Introduction to PCB Thickness
Printed Circuit Board (PCB) thickness is a crucial aspect to consider when designing and manufacturing electronic devices. The thickness of a PCB can impact its mechanical strength, electrical properties, and overall performance. In this article, we will explore the standard PCB thicknesses, factors that influence the choice of thickness, and how to determine the right standards for your specific application.
Understanding PCB Thickness Standards
PCB thickness is typically measured in mils (thousandths of an inch) or millimeters (mm). The most common PCB thicknesses used in the industry are:
Thickness (mils) | Thickness (mm) |
---|---|
31.5 | 0.8 |
39.4 | 1.0 |
47.2 | 1.2 |
59.1 | 1.5 |
62.9 | 1.6 |
78.7 | 2.0 |
These standard thicknesses have been established by industry organizations such as the IPC (Association Connecting Electronics Industries) and are widely accepted by PCB manufacturers worldwide.
Factors Influencing PCB Thickness Choice
Several factors can influence the choice of PCB thickness for a particular application. These include:
-
Mechanical Strength: Thicker PCBs offer greater mechanical strength and rigidity, making them suitable for applications that require durability and resistance to vibration or impact.
-
Electrical Properties: The thickness of a PCB can affect its electrical properties, such as impedance and capacitance. Thicker boards may be necessary for high-speed or high-frequency applications to maintain signal integrity.
-
Component Mounting: The thickness of a PCB should be compatible with the components that will be mounted on it. Some components, such as connectors or heavy components, may require a thicker board for proper support.
-
Manufacturing Constraints: The choice of PCB thickness can be influenced by manufacturing constraints, such as the capabilities of the PCB fabrication facility or the available materials.
-
Cost: Thicker PCBs generally cost more to manufacture due to the increased material usage and processing time. The cost factor should be balanced with the performance requirements of the application.
Determining the Right PCB Thickness Standards
To determine the appropriate PCB thickness for your application, consider the following steps:
-
Assess the Mechanical Requirements: Evaluate the mechanical stresses and environmental conditions that the PCB will be subjected to. If the board needs to withstand vibration, shock, or high temperatures, a thicker PCB may be necessary.
-
Consider Electrical Performance: Analyze the electrical requirements of your design, such as signal integrity, power handling, and impedance control. High-speed or high-frequency applications may require specific PCB thicknesses to maintain signal quality.
-
Review Component Specifications: Check the specifications of the components that will be mounted on the PCB. Ensure that the chosen PCB thickness is compatible with the component packages and mounting requirements.
-
Consult with PCB Manufacturers: Discuss your requirements with experienced PCB manufacturers. They can provide guidance on the most suitable PCB thickness based on your design, manufacturing constraints, and industry standards.
-
Prototype and Test: Before finalizing the PCB thickness, it is advisable to create prototypes and perform thorough testing. This allows you to validate the mechanical and electrical performance of the chosen thickness and make any necessary adjustments.
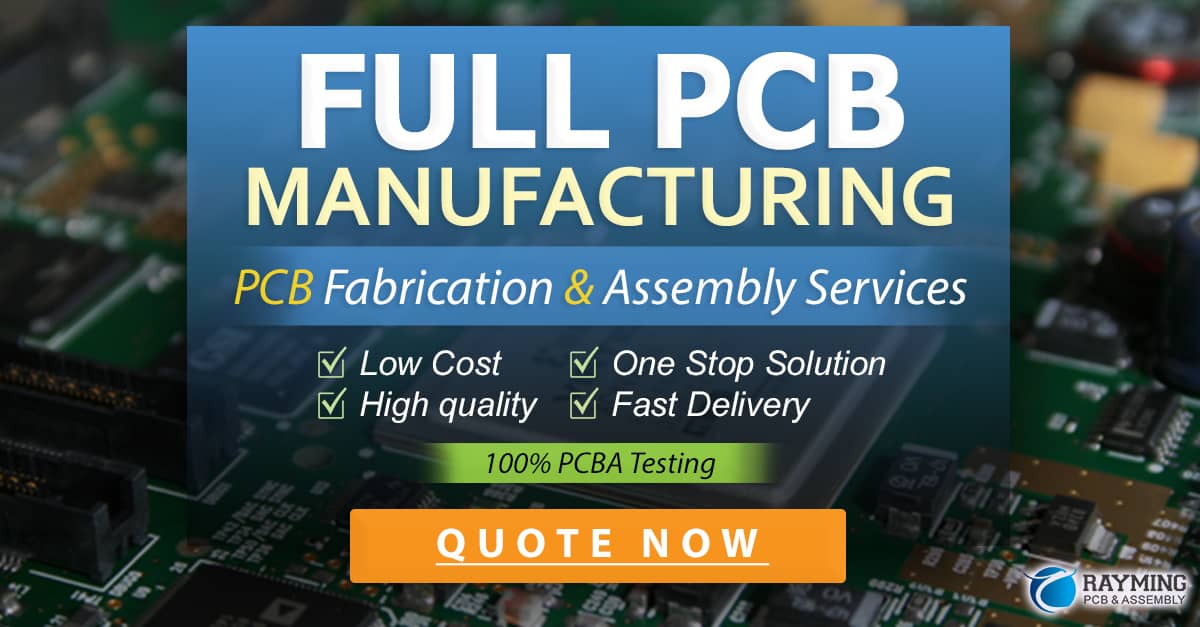
PCB Thickness and Layer Count
In addition to the overall thickness, the number of layers in a PCB also plays a significant role in its performance and functionality. Multi-layer PCBs offer several advantages over single-layer boards:
-
Increased Routing Density: Multi-layer PCBs allow for higher routing density, enabling more complex designs and miniaturization of electronic devices.
