Introduction to PCB Fabrication
Printed Circuit Board (PCB) fabrication is a complex process that involves multiple steps and requires specialized knowledge and equipment. This article will provide an in-depth look at the PCB fabrication set-up process, including the materials, tools, and techniques used to create high-quality PCBs.
What is a PCB?
A PCB is a flat board made of insulating materials, such as fiberglass or plastic, with conductive tracks, pads, and other features etched onto its surface. These boards are used to mechanically support and electrically connect electronic components using conductive pathways, tracks, or signal traces.
Importance of PCB Fabrication
PCB fabrication is crucial for the production of electronic devices, as it allows for the miniaturization and integration of complex circuits. Without PCBs, electronic devices would be much larger, less reliable, and more expensive to produce.
PCB Fabrication Materials
Substrate Materials
The most common substrate materials used in PCB fabrication are:
- FR-4: A fiberglass-reinforced epoxy laminate, widely used due to its excellent mechanical and electrical properties.
- Polyimide: A high-performance material with superior thermal stability and chemical resistance, used in applications with demanding requirements.
- Aluminum: Used for its excellent thermal conductivity in applications that require heat dissipation.
Copper Foils
Copper foils are used to create the conductive tracks on the PCB surface. The most common thicknesses are:
Thickness (oz) | Thickness (μm) |
---|---|
0.5 | 17.5 |
1 | 35 |
2 | 70 |
Solder Mask and Silkscreen
- Solder Mask: A protective layer applied over the copper traces to prevent oxidation and provide electrical insulation.
- Silkscreen: A printed layer used to add text, logos, and component identifiers to the PCB surface.
PCB Fabrication Tools and Equipment
CAD Software
Computer-Aided Design (CAD) software is used to create the PCB layout and generate the necessary files for fabrication. Some popular CAD tools include:
- Altium Designer
- KiCad
- Eagle
Fabrication Equipment
The following equipment is used in the PCB fabrication process:
- Plotter: Used to print the PCB design onto photosensitive film.
- Exposure Unit: Used to transfer the design from the film onto the copper-clad laminate.
- Etching Machine: Used to remove unwanted copper from the laminate, leaving only the desired tracks.
- Drilling Machine: Used to create holes for component placement and vias.
- Solder Mask Application Equipment: Used to apply the solder mask layer to the PCB surface.
- Silkscreen Printing Equipment: Used to apply the silkscreen layer to the PCB surface.
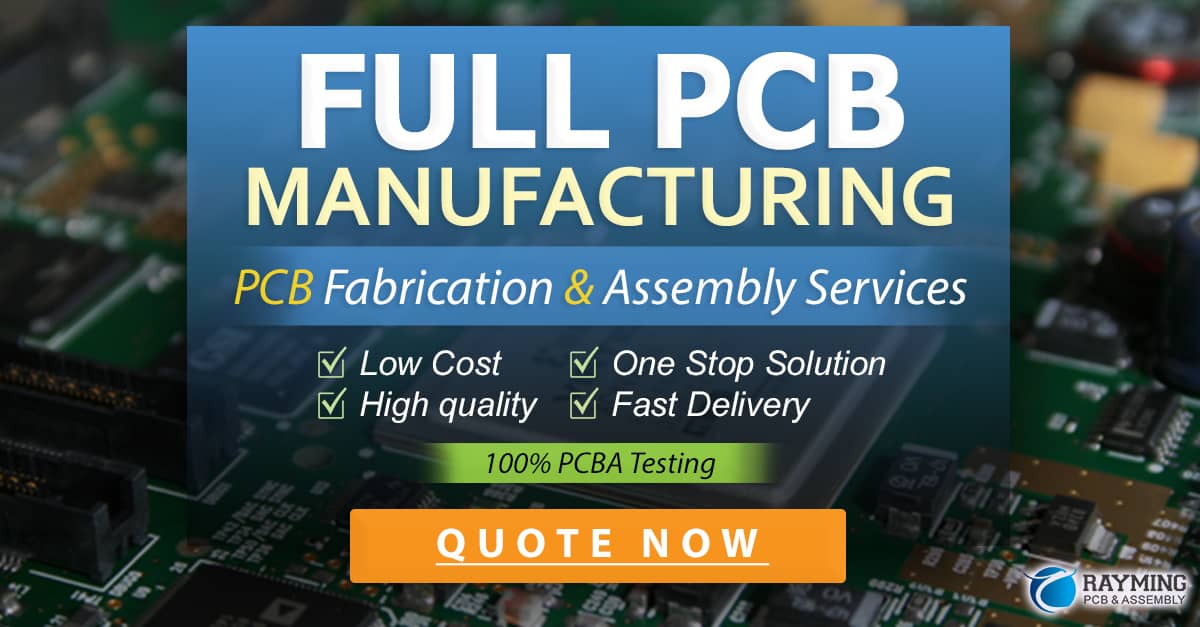
PCB Fabrication Process
Design and Layout
The first step in PCB fabrication is to create the design and layout using CAD software. This involves:
- Schematic Capture: Creating a schematic diagram of the circuit.
- Component Placement: Arranging the components on the PCB layout.
- Routing: Creating the conductive tracks that connect the components.
- Design Rule Check (DRC): Verifying that the layout meets the manufacturing constraints and design rules.
Fabrication Steps
Once the design is complete, the following steps are performed to fabricate the PCB:
- Film Plotting: The design is printed onto photosensitive film using a plotter.
