What is PCB Solder Mask?
Solder mask, also known as solder resist or solder stop, is a thin layer of polymer applied to the copper traces of a PCB. This coating serves multiple purposes, including protecting the copper from oxidation, preventing solder bridges during the assembly process, and providing electrical insulation between adjacent traces.
Composition of Solder Mask
Solder mask is typically composed of a photosensitive polymer, which can be selectively exposed and developed to create openings for component pads and other features. The most common types of solder mask include:
- Liquid Photoimageable Solder Mask (LPSM)
- Dry Film Photoimageable Solder Mask (DFSM)
Both types of solder mask are applied to the PCB surface and then exposed to UV light through a photomask, which defines the areas where the solder mask should remain.
Functions of Solder Mask in PCB
1. Protection from Oxidation
One of the primary functions of solder mask is to protect the copper traces on the PCB from oxidation. When exposed to air, copper can quickly oxidize, forming a layer of copper oxide that can hinder the soldering process and affect the electrical conductivity of the traces. By covering the copper with solder mask, the PCB is protected from oxidation, ensuring better solderability and long-term reliability.
2. Electrical Insulation
Solder mask provides electrical insulation between adjacent copper traces, preventing short circuits and ensuring proper signal integrity. The insulating properties of solder mask help to maintain the desired electrical characteristics of the PCB, such as impedance and crosstalk reduction.
3. Solder Bridge Prevention
During the soldering process, there is a risk of solder bridging, where solder inadvertently connects two adjacent pads or traces. Solder mask helps to prevent this issue by acting as a barrier between the pads and traces, confining the solder to the desired areas. This is particularly important in high-density PCB designs, where the spacing between components is minimal.
4. Improved Aesthetics
In addition to its functional benefits, solder mask also enhances the visual appearance of the PCB. Solder mask is available in various colors, with green being the most common. The uniform color of the solder mask provides a clean and professional look to the PCB, making it easier to identify components and traces.
5. Marking and Labeling
Solder mask can also be used for marking and labeling purposes on the PCB. Text, logos, and other markings can be selectively exposed on the solder mask to provide information such as component designators, polarity indicators, and company branding. This aids in the assembly process and makes it easier to troubleshoot and repair the PCB if needed.
Solder Mask Application Process
The application of solder mask to a PCB involves several steps:
-
Surface Preparation: The PCB surface is cleaned to remove any contaminants that may affect the adhesion of the solder mask.
-
Solder Mask Application: The liquid or dry film solder mask is applied to the PCB surface using techniques such as screen printing, curtain coating, or roller coating.
-
Exposure: The solder mask is exposed to UV light through a photomask, which defines the areas where the mask should remain.
-
Developing: The unexposed portions of the solder mask are removed using a developing solution, revealing the copper pads and traces.
-
Curing: The solder mask is cured using heat or UV light to fully polymerize and harden the coating.
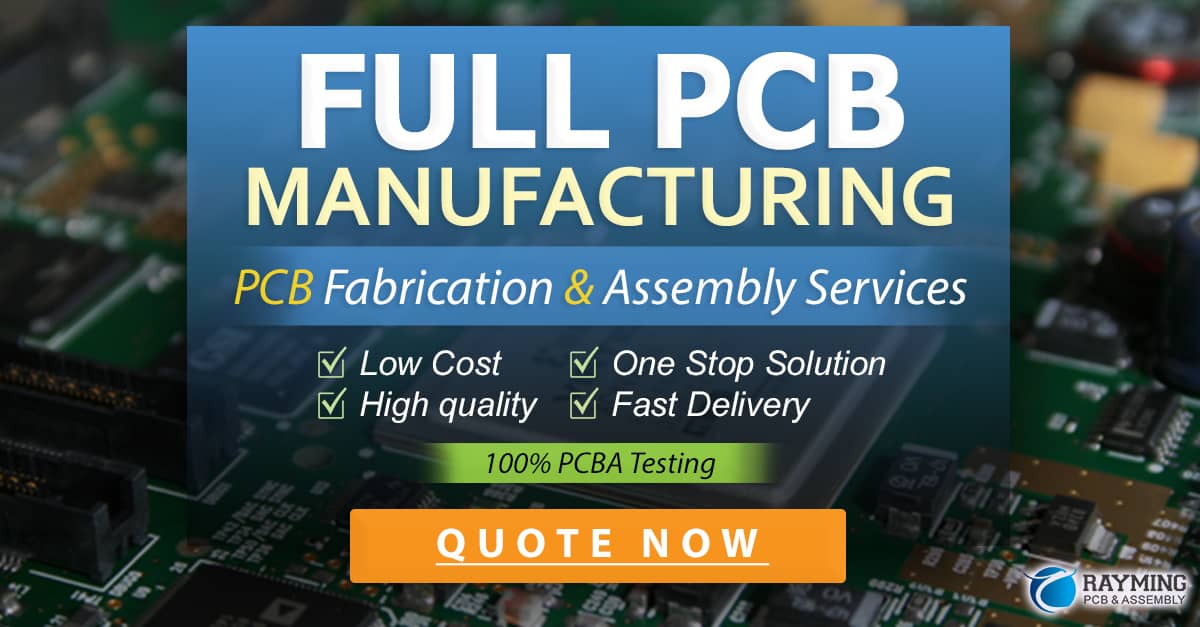
Solder Mask Design Considerations
When designing a PCB, several factors should be considered to ensure the proper application and functionality of the solder mask:
Solder Mask Clearance
Solder mask clearance refers to the distance between the edge of a component pad and the solder mask opening. Adequate clearance is necessary to ensure proper soldering and prevent solder mask from encroaching on the pad. The clearance requirements may vary depending on the PCB fabrication capabilities and the specific component requirements.
