Turnkey PCB assembly refers to a streamlined service provided by electronics manufacturers where they handle the complete process of assembling printed circuit boards (PCBs). This spans from procuring components to soldering to post-production testing. The customer simply provides their finished board design files and bill of materials (BOM) to the turnkey supplier.
This consolidated outsourcing approach minimizes the client’s labor for overhead-intensive manufacturing processes. The service provider oversees assembly based on pre-established quality parameters, affording customers faster product deployment without acquiring assembly tools or expertise.
What Does Turnkey Mean?
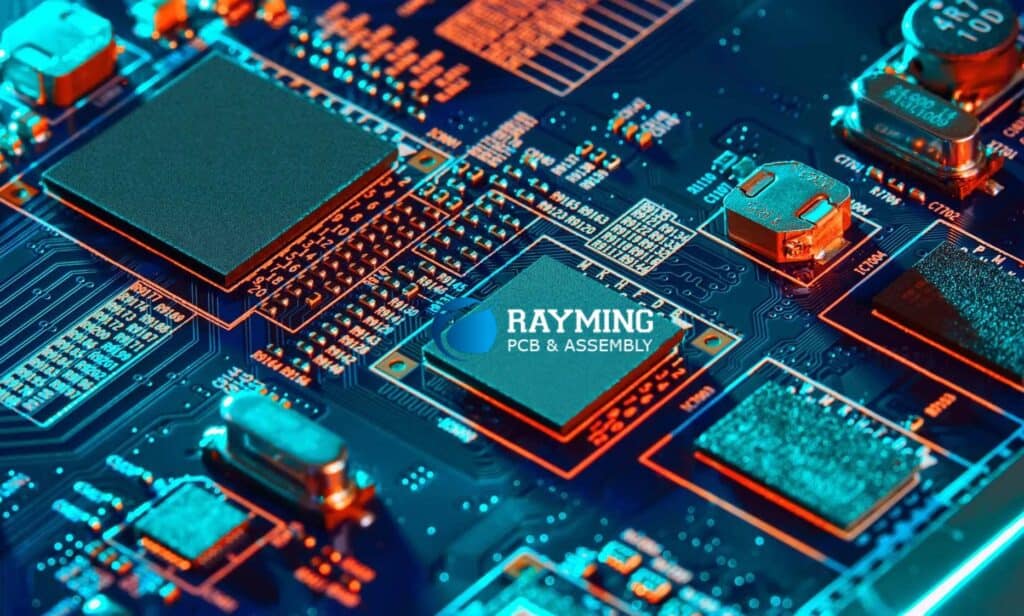
The term “turnkey” comes from the metaphor of a locked device that simply needs a key turned to activate and start up. Applied to industry, it refers to acquiring a fully ready-made solution merely needing client input to deploy.
For PCB assembly services labeled as turnkey, this signifies the heavy lifting of the soldering, inspection, testing, programming and other manufacturing work gets handled out-of-box by the vendor. The customer supplies their Gerber files and parts list as the figurative “key” to kick-start fabrication of their populated board design.
Scope of Turnkey PCB Assembly
A turnkey assembly provider typically offers to execute nearly the entire population process for a supplied PCB design. This may encompass:
- Sourcing components – Procure required resistors, ICs, connectors, etc, per supplied BOM from vetted suppliers
- Kitting parts – Organize discrete reels/cut-tape parts into kits assigned per PCB
- Solder paste application – Print solder paste on pads for surface-mount devices
- Pick-and-place – Robotic SMT mounting of tiny chips and capacitors
- Reflow soldering – Heat curing solder paste deposits to affix components
- In-circuit testing – Validate functioning after reflow process
- Conformal coating – Apply protective material across populated surface
- Final functional test – Power-on testing that boards behave correctly
- Packaging – Bag or box assembled boards for shipping
This demonstrates how turnkey encompasses all the key stages in transforming PCB designs into working populated boards – no steps omitted.
Why Use Turnkey Assembly Services?
