An In-Depth Look at This Innovative Manufacturing Technology
SMT PTH (Surface Mount Technology Plated Through Hole) is an exciting new development in the world of PCB (printed circuit board) manufacturing that combines the benefits of both surface mount and through-hole technologies. As electronics continue getting smaller and more complex, innovations like SMT PTH allow manufacturers to create more compact and efficient circuit boards to power the devices we use every day.
In this comprehensive guide, we’ll explore what exactly SMT PTH is, why it offers advantages over older methods, how the process works, and the future outlook for this technology. Let’s dive in!
What is SMT PTH?
SMT PTH is a hybrid technology that allows through-hole components to be placed on the same side of a PCB as surface mount components. Traditional SMT (surface mount technology) involves mounting components directly onto the surface of the board, while with through-hole parts, leads are inserted into holes drilled all the way through the PCB.
With SMT PTH, plated through holes are created on PCBs fabricated for surface mount assembly. Components with leads, like resistors, capacitors, connectors, etc. can then be automatically placed directly onto the surface right over the plated through holes using standard SMT equipment. This eliminates the need for two-sided assembly while still allowing the use of leaded components.
Here’s a quick comparison of the three technologies:
Technology | Description |
---|---|
SMT | Components mounted directly to surface of PCB |
Through-hole | Leads inserted into holes drilled completely through PCB |
SMT PTH | Through-hole components surface mounted over plated through holes |
As you can see, SMT PTH combines elements of both traditional SMT and through-hole assembly for a best-of-both-worlds approach.
Why Use SMT PTH?
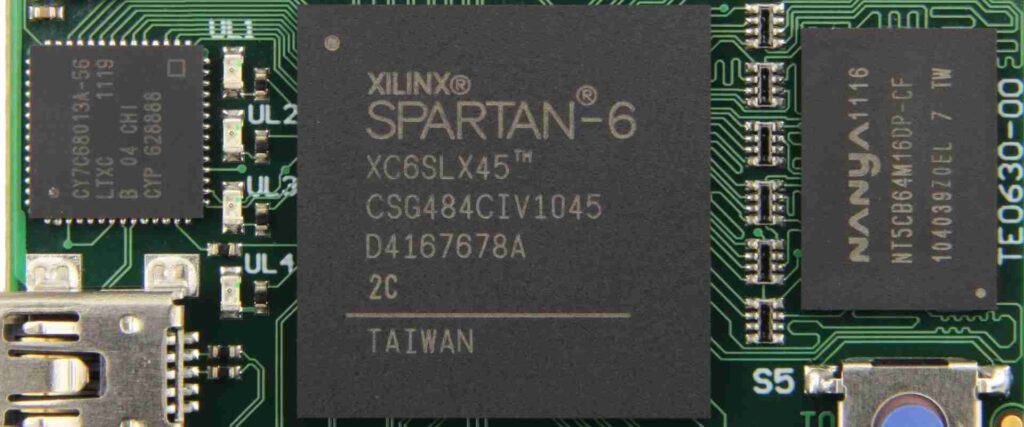
SMT PTH provides several important benefits that make it advantageous over older manufacturing methods:
Higher Component Density
Since through-hole parts can be surface mounted without needing to drill holes all the way through, components can be placed closer together on both sides of the board. This allows for greater component density.
Simplified Assembly
With SMT PTH, only one side of the board needs to be assembled. The pick-and-place machine can add all components, which streamlines assembly. There’s no need for separate SMT and through-hole assembly lines.
Improved Reliability
With traditional plated through holes, issues could arise from misalignment between layers or poor hole wall integrity. SMT PTH eliminates these pain points entirely.
Enables Miniaturization
The higher component density possible with SMT PTH allows for overall reduction in PCB size, enabling more compact end products.
Efficient Automated Production
SMT PTH allows all components to be placed by high-speed automated pick-and-place assembly equipment in a single pass. This leads to faster and more cost-effective assembly.
For these reasons, SMT PTH can be a better solution than solely SMT or through-hole assembly for many electronics manufacturing applications. The PCB industry is increasingly adopting it to reap the benefits.
How Does SMT PTH Work?
The SMT PTH process involves a few key steps:
The PCB manufacturer creates a board designed specifically for surface mount assembly. Through-holes plated with copper are added wherever leaded components will be placed.
2. Stencil Application
A metal stencil is created with cutouts matching the through hole locations on the PCB. Solder paste is applied through the stencil openings onto the PCB pads.
3. Component Placement
The pick-and-place machine uses vacuum suction to sequentially pick components and accurately place them over their matching through holes on the PCB surface.
