Introduction
Printed circuit boards (PCBs) are the backbone of modern electronics. From smartphones to computers to medical devices, PCBs provide the foundation on which components are mounted and connected. As electronic products become more advanced, PCB design and manufacturing has grown increasingly complex. This has led many companies to outsource PCB assembly rather than maintain these capabilities in-house.
Choosing the right printed circuit board assembly (PCBA) partner is critical to the success of your product. This guide will provide a comprehensive overview of PCBA services, factors to consider when selecting an assembly provider, key steps in the PCBA process, and strategies for ensuring quality outcomes. Gaining insight into PCBA best practices can enable your company to get products to market faster and more cost-effectively.
Overview of Printed Circuit Board Assembly Services
PCB assembly, also known as PCBA, involves soldering and assembling electronic components onto a PCB. While some companies still assemble PCBs in-house, most now work with specialized contract manufacturers that offer PCBA services. The key benefits of outsourcing PCBA include:
- Cost savings – Contract manufacturers can achieve significant economies of scale across their operations, reducing assembly costs.
- Specialization – Leading contract manufacturers invest heavily in advanced assembly technologies and employ skilled technicians. This expertise is difficult for individual companies to develop and maintain internally.
- Speed – Large-scale contract assemblers have the capacity to rapidly scale production, helping meet demand and launch products faster.
- Quality – Reputable partners adhere to rigorous quality control standards in order to deliver high yields and function.
- Flexibility – Contract manufacturers offer services globally and can adjust to changing production requirements.
In addition to assembling PCBs, contract manufacturers often provide related services:
- PCB fabrication
- Component sourcing and procurement
- Inventory and warehouse management
- Testing and inspection
- Packaging and order fulfillment
- Reverse logistics and repair
By leveraging these capabilities under one roof, customers can streamline their supply chains and product development cycles.
Key Factors in Selecting a PCBA Partner
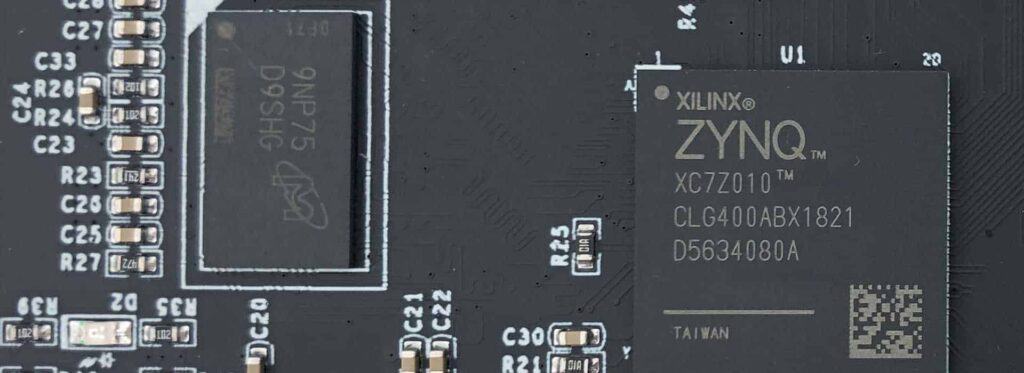
Choosing the right contract manufacturer is perhaps the most important decision in the PCBA process. Here are key factors to consider during selection:
Technical Capabilities
- What assembly technologies do they offer (through-hole, surface mount, etc.)?
- Can they work with the latest component packaging types?
- Do they have experience with your product type?
- Do they assemble flex, rigid-flex, and other PCB technologies?
Quality Processes
- Are they certified to key quality standards like ISO 9001, IATF 16949, or AS9100?
- Do they have rigorous quality inspection procedures?
- How much process documentation and traceability do they provide?
Supply Chain Management
- Can they procure necessary components and manage inventory?
- Do they have preferred supplier relationships?
- How is counterfeit component risk mitigated?
Reliability and Accessibility
- Do they consistently meet on-time delivery targets?
- How transparent are they about production timelines and issues?
- Can they scale rapidly while maintaining quality levels?
Location
- Where are production facilities located relative to your team or target markets?
- Do they have language resources aligned to your needs?
- What are their export control capabilities?
Cost Structure
- How flexible are their pricing models (fixed-price, time & materials, etc.)?
- What are their minimum order quantities and volume tiers?
- Are they willing to provide cost transparency?
Customer Service
- How responsive are their sales and engineering teams?
- Will they assign dedicated account management staff?
- Do they take a collaborative, solution-oriented approach?
You’ll want to evaluate partners on all the above criteria through a formal request-for-quote (RFQ) process. Site visits to prospective manufacturer facilities are also recommended whenever possible.
