Introduction to Soldering Methods
Soldering is an essential skill for anyone working with electronic components and printed circuit boards (PCBs). Through-hole soldering involves inserting component leads through holes in a PCB and soldering them in place on the opposite side. There are several methods for through-hole soldering, each with its own advantages and disadvantages. In this article, we will explore some of the most common through-hole soldering methods.
Hand Soldering
Hand soldering is the most basic and versatile method for through-hole soldering. It involves using a soldering iron to manually apply solder to the component leads and PCB pads. Hand soldering allows for precise control and is suitable for small-scale projects or repairs.
Tools and Materials Needed
- Soldering iron
- Solder wire (lead-based or lead-free)
- Soldering iron tip cleaner
- Flux (optional)
- Tweezers
- Wire cutters
Procedure
- Set the soldering iron to the appropriate temperature (typically 300-400°C).
- Clean the soldering iron tip using a damp sponge or brass wool.
- Apply a small amount of solder to the tip to promote heat transfer (tinning).
- Insert the component lead through the PCB hole.
- Touch the soldering iron to the component lead and PCB pad simultaneously.
- Apply solder to the joint, allowing it to melt and flow around the lead and pad.
- Remove the soldering iron and let the joint cool.
- Trim any excess lead length using wire cutters.
Wave Soldering
Wave soldering is an automated process used for mass production of through-hole soldered PCBs. The PCB is passed over a molten solder wave, which solders all the components in a single pass. Wave soldering is fast and efficient but requires specialized equipment and is less suitable for small-scale projects.
Equipment and Materials
- Wave soldering machine
- Solder pot with molten solder
- Solder flux
- Conveyor system
- PCB pallet or carrier
Process
- Prepare the PCB by applying solder flux to the component leads and pads.
- Place the PCB on a pallet or carrier, with the components facing down.
- Feed the pallet into the wave soldering machine’s conveyor system.
- The PCB passes over a preheating zone to activate the flux and prevent thermal shock.
- The PCB then passes over the molten solder wave, which solders all the components simultaneously.
- The PCB exits the machine and cools down.
- Clean any excess flux residue from the PCB using an appropriate solvent.
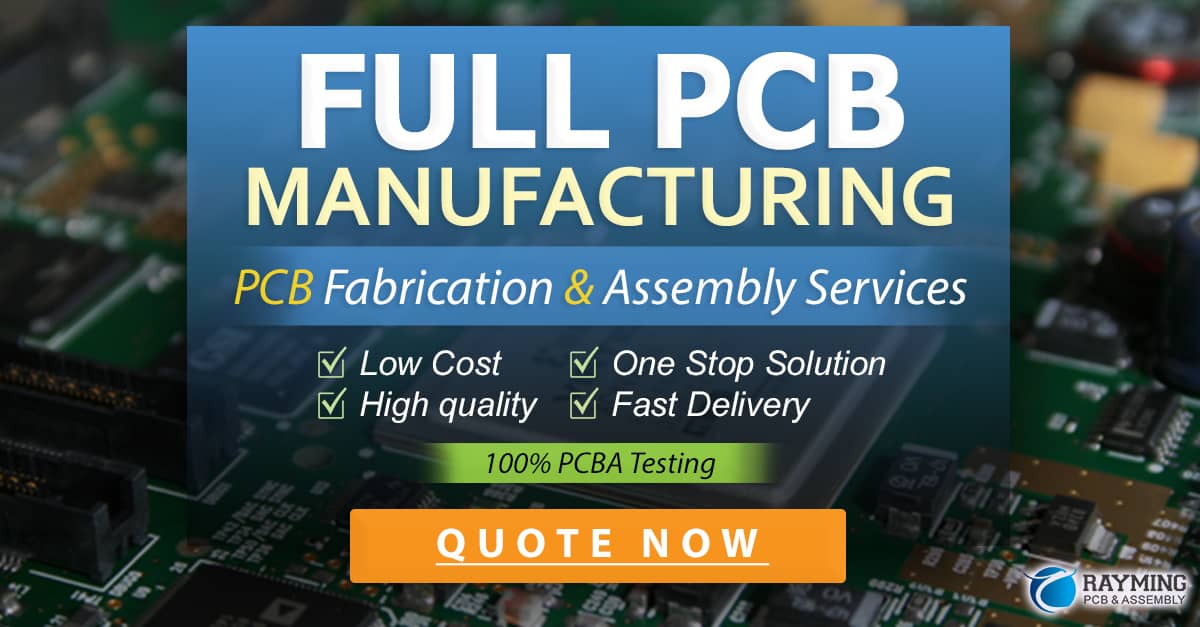
Selective Soldering
Selective soldering is a semi-automated process that combines the precision of hand soldering with the speed of automated soldering. It involves using a programmable soldering machine to solder specific components or areas on a PCB. Selective soldering is useful for PCBs with mixed through-hole and surface-mount components or when certain components are heat-sensitive.
