As a hardware startup, designing and building your first prototype PCB (printed circuit board) is a major milestone. However, assembling prototype boards can be complex and time-consuming without the right expertise and resources. This is where utilizing professional prototype PCB assembly services can accelerate your product development cycle.
In this comprehensive guide, we’ll cover everything you need to know about prototype PCB assembly, including:
- Benefits of Using Prototype Assembly Services
- Prototype vs Production PCB Assembly
- Finding the Right PCB Assembly Partner
- Prototype PCB Assembly Process Step-by-Step
- Key Factors that Influence Prototype PCB Assembly Cost
- Prototype Assembly Quality Considerations
- Documentation Needed for Prototype Assembly
- Testing and Validation of Assembled Prototypes
- Troubleshooting Common Prototype Assembly Issues
- Prototype Assembly FAQs
Let’s get started!
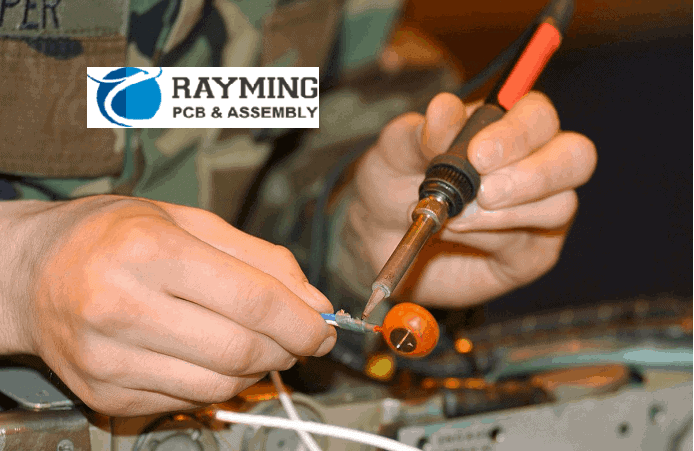
Benefits of Using Prototype PCB Assembly Services
Here are some of the key benefits of leveraging an experienced PCB assembly partner for building your prototype boards:
Faster Time-to-Market – By outsourcing prototype assembly, you avoid having to set up your own SMT assembly line and dealing with long lead times for acquiring equipment. You can get prototypes built and delivered in days/weeks rather than months.
Advanced Manufacturing Capabilities – Contract assemblers invest heavily in advanced SMT assembly equipment and skilled technicians to support the latest components, board sizes, densities, etc. Difficult assemblies beyond your capabilities can be easily handled.
Cost Savings – No need for capital expenditure and hiring additional staff. Economies of scale with aggregated orders across customers keeps assembly costs lower.
Quality & Reliability – Experienced assemblers have rigorous quality control standards and processes which minimize errors and ensure consistently high-quality builds.
Flexibility & Scalability – Prototyping volumes can be flexed up or down to suit iteration needs. Seamless transition to production assembly with the same partner.
Technical Expertise– Assemblers can provide design-for-manufacturing (DFM) guidance, component recommendations, troubleshooting assistance, and other technical support.
Prototype vs Production PCB Assembly
While the assembly process itself remains largely the same, there are some important ways in which prototype assembly differs from full-scale production:
Volumes – Prototype builds are low-volume, often just 10-100 boards. Production volumes are typically 1000s of boards.
PCB Design – Prototype boards may be designed more for validation than optimized for assembly. Production boards are highly assembly-optimized.
Components – Wider variety of components are used in prototypes whereas production maximizes standardization. Prototypes may use more expensive components not suited for cost-sensitive production.
Assembly Process – Some process steps like solder paste inspection, automated optical inspection, x-ray, etc. may be skipped for prototypes.
Testing – Production boards undergo rigorous in-circuit and functional testing. Prototype testing is generally more limited.
Quality – First-pass assembly yield and reliability requirements are lower for prototypes. Production quality needs to be extremely high.
