Introduction to EMS Providers for PCB Assembly
Electronic manufacturing services (EMS) providers offer a range of solutions for companies that design and manufacture electronic devices and components. One of the core services offered by EMS providers is printed circuit board (PCB) assembly. This involves assembling electronic components onto PCBs using surface mount technology (SMT) and through-hole technology (THT) processes.
There are many benefits to outsourcing PCB assembly to an EMS provider. These include:
- Access to advanced manufacturing capabilities – EMS providers invest heavily in SMT equipment, clean rooms, and workforce skills. This gives them significant manufacturing capabilities difficult for an individual company to replicate.
- Cost savings – By leveraging economies of scale, EMS providers can offer PCB assembly services at very competitive costs. It is often cheaper to outsource production rather than maintain specialized equipment and staff.
- Improved time-to-market – Outsourcing PCB assembly frees up designers and engineers to focus on core product development. Getting to market faster is critical for many companies.
- Flexibility – EMS providers maintain extra capacity allowing for quick production ramp-ups when needed. They also readily shift between products for different customers.
- Quality – Leading EMS providers adhere to strict quality standards and certifications resulting in high-reliability PCB assembly.
Below we explore key factors to consider when selecting an EMS partner for PCB assembly.
Key Factors When Selecting an EMS Provider for PCB Assembly
Manufacturing Capabilities and Technology
A top priority is assessing the manufacturing processes, equipment, and workforce skills the EMS provider possesses. Key factors include:
- SMT lines – Highly automated SMT lines accurately and quickly place tiny surface mount components onto PCBs. Look for lines with the latest precision technology.
- Soldering capabilities – The provider should offer wave, reflow, and selective soldering to address pads and pins not suitable for SMT. Pin-in-paste is ideal for bottom terminated components.
- Inspection – Automated optical inspection (AOI) and X-ray inspection after SMT component placement and soldering ensures quality standards.
- IPC certifications – Certification to IPC industry standards for electronics assembly signifies electronics manufacturing expertise. IPC-A-610 certification for acceptability of electronic assemblies is key.
- Miniaturization capabilities – Many products require assembling ultra-small components. Evaluate the EMS provider’s skill in handling miniature components.
- Testing – Can the provider conduct needed tests in-house like in-circuit testing? This avoids delays in third-party testing.
Table 1 – Comparison of Key Manufacturing Capabilities of EMS Providers
EMS Provider | SMT Lines | Soldering Methods | Inspection Tools | IPC Certifications | Miniaturization Skills | In-House Testing |
---|---|---|---|---|---|---|
EMS A | Latest models | All main methods | AOI, X-ray | 620, 7711/7721 | Excellent | Limited |
EMS B | Outdated models | Wave and reflow | Manual visual | 610, 7711 | Average | Broad capabilities |
EMS C | Modern | Wave only | AOI | 610 | Poor | None |
Supply Chain Management
The EMS provider should demonstrate robust supply chain capabilities:
- Procurement – Do they have purchasing power to get the best component pricing and availability? Can they procure from local as well as global sources?
- Inventory – What level of component stocks do they maintain? Can they handle inventory for customers? Shorter lead times are possible with on-hand components.
- Supplier network – An extensive qualified supplier base reduces risk and provides component flexibility. Preferred supplier programs yield cost benefits.
- Counterfeit avoidance – Leading EMS providers implement strict counterfeit component screening standards for their supply chains using testing, certification, and audits.
- Logistics – They should have expertise in international shipping, customs clearance, bonded warehouses, and JIT delivery of PCB assemblies to customers or distribution centers.
