Manufacturing Process
The SMT manufacturing process involves several key steps, including Solder Paste printing, component placement, Reflow soldering, and inspection. Let’s take a closer look at each of these steps:
Solder Paste Printing
The first step in the SMT assembly process is the application of solder paste to the PCB. Solder paste is a mixture of tiny solder particles suspended in a flux medium. A stencil is used to apply the solder paste to the desired locations on the PCB, ensuring precise and consistent solder paste deposits.
Component Placement
Once the solder paste has been applied, the surface mount components are placed onto the PCB using automated pick-and-place machines. These machines use vacuum nozzles to pick up the components from feeders and place them onto the solder paste deposits with high accuracy and speed. Modern pick-and-place machines can place thousands of components per hour, significantly increasing production efficiency.
Reflow Soldering
After the components have been placed, the PCB undergoes a reflow soldering process. The PCB is passed through a reflow oven, which applies a carefully controlled temperature profile to melt the solder paste and form permanent electrical and mechanical connections between the components and the PCB. The reflow soldering process is critical to ensuring the reliability and longevity of the assembled circuit.
Inspection
The final step in the SMT manufacturing process is inspection. Automated optical inspection (AOI) systems are used to verify the correct placement and orientation of components, as well as the quality of the solder joints. In addition to AOI, other inspection methods, such as X-ray inspection and in-circuit testing, may be employed to ensure the functionality and reliability of the assembLED PCB.
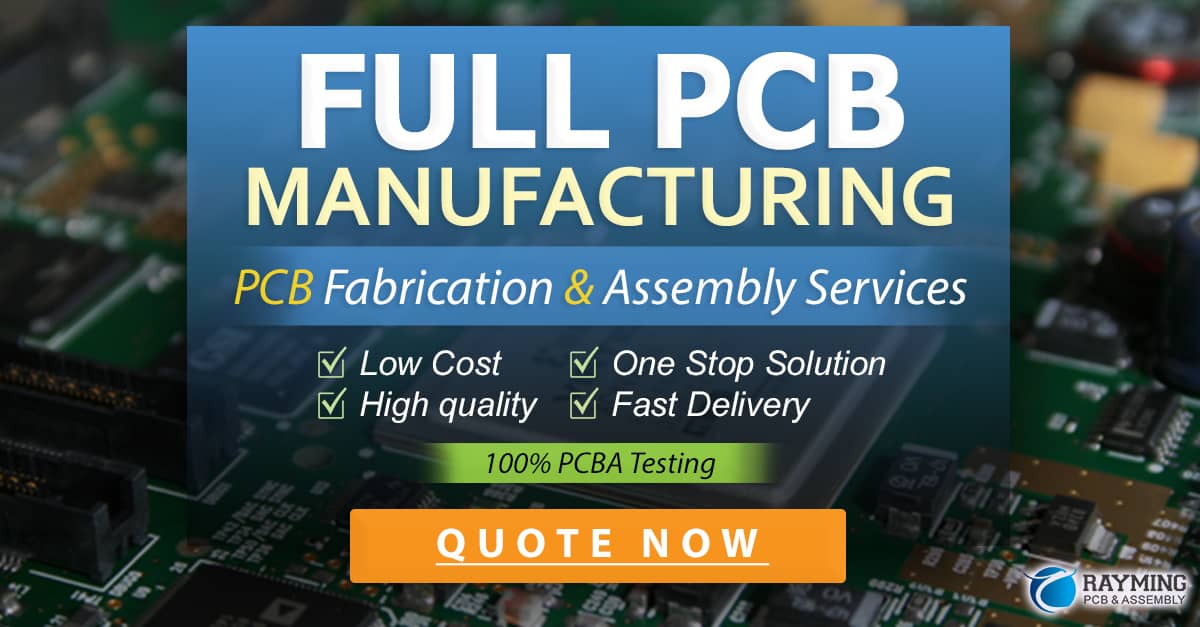
Applications of Surface Mount Technology
SMT has found widespread application across various industries, including:
Consumer Electronics
SMT is extensively used in the production of consumer electronic devices, such as smartphones, tablets, laptops, and gaming consoles. The miniaturization and performance benefits offered by SMT have enabled the development of increasingly powerful and feature-rich devices in compact form factors.
Automotive Electronics
The automotive industry has embraced SMT for the production of electronic control units (ECUs), sensors, and infotainment systems. The harsh operating environment in vehicles demands the use of robust and reliable electronic components, which SMT can provide.
Medical Devices
SMT is employed in the manufacturing of medical devices, such as implantable pacemakers, hearing aids, and portable monitoring equipment. The small size and high reliability of SMT components make them ideal for use in these life-critical applications.
Industrial Automation
Industrial automation systems, such as programmable logic controllers (PLCs), sensors, and actuators, rely on SMT for their production. The increased component density and improved performance offered by SMT enable the development of compact and reliable industrial control systems.
Frequently Asked Questions (FAQ)
1. What is the difference between surface mount technology (SMT) and through-hole technology (THT)?
Surface mount technology involves mounting components directly onto the surface of a PCB, while through-hole technology requires components to be inserted through holes drilled in the PCB. SMT components are smaller and allow for higher component density, while THT components are larger and offer better mechanical stability.
2. Can SMT and THT components be used on the same PCB?
Yes, it is possible to use both SMT and THT components on the same PCB. This is known as a mixed-technology assembly and is often used when certain components, such as connectors or large power devices, are only available in through-hole packages.
3. What are the challenges associated with SMT assembly?
Some of the challenges associated with SMT assembly include the handling of small components, ensuring proper solder paste deposition, and managing thermal profiles during reflow soldering. Proper process control and the use of specialized equipment are essential for overcoming these challenges.
4. How does the size of SMT components compare to THT components?
SMT components are typically much smaller than their THT counterparts. For example, a surface mount resistor may measure just 1.0 mm × 0.5 mm (0402 package), while a through-hole resistor may measure 3.5 mm × 1.8 mm or larger.
5. What is the future outlook for surface mount technology?
The future of SMT looks promising, as the demand for smaller, lighter, and more powerful electronic devices continues to grow. Advancements in materials science, packaging technologies, and manufacturing processes are expected to drive further miniaturization and performance improvements in SMT-based electronics.
Characteristic | Surface Mount Technology (SMT) | Through-Hole Technology (THT) |
---|---|---|
Component Size | Smaller | Larger |
Component Density | Higher | Lower |
Assembly Process | Automated | Semi-automated or manual |
Solder Joint Reliability | Good | Excellent |
Mechanical Stability | Good | Excellent |
Rework and Repair | More challenging | Easier |
In conclusion, surface mount technology has revolutionized the electronics manufacturing industry by enabling the production of smaller, lighter, and more powerful electronic devices. The advantages of SMT, including miniaturization, improved performance, and cost-effectiveness, have made it the preferred choice for a wide range of applications, from consumer electronics to industrial automation. As technology continues to advance, SMT is poised to play a crucial role in shaping the future of the electronics industry.
0 Comments