What is SMT Assembly?
SMT (Surface Mount Technology) assembly is a process used in electronics manufacturing where components are mounted directly onto the surface of a printed circuit board (PCB). This process has revolutionized the electronics industry by enabling the production of smaller, lighter, and more efficient electronic devices. SMT assembly has become the standard method for manufacturing a wide range of electronic products, from smartphones and laptops to medical devices and aerospace equipment.
Key components of SMT Assembly
-
PCB: The printed circuit board is the foundation of the SMT assembly process. It is a flat, insulating substrate that has conductive pathways etched or printed onto its surface to connect electronic components.
-
SMD (Surface Mount Devices): These are the electronic components that are mounted onto the PCB. They come in various shapes and sizes, such as resistors, capacitors, integrated circuits (ICs), and transistors.
-
Solder Paste: A mixture of tiny solder particles suspended in a flux medium, which is applied to the PCB pads where components will be placed. The solder paste holds the components in place during the reflow process and forms the electrical and mechanical connection between the component and the PCB.
-
Pick-and-Place Machine: An automated machine that picks up SMDs from feeders and places them onto the solder paste-coated pads on the PCB with high precision and speed.
-
Reflow Oven: A machine that heats the PCB assembly to a specific temperature profile, causing the solder paste to melt and form a permanent bond between the components and the PCB.
Advantages of SMT Assembly in Reducing Manufacturing Costs
1. Miniaturization and Space Savings
One of the primary advantages of SMT assembly is its ability to produce smaller and more compact electronic devices. SMDs are significantly smaller than their through-hole counterparts, allowing for higher component density on a PCB. This miniaturization leads to several cost-saving benefits:
- Reduced PCB size: Smaller PCBs require less raw material, resulting in lower material costs per unit.
- Increased production efficiency: More PCBs can be produced per panel, reducing the overall manufacturing time and cost.
- Lower shipping and packaging costs: Smaller devices require less packaging material and occupy less space during transportation, leading to reduced shipping costs.
2. Faster Assembly Process
SMT assembly is a highly automated process that enables faster production rates compared to traditional through-hole assembly. The use of pick-and-place machines and reflow ovens allows for the rapid placement and soldering of components onto the PCB. This automation offers several cost-saving advantages:
- Reduced labor costs: Automated machines require fewer human operators, reducing labor costs associated with manual assembly.
- Increased throughput: High-speed pick-and-place machines can place thousands of components per hour, significantly increasing production output and reducing the time required to assemble each unit.
- Shorter lead times: Faster assembly processes allow for quicker turnaround times, enabling manufacturers to respond to customer demands more efficiently and reduce inventory holding costs.
3. Improved Quality and Reliability
SMT assembly offers superior quality and reliability compared to through-hole assembly, leading to cost savings in several areas:
- Reduced defects: The automated nature of SMT assembly minimizes human error and ensures consistent placement and soldering of components, resulting in fewer defects and rework.
- Better thermal and mechanical performance: SMDs have a lower profile and are directly bonded to the PCB surface, providing better thermal dissipation and mechanical stability compared to through-hole components. This improved performance leads to higher reliability and reduced failure rates, minimizing warranty claims and repair costs.
- Easier inspection and testing: SMT assemblies are easier to inspect visually and can be tested using automated optical inspection (AOI) systems, allowing for faster and more accurate quality control, reducing the cost of manual inspection and rework.
4. Design Flexibility and Functionality
SMT assembly allows for greater design flexibility and enhanced functionality, which can lead to cost savings in product development and manufacturing:
- Increased component density: The smaller size of SMDs enables designers to pack more functionality into a smaller space, reducing the need for multiple PCBs or larger devices, ultimately lowering material and assembly costs.
- Improved signal integrity: SMDs have shorter lead lengths and are placed closer to the PCB surface, reducing parasitic inductance and capacitance, which improves signal integrity and allows for higher-frequency operation. This enhanced performance can eliminate the need for additional components or shielding, reducing overall material costs.
