Introduction to PCB Stack-up
A printed circuit board (PCB) stack-up refers to the arrangement of copper layers and insulating materials that make up a PCB. The stack-up determines the electrical properties, signal integrity, and manufacturability of the board. As technology advances and designs become more complex, multi-layer PCBs have become increasingly common. In this article, we will focus on 10-layer PCB stack-ups, providing comprehensive guides on how to design and optimize them for various applications.
Why Choose a 10-Layer PCB Stack-up?
Increased Complexity and Functionality
10-layer PCBs are chosen when a design requires high complexity and functionality. These boards can accommodate a large number of components, circuits, and signal traces, making them suitable for advanced electronic devices such as smartphones, tablets, and high-performance computing systems.
Improved Signal Integrity
With the proper stack-up design, 10-layer PCBs can offer improved signal integrity compared to boards with fewer layers. By strategically placing signal layers and ground planes, designers can minimize crosstalk, reduce electromagnetic interference (EMI), and maintain consistent impedance throughout the board.
Enhanced Power Distribution
The increased number of layers in a 10-layer PCB allows for better power distribution. Dedicated power planes can be incorporated into the stack-up, ensuring stable and clean power delivery to all components on the board. This is particularly important for devices with high power requirements or sensitive analog circuits.
Key Considerations for 10-Layer PCB Stack-up Design
Material Selection
Choosing the right materials is crucial for the performance and reliability of a 10-layer PCB. The most common base material is FR-4, a glass-reinforced epoxy laminate. However, for high-speed or high-frequency applications, materials with lower dielectric constants and loss tangents, such as Rogers or Isola, may be preferred. The thickness and type of copper foil used for each layer should also be carefully considered based on the intended current carrying capacity and signal requirements.
Layer Arrangement
The arrangement of layers in a 10-layer PCB stack-up plays a significant role in its electrical characteristics. A typical stack-up may consist of the following layers:
Layer | Description |
---|---|
1 | Top signal layer |
2 | Ground plane |
3 | Signal layer |
4 | Power plane |
5 | Signal layer |
6 | Signal layer |
7 | Power plane |
8 | Signal layer |
9 | Ground plane |
10 | Bottom signal layer |
This arrangement provides a balance between signal integrity, power distribution, and EMI shielding. However, the exact layer arrangement may vary depending on the specific design requirements.
Impedance Control
Maintaining consistent impedance throughout the PCB is essential for ensuring signal integrity and minimizing reflections. The target impedance for each signal layer should be calculated based on the desired characteristic impedance (typically 50Ω or 100Ω) and the dielectric constant of the insulating material. The width and spacing of the traces, as well as the thickness of the dielectric layers, must be carefully designed to achieve the target impedance.
Via Placement and Optimization
Vias are used to interconnect different layers in a PCB. In a 10-layer board, via placement and optimization become more challenging due to the increased number of layers and potential signal paths. Designers should follow these guidelines:
- Minimize the number of vias to reduce signal discontinuities and manufacturing complexity.
- Place vias strategically to minimize signal path length and avoid crossing sensitive signal traces.
- Use via stitching around high-speed signal traces to provide a low-impedance return path and reduce EMI.
- Consider using blind or buried vias to optimize signal routing and reduce board size.
Signal Layer Pairing
In a 10-layer PCB, signal layers should be paired with adjacent ground or power planes to create a controlled impedance environment. This pairing helps to minimize crosstalk and provide a consistent reference plane for the signals. For example, a high-speed signal layer can be paired with an adjacent ground plane, while a lower-speed signal layer can be paired with a power plane.
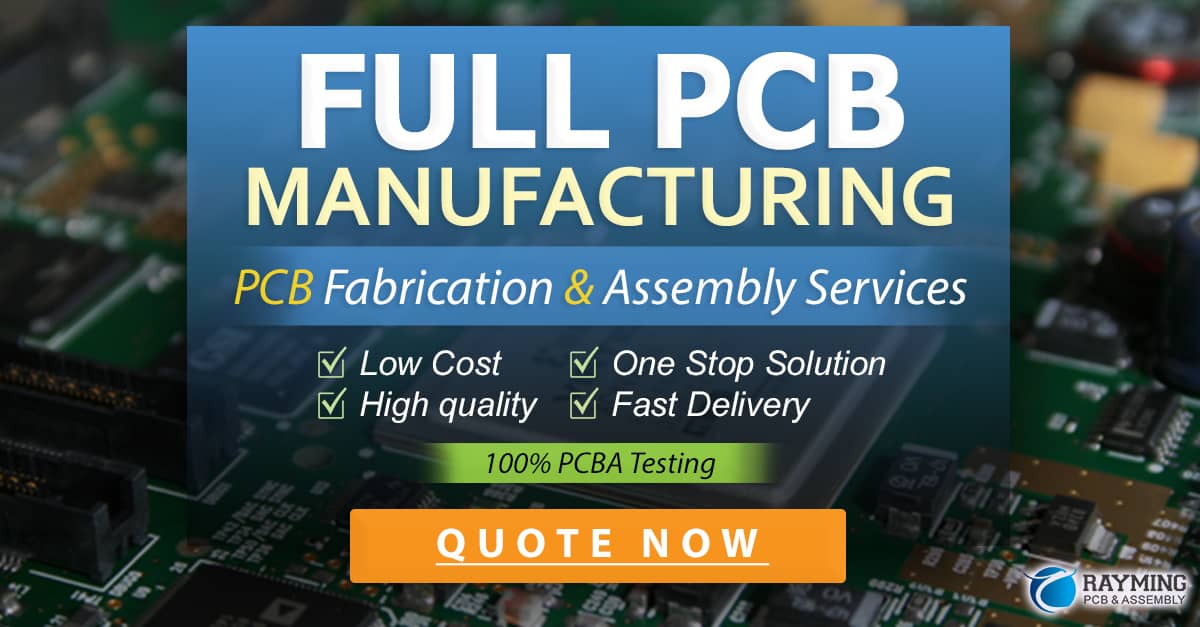
Designing for Manufacturing and Assembly
PCB Thickness and Aspect Ratio
The overall thickness of a 10-layer PCB is determined by the thickness of the individual layers and the insulating materials used. Designers should aim for a total thickness that is manageable for manufacturing and assembly processes. Additionally, the aspect ratio (the ratio of the board’s length to its thickness) should be kept within acceptable limits to prevent warping or other mechanical issues during manufacturing.
