Composition of Solder Paste
Solder paste is made up of two main ingredients:
- Solder alloy powder
- Flux medium
Solder Alloy Powder
The solder alloy powder makes up 80-90% of the paste by weight. It consists of tiny spherical particles of solder, typically a tin-lead (SnPb) alloy or lead-free alloy such as tin-silver-copper (SAC).
Common solder alloys used in paste include:
Alloy | Composition | Melting Point | Characteristics |
---|---|---|---|
Sn63/Pb37 | 63% Tin, 37% Lead | 183°C | Eutectic, good wetting, low cost |
SAC305 | 96.5% Tin, 3% Silver, 0.5% Copper | 217-220°C | Lead-free, good strength & reliability |
Sn42/Bi58 | 42% Tin, 58% Bismuth | 138°C | Low-temperature, very brittle |
The size of the solder particles, known as the mesh size, determines the printing and reflow characteristics of the paste. Mesh sizes range from Type 1 (160-75μm) to Type 7 (<11μm), with smaller sizes used for printing finer features.
Flux Medium
The flux medium makes up 10-20% of the paste. It consists of rosins, activators, solvents, and thickeners. The flux has several important functions:
- Suspends the solder powder in a homogeneous paste
- Protects the powder from oxidation
- Helps the solder wet to the surfaces during reflow
- Removes oxides from the powder and pad/lead surfaces
Flux comes in different activity levels depending on the aggressiveness of the activators:
Flux Type | Activity | Residue | Cleaning |
---|---|---|---|
R | Low | Non-corrosive | Optional |
RMA | Moderate | Mildly activated | Optional |
RA | High | Corrosive | Required |
No-clean | Low | Non-corrosive | Not needed |
No-clean fluxes are most commonly used today to eliminate post-reflow cleaning steps. The flux medium volatilizes during reflow, leaving minimal inert residue.
Solder Paste Properties
Key properties of solder paste that affect its printability, reflow behavior, and reliability include:
Viscosity
Viscosity is a measure of the paste’s resistance to flow. It determines how easily the paste can be dispensed and how well it retains its printed shape. Paste viscosity decreases with increasing temperature and shear rate (faster printing). Viscosity is typically measured using a rotational viscometer and specified in centipoise (cP).
Thixotropy
Thixotropy refers to the paste’s ability to thin out when shear force is applied (during printing) and thicken again when at rest. High thixotropy helps the paste retain its printed shape without slumping. It is measured by comparing the viscosity at different shear rates.
Tackiness
Tackiness refers to the paste’s ability to hold components in place after placement. It prevents components from being displaced during handling or reflow. Tackiness is determined by flux ingredients like rosins. It can be measured using a tackiness tester.
Solder Balls
Solder balling is a defect where small spheres of solder are left behind after reflow, causing shorts. Solder ball resistance depends on the powder size distribution and flux chemistry. It is tested by printing and reflowing paste on a glass slide, then counting solder balls under magnification. IPC standards specify acceptable solder ball levels.
Shelf Life
Solder paste has a limited shelf life, typically 6-12 months when refrigerated (1-10°C). Its viscosity and printability gradually degrade over time due to flux separation, powder oxidation, and evaporation of solvents. Expired paste can cause printing and wetting defects.
Solder Paste Handling
Proper handling of solder paste is essential to ensure consistent print quality and prevent defects. Key aspects of paste handling include:
Storage
Paste should be stored in a refrigerator at 1-10°C to maximize shelf life. It must be allowed to warm to room temperature for several hours before use to prevent condensation. Opened jars should be sealed with tape to prevent drying and used within a few days.
Mixing
Paste ingredients tend to separate over time, with flux rising to the top and heavy powder settling at the bottom. The paste must be thoroughly mixed before use to restore its homogeneous consistency. This is done by hand-stirring with a spatula or using an automatic paste mixer. Over-mixing can introduce air bubbles.
Stencil Loading
Paste is applied to the stencil using a metal squeegee blade. A rolling motion is used to scoop paste from the jar and spread an even layer on the stencil surface. Insufficient paste loading can result in incomplete prints, while excessive loading wastes paste and increases the risk of bridging.
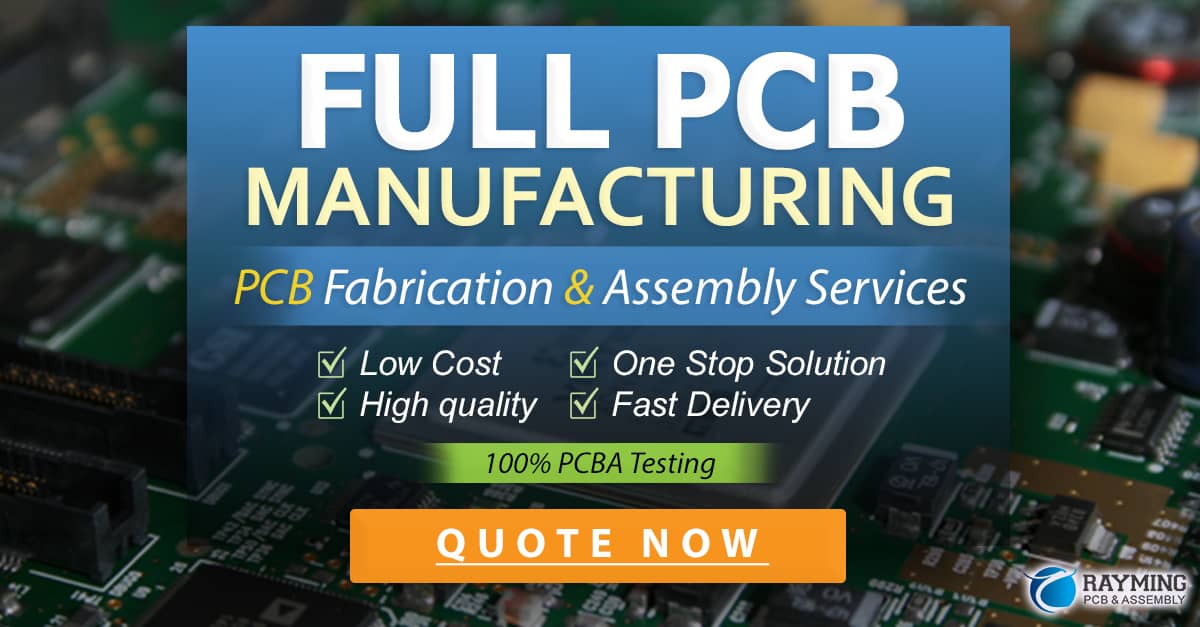
Solder Paste Printing
The solder paste printing process transfers the paste onto the pads of the PCB through a patterned stencil. Factors that affect print quality and consistency include:
Stencil Design
The stencil aperture sizes and shapes must be optimized for the paste mesh size and PCB layout. Apertures that are too small or have high aspect ratios can cause insufficient paste transfer, while oversized apertures cause bridging and shorts. Stencil thickness is typically 4-8 mils, with step-downs used for fine-pitch components.
