Introduction to PCB Fabrication
Printed Circuit Board (PCB) fabrication is a complex process that involves several techniques to create a functional and reliable circuit board. PCB fabrication techniques have evolved over the years, with new technologies and methods being developed to meet the ever-increasing demands of the electronics industry. In this article, we will explore 10 must-know PCB fabrication techniques that are essential for creating high-quality PCBs.
1. Surface Mount Technology (SMT)
Surface Mount Technology (SMT) is a PCB fabrication technique that involves mounting electronic components directly onto the surface of a PCB. SMT has several advantages over through-hole technology, including:
- Smaller component size
- Higher component density
- Faster assembly times
- Lower manufacturing costs
SMT involves several steps, including:
- Solder paste application
- Component placement
- Reflow soldering
- Inspection and testing
Advantage | Description |
---|---|
Smaller component size | SMT components are smaller than through-hole components, allowing for higher component density and smaller PCBs. |
Higher component density | SMT allows for more components to be placed on a PCB, reducing the overall size of the board. |
Faster assembly times | SMT assembly is faster than through-hole assembly, reducing manufacturing time and costs. |
Lower manufacturing costs | SMT requires less drilling and fewer steps than through-hole technology, reducing overall manufacturing costs. |
2. Through-Hole Technology
Through-hole technology is a PCB fabrication technique that involves drilling holes through the PCB and inserting component leads through the holes. The leads are then soldered to the PCB on the opposite side. Through-hole technology has several advantages, including:
- Stronger mechanical connections
- Easier to repair and replace components
- Better for high-power applications
However, through-hole technology also has some disadvantages, including:
- Larger component size
- Lower component density
- Slower assembly times
- Higher manufacturing costs
Advantage | Disadvantage |
---|---|
Stronger mechanical connections | Larger component size |
Easier to repair and replace components | Lower component density |
Better for high-power applications | Slower assembly times |
Higher manufacturing costs |
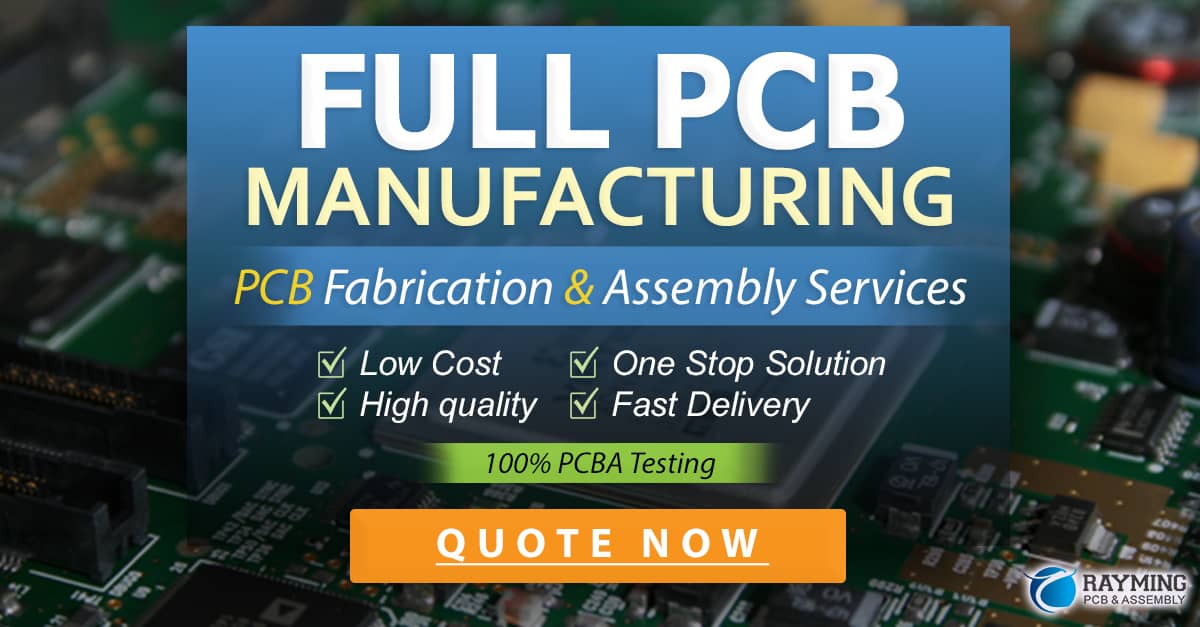
3. Multilayer PCBs
Multilayer PCBs are PCBs that have more than two layers of conductive material. Multilayer PCBs are used in applications that require high component density and complex circuitry. Multilayer PCBs have several advantages, including:
- Higher component density
- Improved signal integrity
- Reduced electromagnetic interference (EMI)
- Better heat dissipation
Multilayer PCBs are fabricated using a process called lamination. The process involves stacking multiple layers of conductive material and insulating material, and then bonding them together under high pressure and temperature.
4. Flexible PCBs
Flexible PCBs are PCBs that are made from flexible materials, such as polyimide or polyester. Flexible PCBs are used in applications that require the PCB to bend or flex, such as in wearable devices or aerospace applications. Flexible PCBs have several advantages, including:
- Reduced weight and size
- Improved reliability
- Better resistance to vibration and shock
- Increased design flexibility
Flexible PCBs are fabricated using a process similar to traditional PCBs, but with some modifications to accommodate the flexible materials.