Key Questions to Ask Prospective PCBA Partners
- What technologies and processes do you use for SMT assembly? Through-hole assembly?
- How do you inspect PCB assemblies after production?
- How do you test assembled boards before shipment?
- What data and documentation will I receive on my board assemblies?
- How do you qualify and monitor your component suppliers?
- What counterfeit avoidance measures do you have in place?
- What are your capabilities for assembling and testing high-speed, high-complexity designs?
- How do you ensure the security and confidentiality of customer data?
- What systems and certifications do you have for quality management?
- How do you guarantee on-time delivery for orders?
- How will you keep me updated on order status and any production issues?
- What support do you provide for new product introduction and ramp-up?
- Do you help optimize designs for manufacturability and cost?
- What IT infrastructure enables collaboration and data exchange with customers?
- How can I regularly monitor process performance metrics?
PCBA Process Step-By-Step
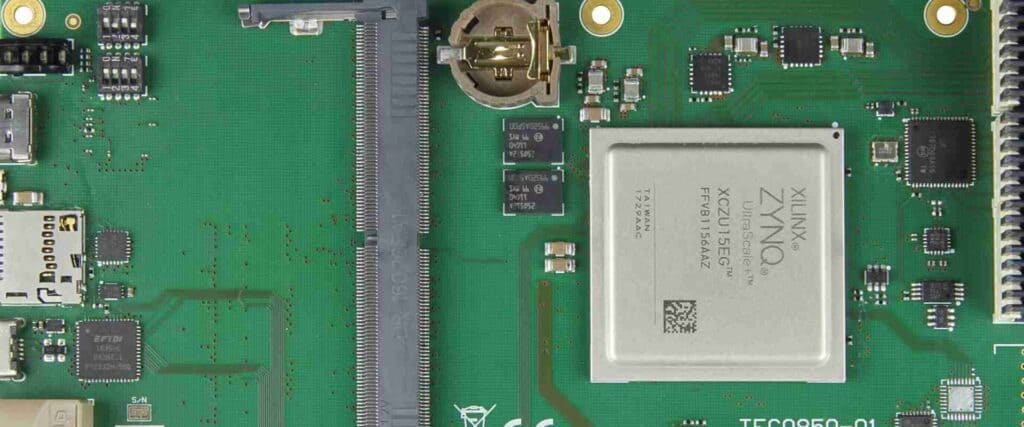
Once you have selected a contract manufacturer, efficient execution of the PCBA process is key to achieving a timely, high-quality outcome. Here are the major steps:
Sourcing Components
The contract manufacturer will source all required components for assembly based on your bill of materials (BOM). Reputable partners have established procurement pipelines to acquire authorized components efficiently. Some key considerations around sourcing include:
- Lead times – Confirm that longer-lead components are ordered in time.
- Authorized distribution – Ensure components are purchased through authorized channels, not brokers.
- Allocation risks – Watch for any constrained components that may be put on allocation by suppliers.
- Cost optimization – the assembler can help identify component substitutions that meet spec at lower cost.
Incoming Components Inspection
All incoming components need to undergo inspection:
- Verification – Confirm components match what was ordered on documentation.
- Visual inspection – Check for damage, defects, or abnormalities on each component.
- Dimensional checking – Validate component dimensions are within toleranced ranges.
- Functional testing – Validate basic functionality for certain complex ICs or modules.
This helps catch counterfeit, damaged, or out-of-spec components before they enter assembly.
Solder Paste Stencil Creation
The solder paste stencil is a thin metal sheet laser-cut with apertures matching the PCB footprint. It is laid over the PCB to apply solder paste precisely before component placement. Quality stencil fabrication and inspection helps ensure reliable solder joints post reflow.
Solder Paste Printing
Solder paste is printed through the stencil apertures onto PCB pads using an automated print machine. This deposits small bricks of solder paste where components will be placed. The stencil is cleaned and inspected between every print cycle.
SMT Pick-and-Place
SMT components are autonomously picked from feeders and precisely placed onto PCB pads using high-speed pick-and-place machines. Accuracy of a few microns is standard. Most SMT lines feature multiple placement heads for high throughput.
SMT Reflow Soldering
The PCB passes through a reflow oven to heat solder joints over liquidus temperature. This “reflows” the solder to form reliable electrical and mechanical connections. Different solder alloys, paste formulations, and profiles are used depending on component types.
Through-Hole Insertion
Some components like connectors or fasteners are inserted into plated through-holes in the PCB. This is done manually or via automated insertion equipment. Leads are bent outwards to anchor the component.
Wave Soldering
The underside of the PCB passes over a wave or fountain of molten solder. This solders through-hole component leads. Nitrogen blanketing prevents oxidation. Some boards also pass through selective wave machines that only solder specific areas.
