Electronics assembly is the process of mounting and soldering electrical components onto printed circuit boards (PCBs) to create fully functional electronic devices and systems. As products become smaller and more complex, using proper assembly techniques, process controls, and best practices is essential for producing high-quality and reliable electronics.
Key Electronics Assembly Techniques
Several standard techniques are utilized during modern electronics assembly:
SMT Assembly
The majority of components are surface mount devices (SMDs) soldered to the PCB surface. Common techniques include:
- Solder Paste Printing – Solder paste is applied on pads through stencils via screen printing or jet dispensing.
- Pick and Place – Robotic pick and place machines populate boards with components rapidly and precisely.
- Reflow Soldering – Assemblies pass through ovens to heat solder paste and attach components.
Through-Hole Assembly
Leaded components are inserted into plated through-holes and soldered. Dual-wave soldering is a common high-volume technique.
Box Build Assembly
Larger electromechanical components, cables, and housings are assembled together with the PCBs into final enclosure.
Conformal Coating
Protective coatings shield assembled boards from moisture, debris, and corrosion threats. Selective coating avoids connectors.
###Testing and Inspection
Electrical testing and visual inspection at multiple points ensures quality. Automated optical inspection (AOI) is widely used.
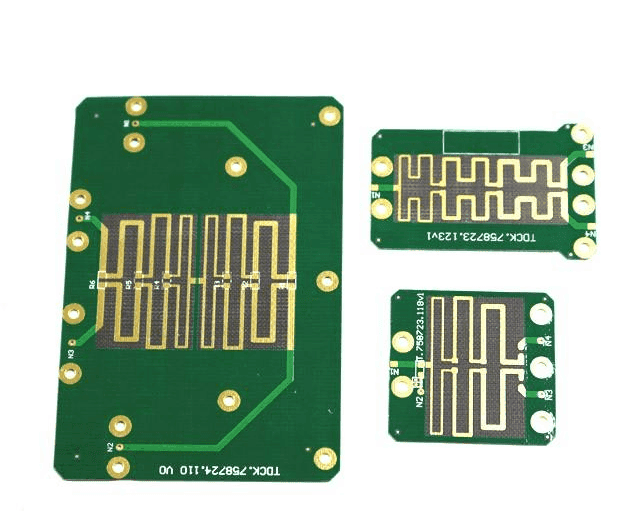
Process Controls and Monitoring
Electronics assembly requires tight process controls and monitoring to build reliability into products:
- Environment Controls – Manage temperature, humidity, and cleanliness in assembly areas.
- In-Process Inspection – Frequency inspection of solder paste, pick and place, and solder joints.
- Traceability – Track components and boards throughout assembly down to the serial number.
- Process Data – Collect and analyze detailed process data to identify potential improvements.
- Corrective Actions – Quickly address any issues observed and identify root causes.
- Process Reviews – Regularly review all processes to confirm procedures are followed consistently.
Best Practices for Quality Assembly
Following best practices ensures consistency and drives quality:
- Qualify Components – Vet suppliers and validate component quality before approving.
- QC Incoming Parts – Inspect incoming components for damage and verify certifications.
- Efficient SMT Programs – Optimize pick and place programs for accuracy, speed, and ease of troubleshooting.
- Standard Operating Procedures – Document procedures for training personnel and process consistency.
- Minimize Handling – Reduce unnecessary handling that could damage boards or components.
- ESD Controls – Use proper ESD handling and packaging methods.
- Cleanliness – Maintain cleanliness of facilities, equipment, and materials.
- Data Management – Organize assembly data in systems for quick analysis and reporting.
- Operator Training – Qualify assembly technicians thoroughly. Evaluate skills regularly.
- Failure Analysis – Investigate fully any defects found to identify improvements.
- Continual Improvement – Set quantified quality goals and consistently refine processes.