- Exposure: The film is placed on top of the copper-clad laminate and exposed to UV light, transferring the design onto the laminate.
- Developing: The exposed laminate is developed, removing the unexposed photoresist.
- Etching: The developed laminate is placed in an etching machine, which removes the unwanted copper, leaving only the desired tracks.
- Drilling: Holes are drilled into the laminate for component placement and vias.
- Solder Mask Application: The solder mask layer is applied to the PCB surface to protect the copper traces and provide insulation.
- Silkscreen Printing: The silkscreen layer is printed onto the PCB surface, adding text, logos, and component identifiers.
- Surface Finish: A surface finish, such as HASL (Hot Air Solder Leveling) or ENIG (Electroless Nickel Immersion Gold), is applied to the exposed copper to prevent oxidation and improve solderability.
Quality Control
Throughout the PCB fabrication process, various quality control measures are implemented to ensure the finished product meets the required specifications. These measures include:
- Visual Inspection: The PCBs are visually inspected for defects, such as shorts, opens, or incorrect component placement.
- Electrical Testing: The PCBs undergo electrical testing to verify that they function as intended and meet the specified electrical characteristics.
- Microsectioning: A sample of the PCBs is cross-sectioned and examined under a microscope to verify the internal structure and integrity of the layers.
Advanced PCB Fabrication Techniques
High Density Interconnect (HDI)
HDI PCBs feature finer traces, smaller vias, and higher component density than traditional PCBs. This allows for the creation of more compact and complex designs. HDI PCBs are fabricated using advanced techniques, such as:
- Microvias: Laser-drilled vias with diameters less than 150μm.
- Sequential Lamination: Building up the PCB in multiple layers, with each layer being laminated and drilled separately.
- Blind and Buried Vias: Vias that start or end on an internal layer, rather than extending through the entire board thickness.
Flexible PCBs
Flexible PCBs are made using thin, flexible substrate materials, such as polyimide. They can be bent, folded, or twisted to fit into tight spaces or conform to curved surfaces. Flexible PCBs are often used in applications where space is limited or where the board needs to move or flex during operation.
Rigid-Flex PCBs
Rigid-Flex PCBs combine the benefits of both rigid and flexible PCBs. They consist of rigid sections connected by flexible sections, allowing for three-dimensional designs and improved reliability in applications with high vibration or stress.
PCB Fabrication Challenges and Solutions
Signal Integrity
As PCBs become more complex and operate at higher frequencies, maintaining signal integrity becomes increasingly challenging. Some techniques used to address signal integrity issues include:
- Impedance Control: Designing the PCB traces to have a specific characteristic impedance to minimize reflections and distortions.
- Differential Signaling: Using differential pairs to cancel out electromagnetic interference (EMI) and improve noise immunity.
- Ground Planes: Incorporating solid ground planes to provide a low-impedance return path for signals and reduce crosstalk.
Thermal Management
Proper thermal management is crucial for ensuring the reliability and longevity of electronic devices. PCB fabrication techniques used for thermal management include:
- Thermal Vias: Using vias to transfer heat from components to the opposite side of the board or to internal layers.
- Metal Core PCBs: Using a metal core substrate, such as aluminum, to improve heat dissipation.
- Heatsinks: Attaching heatsinks to components or the PCB itself to increase the surface area for heat dissipation.
Electromagnetic Compatibility (EMC)
Ensuring that electronic devices do not interfere with each other or with other equipment is essential. PCB fabrication techniques used to improve EMC include:
- Shielding: Using conductive enclosures or coatings to prevent electromagnetic interference (EMI) from entering or leaving the device.
- Grounding: Providing a low-impedance path for electromagnetic energy to return to its source, minimizing radiation and interference.
- Filtering: Using filters to suppress high-frequency noise and prevent it from propagating through the system.
Frequently Asked Questions (FAQ)
-
Q: What is the difference between a single-layer and a multi-layer PCB?
A: A single-layer PCB has conductive tracks on only one side of the substrate, while a multi-layer PCB has conductive tracks on both sides and/or internal layers. Multi-layer PCBs allow for more complex designs and higher component density. -
Q: What is the purpose of vias in a PCB?
A: Vias are conductive holes that allow signals to pass from one layer of the PCB to another. They are used to interconnect the different layers and provide a means for components on opposite sides of the board to communicate. -
Q: What is the difference between HASL and ENIG surface finishes?
A: HASL (Hot Air Solder Leveling) is a surface finish where the exposed copper is coated with a thin layer of solder, while ENIG (Electroless Nickel Immersion Gold) is a surface finish where the copper is first plated with a layer of nickel, followed by a thin layer of gold. ENIG provides better flatness and solderability compared to HASL. -
Q: What is the purpose of the solder mask layer on a PCB?
A: The solder mask layer serves two main purposes: it protects the copper traces from oxidation and provides electrical insulation between adjacent traces. This helps to prevent short circuits and improves the reliability of the PCB. -
Q: What is the typical turnaround time for PCB fabrication?
A: The turnaround time for PCB fabrication varies depending on the complexity of the design, the number of layers, and the chosen fabrication house. For simple designs, the turnaround time can be as short as 24 hours, while more complex designs may take several weeks.
Conclusion
PCB fabrication is a complex process that requires specialized knowledge and equipment. By understanding the materials, tools, and techniques used in PCB fabrication, designers can create high-quality boards that meet the requirements of modern electronic devices. As technology continues to advance, new fabrication techniques and materials will be developed to address the challenges of signal integrity, thermal management, and electromagnetic compatibility.
0 Comments