Introduction to PCB Thickness
Printed Circuit Boards (PCBs) are essential components in modern electronic devices. They provide a platform for mounting and interconnecting electronic components, ensuring the proper functioning of the device. One crucial aspect of PCB design is the thickness of the board. PCB thickness plays a significant role in the performance, reliability, and durability of the electronic device. In this article, we will explore the standard PCB thicknesses, factors influencing the choice of thickness, and the impact of thickness on PCB performance.
Understanding PCB Thickness
What is PCB Thickness?
PCB thickness refers to the distance between the top and bottom surfaces of the printed circuit board. It is typically measured in millimeters (mm) or mils (thousandths of an inch). The thickness of a PCB is determined by the number of copper layers, the thickness of each layer, and the thickness of the insulating substrate material.
Common PCB Thicknesses
PCBs come in various thicknesses to cater to different applications and design requirements. The most common PCB thicknesses are:
Thickness (mm) | Thickness (mils) | Application |
---|---|---|
0.4 | 16 | Very thin, used in mobile devices |
0.6 | 24 | Thin, used in small electronic devices |
0.8 | 32 | Standard thickness for general applications |
1.0 | 39 | Thick, used in industrial applications |
1.2 | 47 | Very thick, used in high-power applications |
Factors Influencing PCB Thickness Choice
When selecting the appropriate PCB thickness for a particular application, several factors need to be considered:
-
Application Requirements: The intended use of the electronic device dictates the PCB thickness. For example, mobile devices require thinner PCBs to minimize the overall device size, while industrial applications may demand thicker PCBs for improved durability and heat dissipation.
-
Component Placement: The size and placement of electronic components on the PCB affect the choice of thickness. Thicker PCBs provide more space for component placement and allow for better heat dissipation.
-
Manufacturing Constraints: The manufacturing process and equipment capabilities may limit the range of PCB thicknesses that can be produced. It is essential to consult with the PCB manufacturer to ensure the desired thickness is feasible.
-
Cost Considerations: Thicker PCBs generally require more material and may incur higher manufacturing costs. The choice of PCB thickness should balance the performance requirements with the budget constraints of the project.
Impact of PCB Thickness on Performance
Mechanical Strength and Durability
The thickness of a PCB directly influences its mechanical strength and durability. Thicker PCBs are more resistant to bending, twisting, and impact forces. They provide better support for heavy components and can withstand harsh environmental conditions. In applications where the PCB is subject to vibration or physical stress, a thicker board is often preferred to ensure long-term reliability.
Thermal Management
PCB thickness plays a crucial role in thermal management. Thicker PCBs have a higher thermal mass, which means they can absorb and dissipate heat more effectively. This is particularly important in high-power applications where components generate significant heat. Adequate PCB thickness helps prevent thermal issues such as overheating, component failure, and reduced lifespan.
Signal Integrity
The thickness of a PCB can impact signal integrity, especially in high-speed and high-frequency applications. Thinner PCBs have shorter signal paths, reducing the overall trace length and minimizing signal loss. However, thinner boards are more susceptible to signal interference and crosstalk. Thicker PCBs provide better isolation between layers and can accommodate wider trace widths, improving signal integrity.
Manufacturing Considerations
PCB thickness affects the manufacturing process and the associated costs. Thinner PCBs are generally easier to manufacture and require less material, resulting in lower production costs. However, thinner boards may pose challenges in terms of handling, component placement, and soldering. Thicker PCBs, on the other hand, may require specialized equipment and processes, leading to higher manufacturing costs.
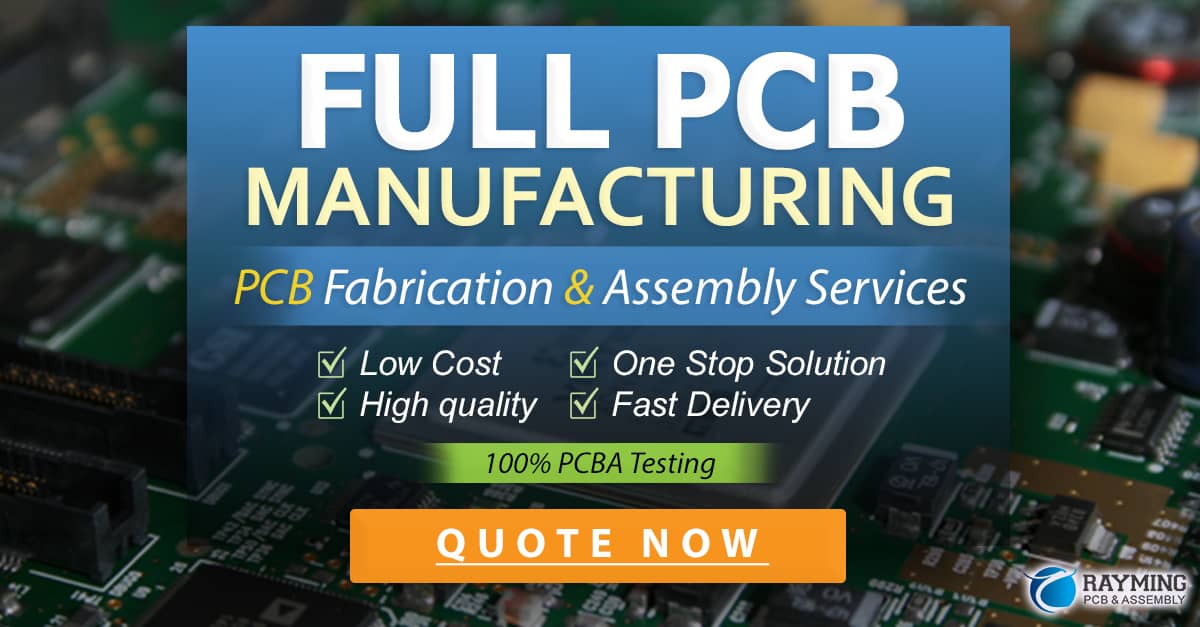
Choosing the Right PCB Thickness
Design Guidelines
When selecting the appropriate PCB thickness for a project, designers should follow these guidelines:
- Consider the application requirements and operating environment of the electronic device.