Lead Times – Prototypes can be assembled very quickly, often within days. Production lead times are longer due to material planning and capacity scheduling.
Pricing – Per unit pricing is higher for low-volume prototyping. Mass production benefits from economies of scale.
Finding The Right Prototype PCB Assembly Partner
With so many options to choose from, here are the key factors to consider when selecting a PCB assembly partner for prototypes:
- Technical capabilities – Evaluate their assembly equipment, component libraries, expertise with complex assemblies, quality certifications, etc.
- Prototype experience – Ask about percentage of revenues from prototyping services and client case studies.
- Scalability – Ensure they have the capabilities to seamlessly scale up to production volumes.
- Quality – Review their quality assurance processes, defect rates, repair/rework capabilities, etc.
- NPI services – Offerings like DFM analysis, BOM review, test development, supply chain management, etc. add value.
- Turnaround times – They should be able to deliver quality prototypes in your required timeframe.
- Cost – Get assembly quotes from multiple assemblers and compare pricing. Understand cost drivers.
- Communication – Responsiveness to quotes & questions, clarity of documentation, project updates etc.
- Location – Consider whether a domestic or overseas assembler is a better fit. Evaluate logistics costs/time.
- Customer support – Post-delivery support for troubleshooting, test data, component sourcing, etc.
Finding a PCB assembly partner that scores well across these parameters will ensure a successful prototyping engagement. Check customer testimonials and get referrals within your network.
Prototype PCB Assembly Process Step-By-Step
The assembly of PCB prototypes involves a typical sequence of manufacturing stages:
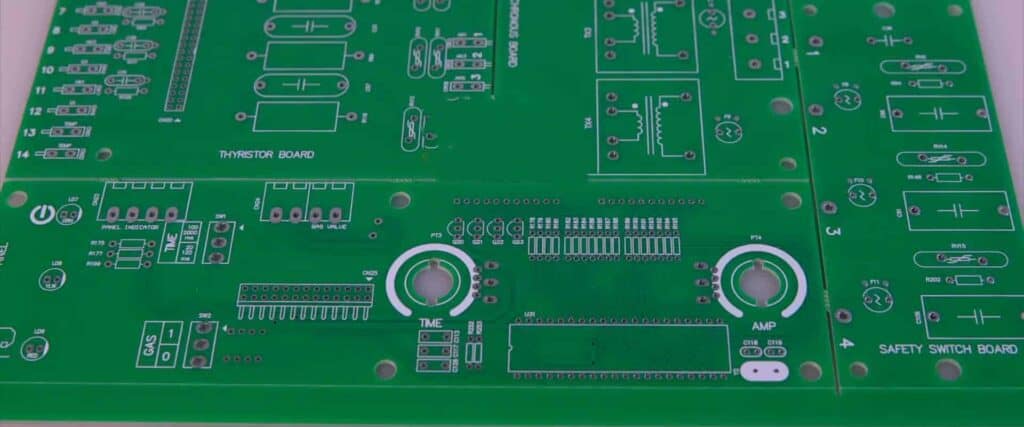
1. Design For Manufacturing (DFM)
- The Gerber, BOM, and assembly drawings are reviewed by the assembler to spot any red flags or design improvements early on. Recommendations are provided to optimize assembly yield.
2. Sourcing Components
- Components are sourced based on the BOM provided. Digikey, Mouser, Arrow etc. are commonly used distributors. Any long lead time components are highlighted.
3. Solder Paste Stencil
- A thin stainless steel stencil with cutouts matching the PCB land patterns is laser cut. Solder paste will be applied through this.
4. Solder Paste Printing
- The stencil is aligned and solder paste is applied on to the PCB through the cutouts. This “prints” solder paste deposit sites.
5. Component Placement
- Using pick-and-place machines, surface mount components are precisely placed on to the solder paste deposits.