4. Reflow Soldering
The populated board passes through a reflow oven. The solder paste melts, forming both the surface mount joints and the through-hole leads.
5. Cleaning
Any post-reflow flux residue is cleaned from the board using an appropriate cleaning agent.
And that’s it! The SMT PTH board is now fully assembled in a single process. The components are securely attached both electrically and mechanically.
Here’s a simple diagram of what an SMT PTH board looks like:
With just a few straightforward steps, SMT PTH provides all the advantages of SMT assembly with the ability to integrate through-hole component leaded parts.
The Future of SMT PTH
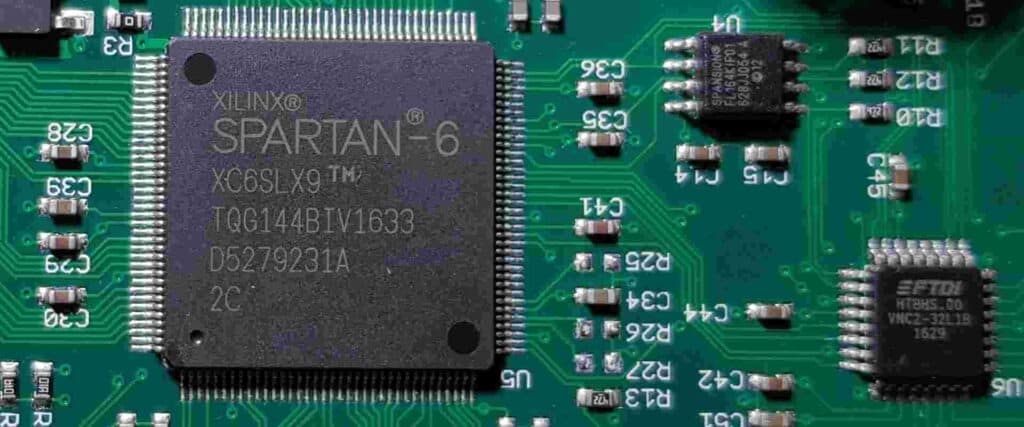
This innovative hybrid technology is rapidly gaining popularity and becoming more widely adopted across electronics manufacturing. Here are some key trends for the future of SMT PTH:
- Increasing Use in Consumer Electronics – Products like smartphones, tablets, IoT devices, and more will benefit from the miniaturization SMT PTH enables.
- Allowing Improved Medical Device Performance – Higher density, reliability, and quality requirements make medical devices ideal applications for SMT PTH.
- Enabling the Growth of Wearables – Smaller wearable tech like smart watches and fitness trackers will leverage SMT PTH to continue getting smaller and more capable.
- Driving Autonomous Vehicle Electronics – The mission-critical electronics powering autonomous cars can benefit greatly from the advantages of SMT PTH manufacturing.
- Continued PCB Fabrication Improvements – As SMT PTH gains popularity, PCB manufacturers will continue innovating fabrication processes tailored specifically for these hybrid boards.
- Allowing Further Miniaturization Across Industries – With demand for smaller electronics only increasing, SMT PTH satisfies desires for compactness across consumer and industrial electronics.
In summary, SMT PTH is poised to grow significantly in adoption and will play an integral role in enabling cutting-edge miniaturized electronic devices and components moving forward.
Frequently Asked Questions About SMT PTH
Q: What types of components work with SMT PTH?
A: Most standard through-hole component types like resistors, capacitors, transistors, connectors, crystals, LEDs, etc. are all candidates for SMT PTH implementation.
Q: Does implementing SMT PTH require new equipment?
A: The standard SMT assembly line equipment used for pick-and-place and reflow soldering can support SMT PTH without modification. Only a PCB fabricated specifically for this process is needed.
Q: How are tall components accommodated?
A: Taller components may require cavity PCB designs where a cavity or pocket is created in the board allowing the component body to sit below flush with the surface.
Q: What are the limitations of SMT PTH?
A: There are some limitations in terms of component height and weight. Additionally, vibrations can cause failure if not designed appropriately. Proper component selection helps overcome these limits.
Q: Is SMT PTH suitable for high-volume production?
A: Yes, SMT PTH is well-suited for volume manufacturing. It allows very efficient assembly using standard automated equipment. The process also is highly repeatable and reliable.
Hopefully this overview gives you a comprehensive understanding of the SMT PTH technology and its powerful benefits. SMT PTH represents an exciting innovation that will drive PCB assembly advances and enable electronics miniaturization for years to come. If you have any other questions, feel free to ask!
0 Comments