Introduction to PCB Manufacturing
Printed Circuit Board (PCB) manufacturing is a complex process that involves multiple steps and techniques to create high-quality electronic circuits. PCBs are essential components in almost all modern electronic devices, from smartphones and computers to medical equipment and aerospace systems. As technology advances and devices become more sophisticated, the demand for better PCB manufacturing processes increases.
In this article, we will explore the various aspects of PCB manufacturing and discuss how to improve the quality and efficiency of the process. We will cover topics such as PCB design, material selection, fabrication techniques, assembly methods, testing, and quality control. By the end of this article, you will have a comprehensive understanding of PCB manufacturing and be equipped with the knowledge to make better PCBs.
The Importance of PCB Design
Understanding the Basics of PCB Design
PCB design is the first and most critical step in the manufacturing process. A well-designed PCB ensures that the electronic components are placed correctly, the connections are properly routed, and the board functions as intended. Poor PCB design can lead to manufacturing issues, reduced performance, and even device failure.
When designing a PCB, several factors must be considered, including:
- Component placement
- Signal integrity
- Power distribution
- Thermal management
- Manufacturability
Best Practices for PCB Design
To create a high-quality PCB design, follow these best practices:
- Use a reliable PCB design software tool
- Follow the manufacturer’s design guidelines
- Keep the design simple and modular
- Use appropriate component packages and footprints
- Optimize signal routing and layer stackup
- Incorporate design for manufacturability (DFM) principles
- Conduct thorough design reviews and simulations
Material Selection for PCB Manufacturing
Types of PCB Materials
The choice of materials used in PCB manufacturing can significantly impact the board’s performance, reliability, and cost. The most common types of PCB materials include:
- FR-4: A glass-reinforced epoxy laminate, widely used for general-purpose PCBs
- High-Tg FR-4: An enhanced version of FR-4 with better thermal stability and performance
- Polyimide: A high-temperature, flexible material used for applications requiring bendability
- Rogers: A high-frequency laminate material used for RF and microwave applications
- Aluminum: A metal-core PCB material used for high-power and heat-dissipation applications
Factors to Consider When Selecting PCB Materials
When selecting PCB materials, consider the following factors:
- Electrical properties (dielectric constant, loss tangent, etc.)
- Thermal properties (glass transition temperature, thermal conductivity, etc.)
- Mechanical properties (strength, flexibility, etc.)
- Environmental resistance (moisture, chemicals, etc.)
- Cost and availability
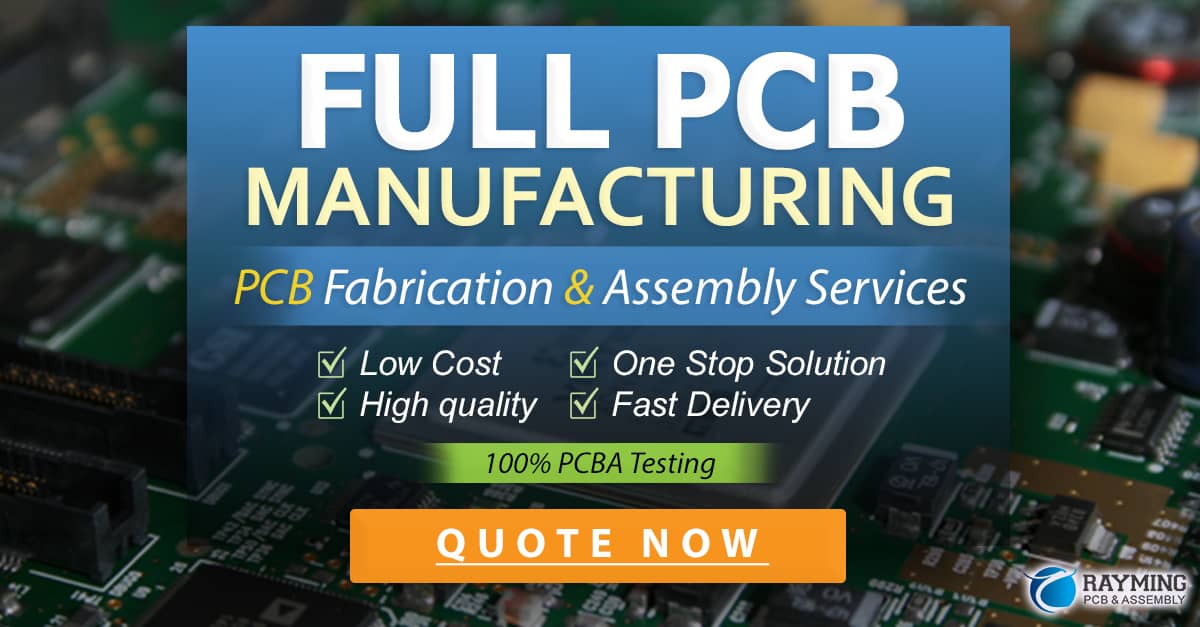
PCB Fabrication Techniques
Overview of PCB Fabrication Process
The PCB fabrication process involves several steps, including:
- Printing the circuit pattern on the copper-clad laminate
- Etching away the unwanted copper to form the circuit traces
- Drilling holes for component mounting and vias
- Applying solder mask and silkscreen for protection and labeling
- Surface finishing the exposed copper for improved solderability and protection
Advanced Fabrication Techniques
As PCBs become more complex and densely populated, advanced fabrication techniques are being developed to improve the manufacturing process. Some of these techniques include:
- High-Density Interconnect (HDI): A method of creating finer pitch and smaller via sizes for increased component density
- Embedded Components: Integrating passive components (resistors, capacitors) within the PCB substrate to save space and improve performance
- Microvias: Using laser drilling to create small, precise vias for high-density interconnects
- Additive Manufacturing: Using 3D printing techniques to create PCBs with unique geometries and materials
PCB Assembly Methods
Through-Hole vs. Surface Mount Assembly
PCB assembly involves attaching electronic components to the board. There are two primary assembly methods:
- Through-Hole Assembly (THA): Components with long leads are inserted through holes in the PCB and soldered on the opposite side
- Surface Mount Assembly (SMT): Components with small leads or pads are placed directly on the PCB surface and soldered using a reflow process
SMT has become the dominant assembly method due to its advantages in terms of component density, manufacturing speed, and cost.
