What is an SMT Machine?
An SMT machine, also known as a pick-and-place machine or a chip shooter, is an automated system designed to place surface mount components onto PCBs with high precision and speed. These machines use advanced vision systems, high-speed placement heads, and sophisticated software to accurately place components on the PCB surface.
Types of SMT Machines
There are several types of SMT machines available in the market, each designed to cater to specific manufacturing requirements:
-
High-Speed Placement Machines: These machines are designed for high-volume production and can place components at speeds of up to 100,000 components per hour (CPH).
-
Multi-Function Placement Machines: These machines offer a combination of high-speed placement and flexibility, allowing for the placement of a wide range of component sizes and types.
-
Flexible Placement Machines: These machines are designed for low to medium-volume production and offer the ability to handle a variety of PCB sizes and component types.
-
Dispensing Machines: These machines are used for applying solder paste, adhesives, or other materials onto the PCB surface prior to component placement.
Key Components of an SMT Machine
An SMT machine consists of several key components that work together to ensure accurate and efficient component placement:
-
Placement Heads: The placement heads are responsible for picking up components from the feeder and placing them onto the PCB surface. Modern SMT machines often feature multiple placement heads to increase throughput.
-
Vision Systems: Vision systems are used to inspect and align components before placement, ensuring accurate positioning on the PCB.
-
Feeders: Feeders store and supply components to the placement heads. There are various types of feeders, such as tape feeders, tube feeders, and tray feeders, each designed to handle specific component packaging.
-
Conveyor System: The conveyor system moves the PCBs through the machine, allowing for continuous production.
-
Software: SMT machines are controlled by sophisticated software that manages the placement process, including component data, placement sequences, and machine settings.
The SMT Assembly Process
The SMT assembly process involves several steps, each critical to ensuring the quality and reliability of the final product:
1. Solder Paste Application
The first step in the SMT assembly process is the application of solder paste onto the PCB surface. Solder paste is a mixture of tiny solder particles suspended in a flux medium. The paste is applied using a stencil or screen printing process, ensuring that the correct amount of paste is deposited on each pad.
2. Component Placement
Once the solder paste has been applied, the PCB is loaded into the SMT machine. The machine’s vision system inspects the PCB and the components to ensure proper alignment. The placement heads then pick up the components from the feeders and place them onto the PCB surface with high precision.
3. Reflow Soldering
After all the components have been placed, the PCB undergoes a reflow soldering process. The PCB is passed through a reflow oven, which heats the solder paste to its melting point, allowing it to form a strong bond between the components and the PCB Pads. The reflow profile, which defines the temperature and duration of the heating process, is carefully controlled to ensure optimal soldering results.
4. Inspection and Testing
Once the reflow soldering process is complete, the PCB undergoes a series of inspections and tests to ensure the quality and functionality of the assembled board. Automated optical inspection (AOI) systems are often used to detect any placement or soldering defects. In some cases, X-ray inspection may be used to inspect solder joints hidden under components. Functional testing is also performed to verify that the assembled board operates as intended.
Advantages of SMT Assembly
SMT assembly offers several advantages over traditional through-hole assembly:
-
Miniaturization: SMT components are generally smaller than through-hole components, allowing for more compact and lightweight electronic devices.
-
Higher Component Density: SMT allows for higher component density on PCBs, enabling more complex and sophisticated electronic designs.
-
Faster Assembly: SMT machines can place components at much higher speeds compared to manual through-hole assembly, significantly reducing production time.
-
Cost-Effectiveness: The high-speed and automated nature of SMT assembly results in lower labor costs and increased production efficiency.
-
Improved Reliability: SMT components have shorter lead lengths and are more securely bonded to the PCB surface, resulting in improved reliability and reduced susceptibility to vibration and mechanical stress.