Copper Balancing and Symmetry
To minimize warping and ensure consistent etching, it is essential to balance the copper distribution across all layers of the PCB. This means that the copper area on each layer should be roughly equal, and the stack-up should be symmetrical about the center line. Copper thieving or copper pours can be used to achieve copper balance in areas with low copper density.
Drilling and Plating Considerations
10-layer PCBs require precise drilling and plating processes to ensure reliable interconnections between layers. Designers should adhere to the manufacturer’s minimum hole size and spacing requirements to avoid drilling and plating issues. Additionally, the aspect ratio of the holes (the ratio of the hole depth to its diameter) should be kept within the manufacturer’s recommended range to ensure proper plating coverage.
Testing and Verification
Design Rule Checking (DRC)
Before sending a 10-layer PCB design for manufacturing, it is crucial to perform a thorough design rule check (DRC). DRC helps to identify any violations of the manufacturer’s design guidelines, such as minimum trace width, spacing, or hole size. By resolving these issues early in the design process, designers can avoid costly manufacturing delays and potential reliability problems.
Signal Integrity Simulation
Signal integrity simulation is an essential step in verifying the performance of a 10-layer PCB. By simulating the behavior of signals in the board, designers can identify potential issues such as crosstalk, reflections, or impedance mismatches. Tools like Hyperlynx or Sigrity can be used to perform signal integrity simulations and optimize the design accordingly.
Prototype Testing
Once the design has been verified through DRC and signal integrity simulations, it is recommended to manufacture a prototype of the 10-layer PCB. The prototype should be thoroughly tested to validate its electrical performance, mechanical integrity, and thermal characteristics. Any issues identified during prototype testing should be addressed before proceeding to full-scale production.
Frequently Asked Questions (FAQ)
-
Q: What are the advantages of using a 10-layer PCB over a board with fewer layers?
A: 10-layer PCBs offer several advantages, including increased complexity and functionality, improved signal integrity, and enhanced power distribution. They can accommodate a larger number of components and circuits, making them suitable for advanced electronic devices. -
Q: How does the layer arrangement affect the performance of a 10-layer PCB?
A: The layer arrangement in a 10-layer PCB plays a crucial role in its electrical characteristics. By strategically placing signal layers, ground planes, and power planes, designers can optimize signal integrity, minimize crosstalk, and ensure stable power delivery to all components on the board. -
Q: What materials are commonly used for 10-layer PCBs?
A: The most common base material for 10-layer PCBs is FR-4, a glass-reinforced epoxy laminate. However, for high-speed or high-frequency applications, materials with lower dielectric constants and loss tangents, such as Rogers or Isola, may be preferred. -
Q: How can designers achieve consistent impedance in a 10-layer PCB?
A: To achieve consistent impedance in a 10-layer PCB, designers must carefully calculate the target impedance for each signal layer based on the desired characteristic impedance and the dielectric constant of the insulating material. The width and spacing of the traces, as well as the thickness of the dielectric layers, must be designed accordingly. -
Q: What are some important considerations for manufacturing and assembling 10-layer PCBs?
A: When designing 10-layer PCBs for manufacturing and assembly, designers should consider factors such as PCB thickness and aspect ratio, copper balancing and symmetry, and drilling and plating requirements. Adhering to the manufacturer’s guidelines and recommendations can help ensure a smooth and reliable manufacturing process.
Conclusion
Designing a 10-layer PCB stack-up requires careful consideration of numerous factors, including material selection, layer arrangement, impedance control, via placement, and manufacturing constraints. By following the guidelines and best practices outlined in this article, designers can create robust and reliable 10-layer PCBs that meet the demanding requirements of modern electronic devices. Through proper design, simulation, and testing, designers can ensure optimal performance and manufacturability of their 10-layer PCB designs.
0 Comments