What is an LED PCB?
An LED PCB, or Light Emitting Diode Printed Circuit Board, is a specialized type of circuit board designed to power and control LEDs. LEDs are highly efficient, long-lasting, and versatile light sources that are widely used in various applications, from simple indicator lights to complex lighting systems. By integrating LEDs onto a PCB, designers can create compact, reliable, and cost-effective lighting solutions.
LED PCBs come in various shapes, sizes, and configurations, depending on the specific requirements of the application. They can be single-sided, double-sided, or multi-layered, and can feature different types of LEDs, such as SMD (Surface Mount Device) or through-hole LEDs.
Key Components of an LED PCB
An LED PCB typically consists of the following components:
- Substrate: The base material of the PCB, usually made of FR-4 (Flame Retardant 4), a glass-reinforced epoxy laminate.
- Copper Traces: Conductive paths that carry electrical signals and power to the LEDs and other components on the board.
- Solder Mask: A protective layer that covers the copper traces, preventing short circuits and oxidation.
- Silkscreen: A printed layer that provides text, logos, and other identifying marks on the PCB.
- LEDs: The light-emitting components that are soldered onto the PCB.
- Resistors: Components that limit the current flowing through the LEDs, protecting them from damage.
- Connectors: Optional components that allow the LED PCB to be connected to other devices or power sources.
Advantages of Using LED PCBs
There are several reasons why LED PCBs are preferred over other lighting solutions:
Energy Efficiency
LEDs are highly energy-efficient compared to traditional light sources like incandescent bulbs or fluorescent lamps. They convert a higher percentage of electrical energy into light, resulting in lower power consumption and reduced operating costs.
Long Lifespan
LEDs have a significantly longer lifespan than other light sources. With proper thermal management and current control, LEDs can last for tens of thousands of hours, minimizing maintenance and replacement costs.
Compact Size
LED PCBs allow for the creation of compact and lightweight lighting systems. This is particularly advantageous in applications where space is limited, such as in portable devices, automotive lighting, or small electronic displays.
Design Flexibility
LED PCBs offer a high degree of design flexibility. They can be customized to fit specific shapes, sizes, and layouts, enabling designers to create unique and innovative lighting solutions. Additionally, LEDs are available in a wide range of colors and can be easily controlled to produce dynamic lighting effects.
Reliability
LED PCBs are solid-state devices with no moving parts, making them highly resistant to vibration, shock, and other mechanical stresses. This inherent reliability makes LED PCBs suitable for use in demanding environments, such as industrial, automotive, and aerospace applications.
Applications of LED PCBs
LED PCBs find applications in a wide range of industries and products, including:
- Automotive Lighting: LED PCBs are used in headlights, taillights, interior lighting, and instrument panel illumination.
- General Illumination: LED PCBs are used in residential, commercial, and industrial lighting fixtures, such as bulbs, tubes, and panels.
- Backlighting: LED PCBs are used to backlight LCD displays in smartphones, tablets, laptops, and televisions.
- Signage and Displays: LED PCBs are used in digital signage, billboards, and other large-scale displays.
- Medical Devices: LED PCBs are used in medical equipment, such as surgical lighting, endoscopes, and dental curing lights.
- Horticulture: LED PCBs are used in grow lights for indoor farming and greenhouse applications.
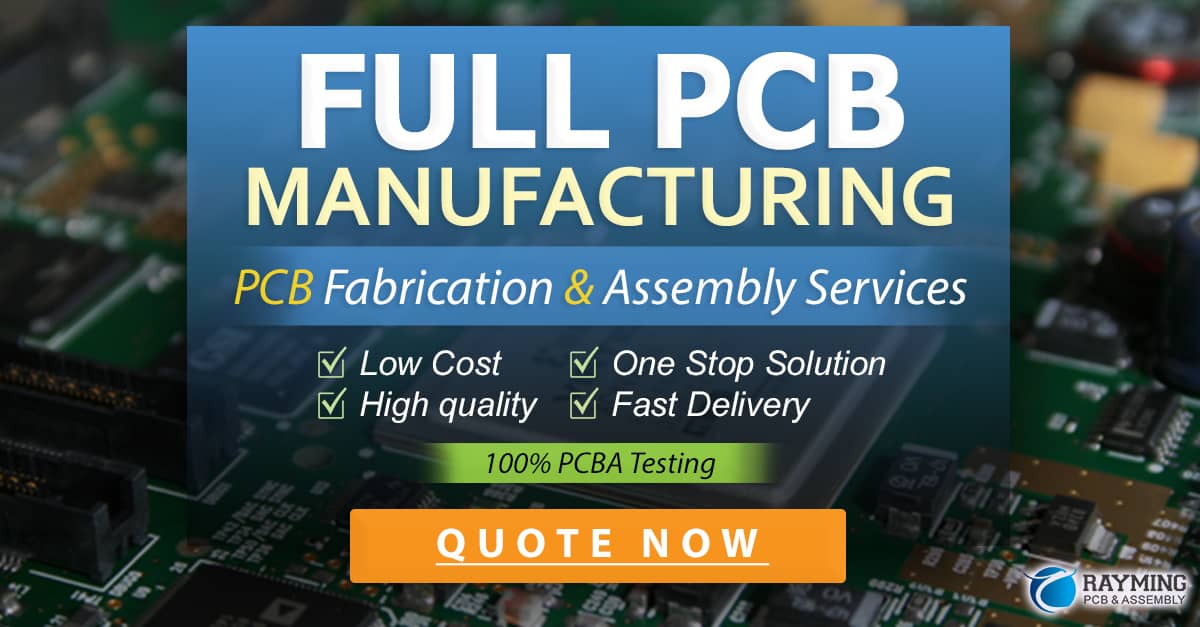
Design Considerations for LED PCBs
When designing an LED PCB, several factors must be considered to ensure optimal performance, reliability, and longevity:
Thermal Management
LEDs generate heat during operation, which can negatively impact their performance and lifespan if not properly managed. LED PCBs must be designed with adequate thermal management features, such as heatsinks, thermal vias, or metal core substrates, to dissipate heat effectively.
