Introduction to DFM-optimized PCB
Design for Manufacturability (DFM) is a crucial aspect of the printed circuit board (PCB) design process that focuses on optimizing the design to enhance manufacturability, reduce costs, and improve the overall quality of the final product. By incorporating DFM principles into the PCB design process, engineers can streamline the manufacturing process, minimize potential issues, and ensure a faster time-to-market.
In this article, we will explore the key aspects of DFM-optimized PCB design and how it can help reduce costs and accelerate the manufacturing process.
The Importance of DFM in PCB Design
DFM plays a vital role in the PCB design process by addressing the following key areas:
-
Cost reduction: By optimizing the design for manufacturability, DFM helps minimize production costs, material wastage, and potential rework, ultimately leading to a more cost-effective PCB.
-
Faster production: DFM-optimized designs are easier to manufacture, resulting in shorter production cycles and faster time-to-market.
-
Improved quality: Incorporating DFM principles minimizes the risk of manufacturing defects, ensuring higher quality PCBs and reducing the need for costly rework.
-
Enhanced reliability: DFM-optimized PCBs are more reliable, as they are designed to withstand the rigors of the manufacturing process and perform optimally in their intended application.
Key Aspects of DFM-Optimized PCB Design
To create a DFM-optimized PCB, designers must consider the following key aspects:
1. Component Selection and Placement
Choosing the right components and placing them optimally on the PCB is crucial for DFM. Consider the following factors:
- Component packagetype: Select component package types that are easy to manufacture and have a high yield rate, such as surface-mount devices (SMDs) and chip-scale packages (CSPs).
- Component size and pitch: Opt for larger component sizes and wider pitches to facilitate easier soldering and inspection.
- Component orientation: Ensure consistent component orientation to simplify the assembly process and minimize errors.
- Component placement: Place components in a way that minimizes the risk of tombstoning, shadowing, and other placement-related issues.
2. Board Layout and Routing
The board layout and routing play a significant role in DFM. Consider the following guidelines:
- Board size and shape: Choose a board size and shape that is easy to manufacture and handle, avoiding sharp corners and irregular shapes whenever possible.
- Layer count: Minimize the number of layers to reduce manufacturing complexity and cost. However, ensure that the layer count is sufficient to meet the design requirements.
- Trace width and spacing: Maintain appropriate trace widths and spacing to ensure reliable electrical connections and minimize the risk of short circuits.
- Via placement: Place vias strategically to improve manufacturability and minimize the risk of defects.
3. Solder Mask and Silkscreen
The solder mask and silkscreen layers are essential for protecting the PCB and providing visual references for assembly. Consider the following DFM guidelines:
- Solder mask expansion: Ensure adequate solder mask expansion around pads and traces to prevent solder bridging and short circuits.
- Silkscreen legibility: Use clear and legible silkscreen markings to facilitate accurate component placement and assembly.
- Silkscreen placement: Avoid placing silkscreen markings too close to pads and traces to prevent ink bleeding and contamination.
4. Panelization and Tooling
Panelization and tooling are critical aspects of DFM that impact the manufacturing process. Consider the following factors:
- Panel size and layout: Choose a panel size and layout that optimizes material usage and minimizes waste.
- Tooling holes and fiducials: Include appropriate tooling holes and fiducials to ensure accurate registration and alignment during the manufacturing process.
- V-scoring and routing: Use V-scoring and routing techniques to facilitate easy separation of individual PCBs from the panel.
5. Testing and Inspection
Designing for testability and inspection is crucial for ensuring the quality and reliability of the manufactured PCBs. Consider the following DFM guidelines:
- Test points: Include sufficient test points to facilitate automated testing and debugging.
- Inspection access: Ensure adequate access for visual inspection and automated optical inspection (AOI) to identify potential defects.
- Boundary scan: Implement boundary scan technology, such as JTAG, to enable efficient testing and debugging of complex PCBs.
