What is PCB Solder Mask?
PCB solder mask, also known as solder resist or solder stop mask, is a thin layer of polymer applied to the copper traces of a printed circuit board (PCB). Its primary purpose is to protect the copper traces from oxidation, prevent solder bridges from forming between closely spaced pads, and provide electrical insulation. Solder mask also helps to improve the overall durability and reliability of the PCB.
Benefits of Using PCB Solder Mask
- Protection against oxidation and corrosion
- Prevention of solder bridges
- Electrical insulation
- Improved durability and reliability
- Enhanced aesthetics and readability
The 4 Main Types of PCB Solder Mask
There are four main types of PCB solder mask, each with its own unique properties and applications:
- Liquid Photoimageable Solder Mask (LPISM)
- Dry Film Photoimageable Solder Mask (DFISM)
- Liquid Photoimageable Solder Mask (LPI)
- Epoxy Liquid Solder Mask
1. Liquid Photoimageable Solder Mask (LPISM)
LPISM is the most common type of solder mask used in the PCB industry. It is a liquid-based photopolymer that is applied to the PCB surface using screen printing or spraying techniques. After application, the solder mask is exposed to UV light through a photographic film, which hardens the exposed areas while leaving the unexposed areas soft. The soft areas are then removed using a developer solution, revealing the desired solder mask pattern.
Advantages of LPISM
- High resolution and accuracy
- Excellent adhesion to the PCB surface
- Good electrical insulation properties
- Wide range of available colors
- Cost-effective for large-scale production
Disadvantages of LPISM
- Requires specialized equipment for application and development
- Longer processing time compared to other methods
- May require multiple coats for optimal coverage
2. Dry Film Photoimageable Solder Mask (DFISM)
DFISM is a solid photopolymer film that is laminated onto the PCB surface using heat and pressure. Like LPISM, it is exposed to UV light through a photographic film and developed to reveal the desired solder mask pattern. DFISM is known for its excellent thickness control and uniformity, making it ideal for high-density PCB designs.
Advantages of DFISM
- Excellent thickness control and uniformity
- High resolution and accuracy
- Good electrical insulation properties
- Faster processing time compared to LPISM
- Ideal for high-density PCB designs
Disadvantages of DFISM
- Higher material cost compared to LPISM
- Limited color options
- May require specialized lamination equipment
3. Liquid Photoimageable Solder Mask (LPI)
LPI is a newer type of solder mask that combines the benefits of LPISM and DFISM. It is a liquid photopolymer that is applied to the PCB surface using curtain coating or spraying techniques. LPI offers excellent thickness control, high resolution, and fast processing times, making it an increasingly popular choice for PCB manufacturers.
Advantages of LPI
- Excellent thickness control and uniformity
- High resolution and accuracy
- Good electrical insulation properties
- Fast processing time
- Wide range of available colors
Disadvantages of LPI
- Higher material cost compared to LPISM
- Requires specialized coating equipment
- May require multiple coats for optimal coverage
4. Epoxy Liquid Solder Mask
Epoxy liquid solder mask is a two-part epoxy-based coating that is applied to the PCB surface using screen printing or spraying techniques. It offers excellent chemical and heat resistance, making it ideal for harsh environmental conditions. However, epoxy liquid solder mask has lower resolution and accuracy compared to photoimageable solder masks.