6. Reflow Soldering
- The PCB moves through a convection reflow oven to heat up. The solder paste melts, creating solder joints that attach components.
7. Inspection
- For prototypes, often just a visual inspection is done. For critical assemblies, automated optical inspection may be used.
8. Conformal Coating
- A protective plastic coating may be selectively applied to safeguard against environmental damage.
9. Programming
- Any firmware or test software is loaded on to microcontrollers present on the board.
10. Functional Testing
- Basic tests are done to validate assembly integrity and that the board works as expected.
11. Packaging & Shipment
- The assembled prototypes are packaged and shipped to the customer by their requested courier.
This comprehensive assembly process ensures that the assembled prototypes are ready for installation, integration, and full testing by the product development team.
Key Factors that Influence Prototype PCB Assembly Costs
The costs of assembling PCB prototypes depends on a variety of factors:
1. Board Size
Larger PCB sizes occupy more area on assembly panels and require larger stencils. This pushes up cost.
2. Component Types and Counts
More components, especially tiny passives and BGAs, increase placement time and skill required. High cost adds up across many components.
3. BOM Sourcing Challenges
Hard-to-source components not available with trusted distributors require costlier custom sourcing.
4. PCB Complexity
Dense boards with 100s of components, small pitch ICs, and high layer counts make assembly costlier.
5. Through-hole Components
These must be manually inserted and soldered, increasing labor content versus only SMT components.
6. Compliance Requirements
Assemblies requiring full traceability, certified operators, cleanrooms etc. are costlier.
7. Low Volume
Setting up assembly line, stencils, sourcing etc. for prototyping volumes <100 boards has high fixed costs.
8. Special Processing
Add-ons like wash, adhesive curing, selective conformal coating, programming etc. increase costs.
9. Expedited Delivery
Super quick turnaround times can multiply costs due to out of cycle scheduling, extra shifts etc.
10. Location
Assemblers in low-labor-cost countries offer lower pricing, but have higher logistics costs.
Prototype PCB Assembly Quality Considerations
While prototypes have functional and design validation as their primary goal, it is still important to give due consideration to assembly quality:
- Work with assemblers that follow IPC standards for their processes – IPC J-STD-001, IPC-A-610, IPC 7711/7721 etc.
- Request advanced inspection techniques like x-ray and automated optical inspection for high reliability prototypes.
- Perform first-article inspections on initial prototypes from a batch for workmanship defects.
- Implement process controls for paste printing, component storage, reflow profiling etc.
- Mandate ESD control procedures for handling sensitive components.
- Insist on certifications like ISO9001, ISO13485 etc. and regular employee training.
- Capture full traceability data during assembly including operator details, component batches etc.
- Define quality metrics like defect rates, repairs, yields etc. and monitor trends.
- Get assembler support for troubleshooting any issues with delivered prototypes.
While striving for great quality is good, avoid prematurely over-specifying production-grade requirements during prototyping which can impact costs and lead times.
Documentation Needed for Prototype PCB Assembly
To enable a smooth assembly process, ensure you provide your PCB assembler with all the necessary details:
- Gerber Files – The PCB fabrication data files containing copper layers, solder masks, silkscreen, drill data etc.
- Bill of Materials (BOM) – Complete list of components, their reference designators, manufacturers part numbers, quantities, and other attributes.
- Assembly Drawings – Mechanical drawings depicting component placement locations and orientations.
- Component Data – Datasheets for any components that are not industry standard.
- Sourcing Preferences – Approved vendors, or vendors to avoid, for procuring components.
- Any Special Instructions – Notes on which side of board to assemble, solder mask requirements, wash process etc.
- Test Procedures – Details on any testing or inspection needed post-assembly.
- Firmware Files – Hex/binary files to be programmed on any microcontrollers.
- Delivery Address – Where assembled prototypes need to be shipped to.
Providing this comprehensive information upfront prevents delays and errors in prototyping your PCB designs.