Conformal Coating
A protective polymer coating may be selectively applied over the PCB assembly, leaving connectors exposed. This “conforms” to the board topology and prevents shorting, leakage currents or corrosion.
AOI and Testing
Every PCB assembly is put through automated optical inspection (AOI) and testing procedures:
- AOI checks for defects like missing or misaligned components, insufficient solder, board damage, and more.
- In-circuit testing (ICT) validates electrical performance and catches hard faults.
- Functional testing confirms the board executes properly and meets specifications.
Box Build Assembly
For full box-build assembly, the contract manufacturer can integrate the PCB assembly into the full product enclosure with additional components and wiring.
Final Packaging and Shipment
Assembled boards are packaged based on your requirements, labeled with necessary documentation, and shipped via your requested transport.
PCBA Process Step | Key Considerations |
---|---|
Sourcing Components | Lead times, authorized distribution, allocation risks, cost optimization |
Incoming Components Inspection | Verification, visual inspection, dimensional checking, functional testing |
Solder Paste Stencil Creation | Precision, quality, cleanliness |
Solder Paste Printing | Accuracy, quality inspection |
SMT Pick-and-Place | Speed, precision |
SMT Reflow Soldering | Profiles, paste, thermal management |
Through-Hole Insertion | Accuracy, lead bending |
Wave Soldering | Nitrogen blanketing, selective wave |
Conformal Coating | Selective application, protection |
AOI and Testing | Detecting defects, validating function |
Box Build Assembly | Product integration |
Final Packaging and Shipment | Protection, documentation |
Ensuring Quality Outcomes
To achieve your quality and reliability objectives using third-party assembly, keep these best practices in mind:
- Perform regular process audits – Routinely verify that your CM follows agreed process controls. Review solder profiles, inspection records, test data, etc.
- Implement statistical process control (SPC) – Analyze process performance metrics over time to catch deviations quickly. Common metrics include defects per million opportunities (DPMO), yield, test pass rate, and more.
- Get IPC certification – Having IPC-certified staff demonstrates assembly process capabilities. IPC-A-610 sets soldering and acceptability standards.
- Validate and document tooling – Ensure all assembly tools are validated as capable of meeting specifications. Retain documentation.
- Conduct sample audits – When taking delivery of finished assemblies, fully inspect and test a sample to catch any issues before receiving the full lot.
- Manage component life cycles – Work with your CM to monitor end-of-life notices and make last-time buys for obsolete components requiring redesign.
- Regularly review corrective actions – Any major defects or escapes should lead to defined containment actions and permanent corrective actions (PCAs). Review effectiveness of PCAs with your CM.
By combining robust quality frameworks with hands-on process verification, companies can feel confident in outsourcing PCBA while still meeting their product requirements.
Conclusion
As PCB assembly becomes more complex, partnering with specialized contract manufacturers enables access to advanced manufacturing capabilities, economies of scale, and technical expertise. However, the process requires careful vetting and management. This guide provides a starting framework for PCBA service evaluation, partner selection, process oversight, and quality assurance. By investing the time upfront to find the right partner and put disciplined governance in place, R&D teams can accelerate development cycles and focus their energy on design innovation rather than manufacturing operations. With a rigorous approach, contract assembly enables companies to deliver high-quality, field-reliable products in a timeframe that supports business success.
Frequently Asked Questions
Q: What documentation do I need to provide to a contract manufacturer for PCBA?
A: Typical documents provided for assembly include:
- Bill of materials – List of components, quantities needed, part numbers, suppliers
- PCB fabrication and assembly drawings
- Schematics
- Approved vendor list
- Solder paste stencil and solder data sheets
- Product specifications
- Any required testing instructions
Q: How can I ensure the security of my intellectual property when using a contract manufacturer?
A: Protect IP by having a non-disclosure agreement (NDA) in place. Only provide necessary documentation. Use component reference designators rather than names. Secure any software code or firmware. Routinely audit their security practices.
Q: What is the typical lead time for PCBA production?
A: Lead time depends on factors like order size, production scheduling, and component availability. Typicalassembly lead times range from 2-8 weeks. Work closely with your CM on component procurement to avoid delays.
Q: What standards apply to PCB assembly quality?
A: Key standards include:
- IPC J-STD-001 – Requirements for soldered electrical and electronic assemblies
- IPC-A-610 – Acceptability of electronic assemblies
- IPC-6012 – Qualification and performance of rigid printed boards
Q: Can I easily switch between contract manufacturers if needed?
A: While possible, switching CMs involves re-qualifying processes, creating new documentation packages, and aligning on new procedures. Maintaining a second source provider is recommended for supply continuity if making a complete change.
0 Comments