- Easier design updates and modifications: SMT designs can be easily modified using computer-aided design (CAD) software, allowing for faster and more cost-effective design iterations and updates compared to through-hole designs.
5. Lower Inventory and Logistics Costs
SMT assembly can help reduce inventory and logistics costs in several ways:
- Standardized components: SMDs are widely available and standardized, allowing manufacturers to source components from multiple suppliers and benefit from competitive pricing.
- Reduced inventory holdings: The smaller size of SMDs and the faster assembly process enables manufacturers to maintain lower inventory levels, reducing storage costs and minimizing the risk of obsolete components.
- Streamlined supply chain: The widespread adoption of SMT assembly has led to a more efficient and streamlined electronics supply chain, with distributors and suppliers offering a wide range of SMDs and related services, reducing the costs associated with sourcing and procurement.
Case Studies
1. Smartphone Manufacturer
A smartphone manufacturer switched from through-hole to SMT assembly for its latest model, resulting in significant cost savings:
- PCB size reduction: The use of SMDs allowed for a 30% reduction in PCB size, lowering material costs by 25%.
- Increased production efficiency: The automated SMT assembly process increased production output by 50%, reducing the time required to assemble each phone by 40%.
- Improved reliability: The switch to SMT assembly reduced defects by 60%, resulting in a 50% reduction in warranty claims and repair costs.
Cost Factor | Through-Hole Assembly | SMT Assembly | Cost Savings |
---|---|---|---|
Material Costs | $10 per unit | $7.50 per unit | 25% |
Production Time | 60 seconds per unit | 36 seconds per unit | 40% |
Defect Rate | 1% | 0.4% | 60% |
Warranty Claims | $100,000 per year | $50,000 per year | 50% |
2. Medical Device Manufacturer
A medical device manufacturer adopted SMT assembly for its new line of wearable health monitors, achieving significant cost savings and performance improvements:
- Miniaturization: The use of SMDs allowed for a 40% reduction in device size, making the wearable monitor more comfortable for patients and reducing material costs by 30%.
- Faster assembly: The SMT assembly process increased production output by 60%, reducing the time required to assemble each device by 45%.
- Enhanced functionality: The increased component density enabled by SMT assembly allowed for the integration of additional sensors and features, improving the device’s marketability and value proposition.
Cost Factor | Through-Hole Assembly | SMT Assembly | Cost Savings |
---|---|---|---|
Material Costs | $20 per unit | $14 per unit | 30% |
Production Time | 90 seconds per unit | 49.5 seconds per unit | 45% |
Device Size | 50mm x 50mm x 20mm | 40mm x 40mm x 15mm | 40% |
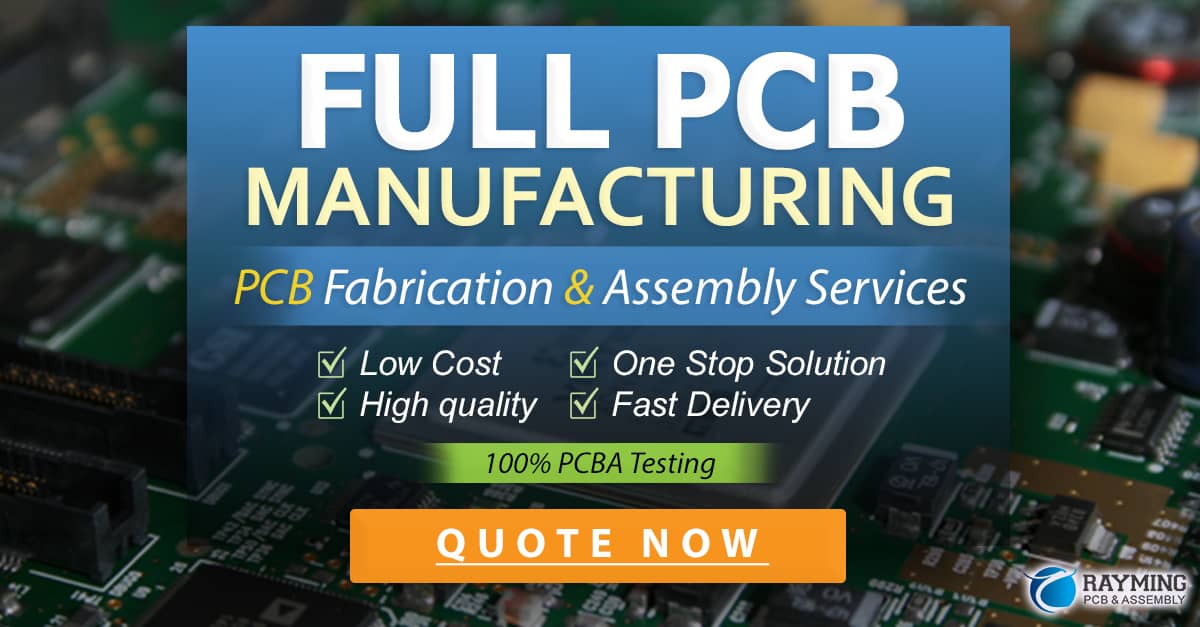
Frequently Asked Questions (FAQ)
-
Q: What is the difference between SMT and through-hole assembly?
