Understanding Solder Joint Quality
Definition of Solder Joint Quality
Solder joint quality refers to the overall integrity, reliability, and performance of the interconnections formed between electronic components and printed circuit boards (PCBs) through the soldering process. A high-quality solder joint ensures proper electrical conductivity, mechanical strength, and long-term stability.
Importance of Solder Joint Quality
The importance of solder joint quality cannot be overstated in the electronics industry. Poor solder joint quality can lead to a range of issues, including:
– Electrical failures and intermittent connections
– Reduced mechanical strength and durability
– Increased susceptibility to thermal and mechanical stresses
– Premature device failure and reduced product lifespan
Ensuring high solder joint quality is essential for maintaining the reliability and performance of electronic devices, minimizing costly rework and repairs, and enhancing customer satisfaction.
Factors Influencing Solder Joint Quality
1. Soldering Materials
The selection of appropriate soldering materials plays a significant role in achieving quality solder joints. The key soldering materials include:
Solder Alloys
Solder alloys are the primary material used in the soldering process. The most commonly used solder alloys are tin-lead (SnPb) and lead-free alloys such as tin-silver-copper (SAC). The composition and properties of the solder alloy directly influence the wetting behavior, melting point, and mechanical strength of the solder joint.
Flux
Flux is a chemical compound applied to the soldering surface to remove oxides, prevent reoxidation, and promote proper wetting of the solder. The choice of flux depends on the soldering process, substrate materials, and environmental considerations. Flux types include rosin-based, water-soluble, and no-clean fluxes.
Flux Type | Characteristics | Cleaning | Applications |
---|---|---|---|
Rosin | Mild activation, good wetting | Requires cleaning | Through-hole, SMT |
Water-Soluble | Strong activation, excellent wetting | Water cleaning | High-reliability |
No-Clean | Low residue, mild activation | No cleaning needed | SMT, wave soldering |
Solder Paste
Solder paste is a mixture of solder alloy particles suspended in a flux vehicle. It is commonly used in surface mount technology (SMT) for precise solder deposition. The solder paste’s composition, particle size, and rheological properties affect the print quality, reflow behavior, and resulting solder joint quality.
2. PCB Design and Manufacturing
PCB Material Selection
The choice of PCB material impacts the solderability and reliability of solder joints. Common PCB materials include FR-4, polyimide, and ceramic. The material’s thermal stability, coefficient of thermal expansion (CTE), and surface finish compatibility should be considered to ensure optimal solder joint quality.
PCB Surface Finish
The PCB surface finish provides a solderable surface and protects the copper pads from oxidation. Common surface finishes include hot air solder leveling (HASL), immersion silver (IAg), immersion tin (ISn), and electroless nickel immersion gold (ENIG). The surface finish affects the wettability, solderability, and long-term reliability of solder joints.
Surface Finish | Characteristics | Shelf Life | Solderability | Cost |
---|---|---|---|---|
HASL | Excellent solderability, uneven surface | Long | Excellent | Low |
IAg | Flat surface, good solderability | Moderate | Good | Moderate |
ISn | Flat surface, good wettability | Short | Good | Low |
ENIG | Flat surface, gold wire bonding | Long | Excellent | High |
PCB Layout and Design
Proper PCB layout and design are crucial for achieving quality solder joints. Key considerations include:
– Adequate pad sizes and shapes for component terminations
– Proper spacing between pads to prevent solder bridging
– Thermal relief patterns for efficient heat dissipation
– Minimizing thermal mismatch between components and PCB
– Optimizing copper trace widths and thicknesses for current carrying capacity
3. Soldering Process Parameters
Soldering Temperature Profile
The soldering temperature profile refers to the time-temperature relationship during the soldering process. It includes preheat, soak, reflow, and cooling stages. Proper control of the temperature profile ensures adequate flux activation, solder melting, wetting, and intermetallic compound (IMC) formation. Deviation from the optimal temperature profile can lead to defects such as cold joints, voids, or excessive IMC growth.
Preheat and Soak
Preheat and soak stages are critical for removing moisture, activating flux, and minimizing thermal shock to components. The preheat rate, soak temperature, and soak duration should be carefully controlled based on the solder paste and component specifications.
Peak Temperature and Time Above Liquidus (TAL)
The peak temperature is the maximum temperature reached during the reflow process, while TAL refers to the time the solder alloy remains above its melting point. Sufficient peak temperature and TAL are necessary for proper solder melting, wetting, and IMC formation. However, excessive peak temperature or prolonged TAL can cause component damage, solder balling, or IMC overgrowth.