Solder Mask Thickness
The thickness of the solder mask can impact its performance and durability. A thicker solder mask provides better insulation and protection but may affect the fine-pitch component placement. Conversely, a thinner solder mask allows for higher-density component placement but may be more susceptible to damage. The optimal solder mask thickness should be determined based on the specific requirements of the PCB design.
Solder Mask Color
While green is the most common color for solder mask, other colors such as red, blue, yellow, and black are also available. The choice of solder mask color is primarily an aesthetic decision but can also serve functional purposes. For example, white solder mask can be used to enhance the visibility of silk-screened markings, while black solder mask can provide better contrast for automated optical inspection (AOI) systems.
Advantages of Using Solder Mask in PCB
The use of solder mask in PCB offers several advantages:
-
Improved Reliability: By protecting the copper traces from oxidation and providing electrical insulation, solder mask enhances the long-term reliability of the PCB.
-
Better Solderability: Solder mask prevents solder bridging and ensures that solder is confined to the desired areas, resulting in better solderability and fewer assembly defects.
-
Enhanced Signal Integrity: The insulating properties of solder mask help to maintain the desired electrical characteristics of the PCB, such as impedance and crosstalk reduction.
-
Increased Durability: Solder mask provides a protective layer that shields the PCB from environmental factors such as moisture, dust, and minor abrasions.
-
Improved Aesthetics: The uniform color and appearance of solder mask give the PCB a professional and clean look.
Challenges and Limitations of Solder Mask
While solder mask offers numerous benefits, there are also some challenges and limitations to consider:
-
Solder Mask Adhesion: Ensuring proper adhesion of the solder mask to the PCB surface can be challenging, particularly in areas with high component density or irregular surfaces.
-
Fine-Pitch Components: As component sizes continue to shrink, the solder mask clearance requirements become more stringent, making it difficult to achieve reliable solder mask coverage in high-density PCB designs.
-
Solder Mask Compatibility: Some components or surface finishes may not be compatible with certain types of solder mask, requiring careful selection of materials and processes.
-
Rework and Repair: When rework or repair is necessary, removing the solder mask to access the underlying copper can be difficult and may cause damage to the PCB.
Future Trends in PCB Solder Mask
As the electronics industry continues to evolve, new trends and technologies are emerging in the field of PCB solder mask:
-
Inkjet Solder Mask: Inkjet printing technology is being explored as a means to selectively apply solder mask, enabling finer resolution and more precise control over the solder mask coverage.
-
High-Temperature Solder Mask: With the increasing use of lead-free solders, which have higher melting points, there is a growing demand for solder masks that can withstand higher temperatures during the assembly process.
-
Environmentally Friendly Solder Mask: There is a trend towards the development of more environmentally friendly solder mask materials, such as halogen-free and biodegradable options, to reduce the environmental impact of PCB manufacturing.
Frequently Asked Questions (FAQ)
-
What is the purpose of solder mask in PCB?
Solder mask serves multiple purposes in PCB, including protecting the copper traces from oxidation, providing electrical insulation between adjacent traces, preventing solder bridges during assembly, and enhancing the visual appearance of the PCB. -
What are the most common types of solder mask?
The two most common types of solder mask are Liquid Photoimageable Solder Mask (LPSM) and Dry Film Photoimageable Solder Mask (DFSM). Both types are applied to the PCB surface and then exposed to UV light through a photomask to define the areas where the mask should remain. -
How does solder mask improve the reliability of a PCB?
Solder mask improves the reliability of a PCB by protecting the copper traces from oxidation, providing electrical insulation, and preventing solder bridging. These factors contribute to better solderability, signal integrity, and long-term durability of the PCB. -
What factors should be considered when designing solder mask for a PCB?
When designing solder mask for a PCB, factors such as solder mask clearance, thickness, and color should be considered. Adequate clearance is necessary for proper soldering, while the thickness and color can impact the performance, durability, and aesthetic appearance of the PCB. -
Are there any challenges or limitations associated with using solder mask in PCB?
Some challenges and limitations associated with solder mask include ensuring proper adhesion to the PCB surface, accommodating fine-pitch components, compatibility with certain materials and processes, and difficulties in rework and repair.
Conclusion
Solder mask plays a crucial role in the functioning and reliability of PCBs. By protecting the copper traces from oxidation, providing electrical insulation, preventing solder bridging, and enhancing the visual appearance of the PCB, solder mask ensures the proper operation and longevity of electronic devices.
When designing and manufacturing PCBs, careful consideration should be given to the selection and application of solder mask, taking into account factors such as clearance, thickness, and color. As the electronics industry continues to advance, new trends and technologies in solder mask are emerging to address the evolving needs of PCB manufacturing.
By understanding the functions, advantages, and challenges associated with solder mask, PCB designers and manufacturers can make informed decisions to optimize the performance and reliability of their products.
Parameter | Description |
---|---|
Solder Mask Type | Liquid Photoimageable (LPSM) or Dry Film Photoimageable (DFSM) |
Solder Mask Color | Green (most common), red, blue, yellow, black |
Solder Mask Thickness | Varies based on PCB design requirements and fabrication capabilities |
Solder Mask Clearance | Distance between component pad edge and solder mask opening |
Solder Mask Application Methods | Screen printing, curtain coating, roller coating |
Solder Mask Curing Methods | Heat curing or UV curing |
Table 1: Key parameters and characteristics of solder mask in PCB manufacturing.
0 Comments