Printer Setup
Key printer settings that affect paste deposition include squeegee pressure, print speed, and snap-off distance. Higher pressure and slower speed increase paste transfer but can cause smearing. Snap-off is the gap between the stencil and PCB, typically 0.01-0.04″. Higher snap-off reduces smearing but can cause inconsistent prints.
Environment
Printing should be done in a temperature and humidity-controlled environment to ensure consistent paste rheology. Optimal conditions are 20-25°C and 35-55% RH. Higher temperatures reduce viscosity and cause slumping, while excessive humidity can cause spattering and solder balling.
Inspection
Printed paste deposits should be 100% inspected using 2D or 3D automated optical inspection (AOI/SPI) systems. These measure the volume, area, and height of each deposit to detect defects like insufficients, bridging, and poor alignment. Feedback from inspection can be used to optimize the printing process.
Solder Paste Reflow
After components are placed on the printed paste deposits, the assembly undergoes a controlled heating process called reflow to melt the solder and form permanent interconnects. The reflow profile must be optimized for the solder alloy, components, and PCB characteristics.
Reflow Profile
A typical reflow profile consists of four stages:
-
Preheat: Gradual heating to 150-170°C to volatilize solvents and activate the flux. Heating rate is 0.5-1.5°C/sec.
-
Thermal soak: Temperature held at 150-170°C for 60-120 sec to equalize component and PCB temperatures.
-
Reflow: Rapid heating (2-3°C/sec) to 20-40°C above the solder melting point for 30-90 sec. Peak temperature and time above liquidus (TAL) must be controlled to prevent component damage and intermetallic growth.
-
Cooling: Forced air cooling at 3-6°C/sec to solidify the solder joints. Slow cooling can cause grain coarsening and embrittlement.
Defects
Common solder paste-related defects that can occur during reflow include:
- Solder Beading: Paste de-wets from the pads and forms spheres due to poor wetting or contamination.
- Voiding: Flux volatiles become trapped in the molten solder, leaving voids that reduce joint strength.
- Head-in-pillow: The component lead rests on the solder surface without collapsing, often due to oxidation or poor wetting.
- Tombstoning: Smaller chip components tilt up on one end due to uneven wetting forces.
Proper paste selection, printing, and profiling are essential to minimizing these defects.
Frequently Asked Questions
What is the shelf life of solder paste?
Most solder pastes have a shelf life of 6-12 months when stored at 1-10°C. The paste should be used within a few days of opening to prevent drying and oxidation. Expired paste can cause printing and reflow defects.
How do you test solder paste quality?
Key parameters for evaluating solder paste quality include:
– Viscosity: Measured using a rotational viscometer to ensure consistent printability.
– Tack force: Measured using a tackiness tester to ensure components hold their placement.
– Solder balling: Tested by printing and reflowing paste on glass slides and counting balls.
– Wetting: Assessed by measuring the spread of reflowed paste on copper coupons.
Regular testing of incoming paste batches can prevent printing and reflow issues.
What is no-clean solder paste?
No-clean solder paste uses a low-residue flux that does not require cleaning after reflow. The flux residues are non-corrosive and can be left on the assembly. No-clean paste eliminates cleaning steps and reduces environmental impact but can interfere with test probes and conformal coating adhesion in some cases.
How do you optimize a solder paste stencil?
Stencil aperture sizes should be based on the pad sizes and paste mesh type. The area ratio (aperture opening divided by wall area) should be at least 0.66 to ensure good paste release. Common aperture reductions are 5-10% smaller than the pad size, with the exact amount depending on the paste.
Stencil thickness should be 4-8 mils for standard SMT, with thinner foils or step-downs used for fine-pitch components to maintain acceptable area ratios. Laser-cut stencils provide the best print definition and release characteristics compared to chemically-etched stencils.
What causes solder beading?
Solder beading occurs when the molten solder de-wets from the pads and component leads and forms spherical balls. The main causes are:
- Contamination or oxidation of the surfaces, preventing wetting
- Insufficient flux activity to remove oxides
- Excessive temperature or time above liquidus, causing flux exhaustion
- Incompatible solder alloy and surface finishes
Solder balls can cause opens or shorts and are a serious reliability concern. Proper paste selection, storage, and reflow profiling are essential to minimizing solder balling defects.
0 Comments