Introduction to PCB Solutions
Printed Circuit Boards (PCBs) are essential components in modern electronics. They provide a compact and efficient way to connect electronic components and create complex circuits. PCB solutions involve the design, manufacturing, and assembly of these boards to meet specific requirements for various applications.
In this comprehensive guide, we will explore useful tips and best practices for PCB solutions. Whether you are a beginner or an experienced professional, these tips will help you optimize your PCB designs, streamline your manufacturing processes, and ensure the reliability and performance of your electronic products.
Key Considerations for PCB Design
Choosing the Right PCB Material
One of the first steps in PCB design is selecting the appropriate material for your board. The choice of PCB material depends on several factors, such as the intended application, operating environment, and required electrical properties. Here are some common PCB materials and their characteristics:
Material | Characteristics | Applications |
---|---|---|
FR-4 | – Cost-effective – Good electrical insulation – Suitable for most general-purpose applications |
– Consumer electronics – Industrial control systems – Telecommunications equipment |
High Tg FR-4 | – Higher glass transition temperature (Tg) – Improved thermal stability – Better resistance to moisture and chemicals |
– Automotive electronics – Aerospace systems – Medical devices |
Polyimide | – Excellent thermal stability – High flexibility – Resistance to harsh environments |
– Flexible circuits – High-temperature applications – Aerospace and military electronics |
Aluminum | – Excellent thermal conductivity – Lightweight – Good mechanical stability |
– High-power LED lighting – Automotive power electronics – RF and microwave circuits |
Defining Layer Stack-up
The layer stack-up of a PCB refers to the arrangement of conductive and insulating layers within the board. Proper layer stack-up design is crucial for signal integrity, power distribution, and manufacturability. Consider the following tips when defining your PCB layer stack-up:
- Determine the required number of layers based on the complexity of your circuit and the routing density.
- Use dedicated power and ground planes to provide low-impedance paths for power distribution and reduce noise.
- Separate sensitive signals, such as high-speed digital or analog signals, from noisy signals to minimize crosstalk and interference.
- Maintain symmetry in the layer stack-up to minimize warpage and ensure uniform thermal expansion.
- Consult with your PCB manufacturer to ensure compatibility with their manufacturing capabilities and design rules.
Component Placement and Routing
Efficient component placement and routing are essential for optimizing PCB performance and manufacturability. Here are some tips to keep in mind:
- Place components in a logical and organized manner, considering signal flow and the proximity of related components.
- Minimize the distance between components to reduce signal path lengths and improve signal integrity.
- Use appropriate component footprints and pad sizes to ensure reliable soldering and assembly.
- Route critical signals first, such as high-speed signals or sensitive analog signals, to prioritize their performance.
- Avoid sharp corners and acute angles in traces to reduce signal reflections and improve manufacturability.
- Follow the manufacturer’s recommended design rules and guidelines for trace widths, spacing, and via sizes.
PCB Manufacturing Process
Fabrication Techniques
PCB fabrication involves several techniques to create the conductive patterns and layers on the board. Understanding these techniques can help you design PCBs that are compatible with the manufacturing process. Common PCB fabrication techniques include:
- Etching: Removing unwanted copper from the PCB substrate to create the desired conductive patterns.
- Drilling: Creating holes in the PCB for through-hole components, vias, and mounting.
- Plating: Applying a thin layer of metal, such as copper or gold, to the holes and surfaces of the PCB to improve conductivity and protect against corrosion.
- Solder Mask Application: Applying a protective layer over the copper traces to prevent short circuits and improve solderability.
- Silkscreen Printing: Adding text, logos, and component identifiers to the PCB surface for easy assembly and identification.
Quality Control and Testing
Ensuring the quality and reliability of PCBs is crucial for the success of your electronic products. Implement robust quality control measures and testing procedures throughout the manufacturing process:
- Conduct visual inspections to identify any defects, such as broken traces, short circuits, or incorrect component placement.
- Perform electrical tests, such as continuity and insulation resistance tests, to verify the integrity of the PCB connections.
- Use automated optical inspection (AOI) systems to detect surface-mount defects and ensure proper component placement.
