Introduction to PCB Assembly
Printed circuit board (PCB) assembly is the process of soldering electronic components onto a PCB to create a functional electronic device. PCB assembly can be done at various volumes, from prototypes and small batches to high-volume production. This guide will focus specifically on the low volume PCB assembly process.
Low volume PCB assembly refers to the production of a small number of PCBs, typically ranging from 1 to a few hundred units. This type of assembly is commonly used for prototypes, testing, and small production runs. The low volume PCB assembly process differs from high-volume production in terms of the equipment, techniques, and costs involved.
Advantages of Low Volume PCB Assembly
- Faster turnaround times
- Lower initial costs
- Flexibility to make design changes
- Ability to test and validate designs before scaling up production
Applications of Low Volume PCB Assembly
- Prototyping and testing new designs
- Small batch production for niche markets
- Research and development projects
- Custom or specialized electronic devices
Steps in the Low Volume PCB Assembly Process
The low volume PCB assembly process can be broken down into several key steps:
- PCB Design and Fabrication
- Component Sourcing and Preparation
- Solder Paste Application
- Component Placement
- Soldering
- Inspection and Testing
- Finishing and Packaging
Let’s explore each of these steps in more detail.
1. PCB Design and Fabrication
The first step in the PCB assembly process is designing the PCB and having it fabricated. This involves creating a schematic diagram and layout of the PCB using specialized software such as Altium Designer, Eagle, or KiCad.
The PCB design should take into account factors such as:
- Component selection and placement
- Signal integrity and electromagnetic compatibility
- Thermal management
- Manufacturing constraints and design for manufacturability
Once the PCB design is finalized, the fabrication process begins. This typically involves the following sub-steps:
- Printing the circuit pattern onto a copper-clad board using photoresist
- Etching away the unwanted copper to leave the desired circuit traces
- Drilling holes for through-hole components and vias
- Applying solder mask and silkscreen layers
2. Component Sourcing and Preparation
The next step is to source the electronic components needed for the PCB assembly. This may involve purchasing components from distributors or directly from manufacturers.
When sourcing components for low volume PCB assembly, it’s important to consider:
- Component availability and lead times
- Minimum order quantities and price breaks
- Alternative or substitute parts in case of supply chain issues
Once the components are received, they need to be prepared for assembly. This may involve:
- Visual inspection for damage or defects
- Arranging components into kits for each PCB
- Programming microcontrollers or other programmable devices
- Forming and cutting component leads to the appropriate length
- Applying adhesive or epoxy to secure components during soldering
3. Solder Paste Application
Solder paste is a mixture of tiny solder balls suspended in flux. It is applied to the PCB pads where surface mount components will be placed. The most common methods of solder paste application for low volume PCB assembly are stencil printing and dispensing.
Stencil Printing
Stencil printing involves using a laser-cut stainless steel stencil with openings that match the PCB pads. The stencil is aligned with the PCB and solder paste is spread across the stencil surface with a squeegee blade, forcing it through the openings and onto the pads.
Advantages of stencil printing:
- Fast and efficient for larger batches
- Consistent solder paste deposits
- Can be automated with a stencil printer
Disadvantages of stencil printing:
- Higher initial cost for stencil fabrication
- Requires careful stencil design and alignment
- May require stencil cleaning between prints
Dispensing
Dispensing involves using a pneumatic or positive displacement syringe to apply solder paste directly onto the PCB pads. This can be done manually or with an automated dispensing machine.
Advantages of dispensing:
- Lower initial cost compared to stencil printing
- Flexibility to make changes or corrections on the fly
- Suitable for low volume and prototype work
Disadvantages of dispensing:
- Slower than stencil printing for larger batches
- Requires operator skill for consistent results
- May require frequent syringe changeovers and cleaning
Method | Pros | Cons |
---|---|---|
Stencil Printing | Fast, consistent, can be automated | Higher initial cost, requires stencil design and alignment |
Dispensing | Lower initial cost, flexible | Slower for larger batches, requires operator skill |
4. Component Placement
After the solder paste is applied, the next step is to place the components onto the PCB. For low volume PCB assembly, this is typically done manually using tweezers or a vacuum pickup tool.