Equipment and Materials
- Selective soldering machine
- Solder wire
- Flux
- PCB fixture or pallet
Process
- Prepare the PCB by applying flux to the component leads and pads.
- Place the PCB in a fixture or pallet designed for the selective soldering machine.
- Program the machine to solder the desired components or areas.
- The machine applies solder to the specified locations using a miniature solder wave or solder jet.
- The PCB is removed from the machine and allowed to cool.
- Clean any excess flux residue from the PCB.
Reflow Soldering
Reflow soldering is primarily used for surface-mount components but can also be used for some through-hole components. In this method, solder paste (a mixture of solder powder and flux) is applied to the PCB pads, and the components are placed on top. The PCB is then heated in a reflow oven, melting the solder and creating the joints.
Equipment and Materials
- Solder paste
- Stencil or syringe for applying solder paste
- Pick-and-place machine (for larger-scale production)
- Reflow oven
- PCB pallet or carrier
Process
- Apply solder paste to the PCB pads using a stencil or syringe.
- Place the through-hole components into their respective holes.
- If using a pick-and-place machine, program it to place any additional surface-mount components.
- Place the PCB in a pallet or carrier and load it into the reflow oven.
- The oven heats the PCB according to a predetermined temperature profile, melting the solder and creating the joints.
- The PCB cools down, and the solder solidifies, completing the soldering process.
- Clean any excess flux residue from the PCB.
Comparison of Soldering Methods
Method | Advantages | Disadvantages |
---|---|---|
Hand Soldering | – Precise control – Suitable for small-scale projects and repairs – Low initial cost |
– Time-consuming for large projects – Requires operator skill and consistency |
Wave Soldering | – Fast and efficient for mass production – Consistent solder joints |
– Expensive equipment – Not suitable for small-scale projects – Limited control over individual joints |
Selective Soldering | – Combines precision and speed – Suitable for mixed-component PCBs – Ideal for heat-sensitive components |
– Higher equipment cost than hand soldering – Requires programming and setup time |
Reflow Soldering | – Suitable for surface-mount and some through-hole components – Efficient for larger-scale production |
– Requires solder paste application – Limited to components that can withstand reflow temperatures |
FAQs
1. What is the best soldering method for small-scale projects?
For small-scale projects, hand soldering is often the most suitable method. It offers precise control and requires minimal initial investment in equipment.
2. Can through-hole components be soldered using reflow soldering?
Yes, some through-hole components can be soldered using reflow soldering. However, the components must be able to withstand the high temperatures involved in the reflow process.
3. What is the difference between lead-based and lead-free solder?
Lead-based solder contains a mixture of tin and lead, while lead-free solder typically consists of tin, copper, and silver. Lead-free solder has a higher melting point and requires slightly different soldering techniques compared to lead-based solder.
4. How do I choose the right soldering iron tip for hand soldering?
When choosing a soldering iron tip for hand soldering, consider the size and shape of the components and PCB pads. A chisel tip is suitable for most general-purpose soldering, while a fine-point tip is ideal for precise work on smaller components.
5. How can I improve the quality of my soldered joints?
To improve the quality of your soldered joints:
– Ensure the soldering iron tip is clean and well-tinned
– Use the appropriate solder wire diameter and type for the job
– Apply heat to both the component lead and PCB pad simultaneously
– Allow the solder to flow around the joint naturally, avoiding excessive solder application
– Keep the soldering iron tip in contact with the joint for a short time to prevent overheating
Conclusion
Through-hole soldering is a crucial skill for anyone working with electronic components and PCBs. The choice of soldering method depends on factors such as project scale, component types, and available resources. Hand soldering is versatile and suitable for small-scale projects, while wave soldering and selective soldering offer speed and efficiency for larger-scale production. Reflow soldering is primarily used for surface-mount components but can also accommodate some through-hole components. By understanding the advantages and disadvantages of each soldering method, you can choose the most appropriate technique for your project and ensure high-quality, reliable solder joints.
0 Comments