- Employ X-ray inspection for hidden defects, such as voids in solder joints or internal layer misalignments.
- Conduct functional testing to validate the performance of the assembled PCB under real-world operating conditions.
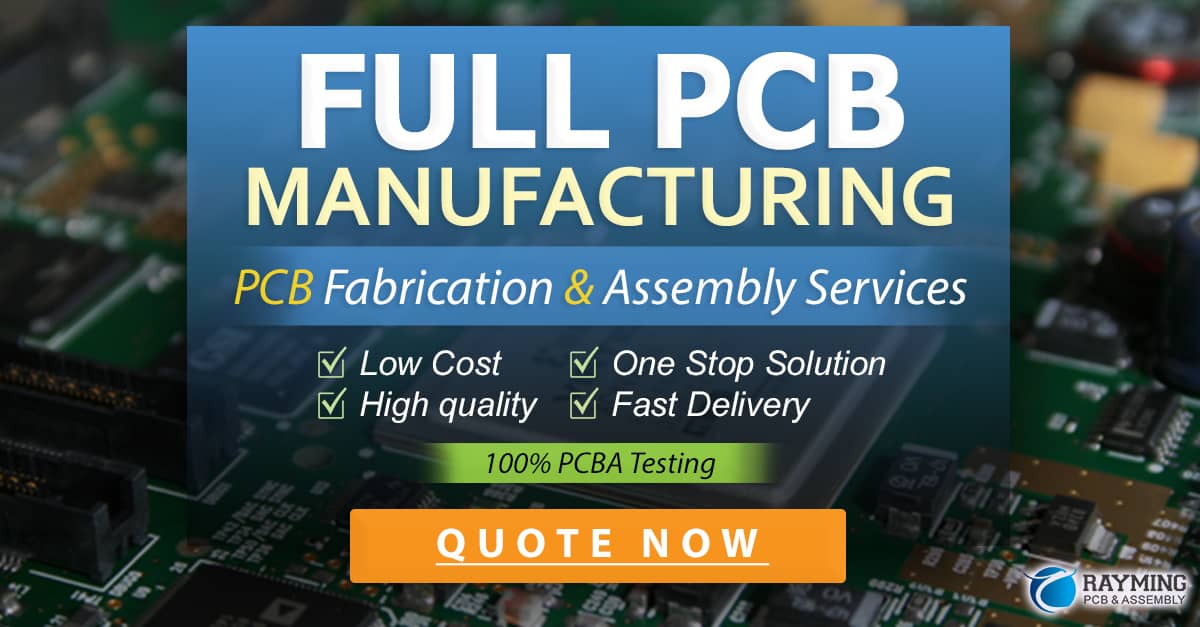
PCB Assembly and Soldering
Surface Mount Technology (SMT)
Surface Mount Technology (SMT) is a popular PCB assembly method that involves mounting components directly onto the surface of the board. SMT offers several advantages, such as smaller component sizes, higher component density, and automated assembly processes. Consider the following tips for successful SMT assembly:
- Use appropriate solder paste and stencil design to ensure accurate and consistent solder deposition.
- Optimize the reflow soldering profile based on the component specifications and PCB material.
- Implement proper component placement and orientation to minimize assembly errors and improve reliability.
- Use appropriate inspection techniques, such as visual inspection or X-ray inspection, to verify the quality of solder joints.
Through-Hole Technology (THT)
Through-Hole Technology (THT) involves inserting component leads through holes drilled in the PCB and soldering them on the opposite side. While THT is less common than SMT, it is still used for certain components that require higher mechanical strength or power handling. Here are some tips for THT assembly:
- Ensure proper hole sizing and spacing to accommodate the component leads and facilitate soldering.
- Use appropriate soldering techniques, such as wave soldering or hand soldering, based on the production volume and component requirements.
- Implement proper lead trimming and cleaning procedures to improve the appearance and reliability of the solder joints.
PCB Troubleshooting and Debugging
Despite careful design and manufacturing, PCBs may sometimes encounter issues that require troubleshooting and debugging. Here are some tips to help you identify and resolve common PCB problems:
- Use visual inspection to identify any obvious defects, such as damaged components, broken traces, or poor solder joints.