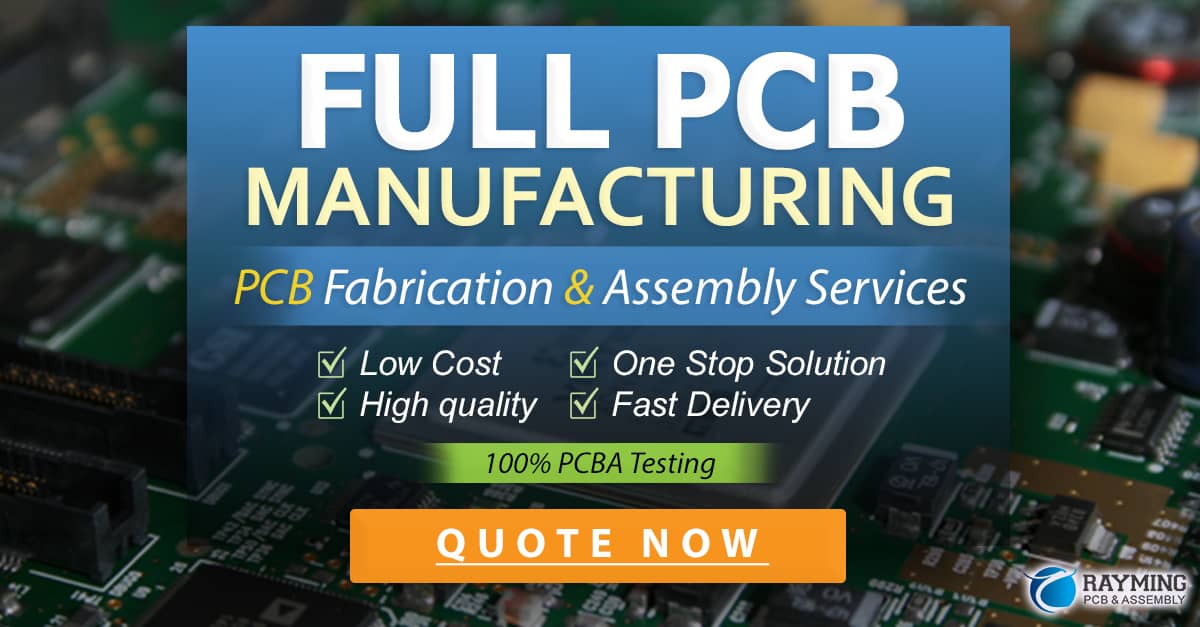
DFM Checklist for PCB Design
To ensure that your PCB design is DFM-optimized, use the following checklist:
DFM Aspect | Checklist Item | ✓ |
---|---|---|
Component Selection | Choose easy-to-manufacture component package types | |
Select appropriate component sizes and pitches | ||
Ensure consistent component orientation | ||
Board Layout and Routing | Choose an easy-to-manufacture board size and shape | |
Minimize layer count while meeting design requirements | ||
Maintain appropriate trace widths and spacing | ||
Place vias strategically for improved manufacturability | ||
Solder Mask and Silkscreen | Ensure adequate solder mask expansion | |
Use clear and legible silkscreen markings | ||
Avoid placing silkscreen markings too close to pads and traces | ||
Panelization and Tooling | Choose a panel size and layout that optimizes material usage | |
Include appropriate tooling holes and fiducials | ||
Use V-scoring and routing for easy separation of individual PCBs | ||
Testing and Inspection | Include sufficient test points for automated testing | |
Ensure adequate access for visual and automated inspection | ||
Implement boundary scan technology for efficient testing |
Collaboration Between Design and Manufacturing Teams
To fully leverage the benefits of DFM, it is essential to foster collaboration between the design and manufacturing teams. This collaboration should involve:
-
Early involvement: Engage the manufacturing team early in the design process to identify potential DFM issues and ensure that the design is optimized for manufacturability.
-
Regular communication: Maintain regular communication between the design and manufacturing teams to address any concerns and ensure that the design meets the manufacturing requirements.