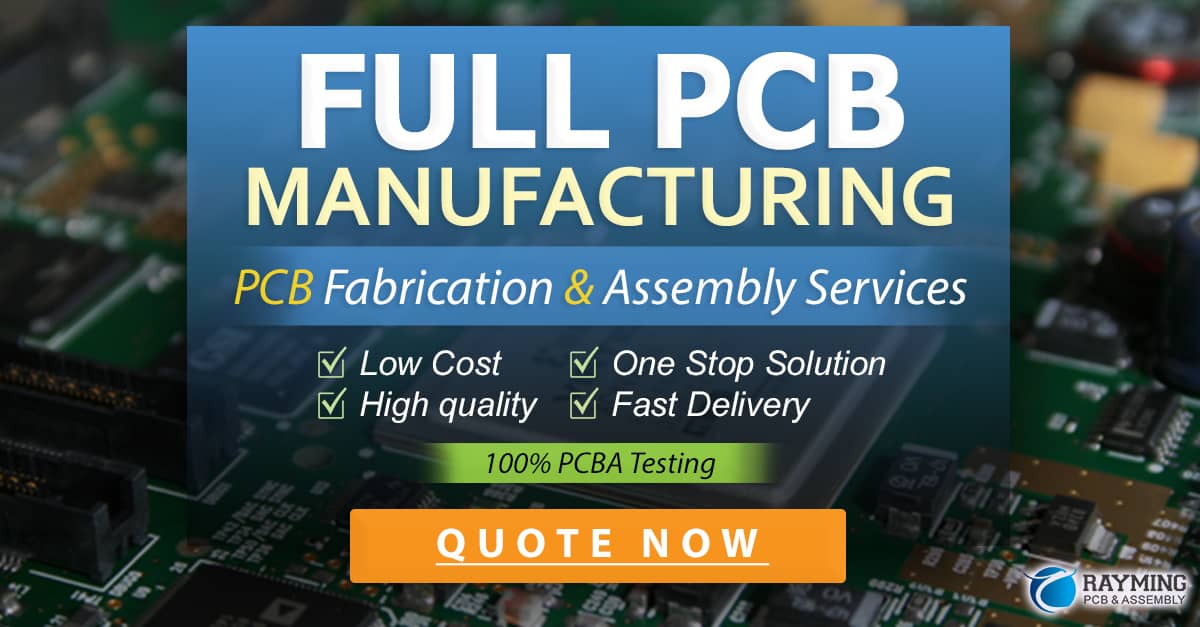
Choosing the Right SMT Machine
When selecting an SMT machine for your manufacturing needs, consider the following factors:
-
Production Volume: Choose a machine that can accommodate your current and future production volume requirements.
-
Component Diversity: Ensure that the machine can handle the various component sizes, types, and packaging used in your products.
-
Accuracy and Speed: Consider the machine’s placement accuracy and speed to ensure it meets your production goals.
-
Flexibility: If your product mix is diverse, opt for a machine that offers flexibility in handling different PCB sizes and component types.
-
Software and Integration: Evaluate the machine’s software capabilities and its ability to integrate with your existing manufacturing systems.
Future Trends in SMT Assembly
As the electronics industry continues to evolve, SMT assembly technology is also advancing to keep pace with new challenges and requirements:
-
Miniaturization: The demand for smaller, more compact electronic devices is driving the development of even smaller SMT components and more precise placement technologies.
-
Flexible and Modular Machines: Manufacturers are increasingly looking for SMT machines that offer flexibility and modularity to adapt to changing production needs.
-
Intelligent and Connected Machines: The integration of artificial intelligence (AI) and Internet of Things (IoT) technologies into SMT machines is enabling predictive maintenance, real-time process monitoring, and remote troubleshooting.
-
Sustainable Manufacturing: There is a growing emphasis on environmentally friendly SMT assembly processes, including the use of lead-free solder pastes and energy-efficient machines.
Frequently Asked Questions (FAQ)
-
What is the difference between SMT and through-hole assembly?
SMT components are mounted directly onto the surface of the PCB, while through-hole components have leads that are inserted into holes drilled in the PCB and soldered on the opposite side. SMT allows for smaller components, higher component density, and faster assembly compared to through-hole. -
How accurate are SMT machines?
Modern SMT machines can achieve placement accuracies of ±0.025 mm or better, depending on the machine’s specifications and the size of the components being placed. -
What is the typical speed of an SMT machine?
The speed of an SMT machine varies depending on the type of machine and the complexity of the assembly process. High-speed placement machines can place up to 100,000 components per hour (CPH), while more flexible machines may have lower placement speeds. -
How does the vision system in an SMT machine work?
The vision system in an SMT machine uses cameras and image processing algorithms to inspect and align the PCB and components before placement. The system captures images of the PCB and components, compares them to pre-defined templates, and makes necessary adjustments to ensure accurate placement. -
What is the role of solder paste in the SMT assembly process?
Solder paste serves as both an adhesive and a conductive medium in the SMT assembly process. It holds the components in place on the PCB surface prior to reflow soldering and forms a strong mechanical and electrical bond between the components and the PCB pads during the reflow process.
Conclusion
SMT machines have transformed the electronics manufacturing landscape, enabling the production of smaller, more complex, and more reliable electronic devices. By understanding the components, processes, and advantages of SMT assembly, manufacturers can make informed decisions when selecting and implementing SMT technology in their production lines. As the electronics industry continues to advance, SMT machines will remain at the forefront, driving innovation and shaping the future of electronics manufacturing.
Aspect | SMT Assembly | Through-Hole Assembly |
---|---|---|
Component Size | Smaller | Larger |
Component Density | Higher | Lower |
Assembly Speed | Faster | Slower |
Placement Accuracy | High (±0.025 mm) | Lower |
Solder Joint Reliability | Higher | Lower |
Design Flexibility | More flexible | Less flexible |
Cost-Effectiveness | Higher | Lower |
Table 1: Comparison of SMT Assembly and Through-Hole Assembly
By embracing the capabilities of SMT machines and staying abreast of emerging trends, manufacturers can position themselves for success in the rapidly evolving world of electronics manufacturing.
0 Comments