Introduction
Printed circuit boards (PCBs) are essential components in nearly all electronic devices and equipment. While high-volume PCB assembly is common for mass-produced consumer electronics, many products are manufactured in lower quantities. Low volume PCB assembly has distinct challenges and considerations compared to high-volume production.
This comprehensive guide examines low volume PCB assembly. It covers topics like:
- Defining low volume PCB quantities
- Pros and cons of low volume PCB assembly
- Design considerations for prototype and low volume PCBs
- Low volume PCB assembly process steps
- Choosing a low volume PCB assembly provider
- Cost factors and calculations for low volume PCB assembly
- Quality control for low volume PCB production
- Testing and inspection of low volume PCBs
- Approaches for transitioning from low to high volume
With insight across these key areas, product developers and engineers can make informed decisions when planning a low volume PCB assembly run.
What Quantities Define Low Volume PCB Assembly?
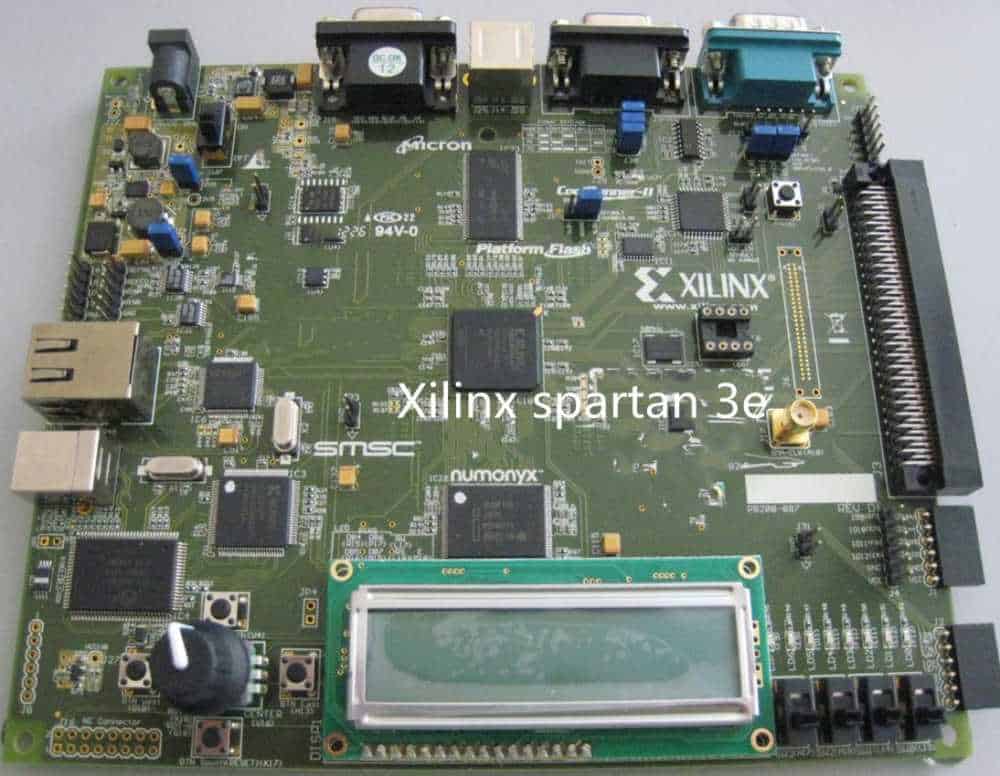
Low volume PCB assembly is a relative term, but generally refers to production runs of 1 to 1,000 boards. Medium volumes range from 1,000 to 10,000 boards. High volume production involves 10,000+ boards.
More specifically, here are typical quantites that classify as low volume in PCB assembly:
- Prototyping: 1-10 boards
- Pre-production: 10-50 boards
- New product introduction (NPI): 50-100 boards
- Short run production: 100-1,000 boards
Lower quantities allow testing of product designs before high volume production. Shorter runs are also suitable for lower volume products that will never require thousands of PCBs.
Advantages of Low Volume PCB Assembly
Low volume PCB assembly provides important benefits:
Faster turnaround – Lead times for low quantities are shorter than high volume orders. A few boards can be produced in days compared to weeks for production runs.