- Evaluate the component placement and heat dissipation needs.
- Assess the signal integrity requirements, especially for high-speed and high-frequency applications.
- Consult with the PCB manufacturer to ensure the desired thickness is feasible and cost-effective.
- Adhere to industry standards and regulations specific to the application domain.
Industry Standards
Various industry standards provide guidelines and recommendations for PCB thickness based on the application and performance requirements. Some notable standards include:
- IPC-2221: Generic Standard on Printed Board Design
- IPC-6012: Qualification and Performance Specification for Rigid Printed Boards
- IPC-6018: Microwave End Product Board Inspection and Test
- MIL-PRF-31032: Performance Specification for Printed Wiring Board, Rigid, Flexible, and Rigid-Flex
Designers should refer to the relevant industry standards to ensure compliance and optimal PCB design.
Cost Optimization
While thicker PCBs offer certain performance advantages, they also come with higher manufacturing costs. To optimize costs without compromising functionality, designers can consider the following strategies:
- Use the minimum PCB thickness that meets the application requirements.
- Minimize the number of layers in the PCB stack-up.
- Opt for standard PCB thicknesses readily available from manufacturers.
- Optimize the PCB layout to reduce the overall board size.
- Consider alternative materials or manufacturing processes that can reduce costs while maintaining performance.
Conclusion
PCB thickness is a critical aspect of printed circuit board design that significantly influences the performance, reliability, and cost of electronic devices. Understanding the standard PCB thicknesses, factors influencing thickness choice, and the impact of thickness on performance is essential for designers to make informed decisions.
By considering the application requirements, component placement, thermal management, signal integrity, and manufacturing constraints, designers can select the appropriate PCB thickness that balances functionality, durability, and cost-effectiveness. Adhering to industry standards and guidelines ensures compliance and optimal PCB design.
As technology advances and electronic devices become more complex, the choice of PCB thickness will continue to play a crucial role in the development of reliable and high-performance products.
Frequently Asked Questions (FAQ)
-
What is the most common PCB thickness?
The most common PCB thickness is 1.6 mm (0.063 inches). This thickness is widely used in various applications and is readily available from PCB manufacturers. -
Can I use a thinner PCB to reduce the overall size of my device?
Yes, using a thinner PCB can help reduce the overall size of your device. However, it’s important to consider the trade-offs, such as reduced mechanical strength and potential signal integrity issues. It’s recommended to consult with a PCB design expert to determine the optimal thickness for your specific application. -
How does PCB thickness affect the manufacturing cost?
Generally, thicker PCBs require more material and may involve additional manufacturing steps, resulting in higher production costs. Thinner PCBs, on the other hand, use less material and are easier to manufacture, leading to lower costs. However, extremely thin PCBs may require specialized handling and processes, which can increase the manufacturing cost. -
What are the advantages of using a thicker PCB?
Thicker PCBs offer several advantages, including improved mechanical strength and durability, better thermal management, and enhanced signal integrity. They provide better support for heavy components and can withstand harsh environmental conditions. Thicker PCBs also have a higher thermal mass, allowing for better heat dissipation. -
Are there any industry standards that govern PCB thickness?
Yes, there are several industry standards that provide guidelines and recommendations for PCB thickness based on the application and performance requirements. Some notable standards include IPC-2221 (Generic Standard on Printed Board Design), IPC-6012 (Qualification and Performance Specification for Rigid Printed Boards), and MIL-PRF-31032 (Performance Specification for Printed Wiring Board, Rigid, Flexible, and Rigid-Flex). Designers should refer to the relevant standards to ensure compliance and optimal PCB design.
0 Comments