Introduction to DFM-assisted PCB Fabrication
Design for manufacturability (DFM) is an approach to printed circuit board (PCB) design that aims to optimize the manufacturing process. By considering the capabilities and limitations of the manufacturing process during the design phase, DFM helps to minimize production issues, improve yield, and reduce costs. DFM-assisted PCB fabrication offers several key advantages over traditional PCB design and manufacturing methods.
Advantage 1: Reduced Manufacturing Costs
One of the primary benefits of DFM-assisted PCB fabrication is reduced manufacturing costs. By designing PCBs with manufacturability in mind, companies can avoid costly production issues and delays. DFM helps to identify potential problems early in the design process, allowing for changes to be made before the board enters production. This proactive approach minimizes the need for expensive rework and saves time and money in the long run.
Consider the following example:
Scenario | Traditional PCB Design | DFM-Assisted PCB Design |
---|---|---|
Design Revisions | 4 | 2 |
Prototype Iterations | 3 | 1 |
Time to Market (weeks) | 12 | 8 |
Manufacturing Cost per Board | $50 | $35 |
In this scenario, the DFM-assisted PCB design required fewer revisions and prototype iterations, resulting in a faster time to market and lower manufacturing costs per board.
Advantage 2: Improved Yield and Reliability
DFM-assisted PCB fabrication helps to improve yield and reliability by ensuring that the board design is compatible with the manufacturing process. By adhering to design rules and guidelines, DFM minimizes the risk of production defects and ensures that the final product meets the required quality standards. This, in turn, leads to higher yields and fewer product failures in the field.
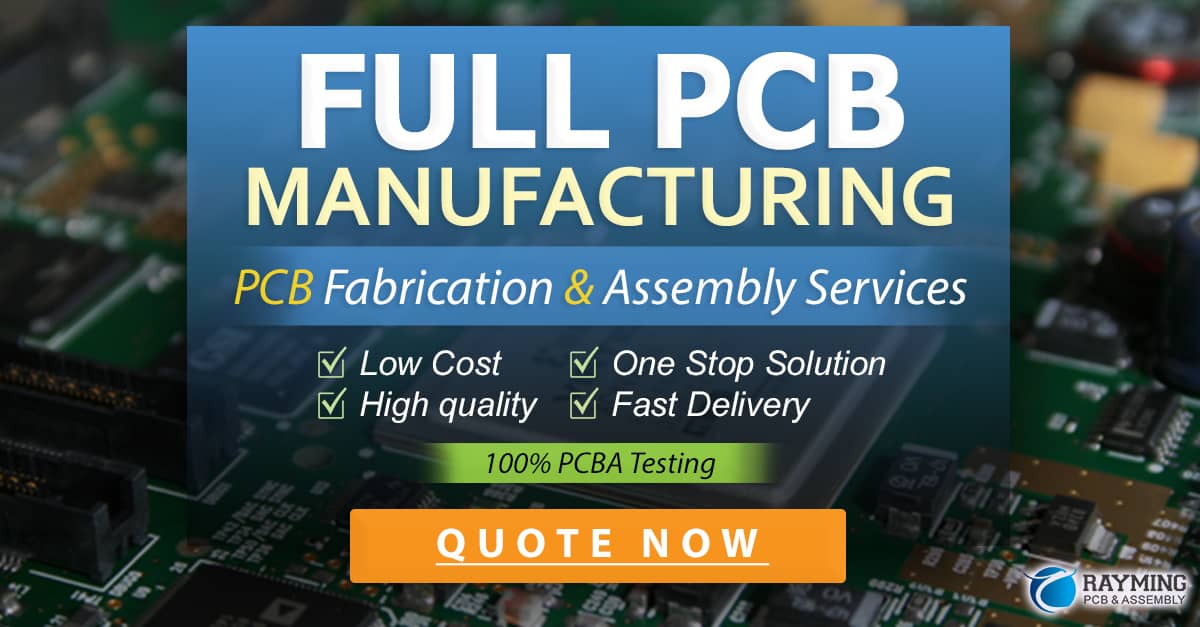
Advantage 3: Faster Time to Market
By streamlining the design and manufacturing process, DFM-assisted PCB fabrication enables faster time to market. With fewer design revisions and prototype iterations, companies can bring their products to market more quickly, gaining a competitive edge. DFM also helps to avoid production delays caused by design issues, further accelerating the time to market.
Advantage 4: Enhanced Design Flexibility
DFM-assisted PCB fabrication allows for greater design flexibility by providing designers with a clear understanding of the manufacturing capabilities and constraints. By working within these parameters, designers can create innovative and complex PCB designs that are still manufacturable. This enables companies to push the boundaries of PCB design while maintaining high levels of quality and reliability.