Design flexibility – Designs can be modified during small scale assembly. Improving the PCB layout and bill of materials (BOM) is much easier with lower quantities.
Lower costs – High volume production requires expensive testing, specialized tools and dedicated facilities. Low volume assembly has lower startup costs.
Pricing ability – Higher per-unit pricing can be applied to smaller quantities to offset production costs. Larger volumes depend on scale economies.
Less risk – Low scale production lets products be thoroughly tested before high-volume manufacturing. Early issues can be addressed before more PCBs are produced.
For these reasons, low volume PCB assembly is recommended for new products still under development.
Challenges of Low Volume PCB Assembly
Despite the advantages, low volume PCB assembly also poses challenges:
Higher per-unit costs – With fewer boards to spread production costs over, the per-board cost is greater for lower quantities.
Manual assembly – Automated assembly lines are generally not practical for prototyping or small scale production. More manual labor increases costs.
Multiple assembly runs – If more PCBs are needed, multiple separate assembly runs may be required. This can increase total production time and costs.
Material waste – Minimum order quantities for components may result in excess parts. Leftover materials increase expenses.
Testing limitations – Comprehensive testing like burn-in for reliability requires large samples. Test coverage is more limited for small builds.
Planning obstacles – Forecasting and scheduling are more difficult with variable low volume demand. Production downtime is also more likely.
While necessary for product development, low volume PCB assembly comes with tradeoffs to weigh against benefits.
Design Considerations for Low Volume PCBs
To maximize quality and reliability when working with a PCB assembly service on low volume boards, the design stage is crucial. Follow these design best practices:
Allow for rework – Include test points and connectors to support debugging and modifications during low volume assembly. Build in space around components in case changes are needed.
Use standard components – Stick to common, well-sourced parts that are easier to procure in smaller quantities. Avoid highly specialized or cutting-edge components.
Minimize BOM line items – Reduce the number of unique components to simplify sourcing and assembly. Consolidate multiple components with similar specs when possible.
Provide reference designs – Share any related high volume boards and the bill of materials. These can guide design and assembly considerations.
Simulate manufacturing – Use CAD tools to model assembly, thermal issues, vibration, etc. Correct any design problems before prototyping builds.
Design for testability – Include test points, indicators, and access to simplified in-circuit testing. This aids assembly verification and fault isolation.
Document extensively – Provide complete documentation on the circuitry, layout, BOM, component datasheets, etc. to avoid assembly issues.
Low Volume PCB Assembly Process Overview
The assembly process for low volume PCBs involves these typical steps:
Sourcing components – Low quantity components are purchased based on the bill of materials. Minimum order quantities may require buying surplus parts.
Kitting parts – Purchased components are organized into kits for each board to be assembled. Parts may be placed onto trays or tapes.
Solder paste application – Solder paste is screen printed or dispensed through stencils onto the PCBs.
Pick and place – Components are picked from feeders and precisely placed onto the solder paste footprints.
Reflow soldering – Boards pass through an oven to heat solder paste and attach components.
Inspection – Assembled boards are visually inspected for defects using optical equipment.
Testing – Basic power-on and functional tests verify boards operate properly after assembly.
Programming – Code may be flashed into programmable devices on the board as a final assembly step.
Conformal coating – A protective coating can be applied to protect boards from environmental factors.
Final inspection – Quality checks confirm boards are fully assembled and functional after all steps are complete.
The low volume assembly process resembles high volume production but with much lower automation. Hand assembly and manual checks are used extensively.