-
Feedback and improvement: Encourage feedback from the manufacturing team to identify areas for improvement in the design process and incorporate their suggestions in future designs.
DFM Analysis and Verification Tools
To aid in the DFM optimization process, designers can leverage various DFM analysis and verification tools. These tools help identify potential manufacturability issues and provide guidance on how to resolve them. Some popular DFM tools include:
-
Mentor Graphics Valor NPI: A comprehensive DFM analysis tool that checks the PCB design against a set of predefined manufacturing rules and guidelines.
-
Cadence Design Systems Allegro PCB Designer: An integrated PCB design environment that includes DFM analysis and verification capabilities.
-
Zuken CR-8000 Design Force: A PCB design solution that incorporates DFM analysis and verification tools to ensure manufacturability.
By utilizing these tools, designers can identify and resolve DFM issues early in the design process, reducing the risk of costly manufacturing defects and delays.
Case Studies: Successful Implementation of DFM in PCB Design
To illustrate the benefits of DFM-optimized PCB design, let’s explore two case studies:
Case Study 1: Telecommunications Equipment Manufacturer
A leading telecommunications equipment manufacturer struggled with high manufacturing costs and long production cycles due to complex PCB designs. By implementing DFM principles and collaborating closely with their manufacturing team, they achieved the following results:
- 25% reduction in manufacturing costs
- 30% faster production cycles
- 40% reduction in manufacturing defects
Case Study 2: Automotive Electronics Supplier
An automotive electronics supplier faced challenges in meeting the stringent reliability requirements of their products. By incorporating DFM guidelines and utilizing DFM analysis tools, they achieved the following outcomes:
- 20% improvement in PCB reliability
- 15% reduction in manufacturing costs
- 50% reduction in time-to-market
These case studies demonstrate the tangible benefits of DFM-optimized PCB design in reducing costs, accelerating production, and improving overall product quality and reliability.
Conclusion
Implementing DFM principles in PCB design is essential for reducing costs, accelerating the manufacturing process, and ensuring the production of high-quality, reliable PCBs. By considering key aspects such as component selection and placement, board layout and routing, solder mask and silkscreen, panelization and tooling, and testing and inspection, designers can create DFM-optimized PCBs that are easier and more cost-effective to manufacture.
Collaboration between design and manufacturing teams, along with the use of DFM analysis and verification tools, further enhances the effectiveness of DFM-optimized PCB design. As demonstrated by the case studies, the successful implementation of DFM can lead to significant cost savings, faster time-to-market, and improved product quality and reliability.
By embracing DFM principles and incorporating them into the PCB design process, companies can gain a competitive edge in today’s fast-paced electronics industry, ultimately delivering better products to their customers while minimizing costs and maximizing profitability.
Frequently Asked Questions (FAQ)
-
What is Design for Manufacturability (DFM) in PCB design?
Design for Manufacturability (DFM) is a design approach that focuses on optimizing the PCB design to enhance manufacturability, reduce costs, and improve the overall quality of the final product. -
How does DFM help reduce PCB Manufacturing Costs?
DFM helps reduce PCB manufacturing costs by minimizing production costs, material wastage, and potential rework. By optimizing the design for manufacturability, DFM ensures a more cost-effective PCB production process. -
What are the key aspects of DFM-optimized PCB design?
The key aspects of DFM-optimized PCB design include component selection and placement, board layout and routing, solder mask and silkscreen, panelization and tooling, and testing and inspection. -
How can collaboration between design and manufacturing teams enhance DFM?
Collaboration between design and manufacturing teams enhances DFM by ensuring early involvement of the manufacturing team in the design process, regular communication to address concerns, and incorporating feedback for continuous improvement. -
What are some popular DFM analysis and verification tools?
Some popular DFM analysis and verification tools include Mentor Graphics Valor NPI, Cadence Design Systems Allegro PCB Designer, and Zuken CR-8000 Design Force. These tools help identify potential manufacturability issues and provide guidance on resolving them.
0 Comments