Introduction to PCB Fabrication
Printed Circuit Board (PCB) fabrication is a complex process that involves multiple steps and requires specialized equipment. PCB fabrication equipment plays a crucial role in ensuring the quality, reliability, and consistency of the final product. RAYMING, a leading provider of PCB fabrication solutions, offers a wide range of audited PCB fabrication equipment to meet the diverse needs of the industry.
PCB Fabrication Process Overview
The PCB fabrication process can be divided into several key stages:
- PCB Design and Layout
- PCB Material Selection
- PCB etching and Drilling
- PCB Lamination
- PCB Solder Mask Application
- PCB Surface Finish
- PCB Electrical Testing
- PCB Packaging and Shipping
Each stage requires specific equipment and expertise to ensure the highest quality standards are met.
RAYMING’s Audited PCB Fabrication Equipment
RAYMING offers a comprehensive range of audited PCB fabrication equipment, ensuring that every stage of the PCB fabrication process is optimized for quality and efficiency. Some of the key equipment categories include:
PCB Etching Equipment
PCB etching is a critical step in the fabrication process, as it creates the conductive traces on the PCB surface. RAYMING’s audited PCB etching equipment includes:
- Conveyorized Spray Etchers
- Horizontal Spray Etchers
- Vertical Spray Etchers
- Bubble Etch Machines
These etching machines are designed to handle a variety of PCB materials and offer precise control over the etching process, ensuring consistent results.
PCB Drilling Equipment
Drilling is another essential step in PCB fabrication, as it creates the holes for component placement and interconnections. RAYMING’s audited PCB drilling equipment includes:
- CNC Drilling Machines
- Laser Drilling Machines
- Mechanical Drilling Machines
These drilling machines offer high precision and speed, enabling the fabrication of complex PCB designs with ease.
PCB Lamination Equipment
PCB lamination involves bonding multiple layers of PCB material together to create a multilayer PCB. RAYMING’s audited PCB lamination equipment includes:
- Hydraulic Lamination Presses
- Vacuum Lamination Presses
- Hot Roll Laminators
These lamination machines ensure proper bonding and alignment of the PCB layers, resulting in a high-quality final product.
PCB Solder Mask Application Equipment
Solder mask is a protective coating applied to the PCB surface to prevent oxidation and improve solderability. RAYMING’s audited PCB solder mask application equipment includes:
- Screen Printing Machines
- Spray Coating Machines
- Curtain Coating Machines
These machines offer precise control over the solder mask application process, ensuring a uniform and reliable coating.
PCB Surface Finish Equipment
PCB surface finish is applied to the exposed copper surfaces to improve solderability and protect against corrosion. RAYMING’s audited PCB surface finish equipment includes:
- HASL (Hot Air Solder Leveling) Machines
- ENIG (Electroless Nickel Immersion Gold) Lines
- OSP (Organic Solderability Preservative) Coating Machines
These machines offer a range of surface finish options to meet the specific requirements of different PCB applications.
PCB Electrical Testing Equipment
Electrical testing is a critical step in ensuring the functionality and reliability of the fabricated PCBs. RAYMING’s audited PCB electrical testing equipment includes:
- Flying Probe Testers
- In-Circuit Testers
- Functional Testers
These testing machines offer comprehensive testing capabilities, enabling the detection and isolation of potential defects before the PCBs are shipped to the customer.