Testing and Validation of Assembled Prototypes
Once the assembled PCB prototypes are received from the assembly supplier, they need to be fully validated before they can be considered ready for their intended use. Some of the testing activities at this stage:
- Visual Inspection – Check board for any missing, damaged or misaligned components. Verify part numbers, polarities etc.
- In-Circuit Testing – Use a bed-of-nails tester to validate electrical connectivity between components and identify any shorts or opens.
- Functional Testing – Exercise critical circuits on the board through predefined stimuli to verify intended functionality.
- Firmware Validation – Run test suites on any microcontrollers on board to validate programmed firmware/software.
- Stress Testing – Perform burn-in type dynamic testing under thermal, vibration or power cycling to validate robustness.
- Compliance Testing – Execute any certifications tests like EMC/EMI, safety etc. that are relevant.
- Bench Characterization – Measure performance parameters like gain, noise, output power, latency, efficiency etc.
- System Integration – Combine with other system modules like enclosure, cables, sensors, software apps etc. and evaluate overall functionality.
While prototyping, testing requirements may be streamlined to keep costs low. But for pre-production prototypes, comprehensive testing is highly recommended before design sign-off.
Troubleshooting Common Prototype Assembly Issues
Despite best efforts, sometimes assembled prototypes may not work as expected. Some common issues and remedies include:
Short Circuits – Could arise from solder bridges, metal debris or overheating damage. Isolate and rework.
Open Circuits – Dry solder joints, lifted pads, broken traces could be the issue. Resolder/repair track.
Wrong Components – Inspect and replace incorrect parts populated per BOM/schematics.
Misaligned Components – Gently reheat and reposition shifted parts.
ESD Damage – Use ESD protection protocols while handling static sensitive boards.
Firmware Errors – Reflash firmware or check for hardware/software incompatibility issues.
Soldering Defects – Insufficient heat or issues like tombstoning. Adjust reflow profile.
Contamination – Remove foreign object debris and clean flux residues.
Power Problems – Check for incorrect power sequencing, voltages, reversed polarity etc.
An experienced assembler will provide troubleshooting support to help quickly resolve prototype issues. Learning from the problems will also lead to design improvements.
Prototype PCB Assembly FAQs
Here are some frequently asked questions about prototyping services:
Q: What are typical lead times for assembling prototypes?
A: Most assembly providers can deliver fully assembled prototypes in about 5-7 working days once they have all the required inputs. Some even offer 48-72 hour rush builds.
Q: Can I source some critical components myself?
A: Yes, you can supply components yourself. This helps reduce lead times. Ensure you send components at least 2-3 days in advance.
Q: How many prototype boards can be built together?
A: Batch sizes of 5-10 boards are typical for initial prototypes. Iterative prototypes may use batches of 20-50 boards. Hundreds of prototypes can be built together for validation builds.
Q: Should I expect any NRE charges for prototypes?
A: Most assemblers waive NRE charges for prototyping. Stencils, programming files etc. can be reused if designs are relatively unchanged across iterations.
Q: Can prototypes leverage the same test fixtures used later for production?
A: Using production test hardware early on helps validate the design. Adapters may be needed to interface prototypes to these fixtures.
Q: Are prototypes hand assembled or use automated assembly?
A: Even for proto assembly, pick & place machines are predominantly used along with solder reflow. Operators may hand-assemble through-hole components.
Conclusion
Prototyping complex electronics products requires significant expertise and infrastructure to assemble the boards correctly. By partnering with an experienced prototype PCB assembly provider, hardware startups and design houses can accelerate product development schedules and focus on design validation rather than assembly logistics. The guide above summarizes the key considerations to keep in mind.
With rigorous quality processes, advanced assembly capabilities, quick turnarounds and experienced technical support, a good assembly partner becomes an invaluable extension of your engineering team. They assemble your prototypes fast, so you can go to market sooner with confidence in your hardware.
0 Comments