Table 2 – Supply Chain Capabilities Comparison between EMS Providers
Supply Chain Factors | EMS A | EMS B | EMS C |
---|---|---|---|
Purchasing Power | High | Medium | Low |
Component Inventory | Extensive | Medium | Minimal |
Supplier Network | Global | Regional | Local |
Counterfeit Avoidance | Robust | Basic | Minimal |
Logistics Services | End-to-end | Limited | Basic |
Quality Systems
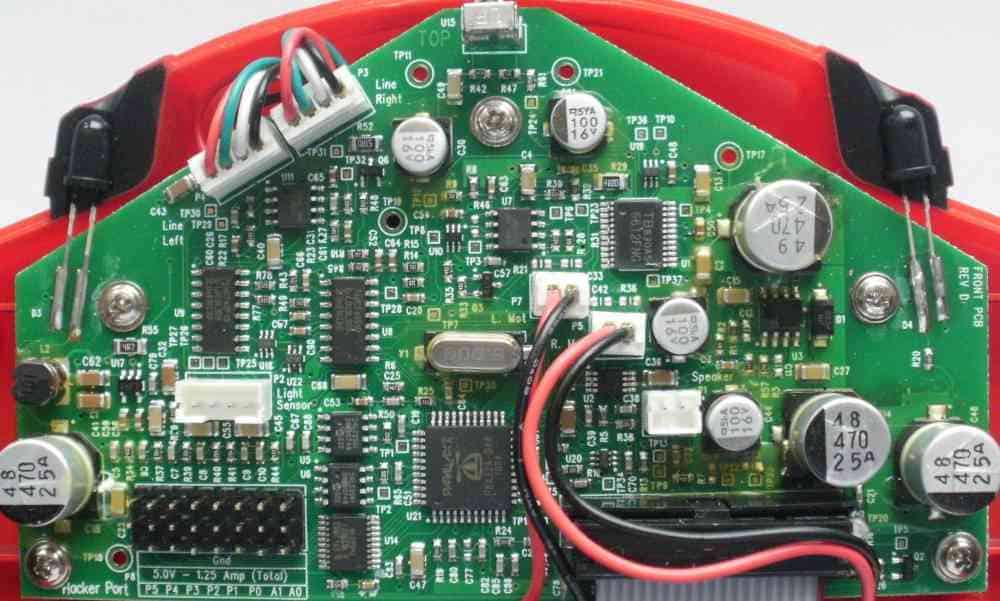
A strong quality system is vital for consistent, high-reliability PCB assembly. Key factors are:
- ISO certification – ISO 9001 compliance reflects solid quality management systems. More advanced certifications like AS9100D or ISO 13485 for medical devices signify world-class quality.
- Process controls – The EMS provider should demonstrate disciplined SMT assembly process controls. This includes clear operator instructions, preventative equipment maintenance, process monitoring, change control procedures, ESD controls, etc.
- Inspection rigor – How often do they perform inspection for workmanship defects? What are their AQL levels? Inspecting every PCB is ideal.
- Traceability – They should maintain lot traceability down to individual PCB serial numbers, not just panels or batches. This enables pinpointing any production issues.
- Corrective action – When defects occur, do they have containment procedures and root cause analysis processes to prevent recurrences?
- Expertise in quality standards – Proficiency in related standards like IPC J-STD-001, IPC-A-610, and IPC-7711/7721 is important.
Engineering Support
The EMS provider should offer knowledgeable engineering support:
- DFM analysis – Can they assess PCB designs and recommend design for manufacturability (DFM) improvements? This avoids downstream issues.
- BOM review – To spot potential component procurement and assembly issues early, they should thoroughly review bill of material (BOM) and component documentation.
- NPI management – They need proven new product introduction (NPI) processes to seamlessly ramp products from design to mass production.
- Test development – For complex products, their engineers should assist customers in designing testing procedures and solutions.
- Tools and analysis – Leading EMS providers possess tools like automated X-ray inspection, 3D scanning, failure analysis labs, and environmental stress testing equipment.
Customer Focus
The EMS provider should act as an extension of the customer’s team with:
- Communication – Open, honest, and frequent communication at all levels avoids issues. Establish metrics with regular status reports.
- Customer portal – An online portal provides design, order, and project tracking in real-time.
- Change management – They should have a structured engineering change management process to rapidly implement needed design tweaks.
- Continuous improvement – A key goal should be continuous improvement in product quality, efficiency, and cost reduction. They should leverage customer feedback for this.
- Problem resolution – When rare problems occur, quick containment and urgent communication to resolve issues is critical.
- Win-win partnerships – Rather than just a vendor, the EMS provider should engage as a strategic partner equally invested in the customer’s success.
The PCB Assembly Process Step-by-Step
Below we outline the typical stages involved in EMS PCB assembly after completing the design phase:
1. Generate BOM and gerber files
The PCB design process results in a bill of materials (BOM) listing all required components, gerber files for board fabrication, and pick-and-place (Centroid) files showing component placements.