For organizations lacking in-house manufacturing equipment and staff, turnkey PCB assembly delivers boards without needing significant process investment. Reasons companies utilize these services include:
1. Eliminates Equipment Acquisition
The turnkey supplier already made capital investments in modern SMT lines, selective soldering tools, and inspection apparatus. Clients avoid these costs.
2. Provides Production Expertise
Experienced assembly technicians execute optimized fabrication routines and leverage quality methodologies like IPC standards – know-how challenging for customers to establish independently.
3. Enables Focusing Design Resources on Core Competencies
Engineering groups concentrate time on what uniquely drives business goals rather than supporting activities. This maximizes ROI of skilled teams.
4. Scales Effectively on Demand
Manufacturing partners expand/contract operations faster than clients can. This supports fluctuating production requirements.
5. Reduces Time-to-Market
Parallelized assembly workflows and rapid prototyping compress fabrication schedules, accelerating product launch speed.
The structured nature of turnkey arrangements allows companies to derive these benefits without taking on the full product deployment burden themselves.
Turnkey for Low, Medium, and High Volume
Turnkey PCB assembly providers have experience supporting a wide range of production scenarios – from small prototype runs to mid-size field deployments to major manufacturing initiatives.
Low Volume
For startup runs, simplified quoting formats allow small businesses or design engineers to quickly manufacture 10-100 units of an innovative new product on lean budgets. These builds validate concepts.
Medium Volume
Once designs mature, scaled up production of hundreds or a few thousand populated boards reduces costs while meeting initial sales demand and field testing needs. Turnkey supports ramping without major investment.
High Volume
Migrating vetted designs offshore to turnkey CMs enables steady-state manufacturing at huge scales across tens or hundreds of thousands of units to satisfy mass market release.
This range highlights the versatility of turnkey assembly for short-run inventions to high-output commercial goods.
Core PCB Assembly Technology
While turnkey providers manage executing board population end-to-end, understanding the key phases and terminology around these processes helps inform what the service entails.
Surface Mount Technology (SMT)
The majority of modern PCB components get mounted as surface mount devices (SMDs). This encompasses small passives like 0603 chips to BGA packages to connectors soldered atop the board. High-speed pick-and-place machines precisely populate these components.
[Picture of SMT pick-and-place]
Solder paste applied by stenciling or jet printing glues components in position so arrays of parts affix simultaneously during the reflow process baking boards through conveyor ovens.
Through Hole Technology (THT)
Some components occupy thru holes on boards rather than surface pads. Often connectors, power circuitry or mechanical fixtures require leads passing fully through. Wave soldering or selective automated solder tools solder these bottom side.
Conformal Coating Application
To safeguard populated boards from condensation, grime and other contaminants affecting electrical function, protective resin coatings get applied over the entire assembly using mechanical spray systems or brushes.
In-Circuit and Functional Testing
Once population finishes, rigorous electrical testing validates boards operate correctly performing actions like checking voltages, continuity, powered behavior and that components configured as expected.
This overview covers primary assembly steps – details the turnkey partner meticulously performs based on customer specifications.
Turnkey Quoting and Ordering
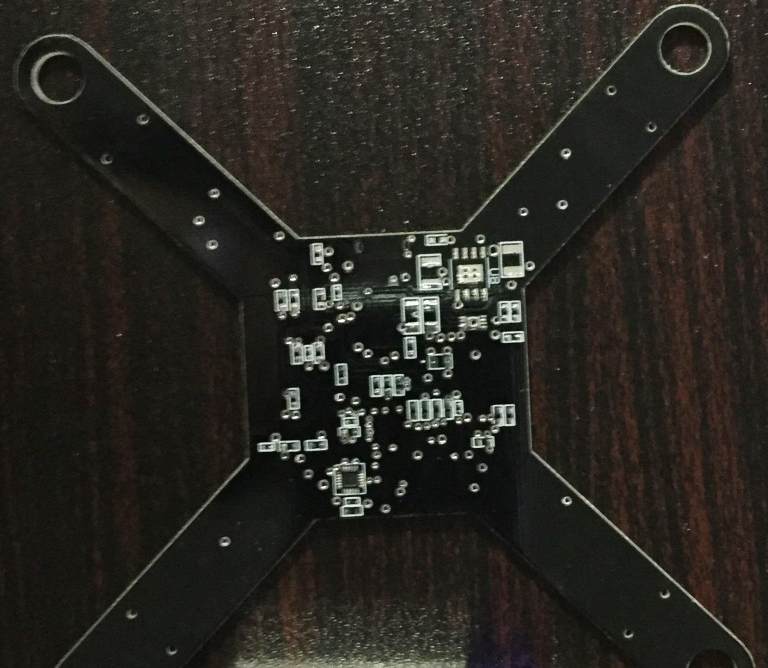
To initiate turnkey PCB assembly services, clients go through structured quoting and order placement stages submitting their fully designed boards and bill of materials.