Advantage 5: Improved Communication and Collaboration
DFM-assisted PCB fabrication promotes better communication and collaboration between the design and manufacturing teams. By involving the manufacturing team early in the design process, designers can gain valuable insights into the production capabilities and limitations. This collaborative approach helps to ensure that the final design is optimized for manufacturability, reducing the risk of production issues and delays.
Advantage 6: Reduced Environmental Impact
DFM-assisted PCB fabrication can help to reduce the environmental impact of electronics manufacturing. By optimizing the design for manufacturability, DFM minimizes the amount of material waste generated during production. This not only reduces costs but also contributes to a more sustainable manufacturing process. Additionally, by improving yield and reliability, DFM helps to reduce the number of defective products that end up in landfills.
Advantage 7: Increased Supply Chain Efficiency
DFM-assisted PCB fabrication can improve supply chain efficiency by ensuring that the board design is compatible with the capabilities of the chosen manufacturing partner. By designing with the manufacturer’s process in mind, companies can avoid the need to switch suppliers mid-production due to incompatible design features. This helps to streamline the supply chain, reducing lead times and minimizing the risk of disruptions.
Advantage 8: Better Product Quality and Reliability
DFM-assisted PCB fabrication contributes to better product quality and reliability by ensuring that the board design is optimized for the manufacturing process. By minimizing the risk of production defects and ensuring that the board meets the required quality standards, DFM helps to produce PCBs that are more reliable and have a longer lifespan. This, in turn, leads to increased customer satisfaction and reduced warranty claims.
Advantage 9: Cost Savings Through Design Optimization
DFM-assisted PCB fabrication enables cost savings through design optimization. By considering the manufacturing process during the design phase, designers can make informed decisions about material selection, component placement, and routing. This optimization helps to reduce the overall cost of the PCB by minimizing the use of expensive materials, reducing the number of layers required, and optimizing the board size.
Consider the following example:
Design Aspect | Traditional PCB Design | DFM-optimized PCB Design |
---|---|---|
Number of Layers | 6 | 4 |
Board Size (mm) | 100 x 150 | 90 x 130 |
Material | High-cost FR-4 | Standard FR-4 |
Cost per Board | $75 | $50 |
In this scenario, the DFM-optimized PCB design uses fewer layers, a smaller board size, and a standard material, resulting in a significant cost saving per board.
Frequently Asked Questions (FAQ)
1. What is Design for Manufacturability (DFM)?
Design for Manufacturability (DFM) is an approach to PCB design that takes into account the capabilities and limitations of the manufacturing process. By considering these factors during the design phase, DFM aims to optimize the design for production, minimizing the risk of manufacturing issues and improving overall efficiency.
2. How does DFM-assisted PCB fabrication differ from traditional PCB design and manufacturing?
DFM-assisted PCB fabrication differs from traditional methods by incorporating manufacturability considerations early in the design process. This proactive approach helps to identify and address potential production issues before the board enters manufacturing, resulting in fewer design revisions, improved yield, and reduced costs.
3. What are some key factors that DFM considers during the PCB design process?
Some key factors that DFM considers during the PCB design process include:
- Manufacturing capabilities and limitations
- Material selection
- Component placement and spacing
- Routing and trace width
- Solder mask and silkscreen design
- Testing and inspection requirements
4. Can DFM-assisted PCB fabrication be applied to both simple and complex PCB designs?
Yes, DFM-assisted PCB fabrication can be applied to PCBs of varying complexity. In fact, DFM is particularly beneficial for complex designs, as it helps to ensure that the board can be manufactured efficiently and reliably, despite its intricacy.
5. How can I implement DFM in my PCB design process?
To implement DFM in your PCB design process, consider the following steps:
- Educate yourself and your team about DFM principles and guidelines.
- Establish a collaborative relationship with your manufacturing partner early in the design process.
- Use DFM-aware PCB design software that can check your design against manufacturing constraints.
- Regularly review and update your DFM guidelines to stay current with advancements in manufacturing technology.
- Foster a culture of continuous improvement, actively seeking feedback from the manufacturing team to refine your DFM practices.
Conclusion
DFM-assisted PCB fabrication offers numerous advantages over traditional PCB design and manufacturing methods. By considering the manufacturability of the board during the design phase, DFM helps to reduce costs, improve yield and reliability, accelerate time to market, and enhance overall product quality. As the demand for high-quality, cost-effective PCBs continues to grow, the adoption of DFM principles will become increasingly essential for companies looking to stay competitive in the electronics industry.
0 Comments