What are PCBs?
PCBs, or Printed Circuit Boards, are the foundation of modern electronics. These boards are used to mechanically support and electrically connect electronic components using conductive tracks, pads, and other features etched from copper sheets laminated onto a non-conductive substrate. PCBs are essential in the design and manufacture of electronic devices, ranging from simple single-layer boards to complex multi-layer boards used in advanced electronic systems.
Types of PCBs
There are several types of PCBs, each with its own unique characteristics and applications:
-
Single-layer PCBs: These are the most basic and cost-effective type of PCBs, with components and tracks on one side of the board.
-
Double-layer PCBs: These boards have conductive layers on both sides, allowing for more complex designs and higher component density.
-
Multi-layer PCBs: These boards consist of three or more conductive layers, enabling even more intricate designs and improved signal integrity.
-
Flexible PCBs: These boards are made from flexible materials, allowing them to bend and conform to various shapes and spaces.
-
Rigid-Flex PCBs: These boards combine rigid and flexible sections, offering the benefits of both types of PCBs in a single design.
PCB Type | Layers | Complexity | Cost | Applications |
---|---|---|---|---|
Single-layer | 1 | Low | Low | Simple devices, DIY projects |
Double-layer | 2 | Medium | Medium | Most consumer electronics |
Multi-layer | 3+ | High | High | Advanced electronics, aerospace, military |
Flexible | 1-2 | Medium | Medium | Wearables, medical devices, compact designs |
Rigid-Flex | 2+ | Very High | Very High | Complex devices requiring both rigidity and flexibility |
PCB Design Process
The PCB design process involves several steps, from concept to final production:
1. Schematic Design
The first step in PCB design is creating a schematic diagram that represents the electrical connections between components. This is done using Electronic Design Automation (EDA) software, such as:
- KiCad
- Eagle
- Altium Designer
- OrCAD
2. Component Selection and Placement
Once the schematic is complete, the next step is to select the appropriate components and place them on the PCB layout. Factors to consider when selecting components include:
- Functionality
- Size and package type
- Power requirements
- Cost and availability
3. PCB Layout
After component placement, the PCB layout is created by routing the conductive tracks between components according to the schematic. Key considerations during PCB layout include:
- Signal integrity
- Power distribution
- Electromagnetic compatibility (EMC)
- Thermal management
- Manufacturing constraints
4. Design Rule Check (DRC) and Gerber File Generation
Before sending the PCB design for manufacturing, it is essential to perform a Design Rule Check (DRC) to ensure that the layout meets all the necessary manufacturing constraints and design guidelines. Once the DRC is passed, Gerber files are generated, which contain all the information needed for PCB Fabrication.
5. PCB Fabrication and Assembly
The final step in the PCB design process is fabrication and assembly. PCB fabrication involves creating the physical board based on the Gerber files, while assembly involves soldering the components onto the board. This can be done manually for small-scale production or using automated pick-and-place machines for larger volumes.
PCB Materials and Properties
PCBs are made from a variety of materials, each with its own unique properties and characteristics. The most common PCB materials include:
1. FR-4
FR-4 is the most widely used PCB material, composed of a glass-reinforced epoxy laminate. It offers good mechanical strength, electrical insulation, and thermal stability.
2. Polyimide
Polyimide is a high-performance material used in flexible PCBs and applications requiring high temperature resistance and dimensional stability.
3. PTFE (Teflon)
PTFE, or Polytetrafluoroethylene, is a low-loss dielectric material used in high-frequency applications, such as RF and microwave circuits.
4. Aluminum
Aluminum PCBs are used in applications requiring excellent thermal conductivity, such as high-power LED lighting and power electronics.