Requesting Assembly Quotes
Customer starts by completing questionnaire specifying key fabrication details like:
- Number of boards required
- Board characteristics – size, layer count, etc
- BOM – quantity per component
- Special fabrication needs
Generating Assembly Quote
Manufacturer reviews inputs and Gerber files then issues comprehensive quote indicating:
- Unit pricing based on order volume
- Cost breakdown for materials, labor, margin
- Estimated production timeline
Placing Purchase Order
If quote meets requirements, customer sends PO with authorization to proceed based on quoted terms. Manufacturer commences kitting and assembly using specified components.
Formalizing expectations upfront ensures optimal bi-directional coordination between client and turnkey supplier through the job.
Quality Management
For end products to work reliably across extended lifetimes often spanning years, assembled boards must function flawlessly despite harsh mechanical, electrical and thermal stresses. This demands vigilant quality management.
Validation and Inspection
Thermal stress screening, x-ray imaging, automated optical inspection and electrical boundary scans are all common techniques used by assembly houses to catch defects before customer delivery.
Industry Standards
Most turnkey providers follow IPC guidelines like IPC-A-610 for inspection criteria or IPC J-STD-001 methodology for soldering quality – establishing rigorously controlled processes.
Change Management Procedures
Once quality parameters set for a given turnkey PCB project, stringent change control governs modifications balancing flexibility and robust products.
Certification Tracking
Suppliers catalog component certifications, operator training credentials, machinery calibrations and other records substantiating compliance to purchaser that assembly quality meets objectives.
With robust quality practices and transparency through production, turnkey operators mitigate reliability risks that developed boards may otherwise exhibit. Getting support here eases customer verification.
Turnkey Assembly Quote Drivers
What key factors determine pricing when turnkey manufacturers generate quotation estimates to populate printed circuit boards? Here are main considerations:
Quote Factor | Description |
---|---|
Board Size | Smaller boards cost less than larger boards to populate |
Layer Count | More board layers increase fabrication difficulty/cost |
Component Type Mix | Complex components add cost (BGA ICs vs. resistors) |
Component Density | More parts packed into same area increases assembly price |
Lead-Free Requirement | Lead-free assembly more expensive than leaded solder |
Order Volume | High volume benefits from economies of scale |
Testing/Inspection Scope | Comprehensive testing adds cost over basic checks |
Specialty Coatings | Conformal coat, potting raise cost from bare SMT assembly |
Certification Requirements | Meeting standards like ISO-9001 increase processes |
PCB Preparation | If turnkey provider must source boards instead of customer, cost goes up |
Geographic Location | Onshore assembly pricier than overseas providers |
Understanding this breakdown helps set expectations around quotes and budgeting for turnkey PCB assembly services spanning prototype through production use cases.
Selecting a Turnkey Assembly Partner
With many electronic manufacturing service (EMS) companies and contract manufacturers offering turnkey PCB assembly globally, here are key considerations when evaluating prospective vendors:
Capabilities Fit – Confirm provider has done similar designs previously and has aptitude for complexity of product
Quality Record – Review defect ratios, customer audits/reviews, quality certifications held
Client References – Reach out to existing users about service experience
Tooling/Machine Investments – Inquire which capital equipment exists; new or dated tools?
Location – Assess if provider site offers needed development iteration speed
Business Stability – Check years in operation, ownership changes, supplierships held
Total Cost – Do bulk pricing tiers align to long-term order volume needs?