Advantages of Epoxy Liquid Solder Mask
- Excellent chemical and heat resistance
- Good electrical insulation properties
- Cost-effective for small-scale production
- Ideal for harsh environmental conditions
Disadvantages of Epoxy Liquid Solder Mask
- Lower resolution and accuracy compared to photoimageable solder masks
- Limited color options
- Longer curing time compared to other methods
- May require multiple coats for optimal coverage
Comparison Table
Solder Mask Type | Resolution | Thickness Control | Processing Time | Material Cost | Ideal Applications |
---|---|---|---|---|---|
LPISM | High | Good | Longer | Low | Large-scale production |
DFISM | High | Excellent | Faster | High | High-density PCB designs |
LPI | High | Excellent | Fast | High | High-density PCB designs |
Epoxy Liquid | Low | Good | Longer | Low | Harsh environmental conditions |
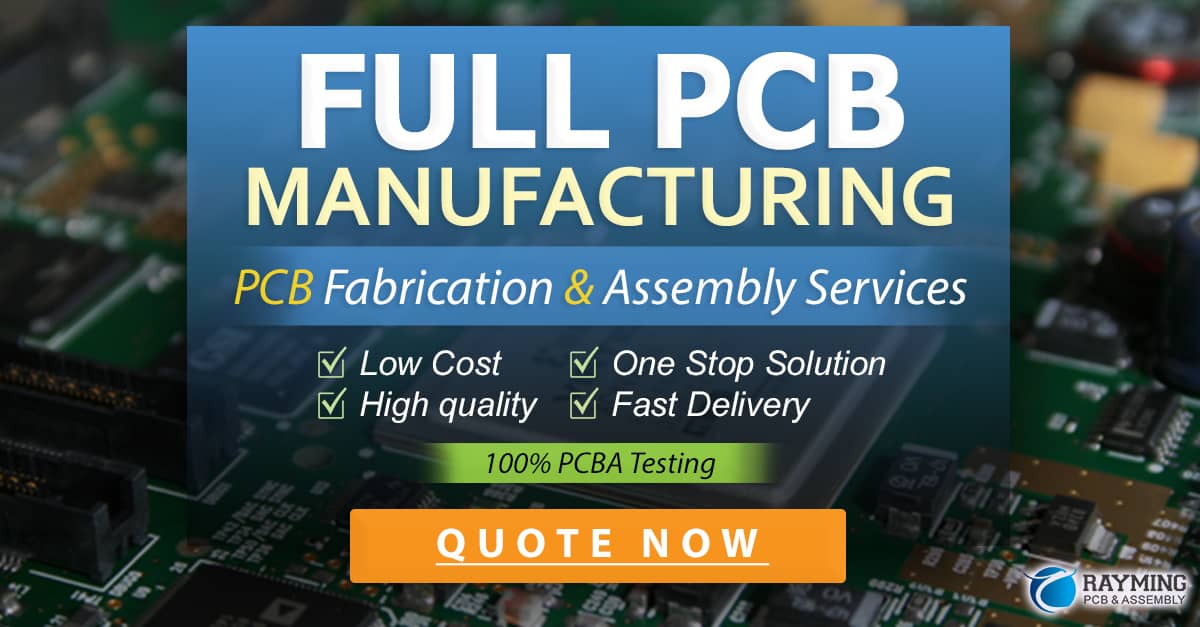
Choosing the Right PCB Solder Mask
When selecting the appropriate PCB solder mask for your project, consider the following factors:
- PCB design complexity and density
- Required resolution and accuracy
- Environmental conditions and durability requirements
- Production scale and budget
- Available equipment and resources
By carefully evaluating these factors and understanding the unique properties of each solder mask type, you can make an informed decision that best suits your PCB manufacturing needs.
Frequently Asked Questions (FAQ)
1. What is the purpose of PCB solder mask?
PCB solder mask serves several purposes, including protecting copper traces from oxidation, preventing solder bridges from forming between closely spaced pads, providing electrical insulation, and improving the overall durability and reliability of the PCB.
2. What is the difference between LPISM and DFISM?
LPISM is a liquid-based photopolymer that is applied to the PCB surface using screen printing or spraying techniques, while DFISM is a solid photopolymer film that is laminated onto the PCB surface using heat and pressure. DFISM offers better thickness control and uniformity compared to LPISM, but has higher material costs and limited color options.
3. What are the advantages of LPI solder mask?
LPI solder mask offers excellent thickness control, high resolution, fast processing times, and a wide range of available colors. It combines the benefits of both LPISM and DFISM, making it an increasingly popular choice for PCB manufacturers.
4. When should I use epoxy liquid solder mask?
Epoxy liquid solder mask is ideal for PCBs that will be exposed to harsh environmental conditions, as it offers excellent chemical and heat resistance. It is also cost-effective for small-scale production runs. However, it has lower resolution and accuracy compared to photoimageable solder masks.
5. How do I choose the right PCB solder mask for my project?
When choosing the right PCB solder mask, consider factors such as PCB design complexity and density, required resolution and accuracy, environmental conditions and durability requirements, production scale and budget, and available equipment and resources. By carefully evaluating these factors and understanding the unique properties of each solder mask type, you can make an informed decision that best suits your PCB manufacturing needs.
Conclusion
PCB solder mask is a critical component in the manufacturing of printed circuit boards, providing protection, insulation, and improved durability. Understanding the four main types of PCB solder mask – LPISM, DFISM, LPI, and epoxy liquid – and their unique properties, advantages, and disadvantages is essential for selecting the most appropriate solder mask for your project. By carefully considering factors such as PCB design complexity, required resolution and accuracy, environmental conditions, production scale, and budget, you can ensure that your PCB manufacturing process is optimized for success.
0 Comments