A: SMT (Surface Mount Technology) assembly involves mounting components directly onto the surface of a PCB, while through-hole assembly requires components to be inserted into drilled holes on the PCB and soldered on the opposite side. SMT assembly allows for smaller components, higher component density, and faster automated assembly compared to through-hole assembly. -
Q: Is SMT assembly suitable for all types of electronic products?
A: SMT assembly is suitable for a wide range of electronic products, from consumer electronics to industrial and medical devices. However, some components, such as certain connectors or high-power components, may require through-hole assembly. In some cases, a combination of SMT and through-hole assembly (mixed technology) may be used to achieve the desired functionality and reliability. -
Q: How does SMT assembly impact product reliability?
A: SMT assembly generally improves product reliability compared to through-hole assembly. SMDs have a lower profile and are directly bonded to the PCB surface, providing better thermal dissipation and mechanical stability. The automated nature of SMT assembly also reduces human error and ensures consistent placement and soldering of components, resulting in fewer defects and improved overall reliability. -
Q: What are the challenges associated with adopting SMT assembly?
A: Some challenges associated with adopting SMT assembly include the initial investment in specialized equipment (pick-and-place machines, reflow ovens, etc.), the need for skilled operators and technicians, and the potential for more complex design and layout considerations. However, the long-term cost savings and performance benefits often outweigh these initial challenges. -
Q: Can existing through-hole designs be converted to SMT assembly?
A: In many cases, existing through-hole designs can be converted to SMT assembly. This process involves redesigning the PCB layout to accommodate SMDs, updating the bill of materials (BOM) to specify SMD equivalents for through-hole components, and modifying the assembly process to incorporate SMT techniques. However, the feasibility and cost-effectiveness of converting a design to SMT assembly should be evaluated on a case-by-case basis, considering factors such as product complexity, volume, and target market.
Conclusion
SMT (Surface Mount Technology) assembly offers numerous advantages over traditional through-hole assembly in reducing manufacturing costs for electronic products. The miniaturization, faster assembly process, improved quality and reliability, design flexibility, and lower inventory and logistics costs associated with SMT assembly contribute to significant cost savings throughout the product lifecycle.
As demonstrated by the case studies, manufacturers across various industries, from consumer electronics to medical devices, have achieved substantial cost reductions and performance improvements by adopting SMT assembly. The smaller PCB sizes, increased production efficiency, reduced defect rates, and enhanced functionality enabled by SMT assembly translate into lower material costs, shorter production times, and improved product marketability.
While adopting SMT assembly may involve initial investments and challenges, the long-term benefits in terms of cost savings, product quality, and competitive advantage make it a compelling choice for manufacturers looking to optimize their production processes and reduce overall manufacturing costs.
As the electronics industry continues to evolve and demand for smaller, more efficient, and cost-effective products grows, SMT assembly will likely remain a crucial technology for manufacturers seeking to stay competitive and meet the ever-changing needs of their customers.
0 Comments