2. Procure components
The EMS provider sources all components and raw PCBs from their extensive supplier network. For best pricing and availability, components may be ordered from local or global sources.
3. Kit components
Upon receipt, all components are inspected, tested, and sorted into kits with the required quantities for a particular PCB assembly batch. serialized for full traceability.
4. Solder paste stencil
A thin stainless steel stencil laser cut with the PCB pad geometries is aligned and applied to the bare PCB. It deposits precise amounts of solder paste on pads.
5. SMT component placement
SMT machines read the centriod file to robotically pick components from feeders and rapidly place them accurately onto the solder paste.
6. Reflow soldering
The PCB panel passes through a reflow oven melting the solder paste to electrically and mechanically attach the SMT components.
7. Inspection
AOI optical inspection and staff visually inspect boards and redo component placement if defects are detected.
8. Conformal coating
For environmental protection, a thin acrylic or urethane coating may be selectively sprayed or brushed onto the SMT components and PCB surface.
9. Through-hole insertion
Leaded components are inserted into plated through-holes either manually or using automation.
10. Wave soldering
The assembled board underside passes over a wave of molten solder attaching leaded components. Additional solder may be manually applied.
11. Attachment hardware
Any brackets, connectors, covers are assembled to complete board population. Serial numbers may be applied.
12. Programming
For programmable boards, firmware/software is loaded by technicians or specialized automated equipment.
13. Testing
Testing like in-circuit testing (ICT) verifies all components have been assembled properly and are functioning.
14. Final inspection
Extensive inspection against IPC-A-610 standards checks for any workmanship issues or flaws. X-ray inspection reveals hidden defects.
15. Packaging
PCBs are individually or batch packaged to protect against damage in shipping. Pick-and-place reels or trays, tape-and-reel, tubes are common methods.
16. Inventory or shipping
Finished PCB assemblies are either stocked in the EMS provider warehouse for quick delivery or drop shipped directly to destinations.
Key Considerations in Designing PCBs for EMS Assembly
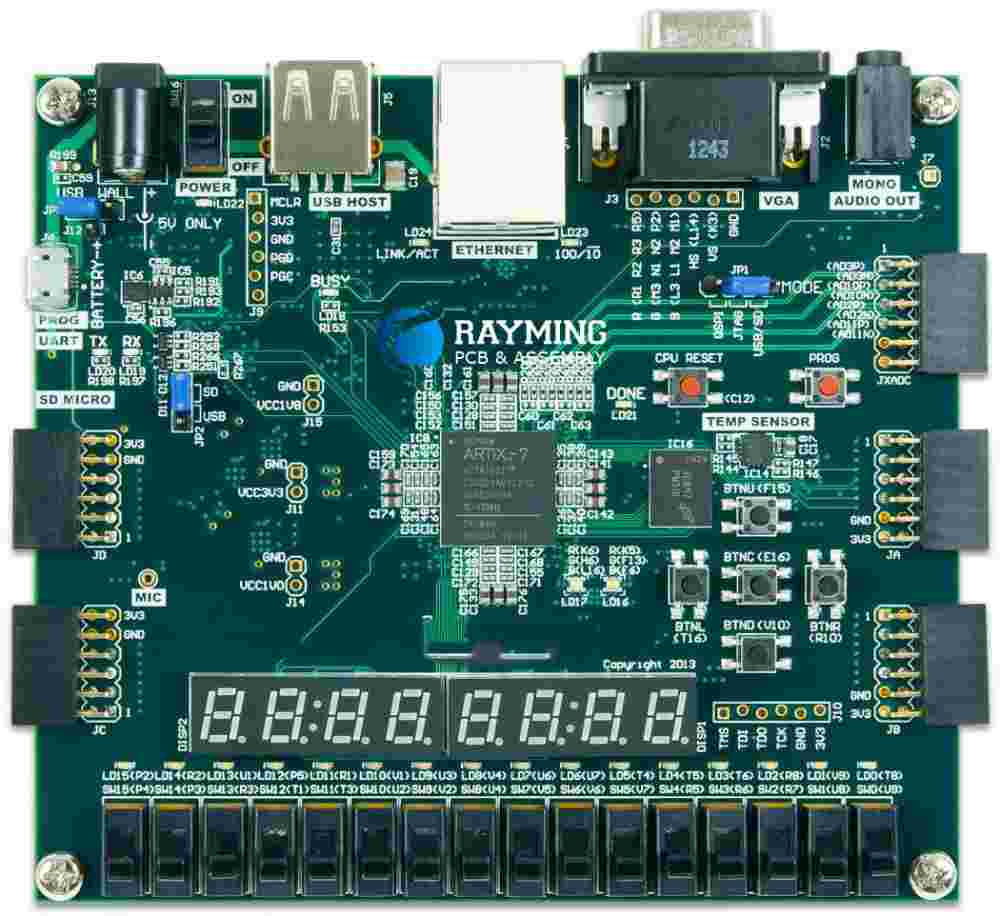
PCB designers should apply design for manufacturability (DFM) principles to optimize boards for ease of volume assembly. Some key guidelines include:
- Component selection – Select component sizes, packages, and lead types standard to EMS provider capability. Understand their minimum component size abilities.