The component placement process involves:
- Aligning the component with the PCB pads
- Pressing the component into the solder paste
- Checking for proper orientation and polarity
- Repeating for all components on the PCB
Some tips for successful component placement:
- Use a lighted magnifying lens or microscope for visual inspection
- Handle components carefully to avoid bending leads or damaging parts
- Double-check polarity and orientation before soldering
- Work from the inside of the PCB outward to avoid disrupting placed parts
For larger batches or more complex PCBs, an automated pick-and-place machine may be used to speed up the component placement process. However, this requires a significant upfront investment and is not always practical for low volume assembly.
5. Soldering
Once all the components are placed, the PCB is ready to be soldered. The most common Soldering Methods for low volume PCB assembly are reflow soldering and hand soldering.
Reflow Soldering
Reflow soldering involves running the PCB through an oven that heats the solder paste to its melting point, allowing it to form a permanent bond between the components and pads. The reflow process typically follows a temperature profile with several stages:
- Preheat: The PCB is gradually heated to activate the flux and evaporate solvents
- Soak: The temperature is held steady to allow all parts of the PCB to reach an even temperature
- Reflow: The temperature is raised above the solder melting point, causing the solder to liquefy and form a bond
- Cooldown: The PCB is cooled at a controlled rate to allow the solder joints to solidify
Advantages of reflow soldering:
- Consistent and reliable solder joints
- Can handle high component density and fine-pitch parts
- Suitable for lead-free and RoHS-compliant soldering
Disadvantages of reflow soldering:
- Requires specialized equipment (reflow oven)
- Consumes more energy compared to hand soldering
- Some components may be sensitive to high temperatures
Hand Soldering
Hand soldering, also known as manual soldering, involves using a soldering iron to melt solder wire and form a joint between the component lead and PCB pad. This method is often used for through-hole components, large components that are difficult to reflow, or rework and repair.
To hand solder a component:
- Apply flux to the component lead and PCB pad to help the solder flow and form a strong bond
- Place the soldering iron tip against the lead and pad simultaneously
- Feed solder wire into the joint and allow it to melt and flow around the lead and pad
- Remove the solder wire and iron and let the joint cool and solidify
Some tips for successful hand soldering:
- Use a temperature-controlled soldering iron with the appropriate tip size and shape
- Keep the tip clean and tinned with solder to ensure good heat transfer
- Work quickly to avoid overheating components or pads
- Use a fume extractor or ventilation to avoid inhaling solder fumes
Method | Pros | Cons |
---|---|---|
Reflow Soldering | Consistent, reliable, handles high density | Requires reflow oven, higher energy consumption |
Hand Soldering | Flexible, suitable for through-hole and rework | Time-consuming, requires operator skill |
6. Inspection and Testing
After soldering, the PCB should be thoroughly inspected and tested to ensure proper assembly and functionality. This step is crucial for catching any defects or issues before the PCB is put into use.
Visual inspection checks for:
- Proper component placement and orientation
- Solder Joint Quality (no bridging, cold joints, or insufficient solder)
- Any damaged or missing components
- Foreign object debris or contamination
Automated optical inspection (AOI) machines can be used to quickly scan the PCB and identify potential defects. However, for low volume assembly, manual visual inspection with a magnifying lens or microscope is often sufficient.
Electrical testing verifies that the PCB functions as intended. This may involve:
- Continuity testing to check for open or short circuits
- Power-on testing to ensure the PCB powers up correctly
- Functional testing to validate that all features and operations work as expected
- Boundary scan testing for more complex digital circuits
If any issues are found during inspection and testing, they should be diagnosed and repaired before proceeding. Common rework techniques include:
- Desoldering and replacing faulty components
- Adding additional solder to insufficient joints
- Using solder wick or a desoldering pump to remove excess solder or bridges
- Cleaning flux residue or contamination from the PCB
7. Finishing and Packaging
The final step in the low volume PCB assembly process is finishing and packaging the PCBs for delivery or use.