Cooling Rate
The cooling rate after the reflow process affects the grain structure, mechanical properties, and solidification behavior of the solder joint. A controlled cooling rate helps prevent thermal shock, minimizes residual stresses, and promotes the formation of a fine-grained solder joint microstructure.
4. Component Selection and Packaging
Component Termination and Compatibility
The termination material and surface finish of electronic components play a crucial role in solder joint quality. Common component terminations include tin, silver, gold, and palladium. The compatibility between the component termination and PCB surface finish should be considered to ensure proper wetting and metallurgical bonding.
Component Package Type
Different component package types have varying requirements for solder joint formation. Surface mount packages such as chip resistors, chip capacitors, QFPs, BGAs, and CSPs require precise solder paste printing and reflow soldering. Through-hole components like PTH connectors and axial/radial lead components rely on wave soldering or manual soldering techniques.
Moisture Sensitivity Level (MSL)
Moisture-sensitive components, particularly plastic encapsulated devices, are susceptible to moisture absorption during storage and handling. Improper management of moisture-sensitive components can lead to delamination, cracking, or “popcorning” during the soldering process. Adhering to the manufacturer’s specified MSL and baking requirements is essential for preventing moisture-related solder joint defects.
5. Environmental Factors
Cleanliness and Contamination Control
Maintaining a clean soldering environment is crucial for achieving high-quality solder joints. Contaminants such as dust, dirt, oils, and flux residues can hinder proper solder wetting and lead to defects like non-wetting, dewetting, or voids. Implementing contamination control measures, including proper handling, storage, and cleaning procedures, helps ensure solder joint integrity.
Temperature and Humidity Control
Ambient temperature and humidity levels can affect the soldering process and solder joint quality. High humidity can lead to moisture absorption by hygroscopic materials, promoting oxidation and reducing solderability. Excessive temperature variations can cause thermal stresses and impact the solder joint’s mechanical integrity. Maintaining a controlled environment with appropriate temperature and humidity levels is essential for consistent solder joint quality.
ESD Protection
Electrostatic discharge (ESD) can damage sensitive electronic components and affect solder joint reliability. Implementing ESD protection measures, such as grounding, ionizers, and ESD-safe packaging materials, helps prevent ESD-related solder joint failures.
Solder Joint Inspection and Quality Assurance
Visual Inspection
Visual inspection is the primary method for assessing solder joint quality. Inspectors examine solder joints for characteristics such as wetting, shape, size, and the presence of defects like bridging, insufficient solder, or voids. Visual inspection can be performed manually or using automated optical inspection (AOI) systems.
X-Ray Inspection
X-ray inspection is used to detect internal solder joint defects that are not visible through visual inspection. It is particularly useful for examining solder joints in ball grid arrays (BGAs), chip scale packages (CSPs), and other area array packages. X-ray inspection can reveal defects such as voids, head-in-pillow (HIP), and missing or misaligned solder balls.
Electrical Testing
Electrical testing verifies the functionality and connectivity of solder joints. Methods include in-circuit testing (ICT), flying probe testing, and boundary scan testing. Electrical testing helps identify opens, shorts, and other electrical anomalies related to solder joint quality.
Mechanical Testing
Mechanical testing evaluates the strength and durability of solder joints. Common methods include shear testing, pull testing, and bend testing. Mechanical testing assesses the solder joint’s ability to withstand physical stresses and provides insights into its reliability under different loading conditions.
Metallurgical Analysis
Metallurgical analysis involves cross-sectioning and microscopic examination of solder joints. It provides detailed information about the solder joint’s microstructure, intermetallic compound formation, and potential defects like cracks or voids. Metallurgical analysis is often used for failure analysis and process optimization.
