Introduction to SMT PCBs
Surface Mount Technology (SMT) has revolutionized the world of Printed Circuit Boards (PCBs) by offering faster production times, higher component density, and improved reliability compared to traditional through-hole mounting. SMT PCBs have become the go-to choice for electronics manufacturers looking to streamline their production processes and meet the growing demand for compact, high-performance devices.
In this article, we will explore the various aspects of SMT PCBs and how they can help speed up your PCB production time. We will cover the advantages of SMT over through-hole mounting, the SMT assembly process, design considerations for SMT PCBs, and best practices for optimizing your SMT PCB production.
Advantages of SMT PCBs over Through-Hole Mounting
SMT PCBs offer several advantages over traditional through-hole mounting:
-
Faster Assembly: SMT components are placed directly onto the PCB surface, eliminating the need for drilling holes and manual insertion of components. This allows for faster placement of components using automated pick-and-place machines.
-
Higher Component Density: SMT components are smaller than their through-hole counterparts, allowing for more components to be placed on a single PCB. This results in more compact and space-efficient designs.
-
Improved Reliability: SMT components have shorter leads and are less prone to mechanical stress, resulting in improved reliability and fewer solder joint failures.
-
Lower Cost: The automated nature of SMT assembly and the smaller size of SMT components lead to lower production costs compared to through-hole mounting.
The SMT Assembly Process
The SMT assembly process consists of several stages:
-
Solder Paste Application: A thin layer of solder paste is applied to the PCB surface using a stencil or screen printing process. The solder paste contains a mixture of tiny solder particles and flux.
-
Component Placement: SMT components are placed onto the solder paste using automated pick-and-place machines. These machines use computer-aided design (CAD) files to accurately position the components on the PCB.
-
Reflow Soldering: The PCB with placed components is passed through a reflow oven, which heats the board to a specific temperature profile. This melts the solder paste, creating a strong bond between the components and the PCB pads.
-
Inspection and Testing: After the reflow soldering process, the PCB undergoes visual inspection and automated optical inspection (AOI) to check for any defects or misaligned components. Electrical testing is also performed to ensure the functionality of the assembled PCB.
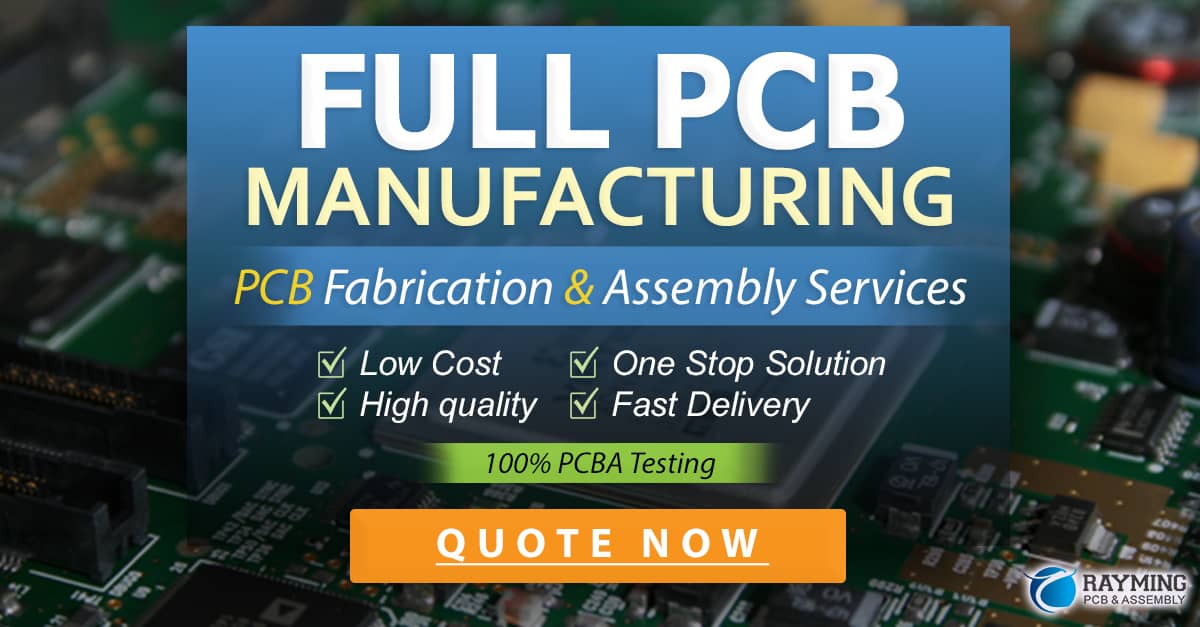
Design Considerations for SMT PCBs
To ensure a smooth and efficient SMT assembly process, consider the following design guidelines:
-
Component Selection: Choose SMT components that are compatible with your PCB design and meet your performance requirements. Consider factors such as package size, pin pitch, and thermal characteristics.
