What is a Barebone PCB?
A barebone PCB, also known as a Bare PCB or a printed circuit board without components, is a fundamental building block in electronics. It is a blank printed circuit board that has been manufactured with the necessary copper traces, pads, and holes, but does not have any electronic components soldered onto it. Essentially, it is a blank canvas waiting for the designer to populate it with various components to create a functional electronic device.
Barebone PCBs are used in a wide range of applications, from simple hobbyist projects to complex industrial electronics. They provide a cost-effective and efficient way to create custom electronic circuits, as the designer has complete control over the placement and selection of components.
Advantages of Using Barebone PCBs
There are several advantages to using barebone PCBs in electronic design:
-
Customization: With a barebone PCB, the designer has complete control over the placement and selection of components, allowing for a high degree of customization to suit specific project requirements.
-
Cost-effective: Using a barebone PCB can be more cost-effective than purchasing a pre-assembled PCB or a complete electronic device, especially for small-scale production or prototyping.
-
Flexibility: Barebone PCBs offer greater flexibility in terms of design changes and modifications, as the designer can easily swap out or add components as needed.
-
Educational value: Working with barebone PCBs can be an excellent way to learn about electronic design and assembly, as it provides hands-on experience with component placement and soldering.
Types of Barebone PCBs
Barebone PCBs come in various types, each with its own characteristics and applications:
-
Single-Layer PCBs: These PCBs have conductive traces on only one side of the board, making them the simplest and most cost-effective option. They are suitable for basic, low-density circuits.
-
Double-layer PCBs: These PCBs have conductive traces on both sides of the board, allowing for more complex circuits and higher component density. They are the most common type of PCB used in electronic devices.
-
Multi-layer PCBs: These PCBs have three or more layers of conductive traces, separated by insulating layers. They are used for complex, high-density circuits that require a high level of signal integrity and electromagnetic compatibility.
-
Flexible PCBs: These PCBs are made from flexible materials, such as polyimide, allowing them to bend and conform to various shapes. They are used in applications where space is limited or where the PCB needs to flex during use, such as in wearable electronics.
-
Rigid-flex PCBs: These PCBs combine rigid and flexible sections, providing the benefits of both types. They are used in applications that require both high component density and flexibility, such as in aerospace and military electronics.
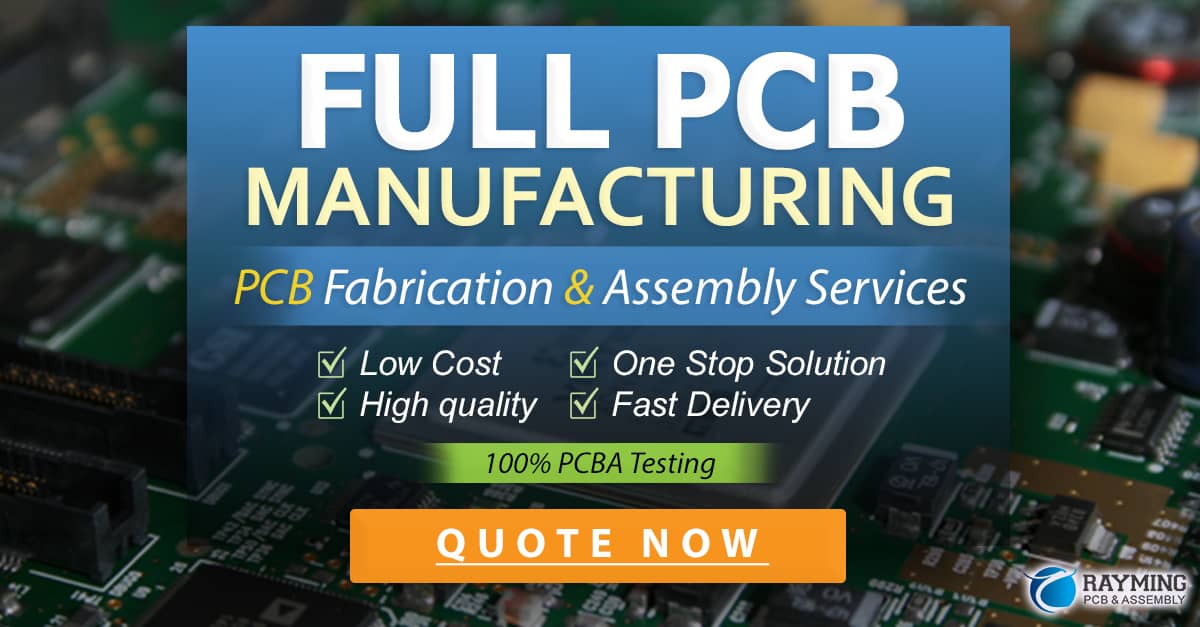
How to Use a Barebone PCB
Using a barebone PCB involves several steps, from designing the circuit to assembling the final product. Here’s a general overview of the process:
-
Circuit design: The first step is to design the electronic circuit using a schematic capture tool or by hand. This involves selecting the appropriate components and determining their connections.