Current Control
LEDs are current-driven devices, meaning that their brightness is directly proportional to the current flowing through them. To ensure consistent brightness and prevent damage, LED PCBs must include current-limiting resistors or constant current drivers.
Optical Design
The optical design of an LED PCB plays a crucial role in determining the light output, distribution, and quality. Factors such as LED placement, lens design, and reflector geometry must be carefully considered to achieve the desired illumination characteristics.
PCB Layout
The layout of an LED PCB can significantly impact its performance and reliability. Designers must ensure proper trace widths, spacing, and routing to minimize voltage drops, electromagnetic interference, and signal integrity issues. Additionally, the placement of components should be optimized for manufacturability and ease of assembly.
Standards and Regulations
LED PCBs must comply with various industry standards and regulations, such as UL, CE, and RoHS, depending on the application and target market. Designers must be aware of these requirements and ensure that their designs meet the necessary criteria for safety, reliability, and environmental compliance.
Manufacturing Process of LED PCBs
The manufacturing process of LED PCBs involves several steps:
- PCB Fabrication: The PCB substrate is fabricated using standard PCB manufacturing techniques, such as etching, drilling, and plating.
- Solder Mask and Silkscreen Application: The solder mask and silkscreen layers are applied to the PCB to protect the copper traces and provide identifying marks.
- LED Placement: The LEDs are placed on the PCB using automated pick-and-place machines or manual placement methods.
- Soldering: The LEDs and other components are soldered onto the PCB using reflow soldering or wave soldering techniques.
- Testing and Inspection: The assembled LED PCB undergoes various tests and inspections to ensure proper functionality, brightness, and color consistency.
Frequently Asked Questions (FAQ)
-
What is the difference between an LED PCB and a regular PCB?
An LED PCB is specifically designed to power and control LEDs, while a regular PCB can be used for various electronic applications. LED PCBs typically include features such as thermal management, current control, and optical design considerations that are specific to LED lighting. -
Can I use any type of LED with an LED PCB?
No, the type of LED used must be compatible with the specific design of the LED PCB. Factors such as the LED package size, forward voltage, and current rating must match the PCB’s design specifications to ensure proper operation and prevent damage. -
How long do LED PCBs typically last?
The lifespan of an LED PCB depends on several factors, such as the quality of the LEDs, the effectiveness of the thermal management, and the operating conditions. With proper design and usage, LED PCBs can last for tens of thousands of hours, often surpassing the lifespan of traditional lighting solutions. -
Are LED PCBs more expensive than other lighting solutions?
While the initial cost of LED PCBs may be higher than some traditional lighting solutions, they offer long-term cost savings due to their energy efficiency, long lifespan, and low maintenance requirements. Over the lifetime of the product, LED PCBs often provide a lower total cost of ownership. -
Can I design and manufacture my own LED PCB?
Yes, it is possible to design and manufacture your own LED PCB, but it requires specialized knowledge and tools. Designing an LED PCB involves considerations such as thermal management, current control, optical design, and PCB layout. Manufacturing requires access to PCB fabrication and assembly equipment. For most applications, it is recommended to work with experienced LED PCB design and manufacturing partners to ensure optimal results.
Conclusion
LED PCBs have revolutionized the lighting industry, offering a wide range of benefits over traditional light sources. Their energy efficiency, long lifespan, compact size, design flexibility, and reliability make them an attractive choice for a variety of applications, from automotive lighting to general illumination and beyond.
Designing and manufacturing LED PCBs requires careful consideration of factors such as thermal management, current control, optical design, and PCB layout. By adhering to best practices and industry standards, designers can create LED PCBs that deliver optimal performance, reliability, and longevity.
As the demand for energy-efficient and sustainable lighting solutions continues to grow, LED PCBs will undoubtedly play an increasingly important role in shaping the future of lighting technology.
0 Comments