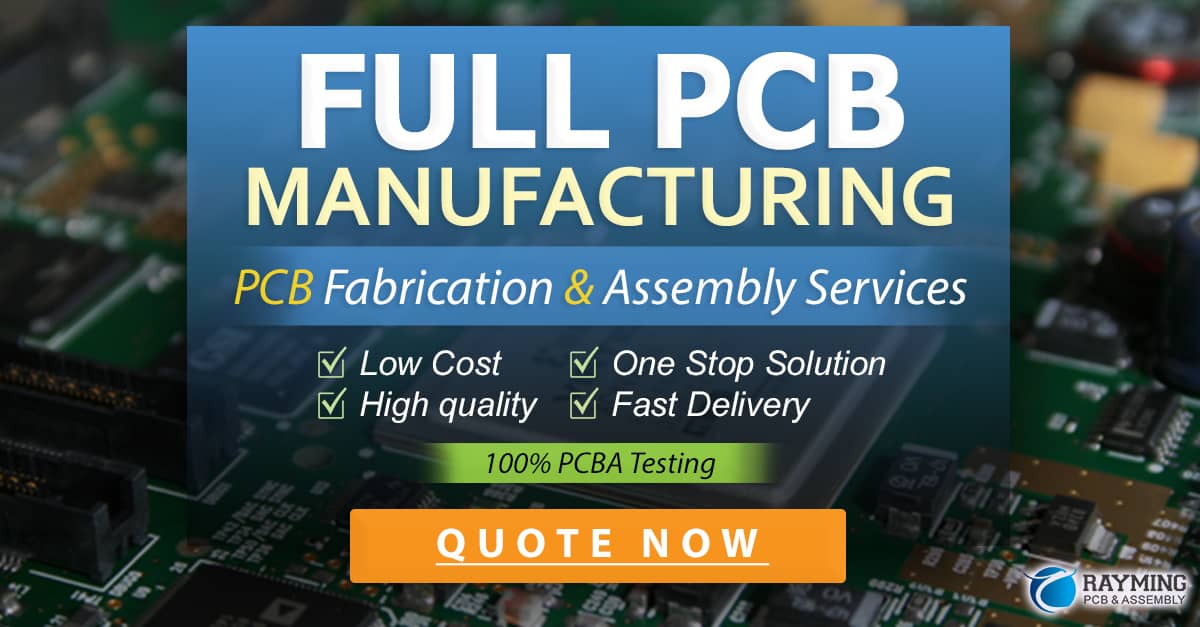
Benefits of RAYMING’s Audited PCB Fabrication Equipment
By using RAYMING’s audited PCB fabrication equipment, manufacturers can enjoy several key benefits:
-
Improved PCB Quality: RAYMING’s equipment is designed to meet the highest quality standards, ensuring consistent and reliable PCB fabrication results.
-
Increased Efficiency: With advanced features and automation capabilities, RAYMING’s equipment enables faster and more efficient PCB fabrication processes.
-
Reduced Manufacturing Costs: By minimizing defects and increasing yields, RAYMING’s equipment helps manufacturers reduce overall manufacturing costs.
-
Enhanced Flexibility: RAYMING’s wide range of equipment options allows manufacturers to handle a variety of PCB designs and materials, offering greater flexibility in their operations.
-
Reliable Support and Service: RAYMING provides comprehensive support and service for its equipment, ensuring that manufacturers can maintain optimal performance and minimize downtime.
PCB Fabrication Equipment Comparison
Equipment Category | Key Features | Benefits |
---|---|---|
PCB Etching Equipment | Precise control, consistent results | Improved trace quality, higher yields |
PCB Drilling Equipment | High precision, fast drilling speeds | Accurate hole placement, faster production |
PCB Lamination Equipment | Proper bonding and alignment | High-quality multilayer PCBs |
PCB Solder Mask Application Equipment | Uniform and reliable coating | Enhanced PCB protection and solderability |
PCB Surface Finish Equipment | Various surface finish options | Improved solderability and corrosion resistance |
PCB Electrical Testing Equipment | Comprehensive testing capabilities | Defect detection and isolation, improved reliability |
Frequently Asked Questions (FAQ)
-
Q: What sets RAYMING’s PCB fabrication equipment apart from other suppliers?
A: RAYMING’s PCB fabrication equipment is audited to ensure the highest quality standards and offers advanced features and automation capabilities for improved efficiency and consistency. -
Q: Can RAYMING’s equipment handle a wide range of PCB materials and designs?
A: Yes, RAYMING offers a wide range of equipment options to accommodate various PCB materials and designs, providing manufacturers with greater flexibility in their operations. -
Q: How does RAYMING’s equipment help reduce manufacturing costs?
A: By minimizing defects and increasing yields, RAYMING’s equipment helps manufacturers reduce overall manufacturing costs, resulting in improved profitability. -
Q: What kind of support and service does RAYMING provide for its equipment?
A: RAYMING provides comprehensive support and service for its equipment, including installation, training, maintenance, and troubleshooting, ensuring optimal performance and minimal downtime. -
Q: Can RAYMING’s PCB electrical testing equipment detect and isolate potential defects?
A: Yes, RAYMING’s PCB electrical testing equipment, such as flying probe testers, in-circuit testers, and functional testers, offers comprehensive testing capabilities to detect and isolate potential defects before the PCBs are shipped to the customer.
Conclusion
RAYMING’s audited PCB fabrication equipment is designed to meet the demanding requirements of the PCB industry, offering a wide range of solutions for every stage of the fabrication process. By investing in RAYMING’s equipment, manufacturers can improve PCB quality, increase efficiency, reduce manufacturing costs, and enhance their overall competitiveness in the market. With comprehensive support and service, RAYMING ensures that its customers can achieve optimal results and succeed in their PCB fabrication endeavors.
0 Comments