-
Improved Signal Integrity: By using dedicated layers for power and ground planes, multi-layer PCBs can reduce electromagnetic interference (EMI) and improve signal integrity.
-
Enhanced Thermal Management: Multi-layer PCBs can incorporate thermal management features, such as thermal vias or dedicated copper layers, to dissipate heat more effectively.
The choice of layer count depends on the complexity of the design, the required functionality, and the manufacturing capabilities. Common layer counts for PCBs include:
- Single-layer
- Double-layer
- Four-layer
- Six-layer
- Eight-layer
- Ten-layer or more
As the layer count increases, the manufacturing complexity and cost also increase. It is essential to strike a balance between the necessary functionality and the cost-effectiveness of the design.
PCB Thickness and Manufacturing Processes
The manufacturing process of a PCB can also influence the choice of thickness. Different manufacturing techniques have their own limitations and capabilities regarding PCB thickness:
-
Through-Hole Technology (THT): THT PCBs typically use thicker boards to accommodate the drilling and plating of through-holes. Common thicknesses for THT PCBs range from 1.6mm to 2.4mm.
-
Surface Mount Technology (SMT): SMT PCBs can be manufactured with thinner boards since they do not require through-hole drilling. Thicknesses as low as 0.4mm are possible with SMT technology.
-
High Density Interconnect (HDI): HDI PCBs employ advanced manufacturing techniques, such as microvias and blind/buried vias, to achieve high routing density. These boards can be made with thinner layers, typically ranging from 0.2mm to 0.8mm.
When selecting the PCB thickness, it is crucial to consider the manufacturing process that will be used and ensure compatibility with the chosen technology.
PCB Thickness and Industry Standards
Industry standards provide guidelines and recommendations for PCB thickness based on various applications and requirements. Some notable standards include:
- IPC-2221: Generic Standard on Printed Board Design
- IPC-6012: Qualification and Performance Specification for Rigid Printed Boards
- IPC-4101: Specification for Base Materials for Rigid and Multilayer Printed Boards
- MIL-PRF-31032: Performance Specification for Printed Circuit Board/Printed Wiring Board, General Specification for
These standards offer detailed information on PCB thickness requirements, tolerances, and testing methods. Adhering to industry standards ensures that your PCB design meets the necessary quality and reliability criteria.
Frequently Asked Questions (FAQ)
-
What is the most common PCB thickness?
The most common PCB thickness used in the industry is 1.6mm (62.9 mils). This thickness provides a good balance between mechanical strength, electrical performance, and cost-effectiveness for many applications. -
Can I use a thinner PCB to reduce the overall size of my device?
Yes, using a thinner PCB can help reduce the overall size of your device. However, it is essential to consider the mechanical and electrical requirements of your application. Thinner PCBs may be more susceptible to warping or damage during handling and assembly. -
How does PCB thickness affect impedance control?
PCB thickness plays a role in impedance control, particularly in high-speed or high-frequency applications. Thinner dielectric layers between the signal traces and the reference plane can help achieve tighter impedance control. However, the choice of thickness should be balanced with other factors such as manufacturing capabilities and cost. -
Are there any limitations on the maximum thickness of a PCB?
While there is no strict upper limit on PCB thickness, excessively thick boards can pose challenges in manufacturing and assembly. Thick boards may require specialized drilling equipment, longer processing times, and may be more prone to warping or delamination. It is advisable to consult with PCB manufacturers to determine the feasibility of very thick PCBs. -
How do I choose the right PCB thickness for my application?
To choose the right PCB thickness, consider the following factors: - Mechanical requirements (strength, rigidity, durability)
- Electrical performance (signal integrity, impedance control, power handling)
- Component specifications (mounting requirements, package compatibility)
- Manufacturing constraints (fabrication capabilities, available materials)
- Cost considerations (material usage, processing time, overall budget)
It is recommended to discuss your specific requirements with experienced PCB manufacturers and adhere to industry standards to ensure the optimal selection of PCB thickness for your application.
Conclusion
PCB thickness is a critical factor in the design and manufacturing of electronic devices. Understanding the standard PCB thicknesses, factors influencing thickness choice, and how to determine the right standards for your application is essential for achieving optimal performance and reliability.
By considering the mechanical requirements, electrical performance, component specifications, manufacturing constraints, and cost factors, you can make an informed decision on the most suitable PCB thickness for your project. Consulting with PCB manufacturers and adhering to industry standards further ensures that your PCB design meets the necessary quality and reliability criteria.
As technology advances and electronic devices become more complex, the selection of appropriate PCB thickness standards becomes increasingly important. By staying informed about the latest industry trends and best practices, you can navigate the challenges of PCB design and manufacturing with confidence and create high-quality, reliable electronic products.
0 Comments