5. High Density Interconnect (HDI) PCBs
High Density Interconnect (HDI) PCBs are PCBs that have a higher wiring density than traditional PCBs. HDI PCBs are used in applications that require high component density and complex circuitry, such as in smartphones and other portable devices. HDI PCBs have several advantages, including:
- Higher component density
- Improved signal integrity
- Reduced size and weight
- Better thermal management
HDI PCBs are fabricated using advanced techniques such as microvias, blind and buried vias, and sequential lamination.
6. Impedance Control
Impedance control is a PCB fabrication technique that involves controlling the impedance of the PCB traces to ensure proper signal integrity. Impedance control is essential in high-speed applications, such as in telecommunications and networking equipment. Impedance control involves several techniques, including:
- Controlled dielectric thickness
- Controlled trace width and spacing
- Controlled copper thickness
- Use of ground planes and power planes
Technique | Description |
---|---|
Controlled dielectric thickness | The thickness of the dielectric material between the signal trace and the ground plane is controlled to achieve the desired impedance. |
Controlled trace width and spacing | The width and spacing of the signal traces are controlled to achieve the desired impedance. |
Controlled copper thickness | The thickness of the copper on the signal traces and ground planes is controlled to achieve the desired impedance. |
Use of ground planes and power planes | Ground planes and power planes are used to provide a stable reference for the signal traces and to reduce crosstalk and EMI. |
7. Solder Mask and Silkscreen
Solder mask and silkscreen are two important PCB fabrication techniques that are used to protect the PCB and provide visual identification of components and other features. Solder mask is a layer of polymer material that is applied over the copper traces on the PCB to prevent solder bridging and to protect the copper from oxidation and other environmental factors. Silkscreen is a layer of ink that is applied over the solder mask to provide visual identification of components, test points, and other features.
Technique | Purpose |
---|---|
Solder Mask | Protects copper traces from solder bridging and oxidation |
Silkscreen | Provides visual identification of components and other features |
8. Via Filling and Capping
Via filling and capping are PCB fabrication techniques that are used to improve the reliability and performance of PCBs. Vias are holes that are drilled through the PCB to provide electrical connections between layers. Via filling involves filling the vias with a conductive material, such as copper or silver epoxy, to improve the electrical and thermal conductivity of the via. Via capping involves covering the via with a layer of copper to prevent the via from being exposed to the environment and to improve the mechanical strength of the via.
Technique | Purpose |
---|---|
Via Filling | Improves electrical and thermal conductivity of vias |
Via Capping | Prevents vias from being exposed to the environment and improves mechanical strength |
9. Copper Thieving
Copper thieving is a PCB fabrication technique that is used to improve the uniformity of the copper plating on the PCB. Copper thieving involves adding additional copper to areas of the PCB that are not covered by traces or components. This additional copper helps to balance the current density across the PCB during the plating process, resulting in a more uniform copper thickness.
10. Automated Optical Inspection (AOI)
Automated Optical Inspection (AOI) is a PCB fabrication technique that is used to inspect the PCB for defects and errors. AOI involves using a camera and image processing software to inspect the PCB for issues such as missing components, solder bridges, and incorrect component placement. AOI is an important quality control step in PCB fabrication, as it helps to identify defects early in the manufacturing process, reducing the risk of costly rework and scrap.
Frequently Asked Questions (FAQ)
1. What is the difference between SMT and through-hole technology?
SMT involves mounting components directly onto the surface of the PCB, while through-hole technology involves inserting component leads through holes drilled in the PCB and soldering them on the opposite side. SMT has several advantages over through-hole technology, including smaller component size, higher component density, faster assembly times, and lower manufacturing costs.
2. What are the advantages of multilayer PCBs?
Multilayer PCBs have several advantages over single-layer PCBs, including higher component density, improved signal integrity, reduced electromagnetic interference (EMI), and better heat dissipation. Multilayer PCBs are used in applications that require high component density and complex circuitry.
3. What is impedance control and why is it important?
Impedance control is a PCB fabrication technique that involves controlling the impedance of the PCB traces to ensure proper signal integrity. Impedance control is essential in high-speed applications, such as in telecommunications and networking equipment, to prevent signal reflections and distortions that can cause errors and malfunctions.
4. What is the purpose of solder mask and silkscreen?
Solder mask is a layer of polymer material that is applied over the copper traces on the PCB to prevent solder bridging and to protect the copper from oxidation and other environmental factors. Silkscreen is a layer of ink that is applied over the solder mask to provide visual identification of components, test points, and other features.
5. What is Automated Optical Inspection (AOI) and why is it important?
Automated Optical Inspection (AOI) is a PCB fabrication technique that is used to inspect the PCB for defects and errors. AOI is an important quality control step in PCB fabrication, as it helps to identify defects early in the manufacturing process, reducing the risk of costly rework and scrap. AOI involves using a camera and image processing software to inspect the PCB for issues such as missing components, solder bridges, and incorrect component placement.
Conclusion
In conclusion, PCB fabrication is a complex process that involves several techniques to create a functional and reliable circuit board. The 10 must-know PCB fabrication techniques discussed in this article are essential for creating high-quality PCBs that meet the ever-increasing demands of the electronics industry. From SMT and through-hole technology to multilayer and flexible PCBs, each technique has its own advantages and disadvantages, and the choice of technique depends on the specific application and requirements of the PCB. By understanding these techniques and their applications, PCB designers and manufacturers can create PCBs that are reliable, efficient, and cost-effective.
0 Comments