Security & IP – Are non-disclosure policies and IT data protections adequate?
Vetting turnkey candidates thoroughly on parameters like these reduces risks of encountering capability gaps, communication hurdles or unanticipated costs down the line.
Bridging Design to Manufacturing
In tandem with outsourcing PCB fabrication and assembly to capable production partners, design-for-manufacturing (DFM) practices ensure a smooth technology transfer.
Design Rule Checks
Running DFM analysis on layouts using specified manufacturer design rules, preferred component families and other constraints maximizes yields, saving cost and time.
Test Point Integration
Adding test points on boards provides access for in-circuit testing probes during population. This makes physical debugging easier also.
Design Data Packages
Compiling complete documentation like assembly drawings, BOM, fabrication files and other details in a manufacturing package simplifies handoff.
Care upfront eases ramps and prevents surprises from designs needing revisions reacting to issues only discovered once reaching the turnkey vendor.
Future Outlook for Turnkey Services
As globalized trade enables increased specialization between engineering design and manufacturing, turnkey PCB assembly solutions grow more attractive across various industries. This leads to several likely trends ahead:
Continual Cost Improvements – Economies of scale and enhanced production automation will allow turnkey providers to reduce service pricing
Quality Bar Raising – Heightened competition sees vendors attain advanced certifications like AS9100 as table stakes capabilities
Scope Expansion – More turnkey suppliers extend offerings to cover complete box/enclosure assembly bringing together PCBs, cabling, electromechanical parts
LOW PART FABRICATION – As additive manufacturing techniques mature, selected turnkey shops may offer rapid printed fabrication of custom plastic enclosures and mechanical fixtures right alongside PCB population
Design Integration – Cloud-based DFM checks and release processes integrate more smoothly between customer and turnkey vendor data environments, preventing revisions
As technology barriers fall, the turnkey PCB assembly methodology should only become easier and more appealing – allowing innovators to transform circuit designs directly to fielded products.
Conclusion
This exploration into turnkey PCB assembly elaborates what this production strategy entails – outsourcing populated board fabrication based upon a furnished component list and board design to capable manufacturing service providers. We covered key facets like:
- Typical scope spanning component procurement through post-assembly test
- Motivations around expertise access, capital avoidance and accelerated time-to-market
- Quoting considerations and quality standards upholding robust products
- Technology overviews around SMT, thru-hole assembly and conformal coating
- Best practices for design transfers and release to turnkey partners
As engineering groups seek ways streamlining moving designs from prototype through mass production, the multitude of heavy burdens eliminated by capable turnkey assembly manufacturers will ensure these simplified outsourcing approaches continue flourishing.
Frequently Asked Questions
Here are answers to some common questions about turnkey PCB assembly:
Does every component on my BOM need specified values/ratings when submitting designs for turnkey?
Ideally, yes – providing complete rated specifications for voltage, tolerance, temperature coefficient, etc. aids the kitting process. But the turnkey supplier can select appropriate rating values if unspecified based on your functional description.
What file deliverables does a turnkey PCB assembly house need?
They need your Gerber fabrication and drill files defining bare PCB layouts along with component placement centroid data, a Bill of Materials (BOM) listing all parts with quantities and a ReadMe covering any special instructions.
Can I make changes to a design or BOM after submitting to turnkey?
Yes, through rigid change control processes. Frequent revisions risk added cost and delays. Turnkey partners define policies about Engineering Change Order (ECO) change flexibility once released.
What process adjustments should I expect when transitioning a prototype board assembly to mass production?
DFM tweaks like increasing tolerances, reducing layer counts, substituting equivalent parts may occur for high-volume processing. The turnkey engineering team handles this while keeping electrical functionality unchanged.
Why might turnkey PCB assembly costs increase after initial quotes during later stages of an project?
If requirements get added like demanding tighter defect standards, undergoing specialized testing, requiring certified components, requesting last-minute priority scheduling etc, then pricing rises accordingly based on increased overhead to satisfy new criteria. Upfront planning for everything needed avoids unexpected hikes.
0 Comments