Choosing a Low Volume PCB Assembly Provider
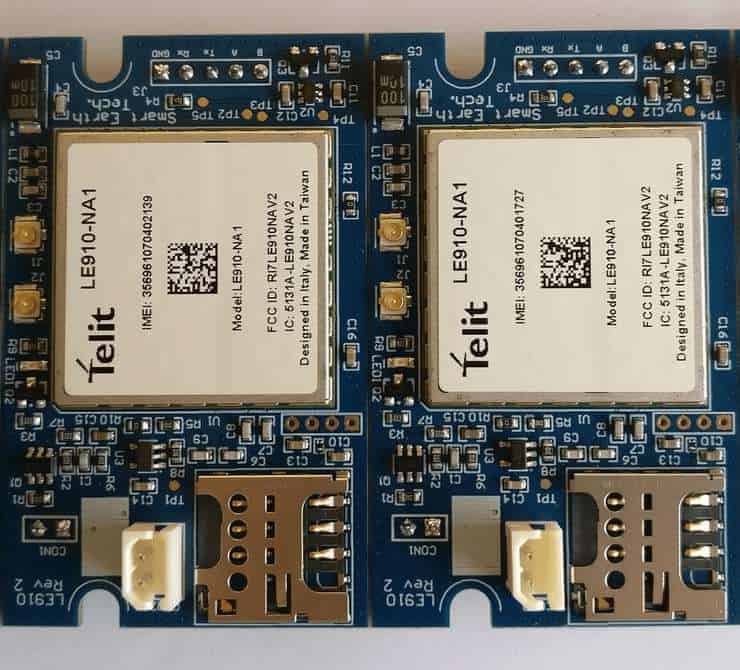
Selecting the right contract manufacturer for low volume PCB assembly requires evaluating several factors:
Technical capabilities – Review supported assembly technologies, component types, board substrates, etc. Ensure the provider can assemble the planned design.
Quality processes – Ask about process controls, inspection procedures, quality certifications, repair policies, etc. This impacts output consistency.
Scalability – Look for ability to seamlessly scale up production volumes over time once testing is complete.
Secondary services – Seek providers that offer additional services like design, procurement, coating, box build, order fulfillment etc. This simplifies sourcing.
Prototyping experience – For assembling first articles, find providers highly experienced with low volume prototype builds.
Communication – Interaction will be important during low volume builds, so evaluate ease of communication with sales and engineering reps.
Geography – Determine if the provider has assembly facilities in the desired region. This impacts logistics lead times and costs.
Engineering support – Look for assembly partners willing to collaborate on design reviews, documentation, troubleshooting, test, inspection etc.
Cost structure – Review pricing models (layer rates, component costs, etc.) and how volumes impact per unit pricing.
Thoroughly qualifying PCB assembly partners helps avoid issues whenprogressing from prototypes to pilot builds.
Cost Factors in Low Volume PCB Assembly
Low volume PCB assembly comes with higher per-unit costs compared to high-volume production. Here are the key factors affecting low volume costs:
Board substrate – Base material costs increase for thicker layers, high-frequency (RF) material, flex PCBs etc.
Board size – Large boards require more materials and occupy more space on panel.
Layer count – Additional layers add cost for lamination, drilling, via processing, etc.
Component types – Specialty components like RF chips, FPGAs, etc. are more expensive and impact BOM cost.
Component count – More components means higher material, placement and soldering costs.
Lead times – Faster turnaround options (24 hour, 3 day, etc.) add premium fees.
Secondary operations – Addition of extra steps like coating, programming, testing etc. increase costs.
Order quantities – Low volumes have much higher cost per board due to setup, labor, and overhead.
Testing and inspection – Manual checks and testing for each board add significant labor cost.
IPC Class – Meeting higher quality classes like IPC-A-610 Class 2 or 3 adds cost.
Certifications – Special regulatory or industry certifications lead to more inspection and validity testing.
Location – Assembly labor rates differ greatly depending on facility geography.
To optimize pricing for low volume orders, only utilize required capabilities and services. Simplify designs and choose economical components when possible.
Quality Control Factors for Low Volume
While low volume PCB production does not allow statistical process controls, extra diligence is required to ensure quality:
- Supplier qualification – Validate suppliers of boards, components and materials. Review their certifications and internal quality system.
- Inspection staff – Leverage IPC certified inspectors to spot defects. Check workmanship against IPC-A-610.
- Process monitoring – Document all process parameters. Monitor for drift from benchmarks. Perform machine maintenance.
- Traceability – Assign unique IDs and serialize boards and components to enable tracking.
- ESD controls – Follow rigorous ESD procedures to avoid static discharge damage, especially with manual handling.
- Operator training – Ensure assembly technicians are properly trained on equipment operation and process steps.