Finishing may involve:
- Conformal coating to protect the PCB from moisture, dust, or contaminants
- Potting or encapsulation for harsh environments or to provide strain relief
- Applying labels, serial numbers, or barcodes for identification and traceability
Packaging considerations include:
- Electrostatic discharge (ESD) protection for sensitive components
- Moisture barrier bags or desiccants to prevent corrosion or mold growth
- Cushioning or padding to prevent damage during shipping and handling
- Appropriate box or container size and material
Low Volume PCB Assembly Equipment and Tools
To set up a low volume PCB assembly workflow, you will need some essential equipment and tools. Here are the key items to consider:
- Soldering iron or station with adjustable temperature control
- Tweezers, pliers, and other hand tools for component handling
- Solder wire (leaded or lead-free) and flux
- Solder paste and applicators (stencils or dispensing needles)
- Reflow oven or hot plate for solder paste reflow
- Fume extractor or ventilation system for soldering
- Magnifying lens, microscope, or digital microscope for inspection
- Multimeter and oscilloscope for electrical testing
- ESD-safe workbench, floor mats, and wrist straps
- Cleaning supplies (isopropyl alcohol, brushes, swabs)
Optional equipment for more advanced low volume assembly includes:
- Stencil printer for solder paste application
- Pick-and-place machine for automated component placement
- Automated optical inspection (AOI) machine for defect detection
- Rework station with hot air pencil and desoldering tools
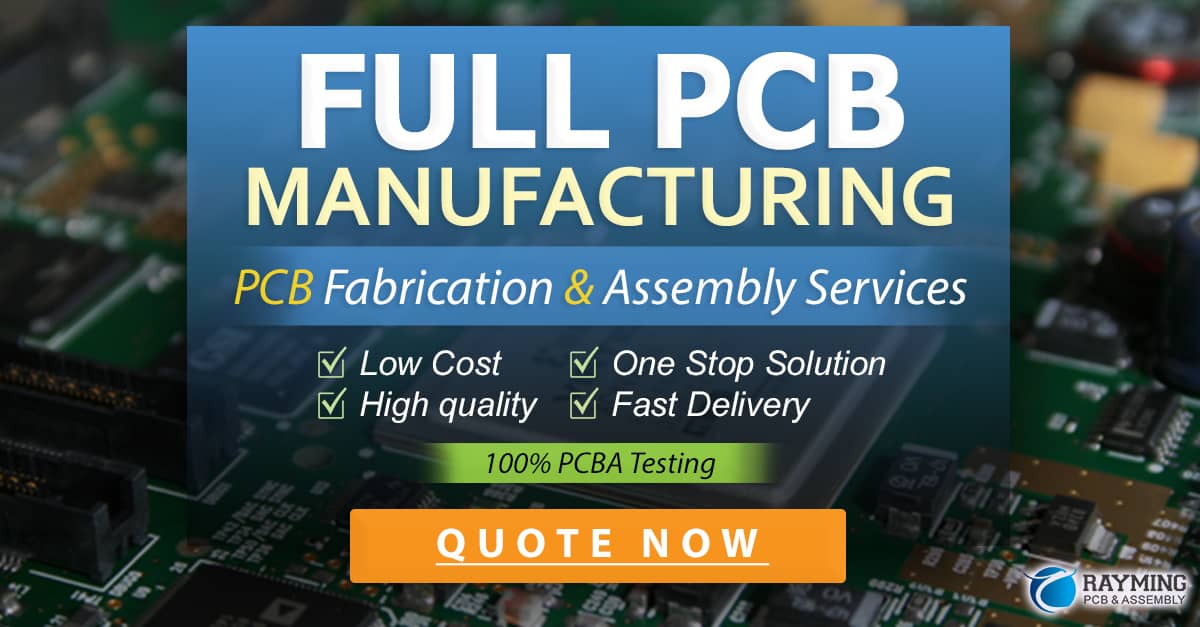
Best Practices for Low Volume PCB Assembly
To ensure successful low volume PCB assembly, follow these best practices:
-
Design for manufacturability: Consider the limitations and capabilities of your assembly process when designing the PCB. Use standard component sizes and pitches, provide adequate spacing between parts, and follow design guidelines for your fabrication vendor.