-
PCB layout: Once the circuit design is complete, the next step is to create a PCB layout using a PCB design software. This involves placing the components on the board and routing the copper traces to connect them according to the schematic.
-
PCB fabrication: After the PCB layout is finalized, the barebone PCB can be manufactured by a PCB fabrication company. This process typically involves printing the copper traces onto the board, drilling holes for through-hole components, and applying a protective solder mask and silkscreen.
-
Component procurement: While the barebone PCB is being manufactured, the designer can procure the necessary electronic components based on the bill of materials (BOM) generated from the schematic and PCB layout.
-
PCB Assembly: Once the barebone PCB and components are ready, the next step is to assemble the board. This involves soldering the components onto the PCB, either by hand or using automated assembly methods like wave soldering or reflow soldering.
-
Testing and debugging: After the PCB is assembled, it is essential to test and debug the circuit to ensure it functions as intended. This may involve using various test equipment, such as multimeters, oscilloscopes, and logic analyzers, to measure voltages, currents, and signal waveforms.
-
Enclosure and packaging: Finally, the assembled PCB can be mounted into an enclosure or packaging, depending on the application and end-use requirements.
Choosing the Right Barebone PCB
When selecting a barebone PCB for a project, there are several factors to consider:
-
Size and shape: The size and shape of the PCB should be appropriate for the intended application and enclosure. Consider the available space and any specific dimensional requirements.
-
Number of layers: The number of layers in the PCB will depend on the complexity of the circuit and the required component density. Simple circuits can use single or double-layer PCBs, while more complex designs may require multi-layer boards.
-
Material: The choice of PCB material will depend on the electrical, mechanical, and environmental requirements of the application. Common materials include FR-4, which is a glass-reinforced epoxy laminate, and high-frequency materials like Rogers or Teflon for RF applications.
-
Copper weight: The copper weight, or thickness, of the PCB traces will affect the current-carrying capacity and impedance of the circuit. Thicker copper traces can handle higher currents and provide better power distribution, but may be more expensive.
-
Surface finish: The surface finish of the PCB pads and traces can affect solderability, durability, and signal integrity. Common surface finishes include hot air solder leveling (HASL), immersion silver, immersion tin, and electroless nickel immersion gold (ENIG).
-
Manufacturer reputation: When choosing a PCB manufacturer, consider their reputation, quality control processes, and customer support. Look for manufacturers with good track records and certifications like ISO 9001 or UL listing.
Common Applications of Barebone PCBs
Barebone PCBs are used in a wide range of electronic applications, including:
-
Consumer electronics: Barebone PCBs are used in various consumer electronic devices, such as smartphones, tablets, laptops, and home appliances.
-
Industrial control systems: In industrial settings, barebone PCBs are used to create custom control systems for machinery, automation equipment, and process monitoring.
-
Medical devices: Barebone PCBs are used in medical devices, such as patient monitors, diagnostic equipment, and implantable devices.
-
Automotive electronics: In the automotive industry, barebone PCBs are used in various electronic systems, including engine control units, infotainment systems, and advanced driver assistance systems (ADAS).
-
Aerospace and defense: Barebone PCBs are used in aerospace and defense applications, such as avionics, communication systems, and radar.
-
IoT and wearables: With the growth of the Internet of Things (IoT) and wearable technology, barebone PCBs are increasingly used to create small, low-power, and connected devices.
Barebone PCB Design Considerations
When designing a circuit using a barebone PCB, there are several important considerations to keep in mind:
-
Component selection: Choose components that are appropriate for the intended application, considering factors such as power rating, voltage, and temperature range. Also, ensure that the components are readily available and have a reliable supply chain.
-
Schematic design: Create a clear and well-organized schematic that accurately represents the circuit design. Use standard symbols and conventions, and include necessary information such as component values, reference designators, and pin numbers.
-
PCB layout: When designing the PCB layout, follow best practices for component placement, trace routing, and grounding. Consider factors such as signal integrity, power distribution, and electromagnetic compatibility (EMC).
-
Design for manufacturing (DFM): Design the PCB with manufacturing in mind, following the guidelines and constraints provided by the PCB manufacturer. This includes considerations such as minimum trace width and spacing, hole sizes, and clearances.
-
Design for assembly (DFA): Consider the assembly process when designing the PCB, ensuring that components are easily accessible and can be soldered using the chosen assembly method. Provide clear markings and labels to aid in the assembly process.
-
Design for test (DFT): Incorporate test points and other features that facilitate testing and debugging of the assembled PCB. This can include test pads, vias, or connectors for attaching test equipment.
-
Thermal management: Consider the thermal requirements of the circuit and design the PCB accordingly. This may involve using thermal relief pads, heat sinks, or other thermal management techniques to dissipate heat and prevent component failures.