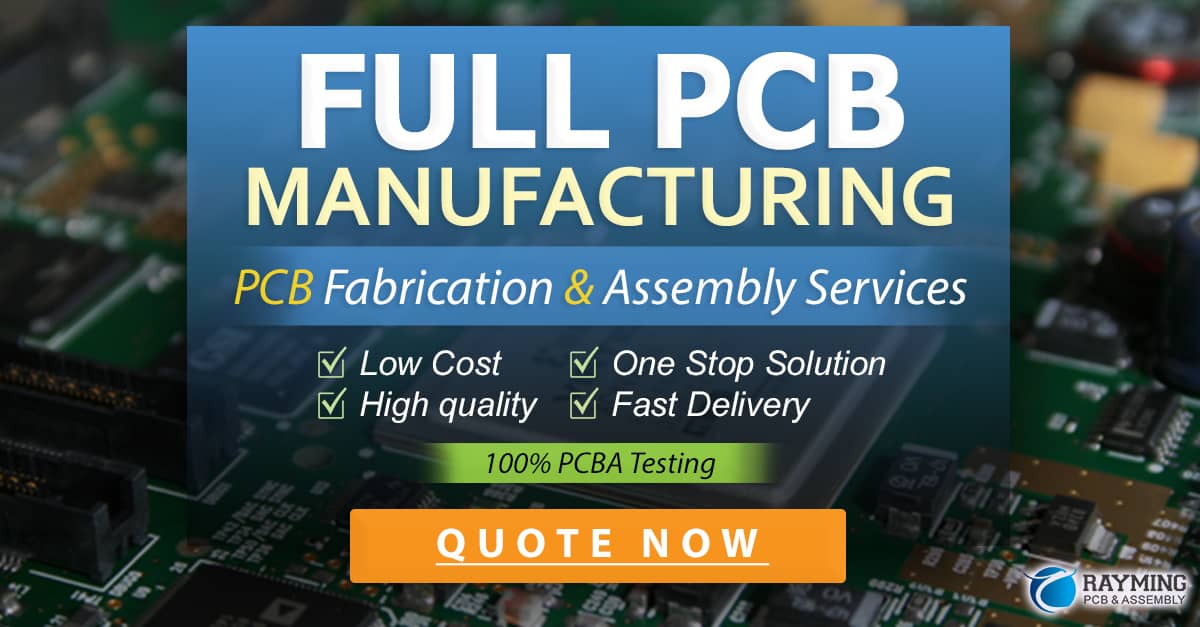
Frequently Asked Questions (FAQ)
1. What is the most common solder alloy used in electronics assembly?
The most common solder alloy used in electronics assembly is tin-lead (SnPb), particularly the eutectic composition of 63% tin and 37% lead (Sn63Pb37). However, due to environmental regulations like the Restriction of Hazardous Substances (RoHS) directive, lead-free solder alloys such as tin-silver-copper (SAC) have gained widespread adoption.
2. What are the main causes of solder joint defects?
The main causes of solder joint defects include:
– Improper soldering temperature profile
– Inadequate or excessive solder volume
– Poor wetting due to contamination or oxidation
– Mismatch in thermal expansion coefficients between components and PCB
– Incorrect component placement or orientation
– Inadequate flux activation or insufficient cleaning
– Mechanical stresses during handling or operation
3. How can voids in solder joints be minimized?
Voids in solder joints can be minimized by:
– Optimizing the soldering temperature profile to ensure proper flux activation and solder melting
– Using solder paste with appropriate rheological properties and minimal air entrapment
– Implementing proper stencil design and printing techniques
– Controlling the reflow atmosphere to minimize oxidation
– Applying vacuum or vapor phase soldering for void reduction in specific applications
4. What is the purpose of intermetallic compounds (IMCs) in solder joints?
Intermetallic compounds (IMCs) are formed at the interface between the solder and the substrate materials (component terminations and PCB pads) during the soldering process. IMCs play a crucial role in providing mechanical strength and metallurgical bonding in solder joints. However, excessive IMC growth can lead to brittle and less reliable solder joints.
5. How can the reliability of solder joints be improved?
The reliability of solder joints can be improved by:
– Selecting compatible materials (solder alloy, component terminations, PCB surface finish)
– Optimizing the soldering process parameters (temperature profile, preheat, cooling rate)
– Implementing robust PCB design practices (pad sizes, spacing, thermal management)
– Using appropriate flux and ensuring proper cleaning
– Conducting thorough inspection and quality control procedures
– Performing accelerated life testing and failure analysis for continuous improvement
Conclusion
Achieving high-quality solder joints is a multifaceted endeavor that requires careful consideration of various influential factors. From material selection and PCB design to soldering process parameters and environmental controls, each aspect plays a vital role in determining the reliability and performance of solder joints.
By understanding the intricacies of solder joint formation, implementing best practices, and conducting thorough inspection and testing, manufacturers can ensure the production of reliable and robust electronic assemblies. Continuous improvement and staying updated with the latest advancements in soldering technologies and standards are essential for maintaining a competitive edge in the ever-evolving electronics industry.
Investing in solder joint quality not only enhances product reliability and customer satisfaction but also reduces costs associated with rework, repairs, and warranty claims. By prioritizing solder joint quality, manufacturers can build a reputation for delivering high-quality electronic products that meet the demanding requirements of today’s market.
0 Comments