-
Choose the right components: Select components that are readily available, have a suitable package type for your assembly process, and meet your performance and reliability requirements. Avoid using obsolete or hard-to-find parts.
-
Plan your assembly workflow: Break down the assembly process into clear steps and assign roles and responsibilities. Create a bill of materials (BOM) and assembly instructions to ensure consistency and repeatability.
-
Maintain a clean and organized workspace: Keep your work area free of clutter and contaminants that could damage components or affect solder joint quality. Use ESD-safe storage and handling procedures for sensitive parts.
-
Inspect and test thoroughly: Don’t skip the inspection and testing steps, even for low volume assembly. Catching defects early can save time and money in the long run. Document your testing procedures and acceptance criteria.
-
Continuous improvement: Monitor your process yields and defect rates and look for opportunities to improve your workflow, equipment, or training. Stay up-to-date with industry best practices and new technologies that could benefit your low volume assembly process.
Frequently Asked Questions (FAQ)
1. What is the typical turnaround time for low volume PCB assembly?
Turnaround times for low volume PCB assembly can vary depending on the complexity of the PCB, the availability of components, and the workload of the assembly vendor. In general, simple PCBs with readily available parts can be assembled in a few days to a week, while more complex designs may take several weeks. Rush services may be available for an additional fee.
2. How much does low volume PCB Assembly Cost?
The cost of low volume PCB assembly depends on several factors, including:
- PCB complexity and layer count
- Number of unique components and total part count
- Component types and package sizes
- Quantity of PCBs to be assembled
- Assembly method (hand soldering vs. reflow)
In general, expect to pay a setup fee for stencils, programming, and tooling, plus a per-PCB cost that decreases with larger quantities. For very low volumes (1-10 PCBs), the setup costs may dominate the total price. It’s best to get quotes from several vendors based on your specific PCB design and requirements.
3. Can I use lead-free solder for low volume PCB assembly?
Yes, lead-free solder can be used for low volume PCB assembly, and in fact may be required for certain applications or markets (e.g. RoHS compliance). Lead-free solder typically has a higher melting point than leaded solder, so it may require higher soldering temperatures and longer dwell times. Make sure your components and PCB substrate are rated for Lead-Free Soldering temperatures.
4. How do I choose a low volume PCB assembly vendor?
When selecting a vendor for low volume PCB assembly, consider the following factors:
- Experience and expertise with your type of PCB and components
- Equipment and capabilities (e.g. reflow ovens, pick-and-place machines, AOI)
- Quality control and testing procedures
- Turnaround time and rush service options
- Pricing and minimum order quantities
- Communication and customer support
Look for vendors that specialize in low volume or prototype assembly, as they will be better equipped to handle the unique challenges and requirements compared to high-volume production houses. Get recommendations from colleagues or online forums, and request quotes and samples from multiple vendors before making a decision.
5. Can I do low volume PCB assembly myself?
Yes, it is possible to do low volume PCB assembly in-house if you have the necessary skills, equipment, and facilities. This can be a good option if you need very fast turnaround times, have proprietary or sensitive designs, or want to maintain complete control over the assembly process.
However, setting up an in-house low volume assembly line requires a significant investment in equipment, materials, and training. You will also need to handle all the logistics of component sourcing, inventory management, and quality control. For most companies, outsourcing low volume PCB assembly to a specialized vendor is more cost-effective and efficient than doing it themselves.
Conclusion
Low volume PCB assembly is a critical process for bringing new electronic products to market quickly and efficiently. By understanding the steps involved in the process, from PCB design and component sourcing to soldering, inspection, and testing, you can ensure successful assembly of your prototype or small batch PCBs.
Choosing the right equipment, tools, and vendors for your low volume assembly needs is key to achieving high quality results and fast turnaround times. Following best practices for design, planning, and process control can help you avoid common pitfalls and optimize your workflow.
Whether you choose to outsource your low volume PCB assembly or bring it in-house, staying up-to-date with the latest technologies and industry trends can help you stay competitive in today’s fast-paced electronics landscape. With the right approach and mindset, low volume PCB assembly can be a powerful tool for innovation and growth.
0 Comments