-
Footprint Design: Create accurate and standardized footprints for your SMT components. Follow the manufacturer’s recommendations for pad size, shape, and spacing to ensure proper solderability and component placement.
-
Placement and Orientation: Optimize component placement and orientation to facilitate automated assembly and minimize the risk of tombstoning (when a component stands up on one end due to uneven heating). Place components in a grid-like pattern and align them in the same orientation whenever possible.
-
Solder Mask and Silkscreen: Use a solder mask to protect the PCB surface from accidental solder bridges and to define the solderable areas. Add a silkscreen layer to provide component labels and assembly instructions, making the PCB easier to assemble and debug.
Best Practices for Optimizing SMT PCB Production
To speed up your SMT PCB production time and ensure high-quality results, consider the following best practices:
-
Use Automated Assembly Equipment: Invest in automated pick-and-place machines, reflow ovens, and inspection systems to streamline your SMT assembly process. Automated equipment reduces human error, increases throughput, and ensures consistent quality.
-
Implement Lean Manufacturing Principles: Adopt lean manufacturing principles, such as just-in-time (JIT) inventory management, continuous improvement, and waste reduction. These principles help optimize your production workflow, reduce inventory costs, and minimize lead times.
-
Establish a Quality Control System: Implement a robust quality control system that includes incoming material inspection, process control, and final product testing. Regularly monitor and analyze production data to identify areas for improvement and prevent defects.
-
Collaborate with Experienced PCB Manufacturers: Partner with experienced PCB manufacturers who specialize in SMT assembly. They can provide valuable expertise, state-of-the-art equipment, and quick turnaround times to help you meet your production goals.
Frequently Asked Questions (FAQ)
-
Q: What is the difference between SMT and through-hole mounting?
A: SMT (Surface Mount Technology) involves placing components directly onto the surface of a PCB, while through-hole mounting requires components to be inserted into drilled holes and soldered on the opposite side of the board. SMT offers faster assembly, higher component density, and improved reliability compared to through-hole mounting. -
Q: Can SMT PCBs handle high-power applications?
A: Yes, SMT PCBs can be designed to handle high-power applications by using specialized components, such as power MOSFETs and heat sinks. Proper thermal management and PCB layout techniques are crucial for ensuring the reliability and performance of high-power SMT PCBs. -
Q: How can I ensure the quality of my SMT PCBs?
A: To ensure the quality of your SMT PCBs, implement a comprehensive quality control system that includes incoming material inspection, process control, and final product testing. Use automated inspection equipment, such as automated optical inspection (AOI) machines, to detect defects and ensure consistent quality. -
Q: What are the common defects in SMT PCB Assembly?
A: Common defects in SMT PCB assembly include solder bridges, tombstoning, component misalignment, insufficient or excessive solder, and cold solder joints. These defects can be minimized by following proper design guidelines, using automated assembly equipment, and implementing process controls. -
Q: How can I choose the right PCB manufacturer for my SMT project?
A: When choosing a PCB manufacturer for your SMT project, consider factors such as their experience, capabilities, quality control processes, and customer support. Look for manufacturers who specialize in SMT assembly, have a proven track record of delivering high-quality PCBs, and offer competitive pricing and lead times.
Conclusion
SMT PCBs offer numerous advantages over traditional through-hole mounting, including faster production times, higher component density, and improved reliability. By understanding the SMT assembly process, following design best practices, and implementing lean manufacturing principles, you can significantly speed up your PCB production time and achieve high-quality results.
When embarking on an SMT PCB project, partner with experienced PCB manufacturers who can provide the expertise, equipment, and support you need to succeed. By leveraging the benefits of SMT technology and working with trusted partners, you can streamline your PCB production process and stay ahead in today’s competitive electronics market.
0 Comments