Factors Affecting PCB Assembly Cost
Several variables come into play when determining the total cost of PCB assembly. These include:
- PCB design complexity
- Component selection and sourcing
- Manufacturing process and technology
- Production volume and batch size
- Quality control and testing requirements
- Shipping and logistics
Let’s dive deeper into each of these factors to understand their impact on the overall PCB assembly cost.
PCB Design Complexity
The complexity of your PCB design is one of the most significant cost drivers in the assembly process. A more intricate design with a higher number of layers, smaller trace widths and spaces, and advanced features like blind and buried vias will naturally incur higher manufacturing costs.
Here’s a breakdown of how design complexity affects PCB assembly cost:
Design Feature | Cost Impact |
---|---|
Number of layers | More layers = higher cost |
Trace width/spacing | Smaller traces/spaces = higher cost |
Vias (through-hole, blind, buried) | Advanced via types = higher cost |
Surface finish (HASL, ENIG, OSP, etc.) | Advanced finishes = higher cost |
Unique shapes or cutouts | Non-standard shapes = higher cost |
To optimize costs, consider simplifying your PCB design wherever possible without compromising functionality. Work closely with your PCB design team and assembly partner to identify opportunities for cost savings through design optimization.
Component Selection and Sourcing
The components you choose for your PCB assembly project also play a crucial role in determining the overall cost. Factors to consider include:
- Component availability and lead times
- Minimum order quantities (MOQs)
- Component packaging (loose, tape and reel, trays)
- Special handling requirements (moisture sensitivity, ESD protection)
Selecting readily available, industry-standard components can help reduce costs and lead times. However, there may be cases where a specialized or custom component is necessary to meet specific performance requirements. In such situations, work with your sourcing team to identify reliable suppliers and negotiate favorable pricing and lead times.
Component Factor | Cost Optimization Strategy |
---|---|
Availability | Choose readily available, industry-standard components |
MOQs | Plan for production volumes that meet supplier MOQs |
Packaging | Opt for tape and reel packaging for automated assembly |
Special handling | Minimize components with special handling requirements |
Manufacturing Process and Technology
The manufacturing process and technology used in PCB assembly also significantly impact the overall cost. Key considerations include:
- SMT (surface mount technology) vs. through-hole assembly
- Automated vs. manual assembly processes
- Reflow soldering vs. Wave Soldering
- Cleaning and inspection requirements
In general, automated SMT Assembly is more cost-effective for high-volume production, while manual through-hole assembly may be more economical for low-volume or prototype builds. The choice of soldering method (reflow or wave) depends on the components used and the specific requirements of your PCB design.
Manufacturing Process | Cost Impact |
---|---|
SMT assembly | More cost-effective for high-volume production |
Through-hole assembly | More economical for low-volume or prototype builds |
Automated assembly | Lower per-unit costs for high-volume production |
Manual assembly | Higher per-unit costs, suitable for low-volume or complex assemblies |
Reflow soldering | Compatible with SMT components, more common in PCB assembly |
Wave soldering | Required for through-hole components, specialized process |
Work with your PCB Assembly Partner to determine the most suitable manufacturing process and technology for your project, considering your budget, timeline, and quality requirements.
Production Volume and Batch Size
Production volume and batch size are critical factors in determining PCB assembly cost. In general, larger production volumes result in lower per-unit costs due to economies of scale. This is because fixed costs, such as setup and tooling expenses, are spread across a larger number of units.
However, it’s essential to strike a balance between production volume and inventory management. Producing too many units at once can lead to excess inventory and tied-up capital, while too few units may result in higher per-unit costs and more frequent production runs.
Production Volume | Cost Impact |
---|---|
Low (< 100 units) | Higher per-unit costs, suitable for prototypes or small batches |
Medium (100-1,000 units) | Moderate per-unit costs, ideal for small-scale production |
High (> 1,000 units) | Lower per-unit costs, benefits from economies of scale |
Consider your anticipated demand, product lifecycle, and inventory holding costs when determining the optimal production volume and batch size for your PCB assembly project.
Quality Control and Testing
Ensuring the quality and reliability of your assembled PCBs is crucial for the success of your project. However, implementing robust quality control and testing procedures can also impact the overall assembly cost. Key aspects to consider include:
- In-circuit testing (ICT)
- Functional testing
- Automated optical inspection (AOI)
- X-ray inspection
- Environmental stress screening (ESS)
The level of quality control and testing required depends on the specific requirements of your industry, application, and target market. While more stringent testing may increase upfront assembly costs, it can ultimately save money by reducing the risk of field failures and product returns.
Testing Method | Cost Impact | Benefit |
---|---|---|
ICT | Moderate | Detects component and assembly defects |
Functional testing | Moderate to high | Verifies product functionality and performance |
AOI | Low to moderate | Identifies surface-level assembly defects |
X-ray inspection | High | Detects hidden defects in complex assemblies |
ESS | High | Identifies potential reliability issues through accelerated stress testing |
Work with your PCB assembly partner to develop a quality control and testing plan that balances cost and risk, ensuring that your assembled PCBs meet the required quality standards for your application.
Shipping and Logistics
Finally, shipping and logistics costs can also impact the total cost of PCB assembly, especially for projects involving overseas manufacturing or time-sensitive deliveries. Factors to consider include:
- Shipping method (air, sea, ground)
- Packaging requirements
- Customs duties and taxes
- Insurance and handling fees
To optimize shipping and logistics costs, consider the following strategies:
- Plan ahead to allow for longer lead times and more cost-effective shipping methods
- Consolidate shipments whenever possible to reduce per-unit shipping costs
- Work with your assembly partner to optimize packaging and minimize dimensional weight
- Consider using a third-party logistics provider (3PL) to streamline customs clearance and distribution
Shipping Method | Cost | Transit Time |
---|---|---|
Air | High | 1-5 days |
Sea | Low | 20-45 days |
Ground | Moderate | 1-10 days (domestic) |
By carefully managing shipping and logistics aspects of your PCB assembly project, you can minimize costs while ensuring timely delivery of your assembled PCBs.