Automated Assembly Processes
To improve the efficiency and accuracy of PCB assembly, automated processes are widely used, including:
- Pick-and-Place Machines: Robotic systems that precisely place components on the PCB
- Reflow Soldering: Applying solder paste and heating the board to melt the solder and attach components
- Wave Soldering: Passing the board over a molten solder wave to solder through-hole components
- Automated Optical Inspection (AOI): Using computer vision to detect assembly defects and ensure quality
PCB Testing and Quality Control
Types of PCB Testing
To ensure the quality and reliability of manufactured PCBs, various testing methods are employed, such as:
- In-Circuit Testing (ICT): Using a bed-of-nails fixture to test individual components and connections
- Flying Probe Testing: Using movable probes to test specific points on the PCB
- Functional Testing: Verifying the board’s overall functionality under real-world conditions
- Boundary Scan Testing: Using built-in test circuitry (JTAG) to test complex digital components
- Burn-In Testing: Subjecting the PCB to elevated temperatures and voltages to identify early failures
Implementing Quality Control Measures
To maintain high quality standards in PCB manufacturing, implement the following quality control measures:
- Establish and follow a comprehensive quality management system (QMS)
- Conduct regular process audits and inspections
- Use statistical process control (SPC) to monitor and optimize manufacturing processes
- Implement traceability and root cause analysis for defect prevention
- Foster a culture of continuous improvement and employee training
Frequently Asked Questions (FAQ)
1. What is the difference between a single-layer and multi-layer PCB?
A single-layer PCB has conductive traces on only one side of the substrate, while a multi-layer PCB has traces on both sides and/or internal layers. Multi-layer PCBs offer higher component density, better signal integrity, and improved EMI performance, but are more complex and expensive to manufacture.
2. What is the purpose of solder mask on a PCB?
Solder mask is a protective coating applied to the copper traces on a PCB. It serves several purposes:
- Preventing solder bridges and short circuits during assembly
- Protecting the copper from oxidation and environmental damage
- Providing electrical insulation between adjacent traces
- Improving the board’s aesthetic appearance
3. What are vias, and why are they used in PCBs?
Vias are small holes drilled through a PCB to connect traces on different layers. They are used to:
- Route signals between layers in multi-layer PCBs
- Provide electrical and thermal connections to ground or power planes
- Facilitate component mounting and assembly
There are several types of vias, including through-hole, blind, buried, and microvias, each with specific applications and manufacturing requirements.
4. How can I reduce the cost of PCB manufacturing?
To reduce the cost of PCB manufacturing, consider the following strategies:
- Optimize the board size and layout to minimize material waste
- Use standard component packages and sizes to avoid custom tooling
- Minimize the number of layers and drilling operations
- Choose cost-effective materials and surface finishes
- Order in larger quantities to benefit from economies of scale
- Work with a reputable PCB manufacturer to leverage their expertise and buying power
5. What are some common PCB manufacturing defects, and how can they be prevented?
Common PCB manufacturing defects include:
- Shorts and opens: Caused by incorrect etching, drilling, or assembly; prevented by proper design and process control
- Solder bridges: Caused by excess solder or improper reflow; prevented by using solder mask and optimizing the soldering process
- Component misalignment: Caused by incorrect placement or shifting during reflow; prevented by using vision systems and proper component securement
- Delamination: Caused by moisture, heat, or mechanical stress; prevented by using appropriate materials and handling procedures
- Contamination: Caused by dirt, dust, or chemical residues; prevented by maintaining a clean manufacturing environment and following proper cleaning procedures
To prevent these defects, implement a robust quality control system, conduct regular process audits, and work closely with your PCB manufacturer to identify and address potential issues.
Conclusion
PCB manufacturing is a complex and constantly evolving field that requires a deep understanding of design principles, materials, fabrication techniques, assembly methods, and quality control measures. By following the best practices and strategies outlined in this article, you can improve the quality, reliability, and cost-effectiveness of your PCB manufacturing process.
Remember to prioritize PCB design, select appropriate materials, leverage advanced fabrication techniques, optimize assembly processes, and implement rigorous testing and quality control measures. Continuously monitor and improve your manufacturing process to stay competitive in the ever-changing world of electronics.
By mastering the art and science of PCB manufacturing, you can create better, more innovative electronic products that meet the demands of today’s fast-paced, technology-driven world.
0 Comments