Material | Dielectric Constant | Dissipation Factor | Thermal Conductivity (W/mK) | Tg (°C) | Applications |
---|---|---|---|---|---|
FR-4 | 4.5 | 0.02 | 0.3 | 130-140 | General purpose |
Polyimide | 3.5 | 0.002 | 0.2 | 260 | Flexible PCBs, high-temp |
PTFE | 2.1 | 0.001 | 0.25 | 327 | High-frequency, low-loss |
Aluminum | – | – | 150-220 | – | High-power, thermal management |
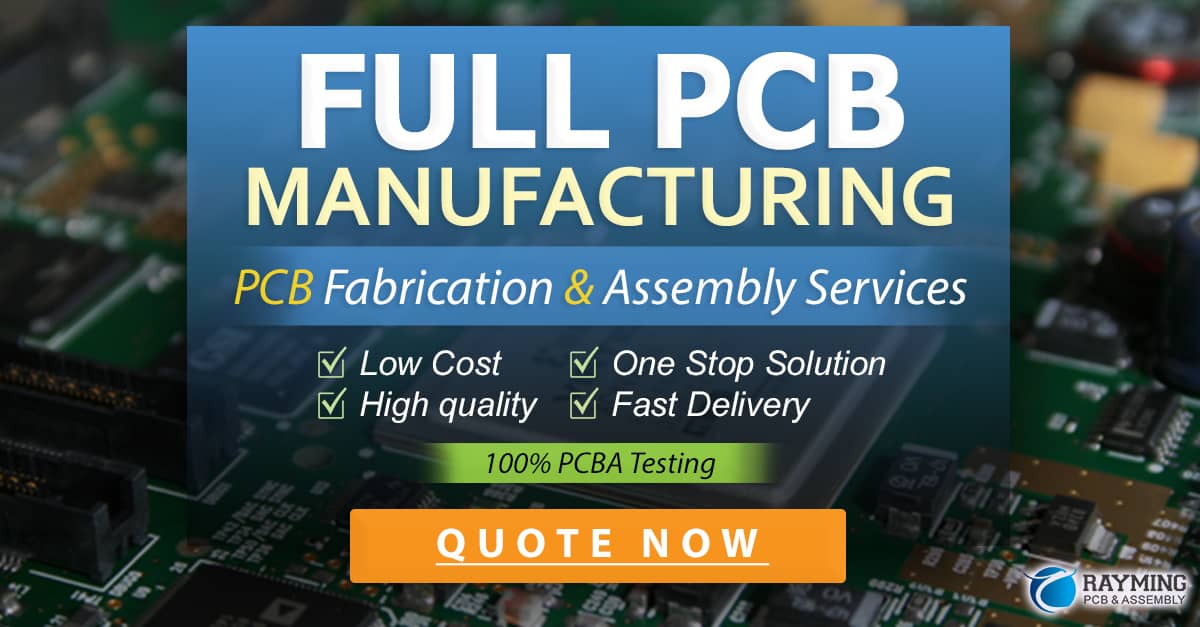
PCB Manufacturing Processes
PCB manufacturing involves several processes, each contributing to the final quality and reliability of the board:
1. Etching
Etching is the process of removing unwanted copper from the PCB substrate to create the desired conductive pattern. The most common etching methods are:
- Chemical etching: Uses a chemical solution to dissolve the unwanted copper.
- Plasma etching: Uses a plasma to remove the copper in a highly controlled manner.
2. Drilling
Drilling creates holes in the PCB for component leads, vias, and mounting. This can be done using mechanical drills or laser drilling for smaller, more precise holes.
3. Plating
Plating involves depositing a thin layer of metal (usually copper) onto the PCB surface and in the drilled holes to improve conductivity and protect the copper from oxidation. Additional finishes, such as nickel, gold, or tin, may be applied for specific applications or to enhance solderability.
4. Solder Mask and Silkscreen
The solder mask is a protective layer applied to the PCB surface to prevent accidental short circuits and protect the copper from oxidation. Silkscreen is a printed layer that adds text, logos, and component identifiers to the PCB for easier assembly and debugging.
PCB Testing and Inspection
To ensure the quality and reliability of PCBs, various testing and inspection methods are employed throughout the manufacturing process:
1. Automated Optical Inspection (AOI)
AOI uses cameras and image processing algorithms to inspect the PCB for defects, such as missing components, incorrect component placement, or solder bridging.
2. X-ray Inspection
X-ray inspection is used to detect defects in hidden or obscured areas, such as under Ball Grid Array (BGA) packages or within multi-layer boards.
3. In-Circuit Testing (ICT)
ICT uses a bed-of-nails fixture to make electrical contact with the PCB and test the functionality of individual components and circuits.
4. Functional Testing
Functional testing involves powering up the assembLED PCB and verifying that it performs as intended in its final application.
Frequently Asked Questions (FAQ)
-
What is the difference between a single-layer and a double-layer PCB?
A single-layer PCB has conductive tracks and components on one side of the board, while a double-layer PCB has conductive layers on both sides, allowing for more complex designs and higher component density. -
What is the purpose of a solder mask on a PCB?
The solder mask is a protective layer applied to the PCB surface to prevent accidental short circuits and protect the copper from oxidation. It also helps to define the areas where solder should be applied during assembly. -
What is the role of vias in a PCB?
Vias are conductive holes that connect different layers of a multi-layer PCB, allowing signals and power to pass between layers. They are essential for creating complex interconnects and optimizing signal routing. -
What is the difference between through-hole and surface-mount components?
Through-hole components have long leads that are inserted into holes drilled in the PCB and soldered on the opposite side. Surface-mount components have smaller leads or pads that are soldered directly onto the surface of the PCB, allowing for higher component density and smaller board sizes. -
What is the purpose of a Design Rule Check (DRC) in PCB design?
A Design Rule Check (DRC) is performed to ensure that the PCB layout meets all the necessary manufacturing constraints and design guidelines. This includes checking for minimum trace widths, clearances, drill sizes, and other parameters to ensure that the PCB can be reliably manufactured and assembled.
In conclusion, understanding the fundamentals of PCBs is essential for anyone involved in electronic design, manufacturing, or troubleshooting. By familiarizing yourself with the types of PCBs, design processes, materials, manufacturing techniques, and testing methods, you can create more reliable, efficient, and cost-effective electronic products. As technology continues to advance, staying up-to-date with the latest developments in PCB design and manufacturing will be crucial for staying competitive in the ever-evolving world of electronics.
0 Comments