PCB Assembly Cost Optimization Strategies
Now that we’ve explored the key factors influencing PCB assembly cost, let’s summarize some strategies for optimizing your expenses:
- Simplify your PCB design wherever possible, minimizing complexity and using industry-standard components and processes.
- Plan for production volumes that balance per-unit costs and inventory management, taking advantage of economies of scale when appropriate.
- Choose the most suitable manufacturing process and technology for your project, considering your budget, timeline, and quality requirements.
- Implement a quality control and testing plan that balances cost and risk, ensuring that your assembled PCBs meet the required quality standards.
- Optimize shipping and logistics costs by planning ahead, consolidating shipments, and working with your assembly partner to streamline packaging and distribution.
- Foster open communication and collaboration with your PCB design team and assembly partner to identify opportunities for cost savings and process improvements.
By understanding the factors that impact PCB assembly cost and implementing these optimization strategies, you can effectively manage your budget and ensure the success of your electronics manufacturing project.
Frequently Asked Questions (FAQ)
- What is the most significant factor affecting PCB assembly cost?
-
PCB design complexity is one of the most significant cost drivers in the assembly process. A more intricate design with a higher number of layers, smaller trace widths and spaces, and advanced features will incur higher manufacturing costs.
-
How can I reduce the cost of PCB assembly without compromising quality?
-
To reduce PCB Assembly Costs without compromising quality, consider simplifying your PCB design, using industry-standard components, optimizing production volumes, and working closely with your assembly partner to identify cost-saving opportunities.
-
Is automated or manual assembly more cost-effective for my project?
-
The choice between automated and manual assembly depends on your production volume and PCB complexity. Automated SMT assembly is generally more cost-effective for high-volume production, while manual through-hole assembly may be more economical for low-volume or prototype builds.
-
How do I determine the optimal production volume for my PCB assembly project?
-
To determine the optimal production volume, consider your anticipated demand, product lifecycle, and inventory holding costs. Strike a balance between achieving lower per-unit costs through economies of scale and minimizing excess inventory and tied-up capital.
-
What can I do to minimize shipping and logistics costs for my PCB assembly project?
- To minimize shipping and logistics costs, plan ahead to allow for more cost-effective shipping methods, consolidate shipments whenever possible, optimize packaging to reduce dimensional weight, and consider working with a third-party logistics provider (3PL) to streamline customs clearance and distribution.
By understanding the factors influencing PCB assembly cost and implementing cost optimization strategies, you can effectively manage your budget and ensure the success of your electronics manufacturing project. Remember to foster open communication and collaboration with your PCB design team and assembly partner to identify opportunities for cost savings and process improvements continuously.
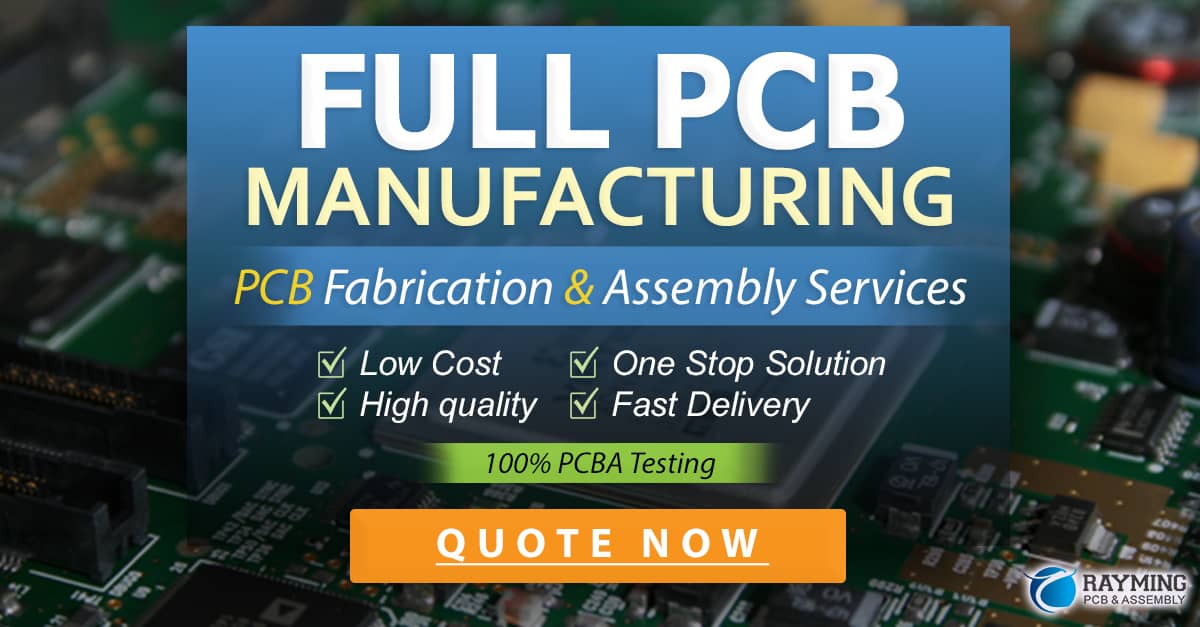
0 Comments