- PCB density – Avoid designs exceeding the assembly density capability of the EMS provider to prevent defects or the need for specialized processes.
- Component placement – Optimize component placement for high-speed automated assembly. Grouping similar components together aids this.
- Solderability – Specify component leads, terminals, and PCB pad finishes with excellent soldering compatibility and capillary action like ENIG or immersion silver plating.
- Thermal relief – Include thermal relief cutouts in large copper regions on PCB pads to facilitate solder flow underneath component leads.
- Fiducials and tolerances – Have at least 2 to 3 fiducial markers on all board layers. Control board fabrication tolerances to aid automated assembly.
- Test points – Include test points linking to most nets to enable in-circuit testing. Testability equals quality.
- ESD – Follow ESD handling guidelines like grounding points. Sensitive components may need ESD protection diodes.
Collaborating with EMS engineers on DFM analysis from the start of the design process ensures manufacturability and avoids costly re-spins later on.
FAQs on EMS PCB Assembly
Q: What are the typical lead times for EMS PCB assembly?
Lead times vary considerably based on factors like order size, production backlogs, complexity, procurement delays, and testing requirements. However, 4 to 6 weeks from issuing an assembly order is fairly standard for moderate volumes of boards. For high-volume production runs, lead times under 2 weeks are possible. Prototype and NPI builds often take 6 to 8 weeks.
Q: How long do EMS providers keep components in stock?
For expensive or critical components, EMS providers aim to keep adequate stocks for 6 to 12 months based on forecasts from customers. Fast moving commodity components are kept in stock continuously. Uncommon components may be sourced on relatively short lead times only when needed for orders. Keeping stock too long risks component expiration or obsolescence.
Q: Can EMS providers handle low-volume or prototype PCB assembly?
Absolutely. The same advanced assembly lines that build high volumes are adept at lower volumes. Prototypes may follow a longer NPI process versus standard products already proven for manufacturing. Lower volumes do incur slightly higher per unit costs. But EMS providers gain efficiencies with common components used across different customer products.
Q: Should every PCB be tested by EMS providers?
While 100% electrical testing of every board is ideal, for high volume cost-sensitive products, testing a statistical sample is common. Critical parameters are tested on a sample basis per an acceptance quality limit (AQL) plan. Functional testing typically occurs on a smaller percentage. Higher reliability products like medical devices often mandate testing every board.
Q: Can EMS providers assemble odd-form factor or large PCBs?
While uncommon large PCBs or unusual shapes can require specialized handling, experienced EMS providers have custom fixtures to accommodate non-standard assemblies. Large boards may use tall solder pallet wave solder machines. Flex-rigid PCBs integrate flex circuits with rigid boards. Discuss any special requirements with your EMS early in the design phase.
Conclusion
Partnering with a high-caliber EMS provider for PCB assembly provides immense technology resources and manufacturing expertise difficult for product companies to replicate in-house. Their economies of scale produce cost savings while maintaining quality. Rigorous selection criteria for capabilities, supply chain, quality, engineering, and customer service ensures selecting the right strategic EMS partner for your program’s success. Investing extra effort upfront in design for manufacturability ensures a smooth manufacturing ramp and fulfillment of product reliability goals.
0 Comments