- Employ multimeters and oscilloscopes to measure voltages, currents, and signal waveforms at key points in the circuit.
- Use thermal imaging cameras to detect hot spots or thermal issues on the PCB.
- Isolate and test individual components or sections of the circuit to narrow down the problem area.
- Consult the schematic diagram and compare it with the actual PCB to identify any discrepancies or design errors.
- Seek assistance from experienced engineers or PCB design communities when facing complex or persistent issues.
Advanced PCB Techniques
High-Speed PCB Design
Designing PCBs for high-speed applications requires special considerations to ensure signal integrity and minimize electromagnetic interference (EMI). Here are some tips for high-speed PCB design:
- Use controlled impedance traces to match the characteristic impedance of the signal path and minimize reflections.
- Implement proper termination techniques, such as series termination or parallel termination, to reduce signal ringing and overshoot.
- Minimize the use of vias and layer transitions to reduce signal discontinuities and reflections.
- Use ground planes and power planes to provide low-impedance return paths and reduce EMI.
- Follow recommended layout guidelines for high-speed components, such as memory interfaces, high-speed serial links, or RF circuits.
Flex PCB Design
Flex PCBs offer unique advantages in terms of flexibility, space savings, and reliability in certain applications. When designing flex PCBs, consider the following tips:
- Choose the appropriate flex material based on the required flexibility, durability, and environmental conditions.
- Design the flex circuit with proper bend radius and strain relief features to prevent damage during flexing.
- Use appropriate adhesives and coverlays to protect the flex circuit and improve its mechanical strength.
- Consider the placement of components and connectors to minimize stress on the flex circuit during assembly and use.
- Follow the manufacturer’s design guidelines for trace widths, spacing, and bend radius to ensure manufacturability and reliability.
Frequently Asked Questions (FAQ)
1. What is the difference between a single-sided and double-sided PCB?
A Single-sided PCB has conductive traces on only one side of the board, while a double-sided PCB has traces on both sides. Double-sided PCBs offer higher component density and more routing options compared to single-sided PCBs.
2. How do I choose the right PCB Thickness for my application?
The choice of PCB thickness depends on several factors, such as the component sizes, mechanical requirements, and manufacturing capabilities. Common PCB thicknesses range from 0.4mm to 2.0mm. Consult with your PCB manufacturer to determine the appropriate thickness for your specific application.
3. What is the purpose of a solder mask on a PCB?
A solder mask is a protective layer applied over the copper traces on a PCB. It serves several purposes, including preventing short circuits, improving solderability, and protecting the traces from environmental damage. Solder masks also provide a cosmetic finish to the PCB.
4. How can I reduce electromagnetic interference (EMI) in my PCB design?
To reduce EMI in your PCB design, you can employ several techniques, such as:
- Using proper grounding and shielding techniques
- Minimizing loop areas and current paths
- Separating sensitive signals from noisy signals
- Using filters and suppression components, such as ferrite beads or decoupling capacitors
- Following recommended layout guidelines for high-speed signals and components
5. What are the advantages of using surface mount technology (SMT) over through-hole technology (THT)?
SMT offers several advantages over THT, including:
- Smaller component sizes and higher component density
- Faster and more automated assembly processes
- Improved high-frequency performance due to reduced lead inductance
- Lower manufacturing costs for high-volume production
However, THT still has its place in certain applications that require higher mechanical strength or power handling capabilities.
Conclusion
PCB solutions play a vital role in the development of modern electronic products. By following the tips and best practices outlined in this guide, you can optimize your PCB designs, streamline your manufacturing processes, and ensure the reliability and performance of your electronic devices.
Remember to consider key factors such as material selection, layer stack-up, component placement, and routing during the design phase. Implement robust quality control measures and testing procedures throughout the manufacturing process to guarantee the quality and reliability of your PCBs.
Stay updated with the latest advancements in PCB technology, such as high-speed design techniques and flex PCB solutions, to stay competitive in the ever-evolving electronics industry.
By mastering the art of PCB solutions, you can create innovative and reliable electronic products that meet the demands of today’s market.
0 Comments