- Visual inspection – Perform 100% inspection of solder joints, components placement, markings, board defects, etc.
- Assembly validation – Test completed boards for power on, basic functionality, programming verification, etc.
- Documenting issues – Record any defects, rework performed, parameter deviations, corrective actions etc.
While statistical methods are limited by lower quantities, following disciplined quality procedures for each board is critical.
Testing and Inspection of Low Volume PCBs
Rigorous testing and inspection techniques help avoid problems and defects in low volume PCB assembly:
Visual inspection – All boards, components, and solder joints should be visually examined, often under a microscope. Verify part placements, orientations, markings, solder quality, board integrity and for any damage.
In-circuit test (ICT) – Use fixture boards with test probes to electrically verify all components, connections, and circuitry. Analog and simple digital tests can be applied.
Flying probe testing – Automatically probe test points on each bare board based on a program. Checks for shorts, opens, and basic component functionality.
Functional testing – Run boards through complete functional test routines with all components populated. Confirm intended operation and specifications are met.
X-ray inspection – Use X-ray imaging to inspect internal features like buried vias, inner layer alignments, and inspect solder joint quality.
Automated optical inspection (AOI) – Optically scan assembled boards to compare placements against CAD data and identify defects. Limited by resolution on fine features.
Boundary scan – Leverage boundary scan circuitry to thoroughly test component interconnects and functions using a JTAG interface.
Programming verification – Validate code flashed into programmable chips like microcontrollers, FPGAs, CPLDs, eMMCs, etc.
While low volume limits statistical sampling, 100% inspection and testing of each board is recommended when possible. This helps catch any production issues early.
Transitioning from Low to High Volume
Once PCB designs are proven through low volume assembly, eventually ramping up to larger scale production is typical. Here are tips for a smooth volume transition:
- Optimize assembly process early – Collaborate with provider on potential process improvements and optimizations from the start.
- Improve test coverage – Expand the types and extent of testing as volumes increase. Add scan-based structural testing, ICT fixtures, burn-in etc.
- Analyze defects – Aggregate data from low volume defects to identify necessary design tweaks or process adjustments.
- Validate supply chain – Qualify that suppliers can meet rising component demand without quality drops or lead time slips.
- Evaluate automation – Determine where added automation like SMT lines could cut costs and improve consistency for higher volumes.
- Standardize processes – Document detailed assembly and test procedures so additional facilities can replicate them reliably.
- Plan capacity – Forecast demand and work with providers to schedule capacity for upcoming growth. Avoid shortages or downtime.
- Monitor KPIs – Track key process indicators like yields, defects, cycle times etc. as volumes increase to flag any regression.
With careful planning, low volume PCB assembly can efficiently scale to support wider production when a product design is ready.
Frequently Asked Questions
Here are some common questions about low volume PCB assembly:
What are typical lead times for low volume PCB assembly?
Lead times for under 50 boards are typically ~5-10 days. For quantities of 50-100 units, lead times are ~10-15 days. Above 100 boards, expect ~15-20+ day lead times.
What file formats do I need for low volume PCB assembly?
Supply Gerber files for all layers, NC drill files, assembly drawings, component placement files, bill of materials, any component CAD models, and documentation like assembly notes.
Can I make changes to my PCB design after starting low volume assembly?
Minor changes are possible early in assembly. But the sooner design freeze can be reached, the lower the cost impact and delay risk of engineering changes.
How are components sourced for low volume PCB assembly?
A combination of existing supplier stock and quick-turn small scale procurements are used. Work with your provider to identify any long-lead or specialty parts.
What terminal finishes should I use for low volume PCBs?
HASL lead-free solder finish works well for low cost testing. For more durable plating, ENIG or Immersion Silver are good finishes for low volume boards headed to production.
Conclusion
Low volume PCB assembly enables validating electronic designs before committing to mass production. While requiring greater cost and effort per board, small scale builds reduce risk and provide flexibility during product development.
With mindful design and partner selection, engineers can effectively leverage low volume assembly for prototyping, pilot builds, and transitioning products to full production. The guidelines in this article aim to help successfully plan a low volume PCB project.
0 Comments