Electronics Assembly Quality Metrics
Key metrics provide visibility into process performance and assembly quality:<div class=”table-responsive”>
Metric | Description | Goal |
---|---|---|
First Pass Yield | Percentage of boards passing testing without rework | >98% |
Defects per Million Opportunities (DPMO) | Count of component placement or soldering defects | <100 |
Soldering Defects | Count of insufficient joint, solder balls, etc. | Minimize trend |
Placement Accuracy | Percentage of components in correct location | >99% |
Process Capability (Cpk) | Process consistency vs. tolerances | >1.33 |
Test Coverage | Percentage of components electrically tested | 100% |
</div>
Analyzing these and other metrics enables identifying areas for improvement. Production testing and inspection data offers visibility into assembly robustness.
Electronics Assembly Documentation
Clear documentation is crucial for consistent quality:
- Process Flows – Visual workflows of assembly process steps.
- Work Instructions – Detailed instructions for each process activity.
- Test Procedures – Step-by-step test methods and pass/fail criteria.
- Training Plans – Outline of skills training required for each job.
- Data Forms – Templates for collecting process data for analysis.
- Quality Plans – Defines quality standards, testing, audits, and qualification protocols.
Maintaining Quality through Scale
As production scales from prototype to high-volume, quality focus must be maintained:
- Retain quality-focused staff in key roles even as team grows.
- Keep processes tightly controlled, with automation where possible.
- Expand capacity methodically while monitoring all data for variances.
- Use statistical process control to quickly detect process changes.
- Conduct rigorous supplier oversight and auditing.
- Continually review processes, data, and business systems holistically.
In summary, advanced electronics assembly combines precision techniques with intense quality focus. By leveraging process controls, best practices, quality documentation, and metrics analysis, robust and reliable electronics can be produced at scale. A culture of continual improvement is ultimately key to long term manufacturing excellence.
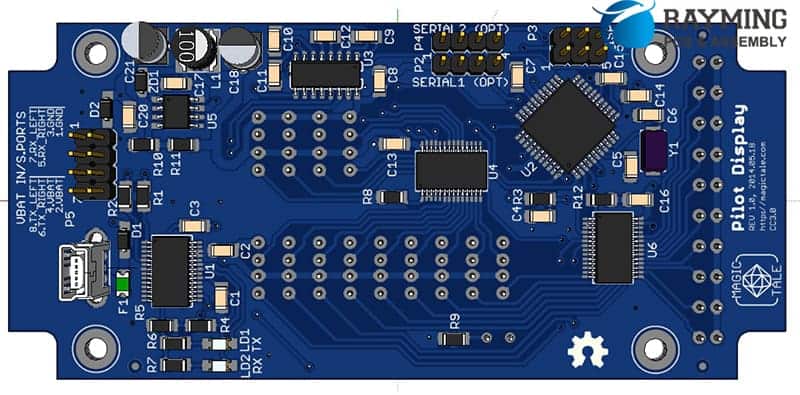
Frequently Asked Questions
What is the most common defect found in electronics assembly?
Insufficient soldering, known as cold solder joints, are the most frequent defect seen in electronics assembly. This can stem from issues like poor thermal control, board warping, or impurities contaminating the joint.
What testing is typically performed for quality control?
Common testing includes in-circuit testing to electrically validate circuits, flying probe testing for shorts, opens, and placement, and automated optical inspection to check solder joints. Function testing verifies overall operation.
What process capability should be targeted for high-volume production?
A process capability (Cpk) greater than 1.33 is generally recommended for critical processes to demonstrate consistency and low defects. Continual improvement targets even higher capability.
How can box build assembly be simplified for operators?
Clear visual instructions, presentation of pre-kitted parts in assembly sequence, purpose-built fixtures, and mistake-proofing features like keyed connectors all help streamline box builds.
What are some key performance indicators (KPIs) for assembly?
First pass yield, defects per million opportunities, placement accuracy, test coverage, workmanship defects, utilization, and cycle time are some core KPIs that provide visibility into assembly performance.
0 Comments