Barebone PCB Assembly Methods
There are several methods for assembling components onto a barebone PCB, each with its own advantages and limitations:
-
Hand soldering: This is the most basic and low-cost method of PCB assembly, suitable for small-scale production or prototyping. It involves manually soldering components onto the PCB using a soldering iron and solder wire.
-
Wave soldering: This method is used for high-volume production of through-hole PCBs. The assembled PCB is passed over a wave of molten solder, which solders the component leads to the PCB pads.
-
Reflow soldering: This method is used for surface-mount PCBs, where the components are placed onto solder paste applied to the PCB pads. The assembled PCB is then passed through a reflow oven, which melts the solder paste and forms a permanent connection between the components and the PCB.
-
Selective soldering: This method is used for PCBs that have a mix of through-hole and surface-mount components. It involves using a specialized soldering machine that applies solder to specific areas of the PCB, such as through-hole component leads.
-
Vapor phase soldering: This method uses a vapor of heated inert fluid, such as Galden, to reflow the solder paste on the PCB. It provides a more uniform and controlled heating process compared to traditional reflow soldering.
The choice of assembly method will depend on factors such as the type and quantity of components, the production volume, and the available equipment and resources.
Barebone PCB Testing and Debugging
After assembling the barebone PCB, it is essential to test and debug the circuit to ensure it functions as intended. Here are some common testing and debugging techniques:
-
Visual inspection: Perform a thorough visual inspection of the assembled PCB, looking for any obvious defects such as bridged solder joints, missing components, or damaged traces.
-
Continuity testing: Use a multimeter to test for continuity between various points on the PCB, such as power and ground connections, to ensure that there are no open circuits or short circuits.
-
Power-on testing: Apply power to the PCB and check for any signs of malfunction, such as overheating, smoke, or unexpected behavior. Use a multimeter or oscilloscope to measure voltages and currents at key points in the circuit.
-
Functional testing: Test the functionality of the circuit by applying input signals and measuring the output response. Compare the results to the expected behavior based on the circuit design and component specifications.
-
Boundary scan testing: For complex PCBs with high component density, use boundary scan testing techniques, such as JTAG, to test for connectivity and functionality of individual components and interconnects.
-
In-circuit testing: Use an in-circuit tester (ICT) to test individual components and circuits on the PCB, comparing the measured values to the expected values based on the circuit design.
-
Thermal imaging: Use a thermal camera to identify hot spots or areas of excessive heat generation on the PCB, which may indicate component failures or design issues.
When debugging a PCB, use a systematic approach to isolate the problem, such as the divide-and-conquer method or the half-split method. Use appropriate test equipment and software tools to aid in the debugging process, and document any changes or modifications made to the circuit.
FAQ
-
What is the difference between a barebone PCB and a complete electronic device?
A barebone PCB is a blank printed circuit board without any components soldered onto it, while a complete electronic device is a fully assembled and functional product that includes the PCB, components, enclosure, and any necessary software or firmware. -
Can I design my own barebone PCB?
Yes, you can design your own barebone PCB using schematic capture and PCB layout software tools. However, it is essential to have a good understanding of electronic design principles, PCB manufacturing constraints, and industry standards. -
How much does it cost to manufacture a barebone PCB?
The cost of manufacturing a barebone PCB depends on various factors, such as the size and complexity of the board, the number of layers, the chosen material and surface finish, and the quantity ordered. Prices can range from a few dollars for simple, low-quantity boards to several hundred dollars for complex, high-quantity boards. -
What is the minimum order quantity for barebone PCBs?
The minimum order quantity (MOQ) for barebone PCBs varies depending on the manufacturer and the specific requirements of the PCB. Some manufacturers offer low MOQs, such as 5 or 10 pieces, for prototyping and small-scale production, while others may require higher MOQs, such as 100 or 1000 pieces, for larger production runs. -
How long does it take to receive a barebone PCB after placing an order?
The lead time for receiving a barebone PCB depends on the manufacturer, the complexity of the board, and the chosen shipping method. Typical lead times range from a few days for quick-turn prototyping services to several weeks for standard production orders. Some manufacturers offer expedited services for faster turnaround times, but these may come at a higher cost.
Conclusion
Barebone PCBs are a fundamental building block in electronic design, providing a cost-effective and flexible way to create custom electronic circuits. By understanding the different types of barebone PCBs, the design and assembly processes, and the testing and debugging techniques, designers can create reliable and high-quality electronic products.
When working with barebone PCBs, it is essential to follow best practices for circuit design, PCB layout, and manufacturing, and to choose reputable suppliers and manufacturers. By staying up-to-date with the latest technologies and trends in the industry, designers can continue to push the boundaries of what is possible with barebone PCBs and create innovative electronic solutions for a wide range of applications.
0 Comments